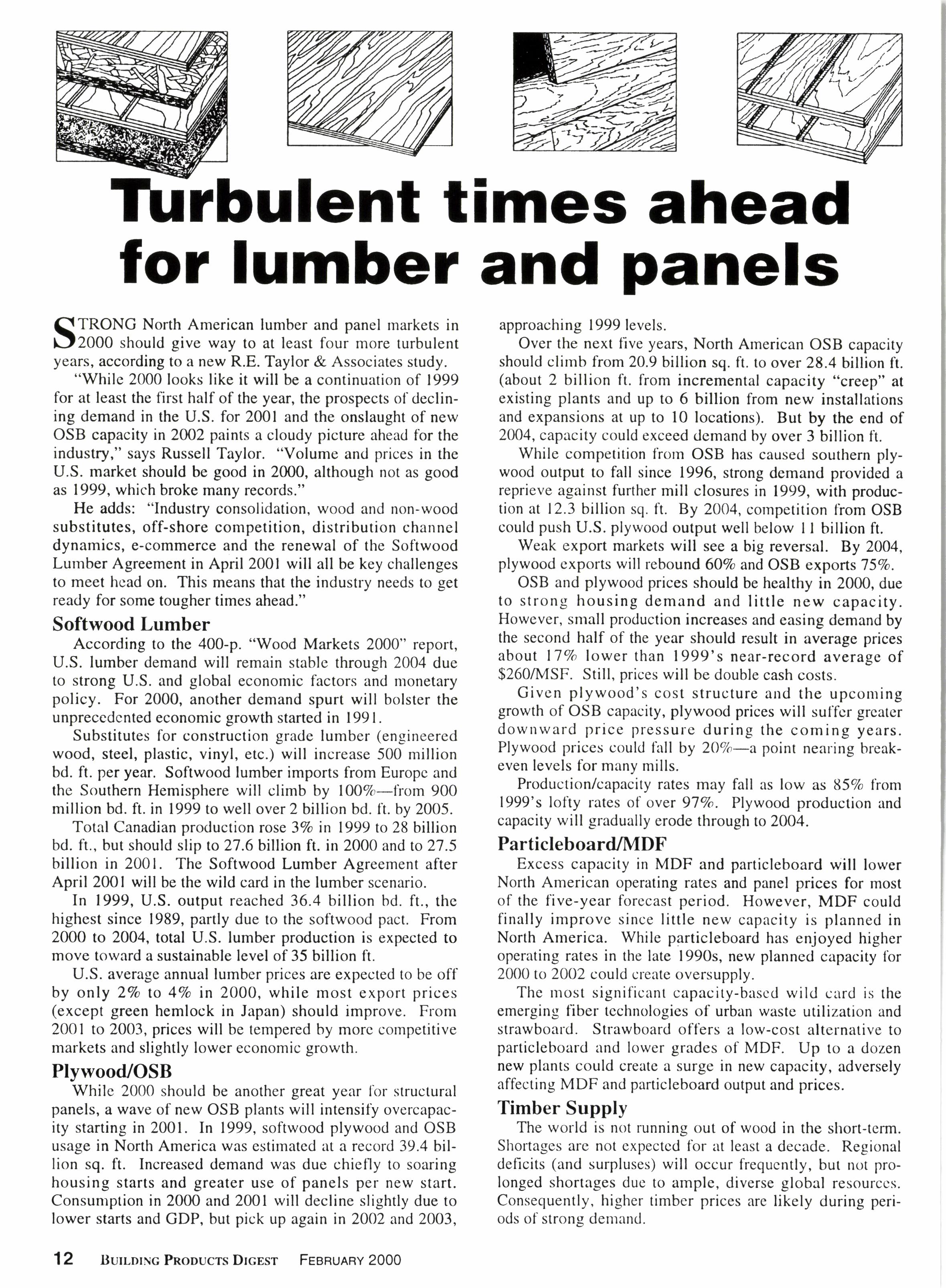
4 minute read
rbulent times ahead for lumber and panels
(]TRONG North American lumber and panel markets in |J2000 should sive wav to at least four more turbulent years, according tlo a n"* R.E. Taylor & Associates study.
"While 2000 looks like it will be a continuation of 1999 for at least the first half of the year, the prospects of declining demand in the U.S. for 2001 and the onslaught of new OSB capacity in2OO2 paints a cloudy picture ahead fbr the industry," says Russell Taylor. "Volume and prices in the U.S. market should be good in 2000, although not as good as 1999, which broke many records."
He adds: "Industry consolidation, wood and non-wood substitutes, off-shore competition, distribution channel dynamics, e-commerce and the renewal of the Sofiwood Lumber Agreement in April 2001 will all be key challenges to meet hcad on. This means that the industry needs to get ready for some tougher times ahead."
Softwood Lumber
According to the 400-p. "Wood Markets 2000" report, U.S. lumber demand will remain stable through 2004 due to strong U.S. and global economic factors and nronetary policy. For 2000, another demand spurt will bolster the unprecedcnted economic growth started in 199 l.
Substitutes for construction grade lumber (engineered wood, steel, plastic, vinyl, etc.) will increase 500 million bd. ft. per year. Softwood lumber imports from Europc and the Southern Hemisphere will climb by IOOVo-from 900 million bd. ft. in 1999 to well over 2 billion bd. fi. by 2005.
Total Canadian production rose 3Vo in 1999 to 28 billion bd. ft., but should slip to 27.6 billion ft. in 2000 and to 27.5 billion in 2001. The Softwood Lumber Agreement after April 20Ol will be the wild card in the lumber scenario.
In 1999, U.S. output reached 36.4 billion bd. ft., the highest since 1989, partly due to the softwood pact. From 2000 to 2004, total U.S. lumber production is expected to move toward a sustainable level of 35 billion ft.
U.S. average annual lumber prices are expected to be off by only 2Vo to 4Vo in 2000, while most export prices (except green hemlock in Japan) should improve. From 2001 to 2003, prices will be tempered by morc cornpetitive markets and slightly lower economic growth.
Plywood/OSB
While 2000 should be another great year lbr structural panels, a wave of new OSB plants will intensify overcapacity starting in 2001. In 1999, softwood plywood and OSB usage in North America was estirnated at a record 39.4 billion sq. ft. Increased demand was due chiefly to soaring housing starts and greater use of panels per new start. Consunrption in 2000 and 2001 will decline slightly due to lower starts and GDP, but pick up again in 2002 and 2003, approaching 1999 levels.
Over the next five years, North American OSB capacity should clirnb from 20.9 billion sq. ft. to over 28.4 billion ft. (about 2 billion ft. from incremental capacity "creep" at existing plants and up to 6 billion from new installations and expansions at up to l0 locations). But by the end of 2004, capacity could exceed demand by over 3 billion fl.
While competition fiorn OSB has caused southern plywood output to fall since 1996, strong demand provided a reprieve against further mill closures in 1999, with production at 12.3 billion sq. ft. By 2004, competition fiom OSB could push U.S. plywood output well below I I billion ft.
Weak export markets will see a big reversal. By 2004, plywood exports will rebound 6OVo and OSB exports 757o. OSB and plywood prices should be healthy in 2000, due to strong housing demand and little new capacity. However, snrall production increases and easing demand by the second half of the year should result in average prices about lTVo lower than 1999's near-record average of $260/lvISF. Still, prices will be double cash costs.
Given plywood's cost structure and the upconring growth of OSB capacity, plywood prices will sut'for greater downward price pressure during the coming years. Plywood prices could fall by 2oo/o-a point nearing breakeven levels for many mills.
Production/capacity rates may fall as low as 857o fiom 1999's lotiy rates of over 9'7Vo. Plywood production and capacity will gradually erode through to 2004.
Particleboard/MDF
Excess capacity in MDF and particleboard will lower North American operating rates and panel prices for most of the five-year forecast period. However, MDF could finally improve since little new capacity is planned in North America. While particleboard has enjoyed higher operating rates in the late 1990s, new planned capacity lbr 2000 to 2002 could create oversupply.
The rnost significtrnt capacity-bascd wild card is the emerging fiber technologies of urban waste utilization and strawboard. Strawboard offers a low-cost alternative to particleboard and lower grades of MDF. Up to a dozen new plants could create a surge in new capacity, adversely affecting MDF and particleboard output and prices.
Timber Supply
The world is not running out of wood in the short-term. Shortages are not expectcd fbr at least a decade. Regional deficits (and surpluses) will occur frequcntly, but not prolonged shortages due to ample, diverse global resourccs. Consequently, higher timber prices are likely during periods of strong denrand.
fN THE last l0 years. medium denlsitv fiber has established itself as a staple among timber processing companies. The international MDF market is estimated to expand this year to a total consumption of 72 million ft., virtually triple the amount produced in 1993.
According to a recent Wood Moulding & Millwork Producers Association member survey, use of MDF continues to increase, especially in the paint grade market-despite the resultant increase in demand for fiber, tightening supply of MDF board and rising board prices.
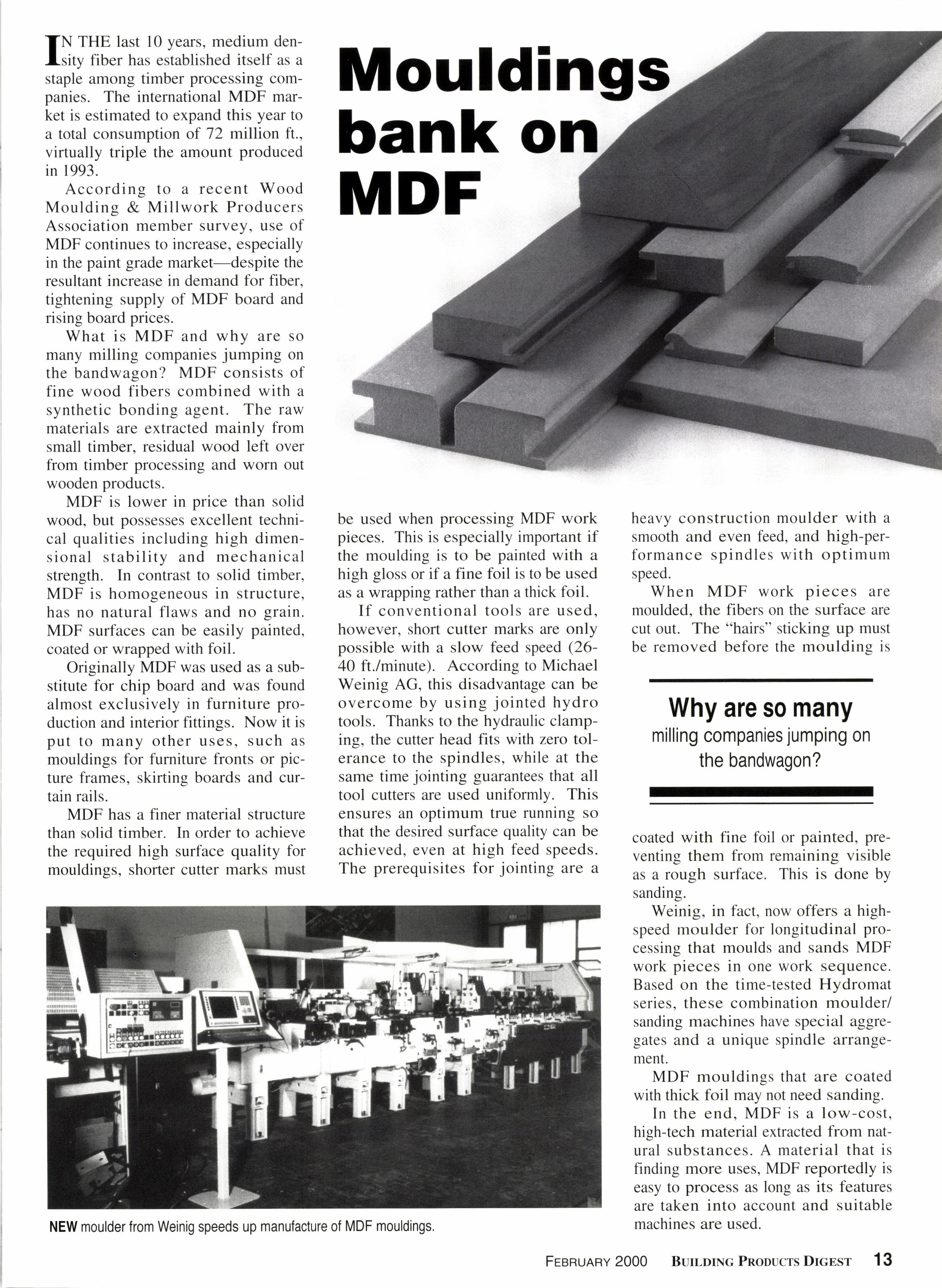
What is MDF and why are so many milling companies jumping on the bandwagon? MDF consists of fine wood fibers combined with a synthetic bonding agent. The raw materials are extracted mainly from small timber, residual wood left over from timber processing and worn out wooden products.
MDF is lower in price than solid wood, but possesses excellent technical qualities including high dimensional stability and mechanical strength. In contrast to solid timber, MDF is homogeneous in structure, has no natural flaws and no grain. MDF surfaces can be easily painted, coated or wrapped with foil.
Originally MDF was used as a substitute for chip board and was found almost exclusively in furniture production and interior fittings. Now it is put to many other uses, such as mouldings for furniture fronts or picture frames, skirting boards and curtain rails.
MDF has a finer material structure than solid timber. In order to achieve the required high surface quality for mouldings, shorter cutter marks must