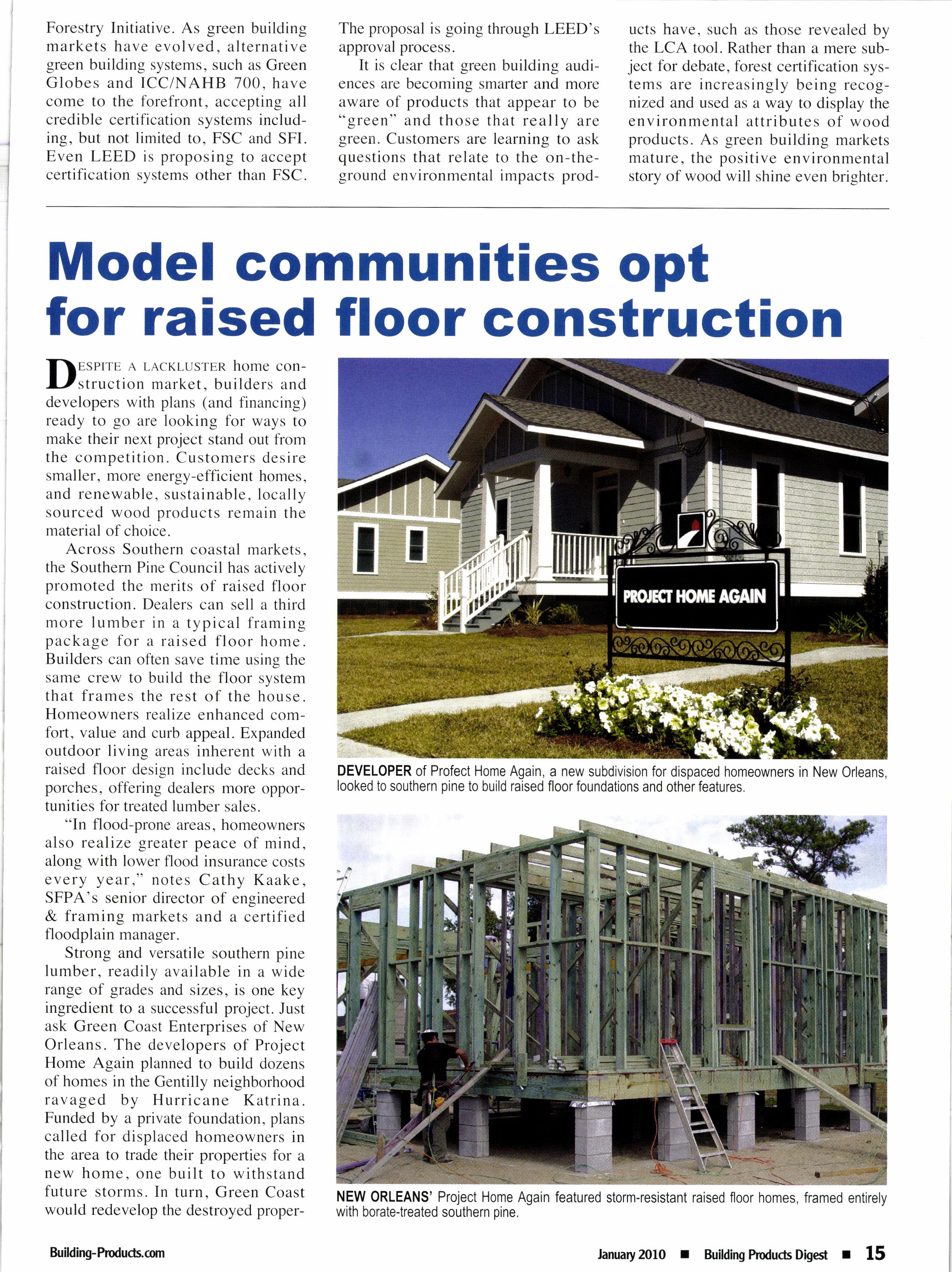
1 minute read
Model communities opt for raised floor construction
hesptre A LACKLUSTEn home conI-lstruction market, builders and developers with plans (and financing) ready to go are looking for ways to make their next project stand out from the competition. Customers desire smaller, more energy-efficient homes, and renewable, sustainable, locally sourced wood products remain the material of choice.
Across Southern coastal markets, the Southern Pine Council has actively promoted the merits of raised floor construction. Dealers can sell a third more lumber in a typical framing package for a raised floor home. Builders can often save time using the same crew to build the floor system that frames the rest of the house. Homeowners realize enhanced comfort, value and curb appeal. Expanded outdoor living areas inherent with a raised floor design include decks and porches, offering dealers more opportunities for treated lumber sales.
"In flood-prone areas, homeowners also realize greater peace of mind, along with lower flood insurance costs every year," notes Cathy Kaake, SFPA's senior director of engineered & framing markets and a certified floodplain manager.
Strong and versatile southern pine lumber, readily available in a wide range of grades and sizes, is one key ingredient to a successful project. Just ask Green Coast Enterprises of New Orleans. The developers of Project Home Again planned to build dozens of homes in the Gentilly neighborhood ravaged by Hurricane Katrina. Funded by a private foundation, plans called for displaced homeowners in the area to trade their properties for a new home, one built to withstand future storms. In turn, Green Coast would redevelop the destroyed proper- ties into replacement homes for others wanting to return.
Following consultations with architect John Schakai and the SFPA staff, plans for elevated, steel-framed homes soon transformed into raised woodframed structures. Pressure treatment with borates was added to all structural components as a long-term defense against termites and decay. Twenty attractive homes were built in twelve weeks. Each home f'eatures porches front and rear. Phase two of the project is moving into building more raised homes on exchanged lots throughout Gentilly. This effort continues to attract local publicity, inspiring other builders and property owners to investigate a raised floor home as an affordable, floodplain-friendly alternative to slab construction on a mound of fill.
Builders are getting creative, too, learning ways to reduce foundation costs in a raised home. Again, wood is the answer. Treated wood pilings used in place of grade beams and concrete block piers have greatly reduced the cost and time required to complete a new home. Phase two of Project Home Again is using treated piling exclusively for its new homes, typically completing the foundation and framing in just four to five days.
In the Baton Rouge area, architect Kevin Harris and developer Jeff