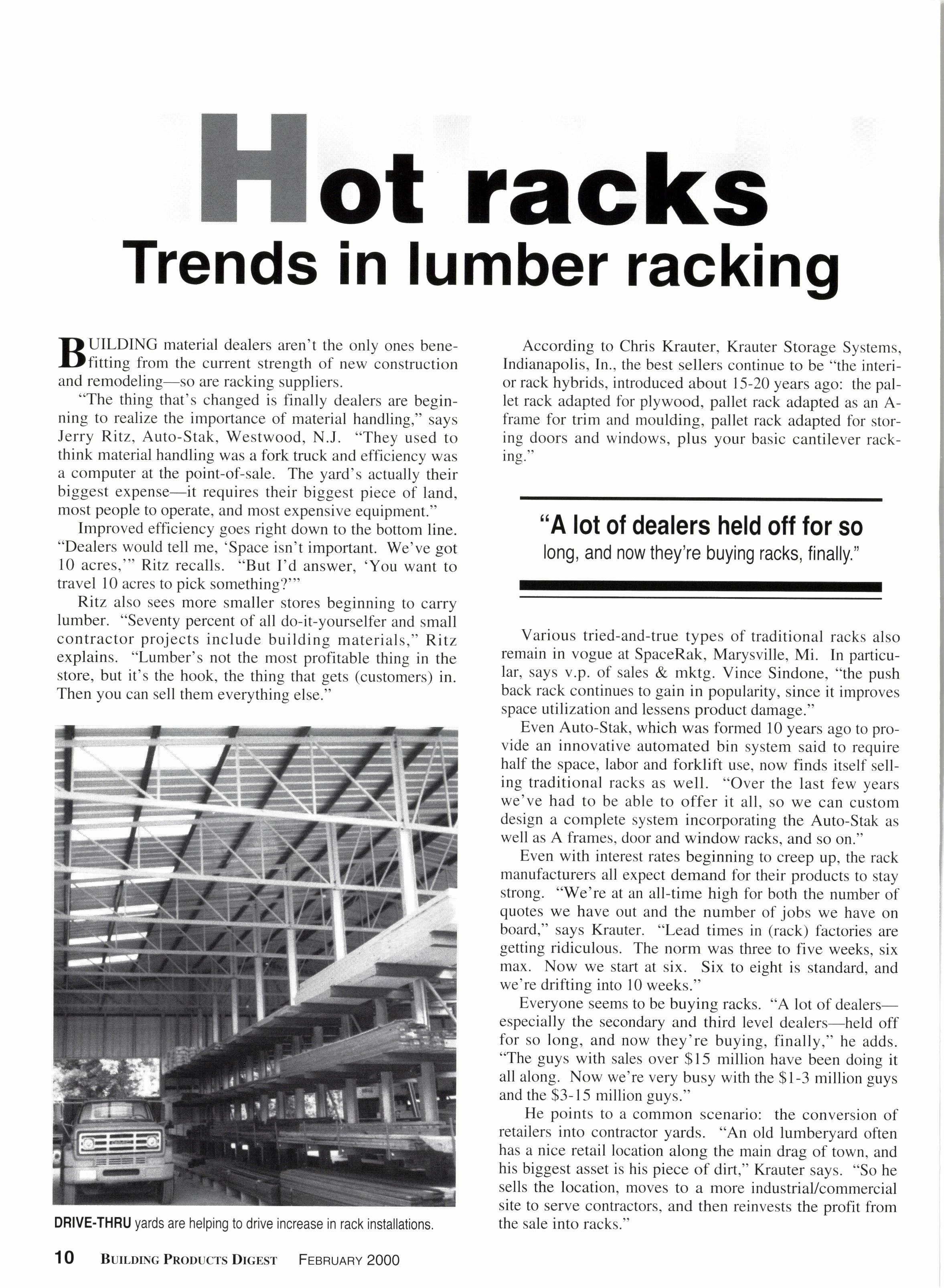
4 minute read
Hot racks Trends in lumber racki ng
D UILDfNG material dealers aren't the only ones beneI-Dfitting from the current strength of new construction and remodeling-so are racking suppliers.
"The thing that's changed is finally dealers are beginning to realize the importance of material handling," says Jerry Ritz, Auto-Stak, Westwood, N.J. "They used to think material handling was a fork truck and efficiency was a computer at the point-of-sale. The yard's actually their biggest expense-it requires their biggest piece of land, most people to operate, and most expensive equipment."
Improved efficiency goes right down to the bottom line. "Dealers would tell me, 'Space isn't important. We've got 10 acres,"' Ritz recalls. "But I'd answer, 'You want to travel l0 acres to pick something?"'
Ritz also sees more smaller stores beginning to carry lumber. "Seventy percent of all do-iryourselfer and small contractor projects include building materials," Ritz explains. "Lumber's not the most profitable thing in the store, but it's the hook, the thing that gets (customers) in. Then you can sell them everything else."
According to Chris Krauter, Krauter Storage Systems, Indianapolis, In., the best sellers continue to be "the interior rack hybrids, introduced about l5-20 years ago: the pallet rack adapted for plywood, pallet rack adapted as an Aframe for trim and moulding, pallet rack adapted for storing doors and windows, plus your basic cantilever racking."
Various tried-and-true types of traditional racks also remain in vogue at SpaceRak, Marysville, Mi. In particular, says v.p. of sales & mktg. Vince Sindone, "the push back rack continues to gain in popularity, since it improves space utilization and lessens product damage."
Even Auto-Stak, which was formed l0 years ago to provide an innovative automated bin system said to require half the space, labor and forklift use, now finds itself selling traditional racks as well. "Over the last few years we've had to be able to offer it all, so we can custom design a complete system incorporating the Auto-Stak as well as A frames, door and window racks, and so on."
Even with interest rates beginning to creep up, the rack manufacturers all expect demand for their products to stay strong. "We're at an all-time high for both the number of quotes we have out and the number of jobs we have on board," says Krauter. "Lead times in (rack) factories are getting ridiculous. The norm was three to five weeks, six max. Now we start at six. Six to eight is standard, and we're drifting into l0 weeks."
Everyone seems to be buying racks. "A lot of dealersespecially the secondary and third level dealers-held off for so long, and now they're buying, finally," he adds. "The guys with sales over $15 million have been doing it all along. Now we're very busy with the $l-3 million guys and the $3- l5 million guys."
He points to a common scenario: the conversion of retailers into contractor yards. "An old lumberyard often has a nice retail location along the main drag of town, and his biggest asset is his piece of dirt," Krauter says. "So he sells the location, moves to a more industriaVcommercial site [o serve contractors, and then reinvests the profit from the sale into racks."
VOUR DECKING customers can |. now stack their decks entirely with plastic components-right down to the understructure.
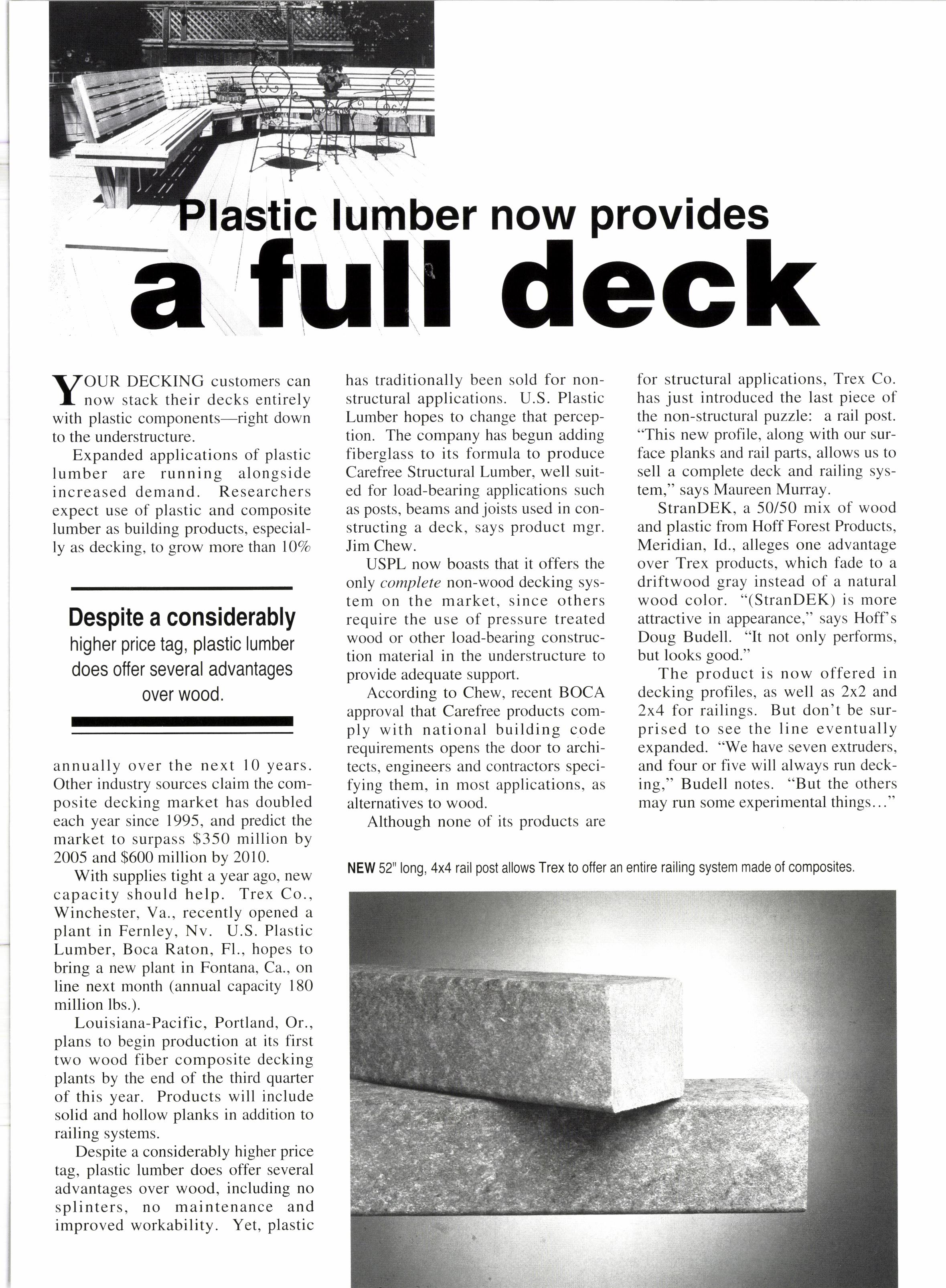
Expanded applications of plastic lumber are running alongside increased demand. Researchers expect use of plastic and composite lumber as building products, especially as decking, to grow more than l07o annually over the next 10 years. Other industry sources claim the composite decking market has doubled each year since 1995, and predict the market to surpass $350 million by 2005 and $600 million by 2010.
Despite a considerably higher price tag, plastic lumber does offer several advantages over wood.
With supplies tight a year ago, new capacity should help. Trex Co., Winchester, Va., recently opened a plant in Fernley, Nv. U.S. Plastic Lumber, Boca Raton, Fl., hopes to bring a new plant in Fontana, Ca., on line next month (annual capacity 180 million lbs.).
Louisiana-Pacific, Portland, Or., plans to begin production at its first two wood fiber composite decking plants by the end of the third quarter of this year. Products will include solid and hollow planks in addition to railing systems.
Despite a considerably higher price tag, plastic lumber does offer several advantages over wood, including no splinters, no maintenance and improved workability. Yet, plastic has traditionally been sold for nonstructural applications. U.S. Plastic Lumber hopes to change that perception. The company has begun adding fiberglass to its formula to produce Carefree Structural Lumber, well suited for load-bearing applications such as posts, beams and joists used in constructing a deck, says product mgr. Jim Chew.
USPL now boasts that it offers the only complete non-wood decking system on the market, since others require the use of pressure treated wood or other load-bearing construction material in the understructure to provide adequate support.
According to Chew, recent BOCA approval that Carefree products comply with national building code requirements opens the door to architects, engineers and contractors specifying them, in most applications, as alternatives to wood.
Although none of its products are for structural applications, Trex Co. has just introduced the last piece of the non-structural puzzle: a rail post. "This new profile, along with our surface planks and rail parts, allows us to sell a complete deck and railing system," says Maureen Murray.
StranDEK, a 50/50 mix of wood and plastic from HoffForest Products, Meridian, Id., alleges one advantage over Trex products, which fade to a driftwood gray instead of a natural wood color. "(StranDEK) is more attractive in appearance," says Hoff's Doug Budell. "It not only performs, but looks good."
The product is now offered in decking profiles, as well as 2x2 and 2x4 for railings. But don't be surprised to see the line eventually expanded. "We have seven extruders, and four or five will always run decking," Budell notes. "But the others may run some experimental things..."