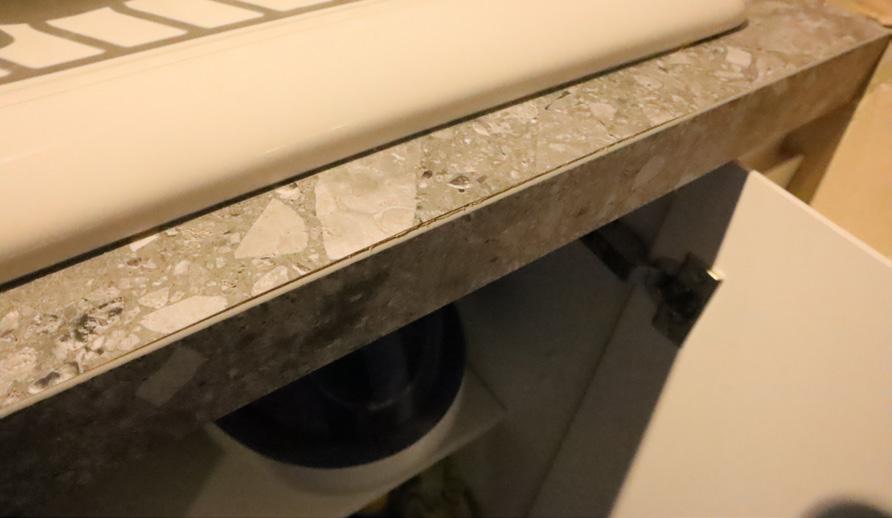
3 minute read
INSTALLER ADVICE
Richard Renouf, Furniture & Floorcoverings Consultant
Advertisement
BEWARE THE 'PICKY' CUSTOMER
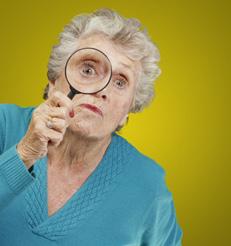
It was the magnifying glass that caught my eye when the customer showed me into her kitchen. It would have been the pride of Sherlock’s collection, no doubt, except that I don’t think it worked properly!
Mrs S consulted her long snagging list and then, using the magnifying glass, tried to locate the issues that she had previously identified, but she wasn’t too successful and had to resort to describing and pointing vaguely to where she thought she’d seen about two-thirds of the items on the list.
The inspection didn’t take long because I work to the general principle that unless a defect is easy to see in normal use of the kitchen, or is likely to lead to problems (such as poor sealing of a worktop joint) then it’s not a valid complaint. After all, fitting a kitchen relies a lot on hand skills and installers have differences in the way they work, so no two installations will ever be the same, therefore the ‘perfection’ that might come with a mass-produced hi-tech item isn’t going to be found.
Other customers have resorted to examining the underside of worktops, the wiring on top of cupboards, the fixing of cornices and light pelmets and similar items that are not within normal sight lines. As long as they are safe, secure and function correctly that’s what matters, although I do have a lot of respect for installers who take the trouble to keep their work tidy even in such places. caused her to get the magnifying glass out. It’s not very often that I go out to a job where there is nothing wrong.
A short while after visiting Mrs S, a worktop manufacturer asked me to look at a square edged laminate worktop. The front edging was coming unstuck. The complaint questionnaire had been filled in and the answers gave no clues about the possible cause of the problem. Everything in the installation instructions had apparently been done: even the positioning of the dog bones and the sealing of the cutouts. There was no swelling, just the lipping separating from the worktop. Therefore, suggested the installer, this was simply a manufacturing fault with the gluing of the lipping. It couldn’t be anything to do with moisture as it wasn’t near the sink.
All of that information was misleading. Actually, I’m being too kind, it was wrong! Moisture checks along the worktop edge showed that there was moisture ingress along the edge of the drainer section of the sink and it was easy to see that the sink had not been fully sealed to the worktop and the failsafe sealant around the cut-out had not been applied. The top of the cabinet below looked as if it had been cut out with an axe, it was so rough, and it was clear that the problems were only going to get worse. The customer was not going to be impressed when the manufacturer sent her the report and she had to have a discussion with the fitter. I couldn’t help but think what Mrs S and her magnifying glass might have found.
I should point out that some of the issues raised by Mrs S were valid complaints, and this was probably what www.richard-renouf.com