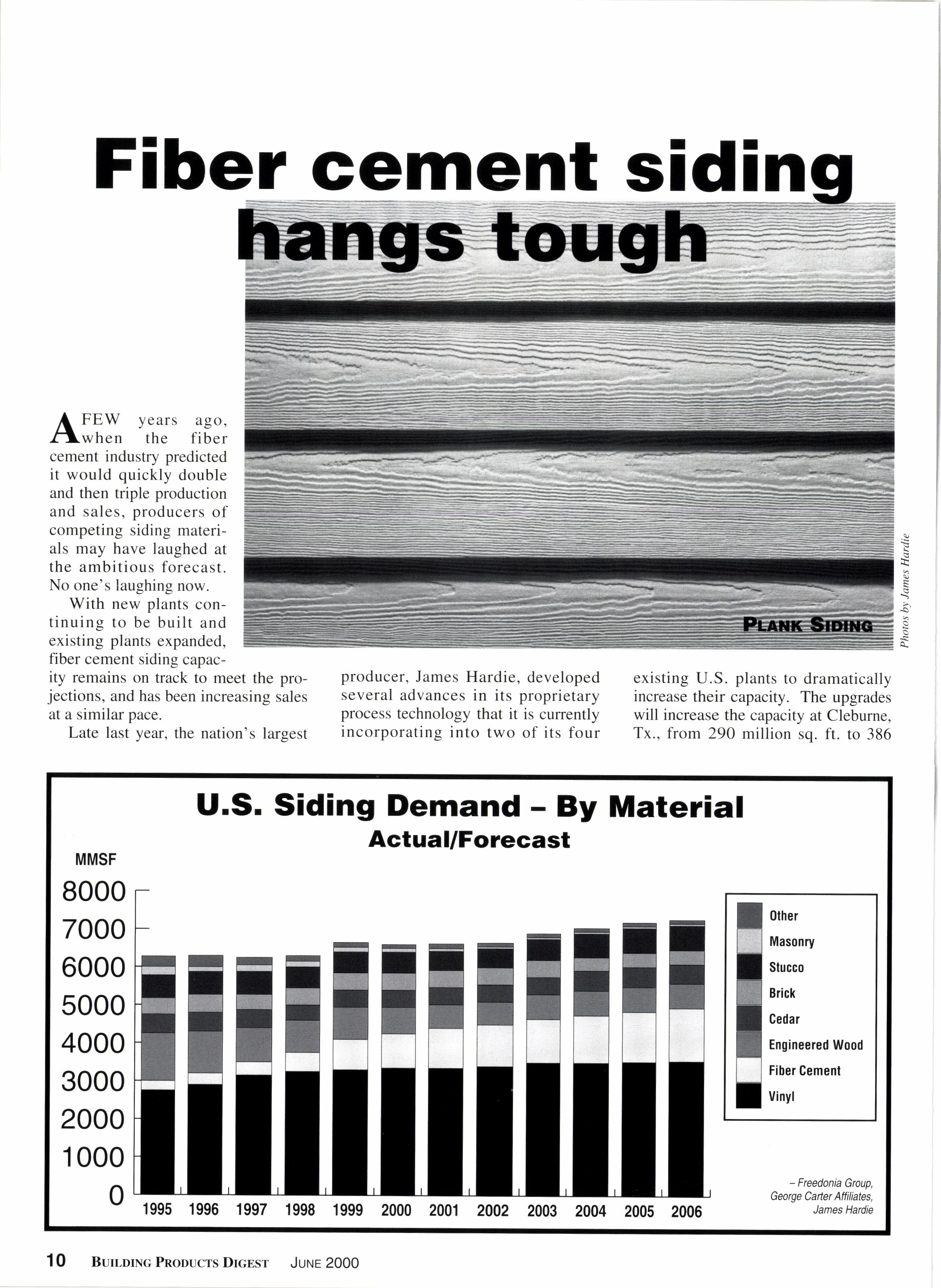
3 minute read
Fiber cement sidin
A FEW vears ago. la,w he n t he I'iber cement industry predicted it would quickly double and then triple production and sales, producers of competing siding materials may have laughed at the ambitious forecast. No one's laughing now.
With new plants continuing to be built and existing plants expanded, fiber cement siding capacity remains on track to meet the projections, and has been increasing sales at a similar pace.
Late last year, the nation's largest
7000 6000 5000 4000 3000 2000 producer, James Hardie, developed several advances in its proprietary process technology that it is currently incorporating into two of its four existing U.S. plants to dramatically increase their capacity. The upgrades will increase the capacity at Cleburne, Tx., fiom 290 million sq. fi. to 386
Siding Demand - By Material
million sq. ft. and at Tacoma, Wa., from 150 million sq. ft. to 200 million sq. ft.
Hardie also is using the new technology in a new facility under construction in Peru, Il., providing an annual production capacity of 200 million sq. ft. from a single line. The plant, expected to begin production by the third quarter of this year, is being confisured to accommodate a second products to improve the loading and stacking of products at customers' warehouses. line to meet future demand.
The new line allows CertainTeed to apply a new-generation sealant called FiberTect to its fiber cement products. Unlike conventional primers, FiberTect penetrates and seals the surface of the siding to protect it from unwanted moisture, while acting as the base coat for painting.
CertainTeed acquired the facility in 1999 from ABTco and later added a second fiber cement siding plant in White City, Or.
The facility will be completely automated from a materials handling perspective, including automated finishing and paint priming lines matched to the capacity of the fiber cement sheet machine.
Cemplank, Inc., which currently operates a fiber cement plant at its headquarters in Blandon, Pa., has two more facilities under construction.
"Currently, we're selling everything we manufacture at our Blandon facility," says Cemplank president Toussaint Dolmans. "Opening these new facilities is a proactive move to support our customers' needs."
The first will open in July in Summerville, S.C., with an annual capacity of 150 million sq. ft. Fourteen months later, the next facility will open in Sherman, Tx., with an annual capacity of 180 million sq. ft.
Additionally, Cemplank's Blandon facility recently became the first among North American plants to gain ISO 9002 certification.
At its Roaring River, N.C., plant, CertainTeed Corp. recently installed a new paint line that applies a special surface sealing system to its products prior to shipment. They also installed a packaging system for palletizing the plant's
Also operating fiber cement facilities in North America are Temple in Waxahachie, Tx., and MaxiTile Building Products, with four plants in Mexico.
According to Hardie, fiber cement's share of the U.S. siding market has grown from less than l7o in 1990 to more than 97o last year. But since the growth is mainly due to sales for new residential construction applications, the company sees huge potential in repair and remodeling, as well as the manufactured housing segment.
By 2002, fiber cement is predicted to achieve about a l57o share of the U.S. siding market. Over the next seven years, total U.S. demand for fiber cement could grow by an annual average of 20Vo, increasing from about 690 million sq. ft. annually one year ago to an estimated 2 billion sq. ft. by 2006.
And while fiber cement wrests a larger share of the siding market, manufacturers also have begun targeting other products, including interior residential applications such as tile backerboard, commercial applications such as abuse resistant internal wall linings, manufactured housing exterior wall panels, residential roofing slates and shingles, residential soffits and trims, plus new patterns, profiles and coatings across the product range.
What is fiber cement?

Fiber cement dates back to the early 1900s when the Europeans produced cement-asbestos materials. Later, when asbestos use was banned in many products, cellulosic fiber from wood was found to be an acceptable substitute.
Fiber cement products, including siding, soffit, trim and backerboards, are made from cellulose fibers, such as kraft pulp, combined with an inorganic mix of sand, cement and other additives. The mixture is formed into large sheets on equipment called-a Hatschek machine and cut to the desired size.
The products are then pressed to produce either a smooth or textured appearance, autoclave cured and factory primed. Pressing reduces wafer absorption and increases strength and density, making fiber cement an exceptionally durable building material. Factory priming can improve painting efficiency and long-term performance.
The final product is said to be more durable than wood and engineered wood siding, look and plrform better than vinyl siding, and weigh less than solid masonry, while remaining cost competitive. Easy to install and maintain, fiber cement products reportedly resist moisture, mold, mildew, pests and other adverse affects of nature; won't expand or contract with changes in temperature or humidity, and, with a "0" smoke development rating, won't burn.
- Temple and Cemplank