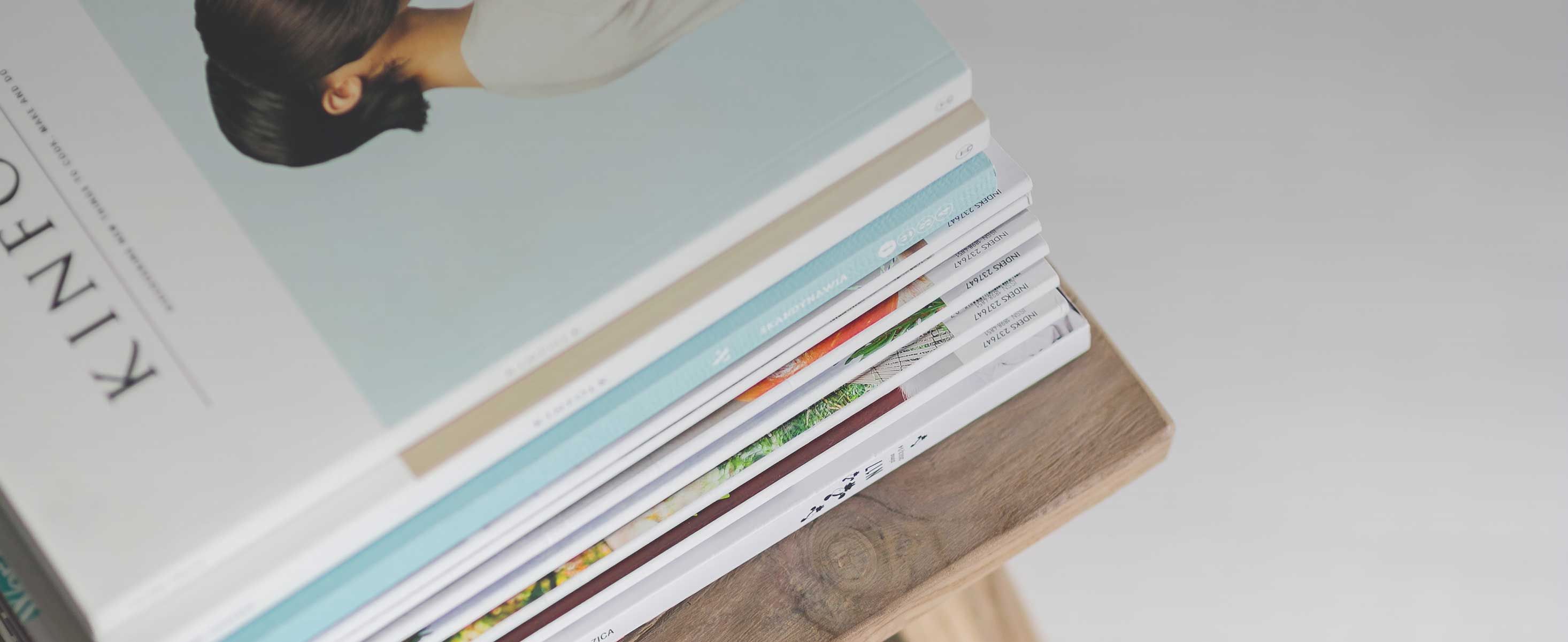
2 minute read
Latest technology runs massive Dc
the carton flow pick positions. All product picked in the modules is batch picked except the static shelving, which is order picked from DMS.
Splitcase orders are picked by full cartons in the modules and then conveyed to a carousel area, where operators pack items in store department shipping containers.
Non-conveyable items are assigned to three basic areas in the warehouse. Items too large to be conveyed are stored on pallets on pennanent racks. Items requiring protection or goods that move faster than replenishment could keep up with are set on stack racks. Stack racks, 4 ft. wide by 8 ft. long and 5 ft. high, can be stacked up to four tiers high. Items that can be placed on the floor, such as appliances, are kept in bulk storage areas. The type of product determines its stack height.
FlodReplenishment Department
delivery of merchandise to individual home centers. Most merchandise arrives in shipping from various areas of the facility via processing conveyors that merge into the quarter-milelong Rapistan sortation system. Featuring rapid view monitoring and maintenance system, the sorter can scan 140 cartons per minute and automatically direct them to the proper shipping door. The remaining merchandise, primarily bulk items, is processed using power equipment and scanned with a LRT.
Transportation
responsibility to move the merchandise off the receiving dock as each truck is unloaded. Employees scan the license plates with a Laser Radio Terminal (LRT) scanner, identifying where in the facility the merchandise should be stored.
Merchandise that arrives pre-distributed by the vendor is flowed directly from the receiving dock to the shipping doors.
Order Selection Department
Products are picked using a LRT scanner that identifies what is needed and where it is located. The layout of the facility is based on the characteristics of the merchandise.
Conveyable items are picked in three distinct areas, and each picking module has three levels of conveyors that transport cartons to the sortation system. Conventional pallet racks, used for replenishment, border the three modules. The pallet racking is nine levels high, with the bottom level replenishing
Palletized goods are staged in designated areas and transferred to dedicated locations utilizing LRTs. Merchandise is also placed in reserve locations to replenish the forward picking location upon store demand.
Shipping Department
It's the job of the shipping department to load trailers accuratelv for
Using contract carriers, the transportation staff ensures timely delivery of processed merchandise to 48 Lowe's stores in Texas, Oklahoma, Louisiana, Arkansas, Mississippi and Missouri. Each store typically receives two to three deliveries a week. The l8-acre main building, with 50 receiving doors and 100 shipping doors, runs two shifts and can eventually serve up to 100 stores. At capacity, it will employ more than 400. The four-acre specialty center, with 28 doors for shipping and receiving, handles non-conveyable items using conventional methods. It will employ over 100 employees and serve 120 stores.
LAYOUT ol Lowe's new DC is designed for fast and efficient receiving, storage and shipping of ooods to uo to 100 reoion- il home'centers. ihe south doors (A) are lor receivino. with room for bulk stoiage (B), permanent racks (C) and pick modules (D). The west doors are for shipping (E).