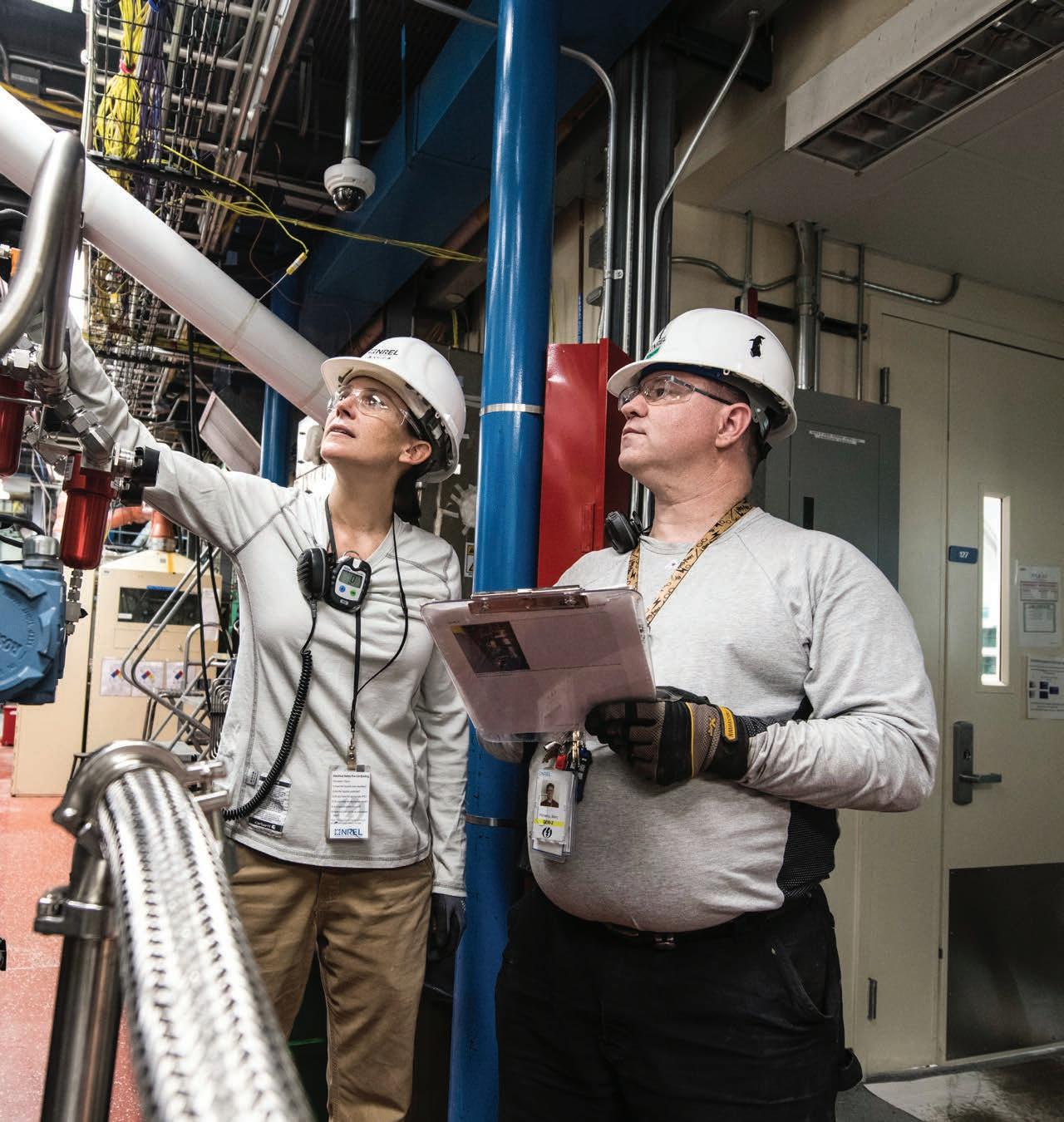
5 minute read
Can Your Operation Pass a Safety Inspection?
Can Your Operation Pass a Safety Inspection?
The word “inspection” is often associated with stress or fear – especially in manufacturing. Surprise inspections can be frustrating and alarming, particularly if any violations result in fines or a temporary stop in production. You do not need to fear inspections if you are always prepared. But, of course, safety measures are not just necessary for passing inspections and avoiding penalties. It is ultimately about creating a safe space for workers, especially in light of new COVID-19 safety precautions as employees are returning to work.
To create a safe environment for everyone, supervisors and managers must pay careful attention to areas that create safety hazards in the workspace. Many safety risks undoubtedly exist in the brushware manufacturing industry related to machinery and other components.
Here are some simple steps to take that will ensure your shop is always up to code and safe for all workers.
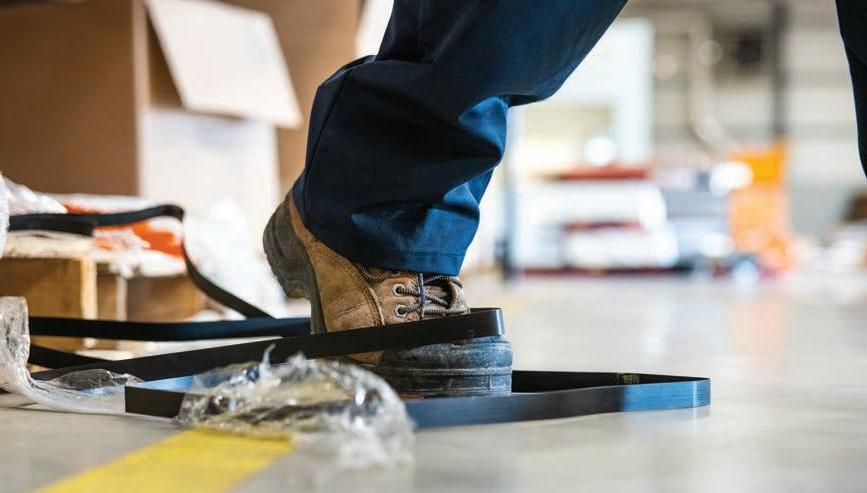
By Troy Clark
1. Address the Common Violations First
First, it is important to understand the safety violations that are present in most manufacturing plants. According to OSHA, the most cited compliance issues in the manufacturing industry include:
• Machine guarding: failing to inspect machinery and/or install proper machine guard techniques to prevent injuries.
• Lockout/Tagout (LOTO) system: not following the proper LOTO protocol and failing to label dangerous substances correctly.
• Hazard communication: failing to enforce hazard communication standards.
• Respiratory protection and personal protective equipment (PPE): not providing adequate respiratory and protection equipment for employees.
• Walking and working surfaces: not maintaining cleanliness.
Many of these safety violations are closely tied to common injuries or even work fatalities in manufacturing. Therefore, it is important to pay close attention to the areas that are commonly hit with violations, including workplace cleanliness, PPE availability, machine maintenance and hazard signage.
2. Check Safety Training Certifications
Another area often overlooked is keeping up with safety training, especially for supervisors and machine operators. In many manufacturing companies, safety training is only offered during orientation and is rarely revisited.
However, a study published by the CDC found a direct correlation between the amount of safety training offered at a business and the number of work injuries. Companies that provided more comprehensive training courses, particularly specialized classes for specific machinery or tasks, had fewer injuries and accidents.
In addition to general health and safety courses, additional training should be offered on subjects like:
• First Aid and CPR
• Record Keeping
• Hazard Communications
• Electrical Safety
• Material Handling
• Hazard Awareness
Safety training must be taken seriously, and all concepts should be enforced by supervisors and managers to instill a culture that prioritizes these standards. It is also important that all certification records are kept up-to-date and that safety courses are offered frequently for all employees.
3. Consider Employee Safety Concerns
It is critical to consider factors that impact your employee’s day-today life.
Take the air quality of the workplace, for instance. Manufacturing can create a lot of dust, debris, vapors and unpleasant odors in the air. Over time, this can be quite taxing on people’s health. There is even evidence that air quality impacts people’s productivity levels.
Another safety issue often overlooked in manufacturing is overworking employees. When employees are overworked, they are more prone to making mistakes, which could cause major safety issues. Be sure that employees are given adequate break times and are not overscheduled.
And finally, consider other factors that could be impacting employee productivity and health, such as the temperature of the workplace, bathroom cleanliness and water availability.

4. Look for Patterns
First, it is key to keep a record of all accidents and safety incidents that occur. These documents are not just important for insurance and legal purposes – they can also shed a light on safety violations or hazards that may not be blatantly clear. Supervisors and managers should be checking incident reports to identify patterns with specific machines, employees or certain situations. This could be a sign of issues that need resolution.
Another solution for identifying hidden hazards is to ask for feedback and suggestions from the employees themselves. Oftentimes, managers are completely unaware of less noticeable issues that employees have to deal with regularly. Workers may also have valuable ideas for solutions that can make the workplace safer and even more efficient.
Conclusion
Merely passing safety inspection should not be the main goal for identifying and resolving safety hazards in the workplace. The purpose of fixing these issues should be to protect employees and to support a more efficient workplace.
Safety inspections are designed to set specific regulations that manufacturing plants need to abide by to ensure the utmost safety standards. By paying attention to common violations, providing adequate safety training programs and focusing on the work experience for employees, the brushware industry can become far safer and, ultimately, better.
Troy Clark is the owner of MSC Safety Solutions, a developer of safety training programs designed to achieve and maintain a wellinformed workforce, from top management to field personnel. He has worked for more than 20 years in the safety industry, specializing in construction and general industry policy development, behavioralbased safety, fall protection and safety management. –brm
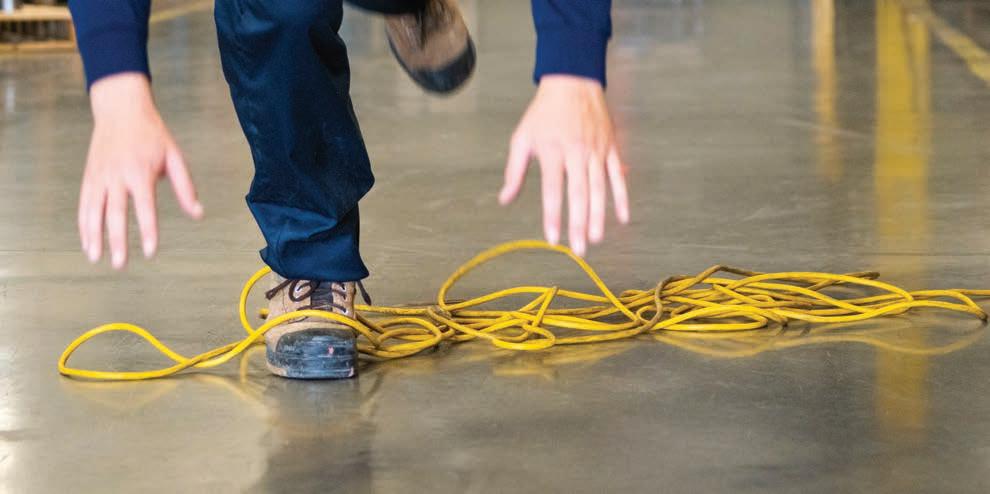
Additional Information
Machine Guarding
OSHA’s website page on machine guarding notes that moving machine parts have the potential to cause severe workplace injuries, such as crushed fingers or hands, amputations, burns or blindness. Safeguards are essential for protecting workers from these preventable injuries. Any machine part, function or process that may cause injury must be safeguarded. When the operation of a machine or accidental contact injure the operator or others in the vicinity, the hazards must be eliminated or controlled. Visit the webpage: https://www.osha.gov/machine-guarding
Lockout/Tagout
Lockout/tagout refers specifically to procedures used to ensure that equipment is shut down and inoperable until maintenance or repair work is completed. It requires that hazardous energy sources be “isolated and rendered inoperative” before work is started on the equipment in question. The isolated power sources are then locked and a tag is placed on the lock identifying the worker who placed it. The worker then holds the key for the lock, ensuring that only he or she can remove the lock and start the machine. This prevents accidental startup of a machine while it is in a hazardous state or while a worker is in direct contact with it. OSHA’s LOTO page: https://www.osha.gov/control-hazardous-energy