
3 minute read
INSTALLER ADVICE
PLAN YOUR WORK AND WORK YOUR PLAN
Richard Renouf, Furniture & Floorcoverings Consultant
Advertisement
Our intrepid KBB inspector, Richard Renouf, ventures to the coast and discusses the necessity of planning and how sometimes solutions are hiding in plain sight.
Boats in gardens make me curious. When they’re at the front of a house on a trailer they seem to be at the ready for an impromptu trip to the seaside or river. But when they’re big enough to need a crane, wedged up on blocks, and clearly have not had any care or maintenance for years, I wonder why they’re there at all, unless they’re simply monuments to good intentions.
Today’s customer had a huge boat in the garden of his cottage, two streets away from the marina. It wouldn’t fit through his side gate – if it had been mobile. But it wasn’t seaworthy, so that issue wasn’t going to trouble him for some time.
He had greeted me at the front door, and as we walked through several rooms he regaled me with the story of his ‘recycled’ cottage. It had been built in 1861 using beams from a Belgian barn and arched windows from the Netherlands, all imported via the local port, he surmised. Floorboards ran in different directions and the bricks changed every few courses when you looked from the inside, although the outside was rendered so it had an acceptable façade.
He pointed to the kitchen doorway and I had to take a second look. The plinths were deeper on the right hand side and whilst the worktops appeared to be horizontal, the floor dropped away significantly. I entered the room and turned to the left to face the sink. Again, the floor was falling away to the left hand side. I took out my laser floor scanner which is the quickest way to check the flatness and level of a floor and found a fall of 32 mm over the 6-metre length. The units at the lower end of the room were hovering above floor level. The feet were extended to their maximum height and the plinths had visible packers underneath.

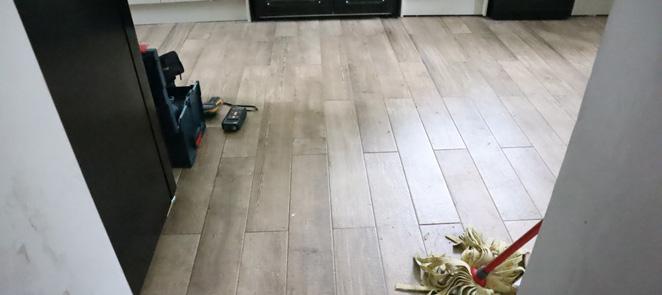
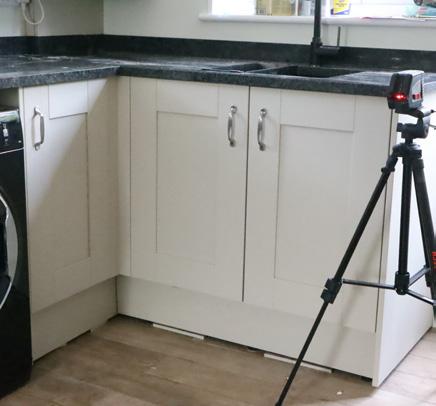
I set up a cross-line laser on a tripod and was amazed that the installer had managed to get the worktops level throughout, but it was pretty clear the marking out had started at the top end of the room and the height had not been checked in several places before the units were fixed into position.
‘I was worried about a flood from the washing machine or dishwasher,’ said the customer. ‘I figured if I put a fall in the screed the water would all flow down and out of the door. I built this extension myself, you know.’
We discussed solutions before we considered who should pay. His partner wouldn’t agree to have the worktops lowered as they would, she felt, end up too low. But he had some wood which he could use to make new plinths – in a contrasting colour and perhaps create a ‘skirt’ around the gaps under the end panels.
I showed him the tall end panels that he had purchased for the tall housings. ‘Why not get some more of these and cut them down to make end panels the right size for the raised units and also to make matching plinths?’ I said.
It was a lightbulb moment for him. ‘I hadn’t thought of that,’ he said. It was certainly a more pleasing option and the actual cost of the materials needed was a fraction of some of the other options he had been thinking of pursuing. It was likely a compromise could be reached with the retailer, who planned the job, and the installer, both of whom didn’t check the basics and act professionally.
The moral of the story? Plan ahead. But remember, even when things go wrong the solution may not be as drastic as you fear.