
12 minute read
COMPARISONS
“But we also want to make sure that once the contract is entered into there is some mechanism where, in case rates increase, the partners are compensated for the higher rates and in case the rates decrease our clients receive the benefit of the lower rates.”
That, Varghese said, “leads us into a question about how the industry can move into a conversation where freight is considered a commodity, not as something that you buy upfront and fixed for a fixed duration and without any relief, regardless of market shifts.” This in turn leads to a conversation about whether there is merit in indexlinking certain freight rates, reaching an environment where base rates are valid for three months, six months, or whatever is mutually agreed. “We want to discuss practical issues in terms of looking at a particular index or a particular methodology in terms of a fair and balanced engagement. This allows the shipping lines to increase their earnings when the market goes up and not be disadvantaged because they’ve given a rate with a three-year validity within which the market had an uptick.”
Different Sectors, Different Parameters
The long lead time for projects makes EPC freight-related planning much more difficult. A manufacturer selling, for example, pharmaceutical goods, has a reasonable projection about demand – they know how they convert into containers, they know where they’re being shipped from, and therefore they can make a plan. “But in an EPC environment, by the time we award a contract, half the purchase orders may not be awarded, and we just don’t know whether these are going to come from Mexico, China, India, Europe or other locations,” Varghese said.
Therefore, in a lumpsum environment, he noted that the risk of cost escalation is purely on the EPC companies; so is the opportunity to reduce cost and maintain profitability. However, when an EPC is spending its client’s money, it needs to show how it is protecting their interests and maintain complete transparency, accountability and auditability in terms of how the freight procurement works.
“The whole conversation is about how we as an industry start focusing on execution rather than having commercial discussions with one disgruntled party in the equation pretty much all the time. We are also clear that if there is a move from the industry to embrace an index-linked mechanism, it should also be in effect during all cyclical movements of freight, not just during the stage where rates are falling, but also when rates are rising.
“This is a two-way street that should embrace fairness and risk sharing, focused on execution,” Varghese said.
Creating indices is something that research consultancy Drewry Shipping Consultants is no stranger to. In 2011 it created the World Container Index, which focuses on container rate trends. The World Container Index, or WCI, reports actual spot container freight rates for major East-West container trade routes. It consists of eight routespecific indices representing individual shipping routes. All indices are reported in U.S. dollar per 40-foot container. The WCI is a composite of the eight route indices weighted for volume on each of the route’s representative trade. Volume is expressed in million twentyequivalent-units. Data for the index is collected from transport intermediaries – freight forwarders and NVOCCs – based in Europe, North America and Asia. These organizations report the freight rates on which they are moving cargo with a number of major shipping lines. Drewry also publishes benchmark spot container freight rates on over 700 lanes in its Container Freight Rate Insight and provides beneficial cargo owners with contract rate benchmarking services via its Benchmarking Club, as well as airfreight rate indices in its Sea and Air Shipper Insight. Drewry also publishes a Multipurpose Time Charter Index which is updated monthly and is free to access on the company’s web site.
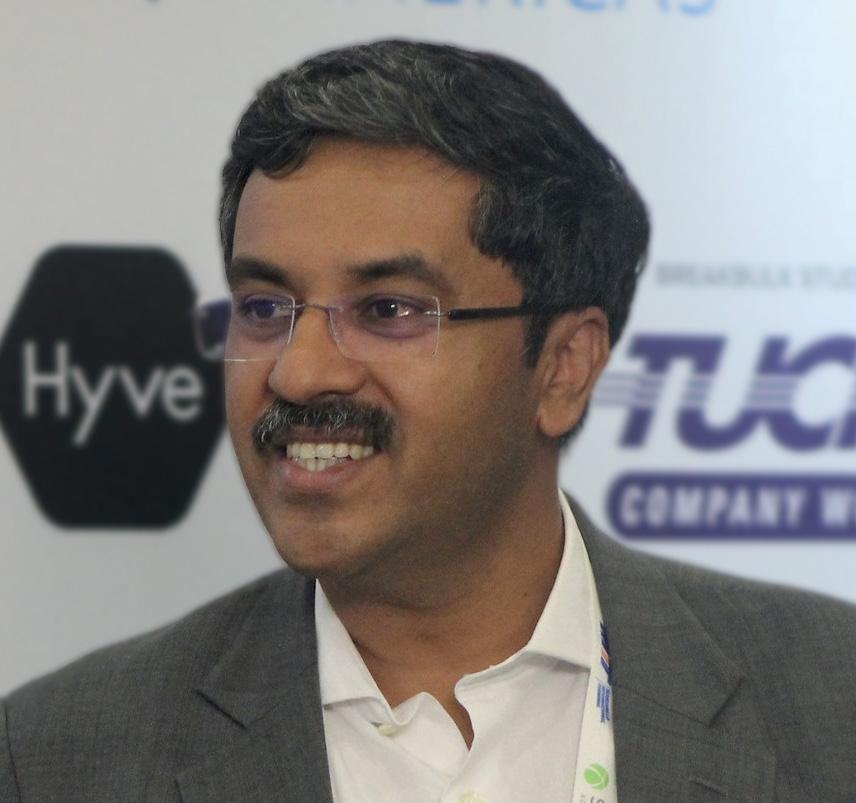
Lack of Standardization
However, applying the same approach to the multipurpose vessel sector could be tricky. Speaking to Breakbulk, Dr Ferenc Pasztor, deputy head of research for Drewry, said it is a “challenging sector” for which to create an index. For the WCI and other Drewry freight rate indices, it created a list of port pairs - which total several hundred and are audited monthly by an auditing group. This group sacrifices internal information in return for improved transparency in the overall market. “Despite the fact that the unit of cargo is standardized, it still requires substantial effort to maintain the indices due to the high number of stakeholders involved in the process and the various surcharges that usually come with the cost of transporting a 40-foot container.” he said.
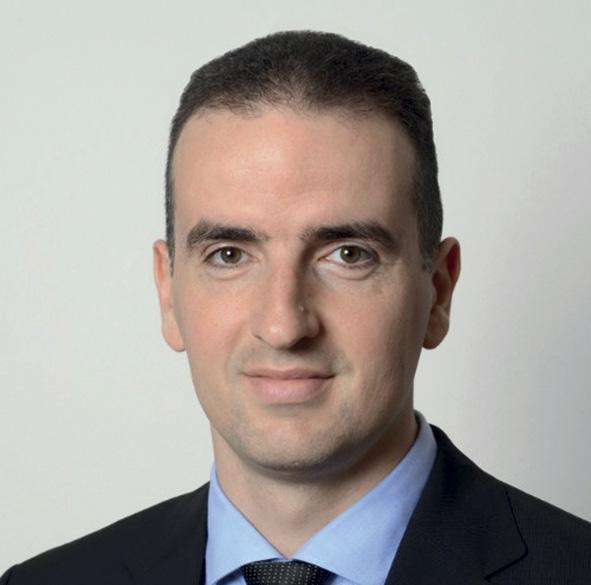
The first stumbling block with an MPV freight rate index is a lack of standardization. Pasztor explained that in terms of process, the first step would be to set up a list of different cargoes, the typical breakbulk and project cargo items. Step two is to list the port pairs for each cargo –“that will be another long list for each item.” Step three is to then get a committee or audit group together.
“People in the industry would be happy to use a reliable freight rate index but so far seemed reluctant to take the initiative and then put the effort into it in the long term.” Pasztor said. There is also the regulatory side to consider. Anti-trust regulations might be an issue, so an independent body would need to lead the process.
Returning to the issue of standardization, he explained that spot freight rates on certain routes might be significantly different between carriers depending on the utilization of their vessels and the competition for cargoes, which complicates indexing.
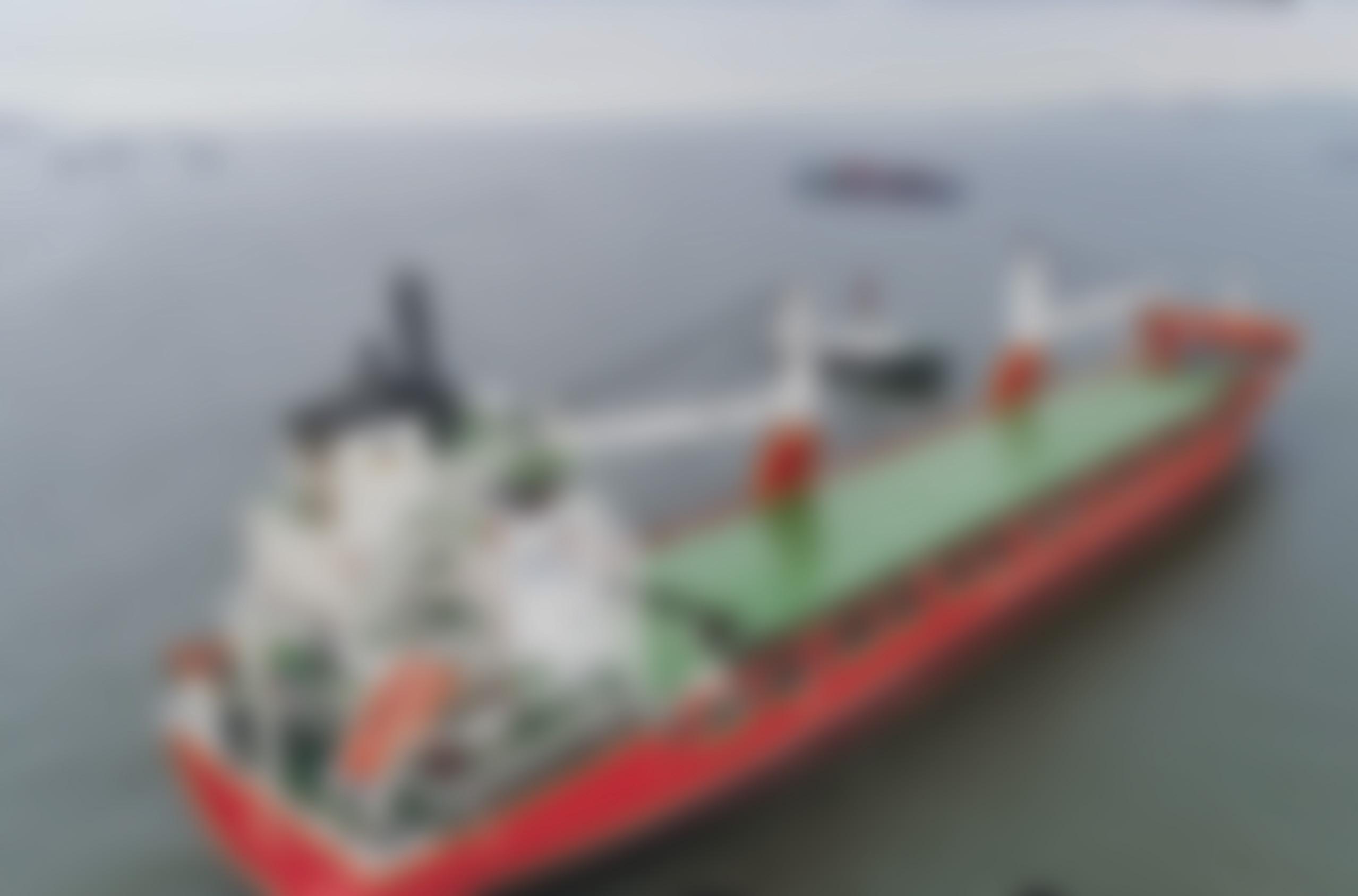
Pasztor felt that for an MPV freight rate index to be successful the beneficial cargo owners/EPCs might have to catalyze it and it would need to revolve around a few select cargo types where size and weight per unit are not too diverse. “If a sufficient number of EPCs were willing to share information confidentially through a neutral third party, such as Drewry, to an agreed set of parameters, a credible index could be created,” Pasztor said.
Carly Fields has reported on the shipping industry for the past 23 years, covering bunkers and broking and much in between.
The International Sustainability Standards Board, or ISSB, has made reporting of Scope 3 emissions mandatory from 2023. This, along with other mandates and internal targets, is putting increased pressure on breakbulk and project cargo businesses to tighten up their greenhouse gas calculation and reporting – with mixed results so far. The process could add to costs but should also increase the preference for low carbon transport options.
As the deadlines for international, national, and corporate net zero and other interim GHG emissions’ targets gets closer, more companies are falling under regulatory calculation and reporting obligations, especially in Europe – where remaining emissions will eventually translate to financial penalties, unless they are removed. Scope 3 emissions include indirect emissions from
Region: Global Problem: Emissions reporting has increased in complexity with 3PLs now mandated to report to shippers
Solution: Forwarders have found novel ways to report to give them an edge over emissions counting laggards transport and supply chains, as well as emissions “embedded” in acquired materials and assets, which are normally associated with raw material extraction and manufacture.
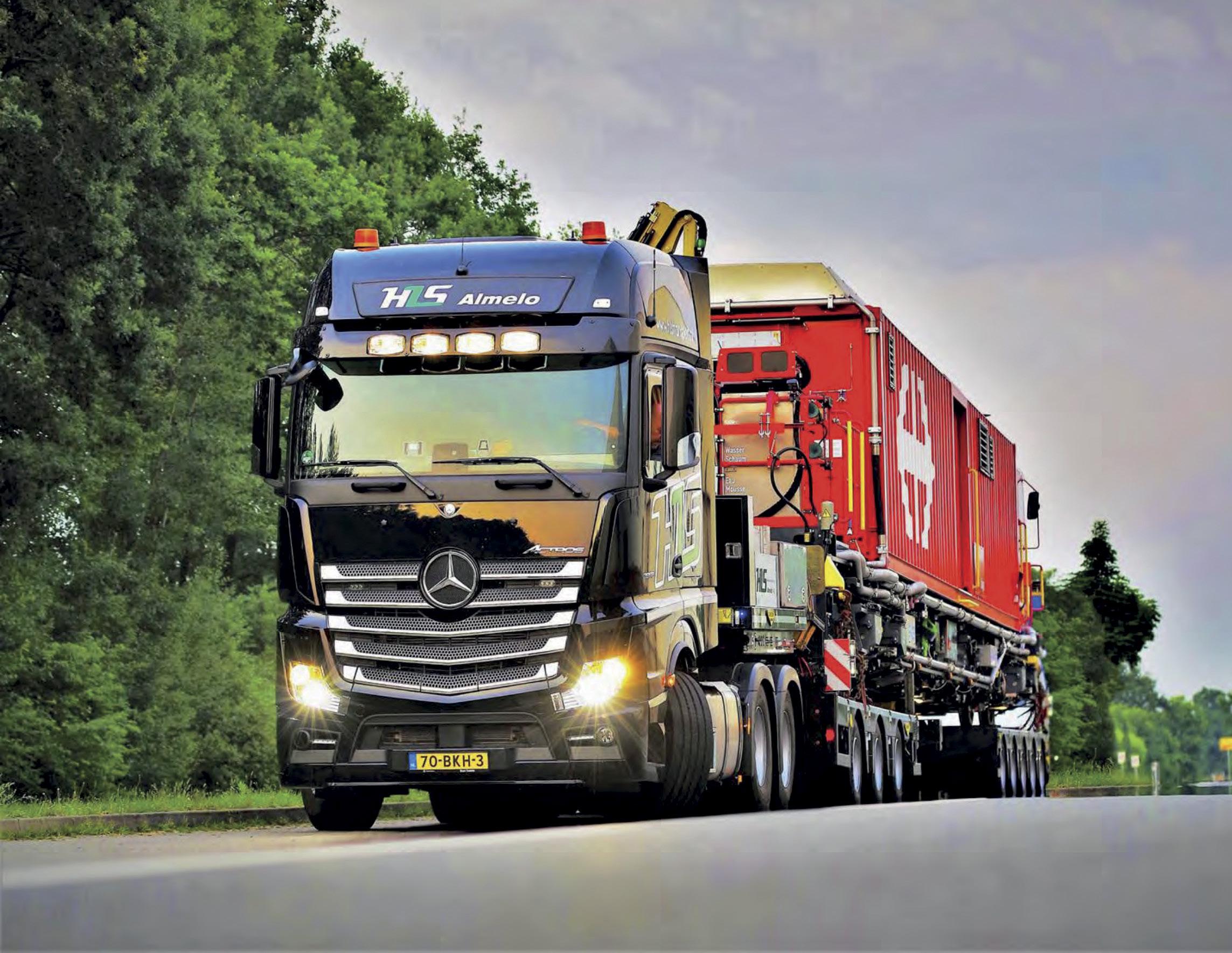
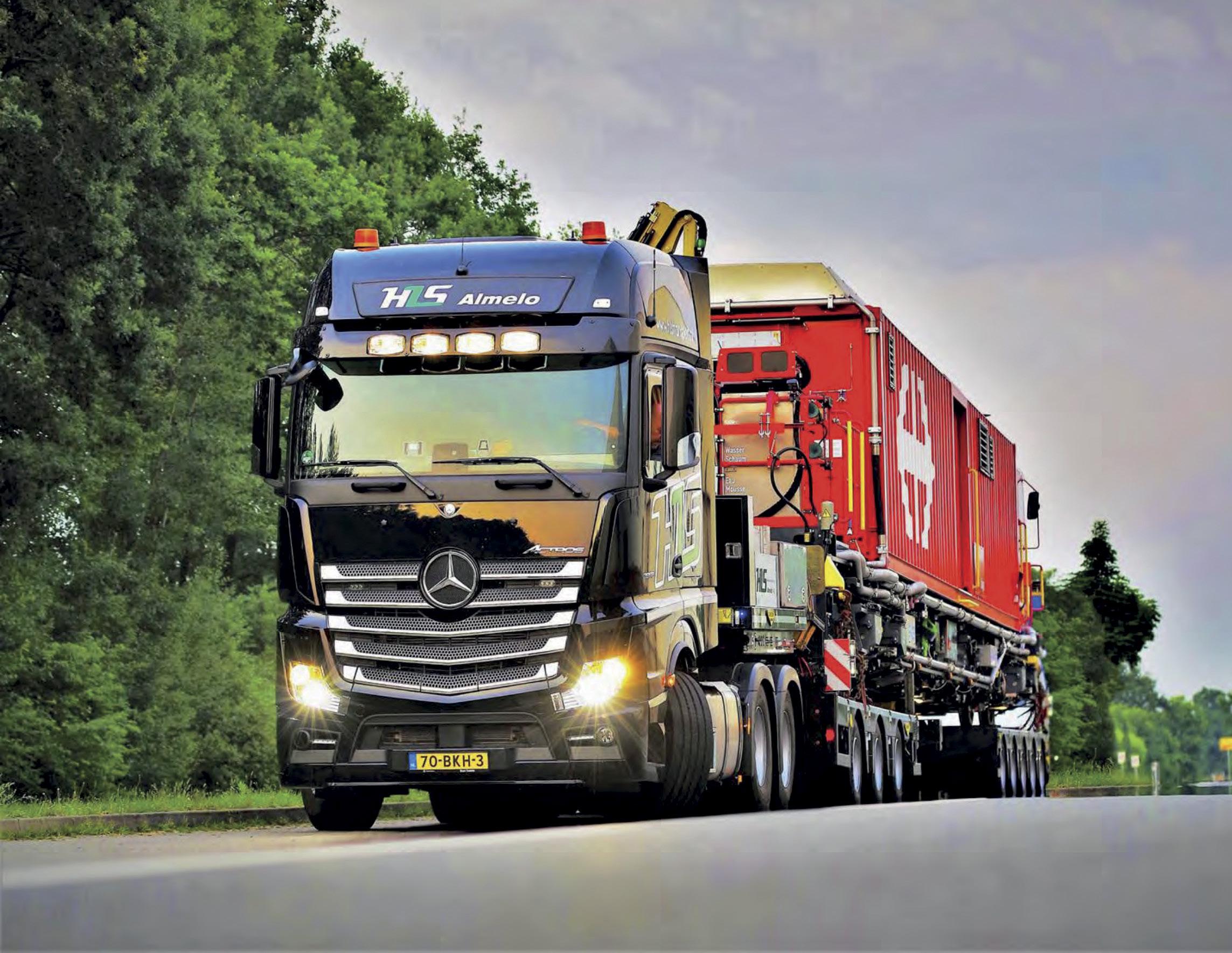
This means most of the direct Scope 1 (and Scope 2 in the case of electric propulsion) emissions of those involved with the transport of breakbulk and project cargo are the Scope 3 emissions of their clientsthe manufacturers and producers of breakbulk and project cargoes. Air transport is more emission-intense than road, with seaborne cargo the least polluting, although there are significant variations between subsectors – as well as variations depending on equipment, energy type and operational efficiency.
The need to gather external data means the Scope 3 reporting process is much more complex than Scope 1 & 2 reporting. In recognition of this, the ISSB’s decision to impose mandatory Scope 3 reporting came alongside relief provisions to help companies apply the new requirements. But while the ISSB’s move has added to pressure to report, Alan Lewis, technical director at the Smart Freight Centre, said to Breakbulk it was far from the only motivation, with pressure also coming from the EU, International Maritime Organization, and other external bodies, as well as internal corporate targets.
Wide Variation in Reporting
So far, however, the pressure to report Scope 3 does not yet appear to have extended to the logistics providers themselves within the breakbulk sector, but only to the manufacturers and other breakbulk/project cargo users. Ton Klijn, director of ESTA, told Breakbulk that “[Our members] are not yet required to report Scope 3 data… Our Scope 1 & 2 data is our clients’ Scope 3 data, so as they need to report that data, we have to provide it.” available and will also be under direct pressure to lower these. Under new EU rules, decided in March 2023, freight and vessel operators will be required to cut GHG intensity by 2 percent from 2025, 6 percent from 2030, 14.5 percent from 2035, 31 percent from 2040, 62 percent from 2045 and 80 percent from 2050, against 2020 baselines. The IMO has more modest global targets. “We are in a transition phase at the moment. The timetable is already laid out –depending on the size of companies. Some are required to report now, and all will be within seven years,” Klijn said.
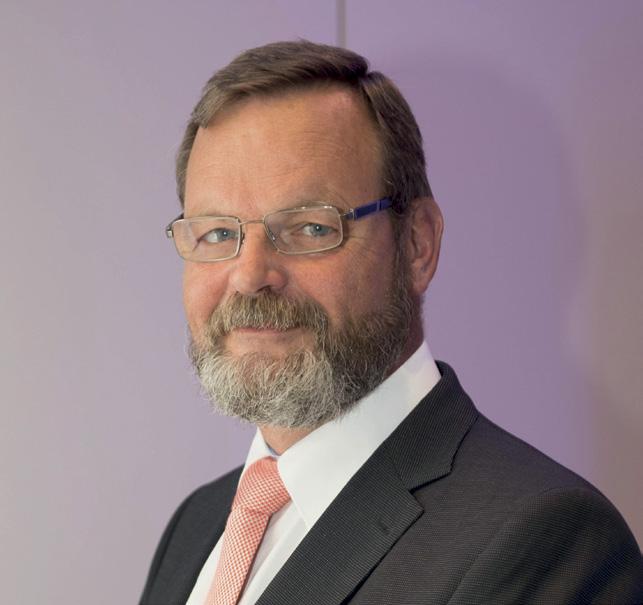
Scope 3 reporting by logistics firms would involve assessing any GHGs used in the manufacture of the transport they use, such as ships, lorries and planes, and in the extraction of the materials that went to make up those assets. Failure to report Scope 3 here means recycled materials, green energy involved in manufacture or extraction and assets that function as part of a circular economy in the sector will not be flagged or rewarded/penalized.
Klijn added that there was a widely varying take-up of Scope 1 & 2 reporting among carriers, with some reluctant and unaware of what data is required, especially outside Europe. He said it was very much a “top-down approach, with big companies first,” with some in Europe, such as Mammoet, already including the data in their annual report. He expected this would trickle down to smaller companies.
Indeed, in Europe the larger transport companies are facing their own Scope 1 & 2 targets, so will have to have the data
As many freight forwarders and third-party logistics firms are generally asset light, they will need to get the information from the shipping lines, truckers, railroads, and air freighters that they contract to move the shipper’s - their client’s - cargo. And those carriers may not know exactly which ship, truck, or plane will be available at the time of booking vs the time of execution of the project. The result is a need to mix projections based on modelling and extrapolation of past performance with reporting that is based as much as possible on actual data about vessel, load and fuel consumption – a trend that is advancing elsewhere, especially in road transport.
Global Differences
Outside Europe the picture is murkier. Dennis Devlin of Maersk, which has its own internal carbon reduction targets, in the U.S., said most carriers don’t “seem especially keen about [reporting emissions] because it may put many of them at a disadvantage sometimes. Many of the ships in the fleet are old and emit quite a lot... breakbulk and heavylift carriers will follow the lead of the container carriers, and (again, my view) move reluctantly and when pushed to do so (which clients/shippers are doing).”
If adequate data is not yet available from logistics providers, SFC’s Lewis said it was possible to supplement the data with modelling to give best estimates. The key to this is to use the best possible information and a common, accepted methodology such as ISO 14083 and the GLEC Framework to ensure you’re comparing like with like. Faced with mandatory Scope 3 reporting – in Europe at least – and the threat of tougher regulations to follow, many of the major project cargo manufacturers and breakbulk producers are beginning to ask for Scope 1 & 2 information from those involved in breakbulk logistics. 4D Supply Chain Consulting President and Global Head, Thomas Skellingsted, noted that this was inevitable, as “non-compliance with reporting requirements will lead to huge penalties, impacting the bottom line. This, in turn, will affect the competitiveness of companies.”
4D Supply Chain Consulting said some of its clients had increased their requests for carbon emission information, but that many were not yet prepared. “It is apparent that although [our clients] are generally aware of the requirement, there is a lack of in-depth understanding of how they can help to deliver the required reports,” Skellingsted said. He added that while top management may be aware, this had often not yet filtered down into the company, leaving many without a process to calculate Scope
3 emissions. “There is also a lack of sustainability goals incorporating the Scope 3 reporting and its associated actions to reduce GHG emissions.”
Lewis added that clients were beginning to require reporting for their Scope 3 calculations as a condition of use. “Others are now requesting that carriers calculate and report but are not (yet) using the information in their own processes – the main purpose of this is to raise awareness, understanding and ownership in preparation for future requirements,” he added.
Major engineering, procurement and construction companies and project cargo shippers have started an initiative through the SFC to push project and breakbulk carriers to commit to some form of Scope 3 reporting. Discussions have been underway for a while based on the GLEC Framework, according to Lewis. The approach is reflected in the recently published ISO14083 that covers GHG emission accounting and reporting for both freight and passenger transport. “More and better quality reporting is happening as each year passes,” he said.
Public Contracts Set the Scene
ESTA’s Klijn said most of his member companies first run into the mandatory emissions reporting issue when they quote for state or municipality jobs, as these entities are under direct political pressure to decarbonize. “So, any government contractors will ask for the data from our members,” and in some cases, it will influence whom they award a job to. North European companies also tend to be in the vanguard of demanding clients, he added.
In the long run, only companies that work to these stricter standards will qualify for public contracts. He noted that Europe was far ahead in this aspect. Lewis added that this should put more pressure on breakbulk and project cargo businesses to tighten up their GHG calculation and reporting, so they can effectively answer the inevitable questions that will come from more of their customers and external reporting platforms.

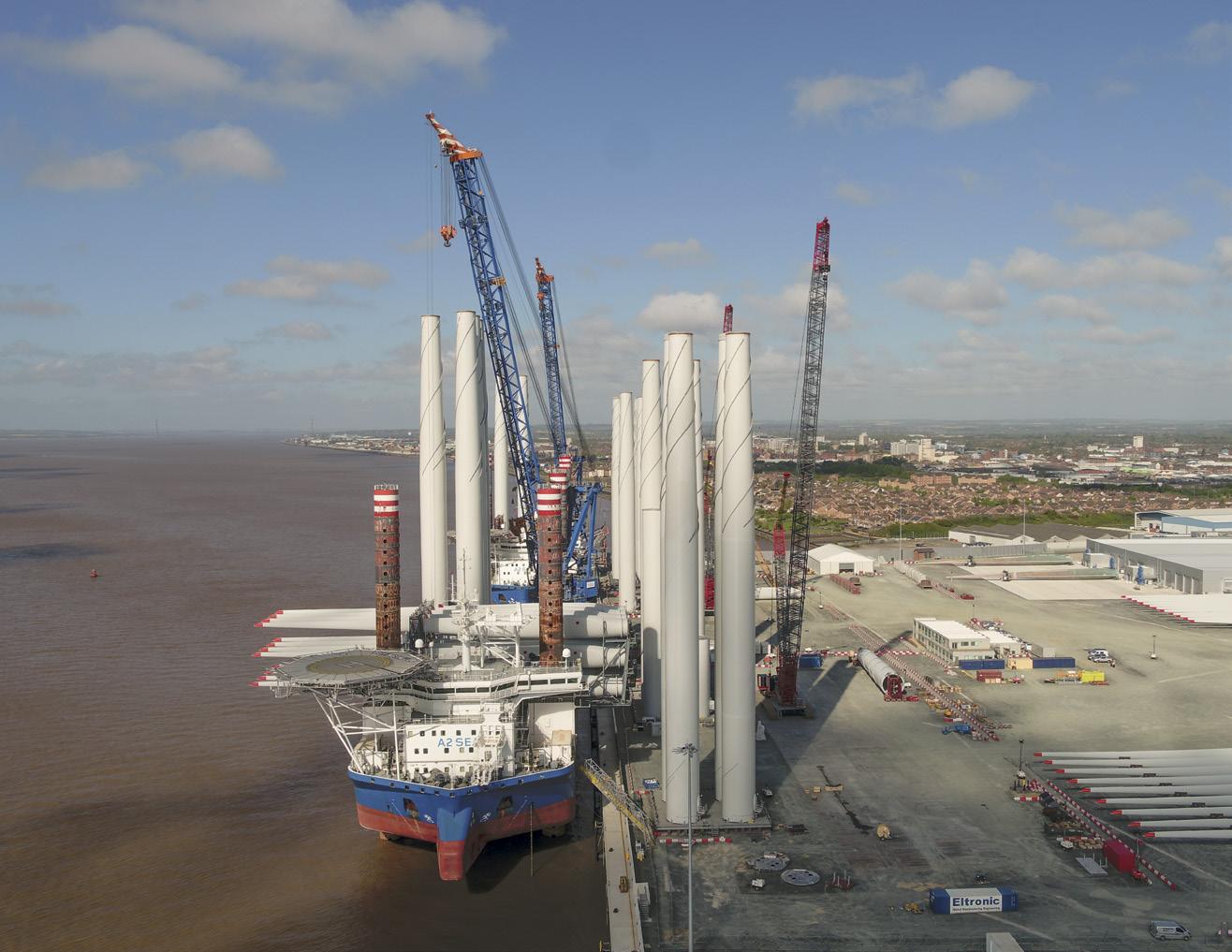
Several companies and organizations are helping facilitate the Scope 3 reporting process by developing emissions calculators. Among these is 4D, which (in addition to reporting its own Scope 1 & 2 emissions) is developing “a sustainability product” to aid its clients’ reporting. Its emissions calculations are based on origin, destination and routing, mode of transportation and cargo weight. Comparisons can be made, and the results used to develop new lower emissions transport strategies.
Focusing on heavy road transport, ESTA is also introducing a CO2 calculator. “Gearing it around heavy transport and the machines that are typically used makes it easier for our members… You can compare different options – surprisingly, sometimes many small trucks emit less than one big one,” Klijn said. He added that lower CO2 options were normally more expensive, while assets with electric plug-in options as an alternative to diesel had an advantage. Once introduced later this year, “the CO2 calculator should also help members with records and auditing if they report consistently.”
Changing Behavior?
So far, however, there is limited evidence that the reporting and pending penalties are actually changing behavior in favor of lower carbon breakbulk transport options. Klijn said some clients were beginning to choose such options, but in the near future, the most that could be expected is that a client “may award a contract to the runner-up bid if it is lower on carbon.” He noted that some cities have already banned diesel, so electric options were now essential in those cases.
Klijn added that as well as greater efficiency through ongoing tightening of European standards, carriers were looking at hydrogen as an alternative to diesel, although a refueling network was still required. “The horizon for hydrogen [use in heavy road vehicles] is between now and five years, certainly by 2030,” he said.
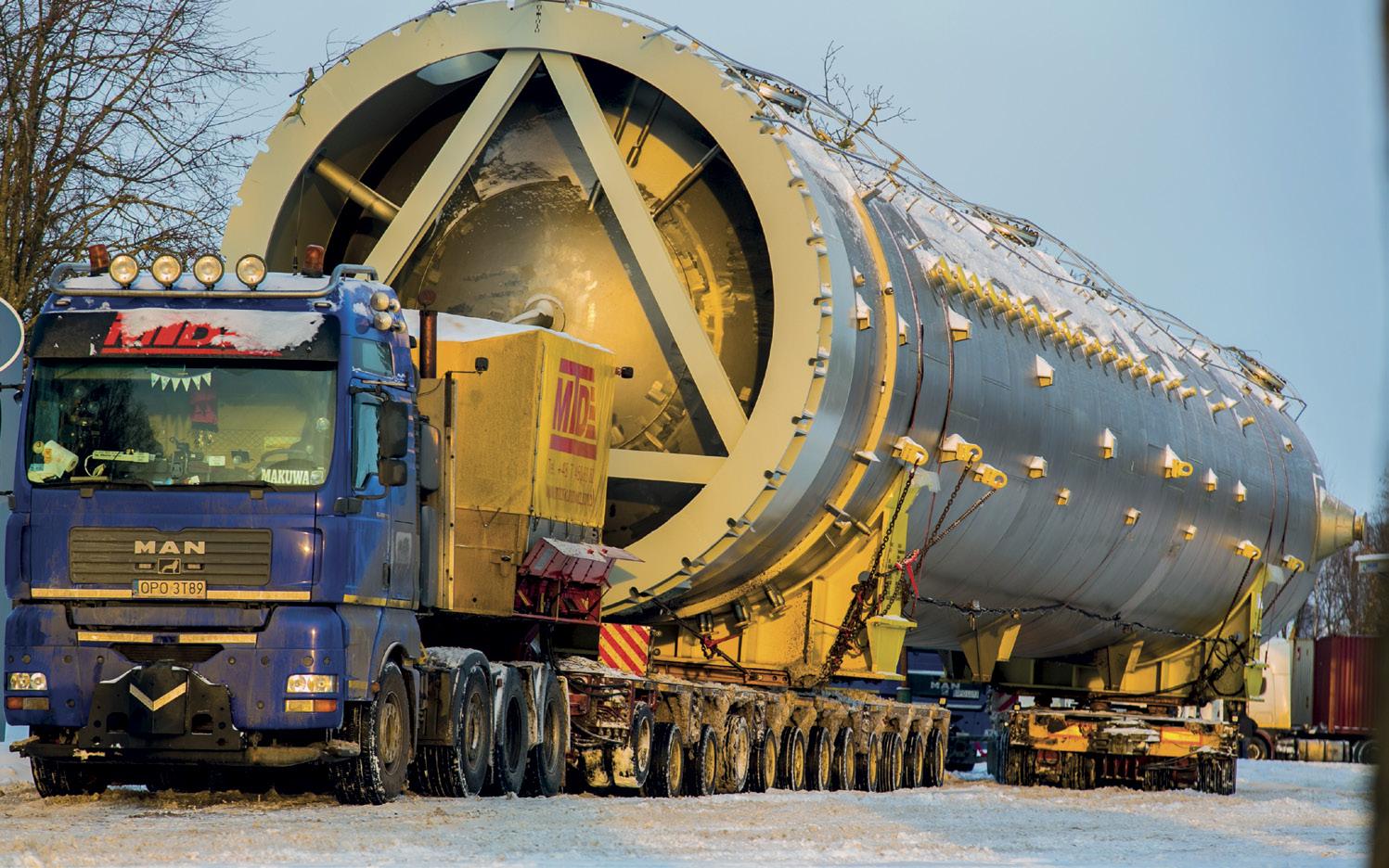
Similarly, big sea freight companies are increasingly ordering vessels fueled with lower carbon options such as LNG and more recently methanol, with ammonia also being considered. Maersk and some other ship operators have set internal net zero targets and are already in the process of reporting and addressing their Scope 1 & 2 emissions.
Mario Hess, global head of customer solutions at deugro, said that in the short term, the requirement to report Scope 3 emissions would probably increase competition among logistics providers as clients sought out providers with lower emissions profiles and solutions in place to report the emissions. “In the longer term, it is likely to become a standard part of doing business, and logistics providers who are able to provide accurate and comprehensive emissions data will have a competitive advantage.”
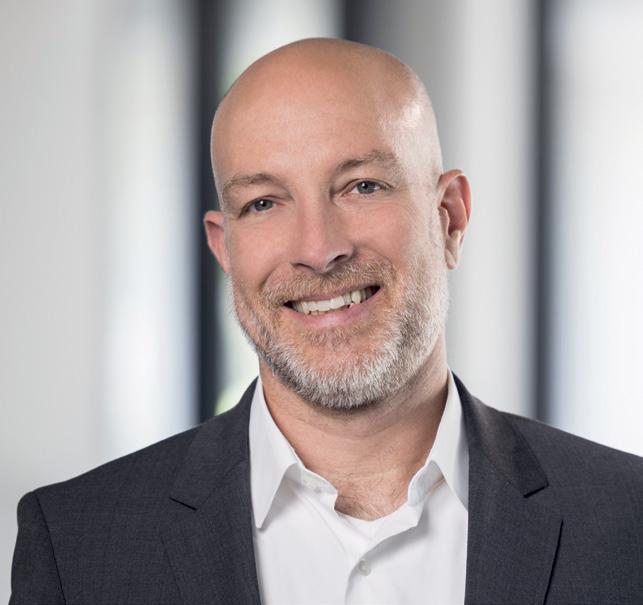
However, reporting is one thing, reducing is another. Klijn said that eventually all involved would have to pay a penalty for emissions – “that’s the only way it’s going to work – it’s no good just saying it’s better for the environment, there has to be a penalty/ financial incentive.”
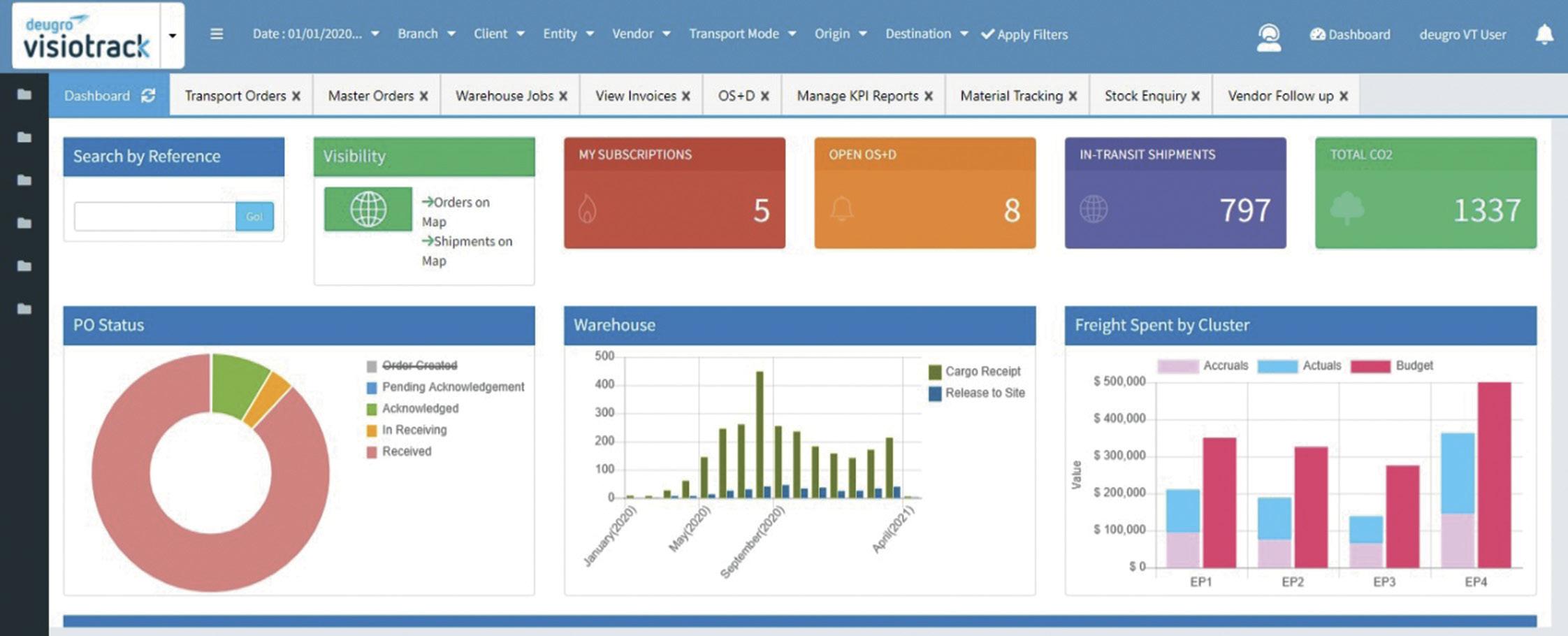