
2 minute read
FIRE/EXPLOSION
Keys to Maximum Explosion Protection
Proper selection and expert installation of explosion protection equipment is critical to asset and personnel protection. However, the pursuit of safety should never end there, as system reliability is largely dependent on maintenance and repair, according to Jeramy Slaunwhite, explosion safety engineer at REMBE Inc.
As for how often a plant should undergo inspection or maintenance to ensure equipment performs as required, the official guiding standard should begin with manufacturer’s recommendations, Slaunwhite says. “For passive systems such as explosion vents, a minimum annual visual inspection for leaks, bolt tightness and damage is recommended. For equipment with moving parts such as isolation flap valves, it’s a good idea to inspect new installations monthly for wear and product buildup. After a couple inspections, the intervals could go to three and then six months— provided no issues are found—and then a minimum deeper, annual inspection to check seals and locking mechanisms.” With every inspection and maintenance activity, Slaunwhite notes, the date and findings should be documented to build a continuous maintenance and condition profile. “This is also beneficial in the case of an incident, to prove diligence and reliability of the protection systems,” he says.
Accessibility can prove critical to maintenance and inspections, according to Slaunwhite “In many industrial environments, the expression ‘Out of sight, out of mind,’ is very relevant with respect to limited maintenance resources,” he says. “When planning protection equipment installations, it is beneficial to consider accessibility. This can be strategically locating equipment, or at least within sight and reach with a mobile lift. Explosion vents used with vent ducts are often completely hidden; an access door in the duct can provide easy access to perform maintenance inspections.”
The notion that fires are somewhat routine in wood processing facilities builds a level of complacency around explosions, from Slaunwhite’s perspective. “In wood processing and handling, the amount of fine dust in the material stream and accumulations in the handling systems can widely vary over time, seasonally or based on material conditions,” he says. “This can result in downplayed sense of awareness for the possibility of larger explosions and explosion propagation between connected equipment.” A comprehensive explosion safety concept should consider all operating conditions and scenarios, Slaunwhite says, including abnormal and upset conditions, as it is often during these times that serious events occur.
REMBE is a strong advocate for both prevention and protection, Slaunwhite emphasizes. “As such, we’re continuing to expand on our early fire detection technology, including the REMBE HOTSPOT, smart infrared thermography designed for harsh industrial environments, and the REMBE GSME gas detection sensors for the precursors of combustion to react before a flame is present,” he adds. “We want to help customers be proactive to identify and manage hotspots, embers and upset thermal events before a flame is present, but also realize that prevention is rarely 100% reliable, so protection strategies are also needed to manage the amplified consequences of explosions.”
T +1 704 716 7022 T +49 2961 7405-0
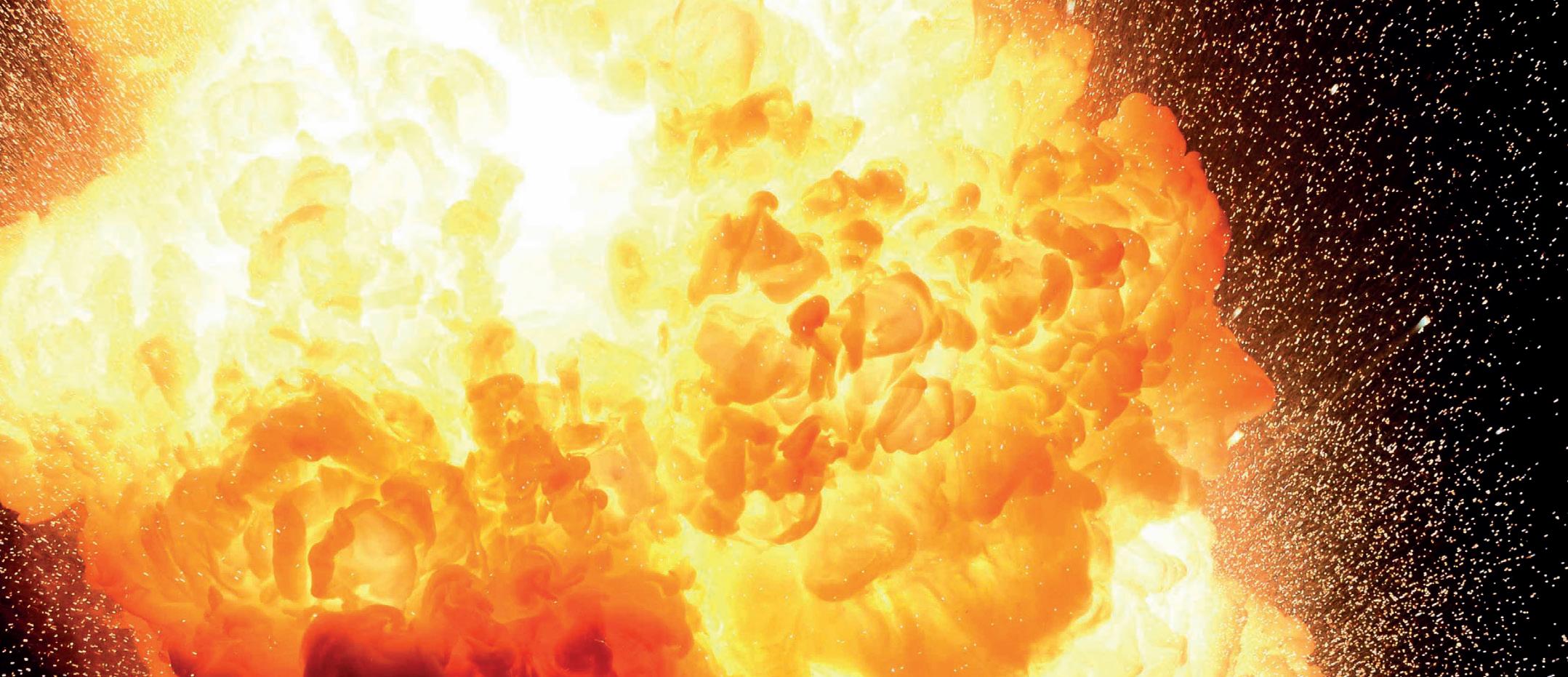
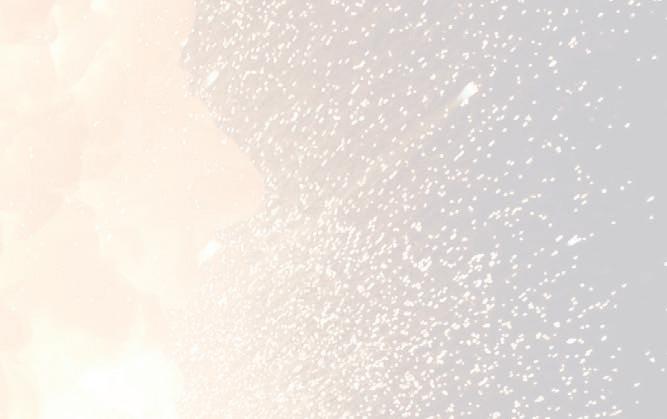
PROTECT YOUR PLANT!
Consulting. Engineering. Products. Service.
·Over 45 years of innovation in comdust explosion protection. ·Venting and isolation to protect personnel and plant. ·Customized indoor/outdoor protection for dust collectors and more.
Inc.