
2 minute read
o your gompute ta ch other?
went t0 a communications company to bring all the locations on line. Networks, Inc., Fort Lauderdale, Fl., designed and installed a specialized system so data would be sent by computer from the vehicles to the plants and to the mainframe at the disrict offices and then on to the mainframe at the main office.
"We do the translation of day+oday infonnation each night, so we can do the invoicing the next day," said Rinker's computer system manager Bill Gearhart.
And now Rinker can look at a computer monitor and, via radios integrated with the computer system, instantly know where every Rinker truck is located. This means on time anival of materials to keep jobs moving smoothly.
"The system tracks daily driver infonnation in eight stiages, from the time each truck arrives at the plant through the time it returns," Gearhart said. 'We can improve efficiency by amlyzng that data, including loading times, slump times, in-plant dmes."
The fint step to getting computers to communicate with each other is finding software tailored to tle requirements of your business. "It used to be you bought the computer, then the software," said Networks president Bob Toombs. "But nowadays you first buy the software."
After acquiring the software, you will have to find someone to design, install, maintain and manage the system. Sometimes companies hire their own in-house staff, but increasingly are finding it more practical to contract network management companies like Networks, Inc., to get them up and running.
"A building materials company shouldn't be running a technical communications compilny," said Toombs. "During the recession people are learning how to do more with fewer people, contracting part-time people for part-time jobs. And there are a lot more people who know computers than know communications. We already have the people in place, so we can provide the service at a considerably lower cost. We leave others free to do their core business."
Networks, Inc., remotely monitors every Rinker computer - and those at about 375 other sites for other companies from Florida to Seattle - 24 hours a day to ensure every system component is operational. They are available on a daily basis for "troubleshooting." Any problems can be diagnosed by remote and, if necessary, a local technician sent in.
But a fimr's computers needn't be located miles apart to need to communicate with each other. Networks, Inc., linked all the computers at Scotty's, joining the half-dozen buildings at the retailer's Winter Haven, Fl., campus via a fiber optics system.
"BH"',illlfi;ff",}3:xT;
with the tightening domestic timber supply, more American companies are looking o establish relationships with Canadian suppliers.
"With lumber, there's no difference at all (between dealing witb American or Canadian suppliers)," explains retailer Ken Marson, Marson & Marson Lumber Inc., lcavenworth, Wa. "We've been buying Canadian lumber for about five, six years now, and if there wasn't a border there, you wouldn't be able to tell the differencg."
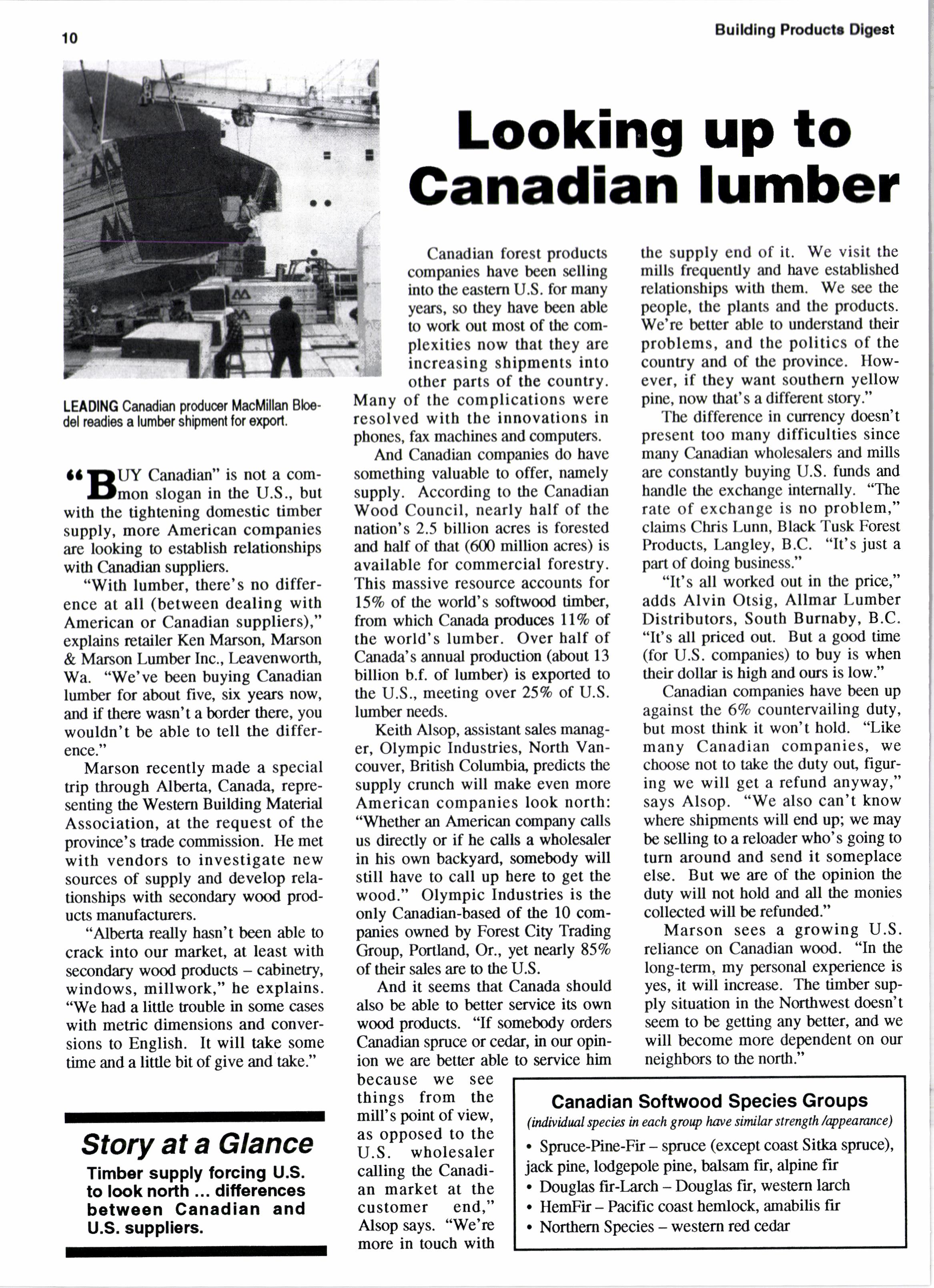
Marson recently made a sPecial rip through Alberca, Canada representing the Western Building Material Association, at the request of the provin@'s trade commission. He met with vendors to investigate new sources of supply and develop relationships with secondary wood products rranufacturers.
'Alberta really hasn't been able to crack into our market, at least with secondary wood producB - cabinetry, windows, millwork," he explains. 'We had a little trouble in some cases with metric dimensions and conversions to English. It will take some time and a little bit of give and take."
Story at a Glance
Timber supply forcing U.S. to look north ... differences between Canadian