
6 minute read
SUPPORTING THE SEMICONDUCTOR SURGE
Bertling Cargo Move Instrumental to Air Liquide Delivery
With global semiconductor supply chains undergoing unprecedented change, the demand for new manufacturing capacity in developed countries is growing. Freight forwarder and transport specialist Bertling Logistics recently assisted in this shift, delivering two outsized air separator units from the United Arab Emirates to Germany, coordinating complex loading and discharge operations as well as overcoming weather-related challenges along the way.
The project originated when multinational semiconductor contract manufacturing and design company GlobalFoundries began work to upgrade its facility in Dresden, Germany and, having developed a strong relationship with French industrial gases and
Regions: Europe, Middle East Problem: Inclement weather and labor snafus put the brakes on the move of two air separator units
Solution: Quick thinking by the project teams found a replacement ship over the difficult festive period services firm Air Liquide, selected them to supply two air separators for the plant.
“Our client was Air Liquide Electronics,” Enrico Lux, project and key account manager at Bertling Logistics, told Breakbulk. He explained that Bertling teams in Germany and Dubai were ready for the challenge having managed similar transports for Air Liquide in
By Malcolm Ramsay
the past, both from the UAE, and over shorter distances within Europe. The units were manufactured at Air Liquide’s Middle East manufacturing site in Ras Al-khaimah in the north of the UAE. Originally established in 2015, this facility has developed a reputation for fabricating outsized and complex components, including manufacturing the largest cryogenic column ever made by Air Liquide.
Careful Handling
For this project, the heaviest unit was an N2 cold box which weighed over 77 tonnes and measured 27.4 meters in length, 5.2 meters in width and 4.0 meters in height. This highly engineered air separation system was destined to form a major part of the cryogenic equipment for the upgrade of the Dresden plant.
The cargo was manufactured alongside a liquid oxygen (LOx) box that weighed more than 25 tonnes and measured over 21.1 meters in length, 3.9 meters in width, and 4.5 meters in height.
Both items required specialist handling expertise due to their size and the sensitive nature of components involved. For Bertling this meant coordinating detailed pre-planning sessions to define the most efficient and cost-effective route.
Bertling’s Lux explained that the project team in Dubai identified a route by road from the manufacturing site to the port of Jebel Ali, around 140 kilometers away to the south.
To load the breakbulk items at the fabrication site, Bertling relied on a conventional hydraulic axle trailer to move the cold box in 4 + 6 + 8 meter spacer + 8 configuration. The LOx Box was also moved by conventional hydraulic axle trailer, but then in 4 + 14 configuration.
“Both units were loaded at the workshop by trailer hydraulic from stools,” Lux said, and then transported directly by road.
Challenging Headwinds to Overcome
Upon arrival at the port of Jebel Ali, the cargo was then destined for ocean shipment aboard a vessel operated by shipping line CMA CGM. Lux explained that the team selected CMA CGM as ocean carrier for the project as “they offered a feasible solution, and we had had good experiences with them for similar transports in the past.”
From the dock at Jebel Ali, the cargo was loaded directly from the waiting trucks to the vessel’s deck using onsite gantry cranes. While this should have been a relatively straightforward process, the teams faced logistical challenges, as weather conditions at the port had deteriorated significantly by the time operations were scheduled to begin.
“Due to unusually strong winds for the Jebel Ali location — resulting in some very strong gusts — the loading operation was stopped/ rejected by the terminal operator on very short notice,” Lux said, adding that this had numerous knock-on effects for the operations because the rigging was already prepared and the trucks were alongside the vessel before the order came through.
As a result, the vessel was forced to sail without the cargo on board and the team from Bertling were required to redraft their plans at short notice. This happened just days before the end of the year, meaning that many operators and alternative providers were paused or on holiday. “It happened on December 29, and we had to find an intermediate storage solution quickly around new year holidays to get the trucks free,” Lux said, adding that the team finally managed to secure another CMA CGM vessel to take the cargo. The cargoes were then both successfully loaded aboard the suezmax container ship APL Salalah
“The cargo left on the ship in December and then took some time to pass through the Suez Canal and then on to the Mediterranean before finally arriving in Rotterdam, ready to be loaded again,” Sina Burkert, director of engineering at Air Liquide, said.
Founded in 1902, Air Liquide is the second largest supplier of industrial gases in the world and has operations in over 70 countries. Headquartered in Paris, France, the firm employs more than 67,000 staff globally and generated almost €30 billion in revenue in 2022.
Labor Hiccups on River Transport
Having successfully sailed more than six thousand kilometers, the cargoes finally arrived at the Port of Rotterdam where Bertling’s German team began preparations for the last leg of the journey.
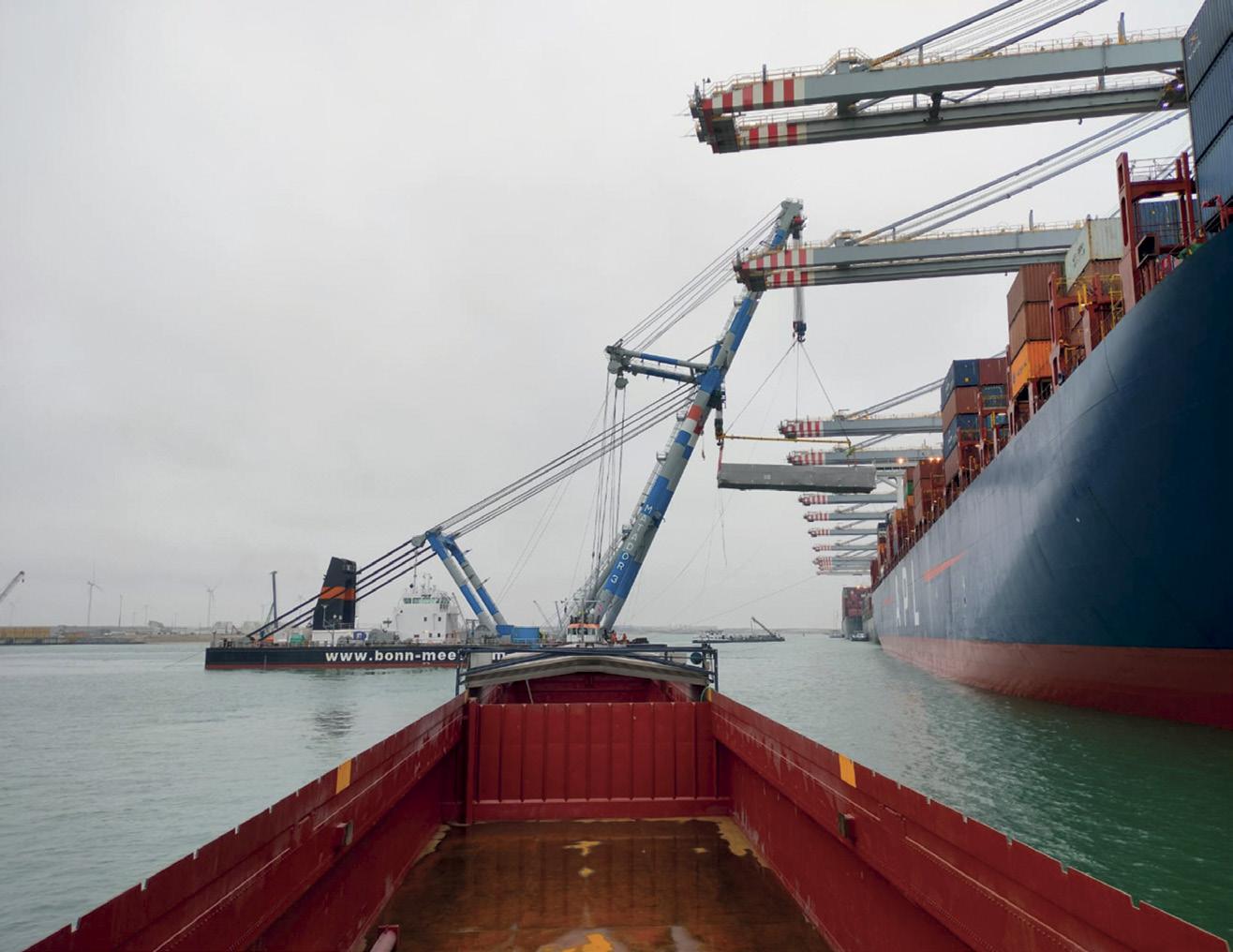
The cargo was discharged directly onto a river barge using a Matador 3 floating crane and, once fully lashed and secured, the barge commenced its journey via inland waterways to Dresden River port, some 800 kilometers to the east.
While this route was free from weather-related issues, the team from Bertling nonetheless faced some challenges during this transport as river workers staged protests over pay and conditions on route through Germany.
“The river barge was blocked for one day on the river Weser due to a warning strike by the Verdi trade union,” Lux said, adding that “the locks were not in operation for a day without any prior notice. As result we had to postpone the unloading operation and road transport in Dresden just four days before the scheduled date.”
This again had knock-on effects for the project, with the team having to adjust the schedule and even having to go so far as rewrite 128 road signs by hand, as the period of validity for the ‘no parking’ signs had changed.
Having finally arrived in Dresden River port, the cargoes were then discharged from the barge onto trucks using crawler and mobile cranes, before the team oversaw delivery to the final destination in Dresden by road.
Lux noted that as the cargoes were discharged out of the river barge in Dresden River port, a key consideration for the team supervising the transfer was the “short distance to final destination within same city” which “required tandem lift by two cranes.”
Production Boost Welcomed
Last year, GlobalFoundries announced plans to invest at least US$1 billion in its new Dresden facility as part of plans to increase its global wafer production capacities from 300,000 in 2020 to 850,000 in 2022. The investment followed an extension of the supply agreement with Air Liquide in early 2022 for the supply of high-purity gases to GlobalFoundries’ Fab 1 in Dresden.
Praising the most recent project move, as ‘high-precision work’, Robin Corral, key account manager at Air Liquide, hailed the work by both the GlobalFoundries Facilities Team and his colleagues from Air Liquide in completing the final installation on time and without issues.
The delivery of the air separation units also followed a strengthening of the strategic long-term manufacturing agreement between GlobalFoundries and Qualcomm Technologies that aims to boost production, particularly in the U.S. and Europe.
Headquartered in Malta, New York, GlobalFoundries is the fourthlargest semiconductor manufacturer in the world and floated on the Nasdaq in October 2021. Since announcing the investment in new capacity in Dresden, the firm has seen rapid development with more advanced capabilities emerging.
“Our Dresden facility is the largest semiconductor manufacturing site in Europe, with approximately 500,000 300mm equivalent semiconductor wafers shipped in 2021,” a spokesperson for GlobalFoundries said. “The facility occupies an area of approximately 407,000 square meters, with clean room extending over an area of approximately 63,000 square meters, which is home to our CMOS and FDX process technologies from 55 nanometer down to the 28/22 nanometer node.”
The specialist air separation units delivered by Bertling and Air Liquide will now play a vital role in the plant, refining gases in a separation process that involves a distillation temperature of around -196°C, helping to dramatically increase production capacity at the site.

“We have seen demand grow and this has driven the need to build new facilities here,” Andreas Riedl, process engineering technician at GlobalFoundries, said. “The air separation units will supply the factory with nitrogen and oxygen, and we will soon be generating up to 8,000 cubic meters of nitrogen per hour, saving up to twelve tankers.”
The firm is also optimistic about the new plant noting “we have this footprint in Dresden and the fastest way to increase capacity is to expand on an existing footprint.”
Based in the UK, Malcolm Ramsay has a background in business analysis and technology writing, with an emphasis on transportation and ports.
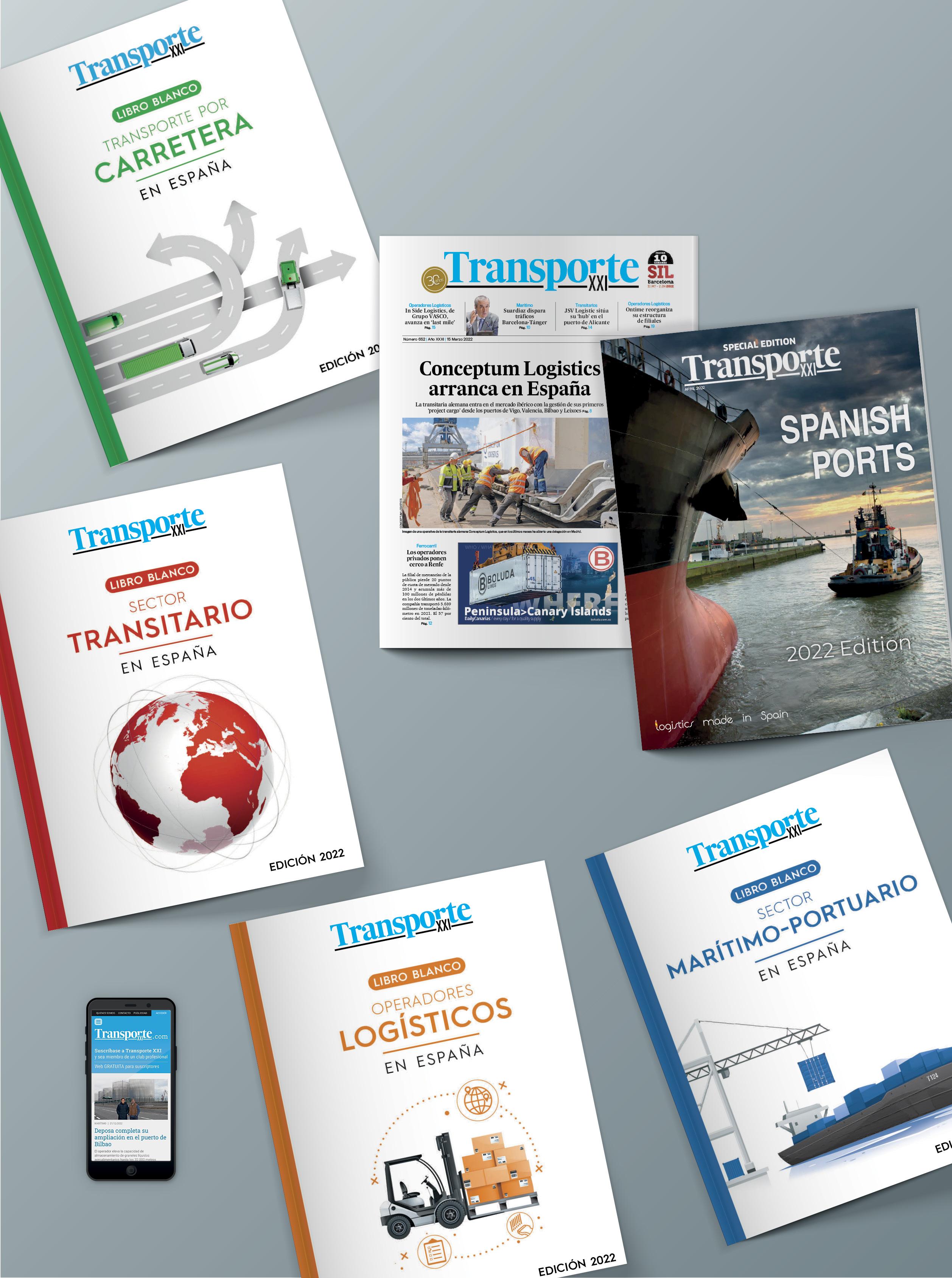