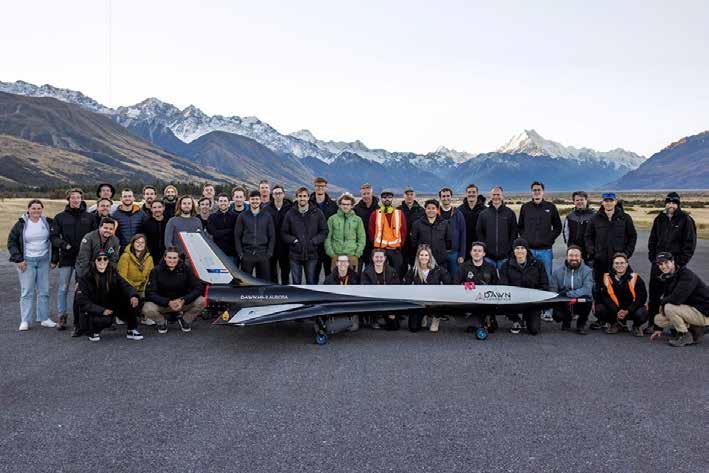
5 minute read
Dawn Aerospace: Rocket-powered spaceplane takes flight on South Island
Dawn Aerospace announced on 06 April the successful completion of the first rocket powered flight campaign of its spaceplane, the Mk-II Aurora.
The flights occurred at Glentanner Aerodrome located at the north west end of Lake Pukaki on the 29, 30, and 31 March. Previously tested using surrogate jet engines, last week’s campaign was the first for the Mk-II Aurora conducted under rocket power.
The Mk-II Aurora is designed for aircraft-like operations and is capable of flying multiple times a day. Unlike traditional rockets, Dawn vehicles take off and land horizontally on a runway and do not require a dedicated launch pad.
“To have demonstrated rapid reusability in the first tests is proof of our core philosophy, and confirmation that rocket-powered vehicles can be operated just like commercial jet aircraft, said Dawn CEO, Stefan Powell. “This fact allows us to rapidly test now, but in the future, it will completely revolutionise the economics of space access.”
“These flights were a monumental achievement for Dawn Aerospace, and the result of years of hard work from the team. After conducting three tests in three days, we believe Mk-II is the most rapidly reusable rocket-powered aircraft in operation,” he said.
The flights aimed to validate key systems and capabilities, such as the rocket engine, rather than striving for maximum speed or altitude. Future tests will look to increase speed and altitude in a ‘build-up’ approach.
During commercial operations, the Mk-II Aurora will fly to 100 km altitude and aims to become the first vehicle capable of such flights twice in a day, laying the foundation for a fully and rapidly reusable first-stage booster.
Initial flights reached altitudes and speeds similar to those demonstrated in previous test flights under jet power, approximately 6,000 feet and 170 knots respectively.
Upon the successful completion of the Mk-II Aurora program, Dawn Aerospace plans to develop the Mk-III, a two-stage orbital vehicle capable of carrying over 1 ton on a suborbital flight or delivering a 250 kg satellite to low Earth orbit (LEO) with an expendable second stage.
“The vast majority of our industry’s carbon footprint is created in the manufacturing of rockets, not the fuel efficiency,” said Powell. “Our orbital vehicle, Mk-III, is designed to be 96% reusable. This is key to delivering on our vision of a sustainable and future-proof space industry.”
The Dawn mission
Already the fastest-growing supplier of green in-space propulsion, Dawn boasts over 15 customers in Europe, Asia, and the USA, and hardware on 11 operational satellites.
Dawn’s mission, states Powell, “is to provide scalable and sustainable space transportation - both from Earth to space and from space to everywhere else.”
According to Powell, it’s important to consider both aspects of this mission in order to address the entire transportation challenge – “from launching off Earth’s surface through to controlled deorbit at the end of a satellite’s life.”
“To address the “from space to everywhere else” part of our mission, we already have a wellestablished business supplying inspace propulsion to satellite builders all over the world,” he wrote in a statement.
“We were the first to demonstrate nitrous bi-propellant propulsion in space, and now are the leading suppliers worldwide of green propulsion with over 50 thrusters in orbit and hundreds more on order. We feel we are well on the way to achieving this part of our mission, and the path forward is clear.”
Why winged vehicles?
Providing a rationale for selecting winged vehicles as the basis for the Dawn platform, Powell commented that winged vehicles can land without functioning engines, which gives them a massive reliability advantage. “This makes many kinds of anomalies survivable – even significant ones - dramatically increasing the robustness of the system, even if the mission must be aborted.”
“This is a lesson learned through the ages of aviation and comes out in the raw statistics of rocket vs. aircraft reliability where a chasm of roughly a factor of 10,000 difference exists between rocket and aircraft reliability,” he stated. “We wanted to lean in on these facts to bring aircraft reliability to spaceflight.”

Where to from here?
According to Powell, the Mk-II is just the start. The next big step will be getting to the performance limits of this first airframe.
“This airframe was built to be extremely hard-wearing and reconfigurable from jets to rocket power. It has undergone many small repairs and unplanned modifications, which all add weight. Naturally, it is not as high-performance as an optimized vehicle could be.
He anticipates that this first version, which is being referred to as the “Mk-IIA,” will reach a maximum altitude of 60kft (20 km) as it has limited propellant capacity.
“The Mk-IIB will be a highly optimised version, using the same aerodynamic shape and basic architecture but pushing every parameter to achieve maximum performance,” he continued. “Upgrades will include wing box tanks to increase propellant storage, a higher thrust engine, a lighter structure, and an RCS system.”
He envisages that the Mk-IIB will be capable of flying supersonic, outside of the atmosphere and, ultimately, to an altitude of over 100km.
“Once the Mk-II mission - to be the first vehicle to fly to space twice in one day - is complete, we will have the skill, team, and confidence to invest in the next step: the full-scale Mk-III vehicle, capable of deploying an expendable second stage which delivers a 250 kg satellite to orbit. We will also be in a prime position to commercialise the Mk-II capability, something we are already fielding much interest in.”