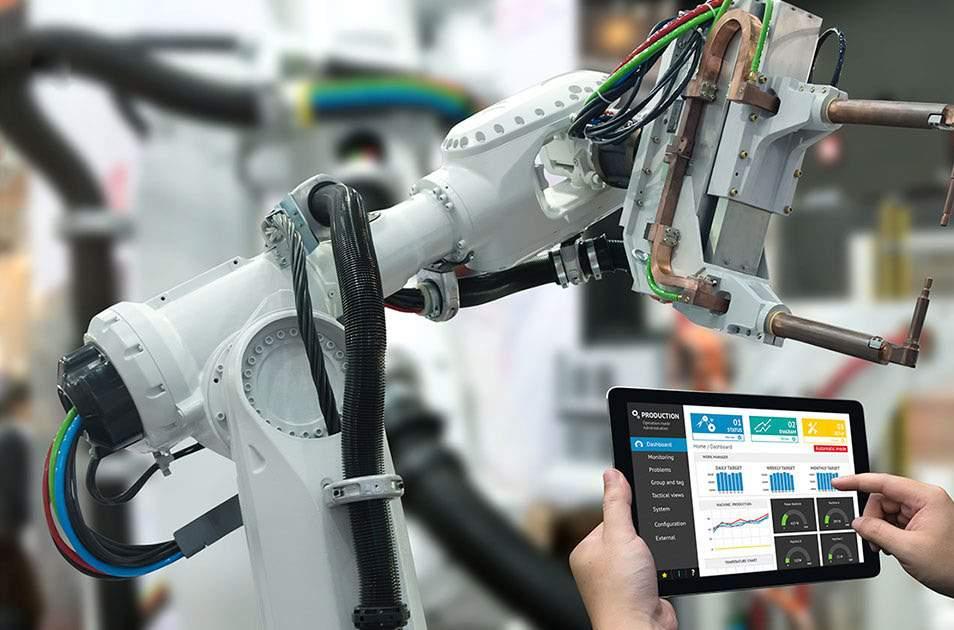
11 minute read
BIG PICTURE
During an interaction with Nitisha from BISinfotech; TS Shankar, Regional Sales Manager-India, Analog Devices highlights the impact of IIoT on communication and automation industry. He says, IIoT tools can play a vital role in enabling location based services, ensuring a seamless transition through various changes. It will have a lasting impact on businesses. The Industrial Internet of Things (IIoT) drives significant improvements in production and operational efficiency, proving transformative for industrialisation. He emphasized the ADI and its deep domain expertise, advanced technologies which connect the industrial equipment and networks of the future with solutions.
Advertisement
QPlease explain the impact of IIoT on the automation industry. How is it going to help businesses?
Automation prevails as a supporting driver of technology and business decisions, data insights, continuous delivery and business profit. Over several decades, we have seen the benefits of automation and are now promoting these systems with advanced data, machine learning and artificial intelligence. And as autonomous systems become more interconnected and communicated, it becomes easier to analyse and interpret data to make intelligent decisions across factories.
The interaction between humans and machines is on the verge of a revolutionary change through IoT that will introduce many possibilities. IIoT, a connected network of intelligent machines, will dramatically change business, just as the
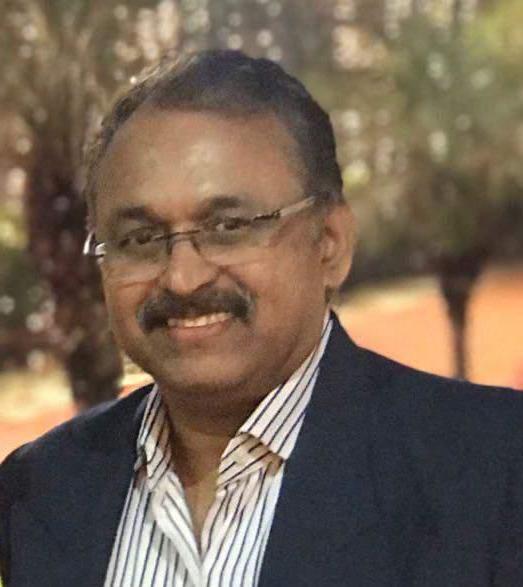
TS Shankar
Regional Sales Manager-India, Analog Devices
consumer Internet has changed our lives. The smart factories are creating new business value by increasing output, asset utilisation and overall productivity. They take advantage of new data streams to deliver flexibility and improved quality while cutting down energy consumption and waste. Increasingly, edge-tocloud is combining intelligent systems that make manufacturing environments become more efficient by optimising mass customisation.
QWhat are the major benefits of Ethernet, and how is it impactful for IIoT?
Intelligent, interconnected automation environments require digitally connected systems, machines, robots, etc., to create and share information. How these machines communicate and the factory communication network they use is at the heart of the enterprise and enable us to drive Industry 4.0. technology with widespread deployment. It is also widely deployed in the IT infrastructure of all manufacturing environments, offering higher bandwidth and enabling faster commissioning.
QWhat are the current industry challenges that you face and the scope for industrial Ethernet?
The more the number of devices, the greater the challenges to keep them synced with each other. And the lack of common standards with IoT is a global challenge. For enterprises to adopt these devices and integrate them within their preexisting infrastructure is a cumbersome process, as network connectivity issues, unresponsive servers and machine downtime are very common. Furthermore, cybersecurity is a major concern with IoT and will remain so until enterprises adopt a global IoT security framework.
Establishing a global IoT infrastructure is also a challenge. Companies adopting IoT should ensure that the design implements a robust IoT logging, monitoring and maintenance framework. In addition to technical challenges related to standards and security, lack of capital investment and skilled talent also hinder IoT adoption.
Industry 4.0 as an ecosystem comprises a diverse set of stakeholders, including hardware vendors, software application vendors, network operators and system integrators. It leads to a broader scope for improvement and adoption within the industry.
Similarly, there is a lot of scope around the adoption of IoT. Industrial Ethernet has emerged as the technology of choice at the control level of the operating system. The goal is to enable seamless connectivity apart from IT and high-end OT networks.
The Industrial Internet of Things (IIoT) drives significant improvements in production and operational efficiency, proving transformative for industrialisation. For a few years now, Ethernet has been the choice of technology for enterprises, data centres and many service provider networks due to advantages like reliability, versatility, high performance and low cost. Similarly, it is becoming a vehicle for industrial applications on the factory floor as well. It accelerates the communication and synchronisation of the actuators participating in the process.
Timely access to data and delivery of that data throughout the automation system depends on the connectivity network. Networking technology must handle the increased data volume, as should manufacturers’ processes and methodologies.
QAccording to you, how can Ethernet solutions be made more advanced for industrial use?
With connectivity being central to the vision for Industry 4.0, three things must become a reality to deliver a truly connected enterprise. First, high-level information technology (IT) or enterprise infrastructure must converge with the plant floor control network. Second, the various networks or manufacturing cells currently on the factory floor must all coexist and interact. Third, we need seamless, secure connectivity across our process environments, from the process edge to the enterprise cloud. We need to adopt a fundamental networking technology that can support interoperability, expandability and accessibility. Ethernet emerges as the ideal solution, a well-understood
QCould you elaborate on ADI’s offerings and strategies in this sector?
Being at the forefront of Industrial Ethernet, ADI has developed a deep portfolio of solutions leveraging its rich automation domain expertise and advanced technologies. Its design ensures time-critical data and seamless connectivity across industrial applications while assuring operational efficiency. The ADI Chronous™ portfolio of scalable Ethernet solutions includes physical layer devices (PHYs), embedded switches and complete platform solutions with multiprotocol software. These are thoroughly tested and verified to be fast in the market. The latest ADI Chronous™ offering enables customers to reduce energy consumption in buildings and their overall carbon footprint through better control of building standards.
Important solutions in this portfolio include:
• ADIN1200, the industry-leading 10 Mbps/100 Mbps Industrial Ethernet PHY with advanced features set and verified robustness.
• The ADIN1300, the industry’s lowest latency, lowest power gigabit PHY, delivers verified robustness for harsh environments.
• The Fido5200/Fido5100, a real-time embedded two-port multiprotocol switch, supports many available TSN features.
• The new ADI Chronous™ offering supports the 10BASE-T1L physical layer Ethernet standard, allowing new data streams from edge nodes in remote and hazardous locations to process and manufacturing facilities.
QHow do semiconductor players like ADI make IIoT more affordable and ‘sensible’ in the real world?
We understand the need for a complete IoT stack and are developing an end-to-end solution that facilitates market adoption. ADI leverages its deep domain expertise and advanced technologies to connect the industrial equipment and networks of the future with solutions like ADI Chronous.
• ADI SmartMesh® wireless products are embedded chips and pre-certified PCB modules complete with fully developed, field-proven, intelligent wireless mesh networking software for moving up the stack.
• Multiprotocol software updates are also supported and available through the ADI Chronous™ developer portal. Our Chronous solutions stand up to the toughest, time-critical environments and open the door to Gigabit and 10BASE-T1L connectivity. Similarly, our SmartMesh products are ultra-powerful, ultra-reliable wireless sensor networks for IoT connectivity even in harsh environments. These multi-hop mesh networks have been developed for distributed sensor applications that feature channel-hopping and time synchronisation for low power.
Our suite of industrial Ethernet products includes technologies, solutions, software and security capabilities designed to connect the real world beyond factory networks and the cloud. ADI leverages over 50 years of experience in industrial connectivity to supply factories with next-generation industrial Ethernet technologies that address the key challenges surrounding seamless and secure edge-to-cloud connectivity.
QHow is India going to derive the potential of IIoT? Which sectors are upfront and name some strategies to enrich IIoT in India?
India is already matching the pace of adoption of new technologies like IoT, 5G, AI and cloud to drive new business models. The Government of India has also initiated various policies and initiatives to leverage the benefits of these disruptive technologies in various sectors. Many start-ups in India are also using these technologies to create new and innovative business models.
Industry watchers have chosen India as a hotspot for IoT deployment. According to one market analyst, the market expects to exceed the USD15 billion target set by India government to reach USD 17 billion in 2021. IoT is enabling new ways to monitor, manage and control devices. It is enabling real-time monitoring of product performance for better insights and faster development of new products. Currently, most IoT data is being used for anomaly detection and control. In the future, the data may be used for predictive analysis and optimisation, creating opportunities for new and innovative business models.
Indian companies are leveraging IoT capabilities in product development. The onset of the pandemic has fuelled the demand for contactless technologies that are likely to lead to the adoption of IoT in the asset and security sectors. The commercial and residential sectors are also integrating with technology to deliver a contactless / touch-free experience. The need for personalised customer experience and increased after-sales will drive retail organisations to implement IoT in the consumer segment. Similarly, in the public sector, the Government of India’s focus on setting up smart cities will create a substantial potential for IoT spending in public safety, traffic management and energy management. Similarly, in the process industries, performance optimisation and preventive maintenance are crucial use cases. Companies that have invested in expensive equipment such as cranes can maintain them remotely using IoT. Sectors such as healthcare, logistics, agriculture, oil and gas, power and core manufacturing in the industrial segment will leverage the adoption of IoT solutions.
QThe omnipresence of IIoT underlines new challenges putting cybersecurity centre stage. Could you highlight the critical security challenges faced by customers, common pitfalls in IIoT security implementation and best practices followed?
Security and privacy can make or break the adoption of IoT products. Challenges include not only hardware vulnerabilities, but also security gaps created during the integration and implementation of IoT systems, as well as remote device access, communication and management. Features and solutions that mitigate these issues include software-based API security. Such security measures can authenticate and authorise data movements between devices.
Security should be a fundamental risk management consideration in planning IIoT strategy. Creating security in today’s increasingly complex networks is not easy. Making it embedded in the entire system requires a multi-layered approach leading to edge devices, controllers, gateways, and stacks. ADI’s chronological portfolio provides security at each node point within the system while minimising trade-offs in power, performance and latency.
Robust connectivity and cybersecurity enable better visibility into the supply chain, allowing the industry to respond to disruptions quickly. The time required to improve connectivity and cybersecurity will vary, largely depending on the company’s operational setup, including the number of machines and software solutions.
As companies increasingly digitise their manufacturing operations, cybersecurity becomes more important. With massive connectivity, companies can more easily improve cybersecurity at all levels when asset downtime is high or operations are shut down, as there will be no major disruptions
from implementing the fix. Companies can quickly take some simple cybersecurity measures, such as critical software updates and firmware updates of hardware. They can build a hardware-based trusted platform and execution strategy to ensure firmware authenticity. They can use a built-in encryption module with public key infrastructure and multi factor authenticated access. These small steps help reduce overall cybersecurity risks. show economic benefits for the end customer. There is also a tendency to prolong battery life by several years. In any wireless-based IoT monitoring system, the transmission of data consumes power. Therefore, smart segmentation, where understanding and processing occurs at the edge and small amounts of data (more sporadic or over shorter periods) due to localised decision making, can add significant value to IoT systems.
QHow has Analog Devices performed in the COVID-19 situation?
With the onset of the pandemic, as working patterns changed, we also adopted remote working. And like everyone, we also observed the need for visibility and the ability to manage teams remotely. Remote monitoring, systems control and connectivity solutions have become a major requirement for industrial businesses.
IIoT tools can play a vital role in enabling location-based services, ensuring a seamless transition through these changes. It will have a lasting impact on businesses even after the pandemic ends. On the customer side, industrialists may see a permanent shift towards contactless delivery or more end-user configurations. IIoT implemented in plug-and-play mode can play an important role in ensuring business continuity. It can minimise economic damage by ensuring employee safety and security, improving liquidity and reducing short-term costs.
QWhat could be the next level of Ethernet solutions?
In future, IoT may include applications that will clearly The ability to build a reliable network, independent of wireless protocols, would be integral to maintaining this high reliability by using alternative paths and channels to remove interference. It will be one where customers will receive personalised services on-demand while deriving economic benefits with optimal use of resources and environmental benefits as well.
Benefits of a convergent network based on Industrial Ethernet include simplified network architecture, cost reduction through the removal of gateways, elimination of hardwired connections, better system optimisation, increased up-time, etc. There are data islands of information and insight that we cannot access today, but as industrial Ethernet deployment becomes the norm, the challenge for Industry 4.0 will shift to security and all this data to maximise our business value.
The vision of Industry 4.0 is to automate processes using connected tools to collect, send and receive information. Industrial Ethernet connectivity will awaken this reality by seamlessly transferring current and future data streams from automation networks to the cloud.
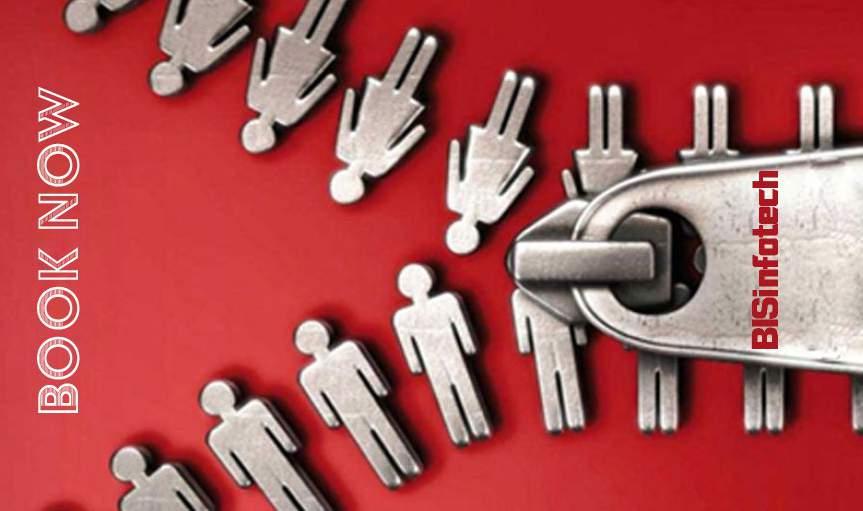