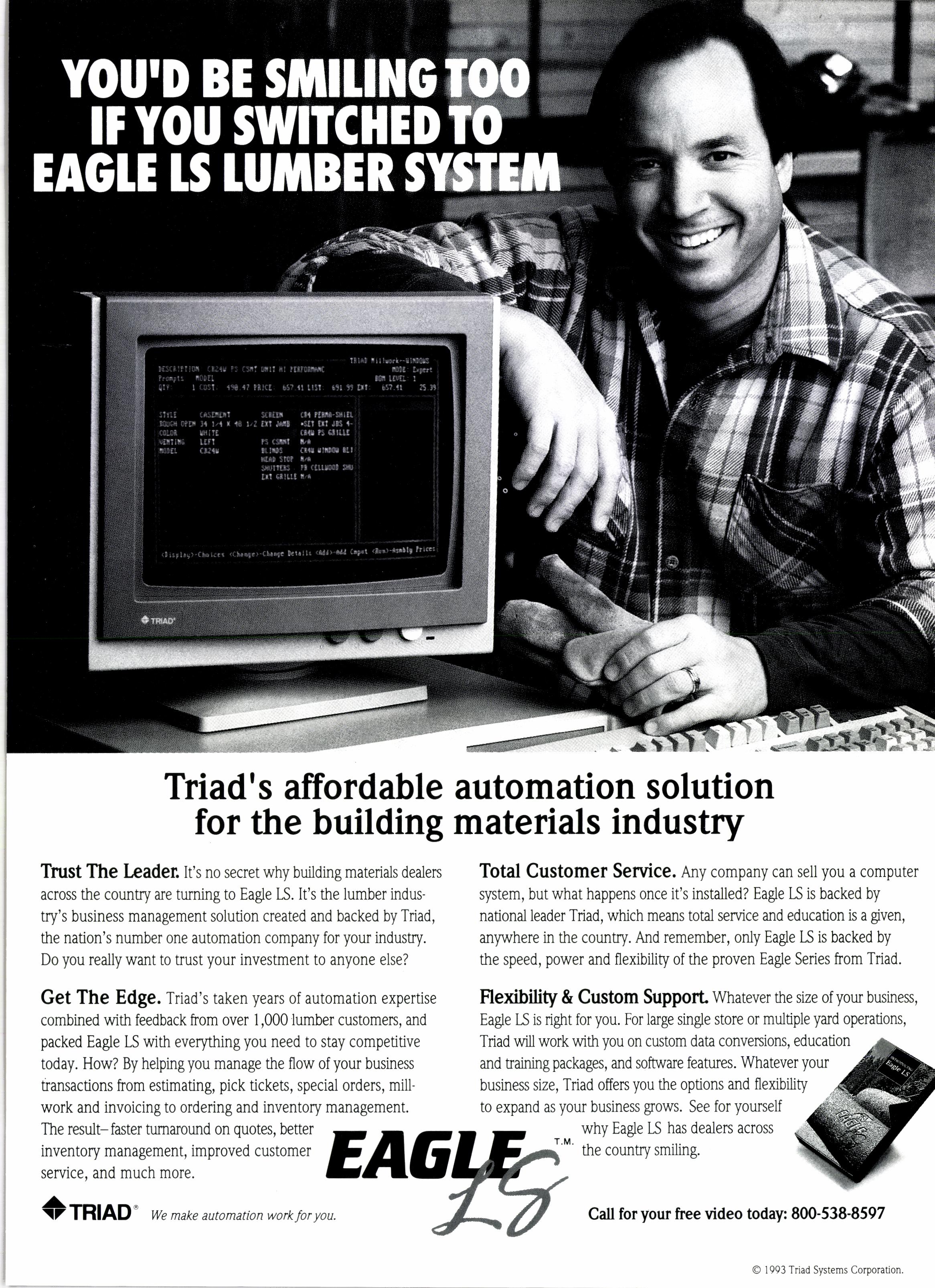
1 minute read
Triad's affordable automation solution for the building materials industry
Trust The kaden It's no secret why building materials dealers acros the country arc tuming to Eagle LS. It's the lumber industry's business management solution created and backed by Triad, the nation's number one automation company for your industry. Do you really want to uust your investment to anyone else?
Get The Edge. Triad's taken years of automation expertise combined with feedback from over l,000lumber customers, and packed Eagle LS with everything you need to stay competidve today. How? By helpingyou manage the flow of your business transactions from estimating, pick tickets, special orders, millwork and invoicing to ordering and inventory management.
The result- faster tumaroun
Total Customer Service. Any company can sell you a computer system, but what happens once it's installed? Ea$e LS is backed by national leader Triad, which means total service and education is a given, anywhere in the country. And remember, only Ea$e LS is backed by the speed, power and flexibilily of the proven Eagle Series from Triad.
Flexibility & Custom Suppott
Whatever the size of your busines, Ea$e I5 is right for you. For luge sin$e store or multiple yud operations, Triad will work with you on custom data convenions, education and training packages, and software features. Whatever your business size, Triad offers you the options and flexibiliff to expand as your business grows. See for yourself
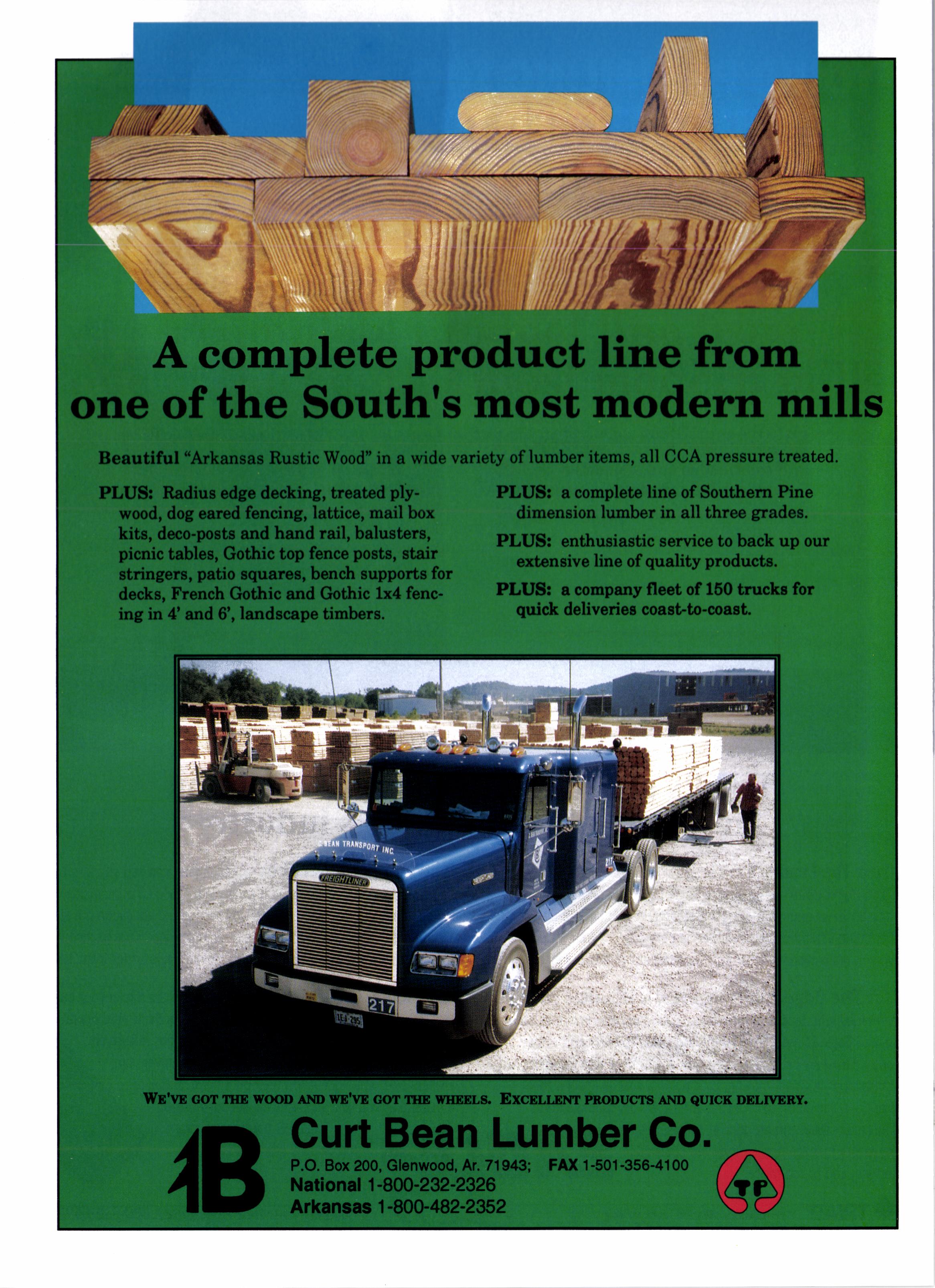
\lll1ilT"H:"","fil,i3l,l?:f i?i;
invenlory, lien rigbts, billing and their 900 vehicles was a constantly arduous, detail-intensive, potentially error and aspirin-filled nightmare for building material supplier Rinker Materials. That is, until their computers learned to talk. to each other.
The West PaIm Beach, Fl., based fimr distributes a variety of building materials, including drywdl, concrete block, ready mix and aggregate. They have many locations because, as the state's largest cement distributor, they ship most of their products by mixer truck. The products must arrive at the jobsite within 90 minutes, so time is everything.
Previously all customer tickets and other information generated in the field had been hand-written. The paperwork was taken back to tle plant and then sent to a district office, where it was input into the computer and finally sent on to the main office. Then, billing and other data processing could fmally be done.
Five years ago, Rinker realized its need for automation. They selected a networking software package and
Story at a Glance
Linking computers at multiple locations and on vehicles ... custom designed localand wide area systems keep logistics manageable.