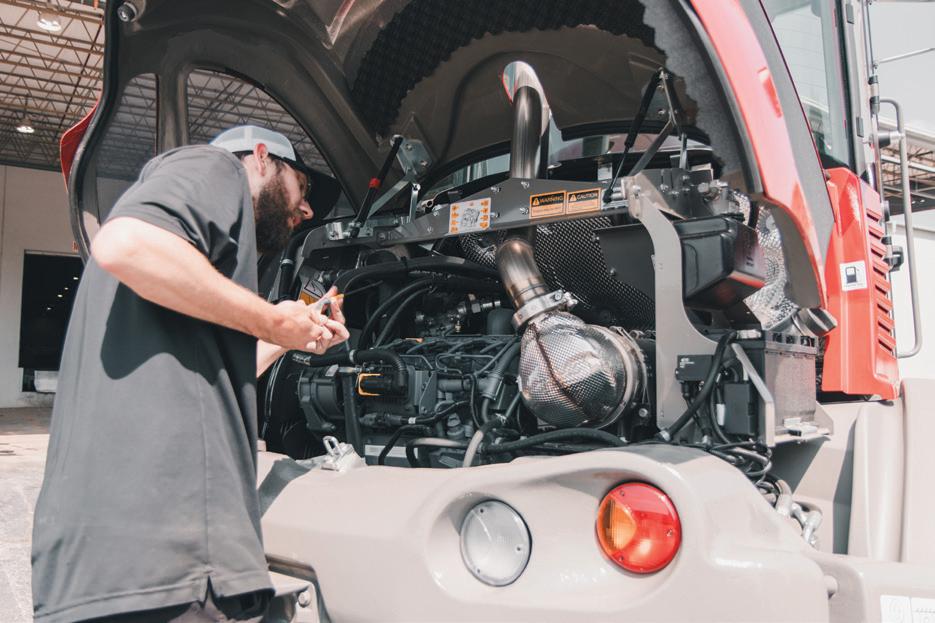
8 minute read
Maintenance musts
SIMPLE, PROACTIVE CARE KEEPS COMPACT WHEEL LOADERS UP AND RUNNING
BY LYNETTE VON MINDEN
Thanks to a growing range of attachments, compact wheel loaders are incredibly useful in all kinds of job site applications, from material handling to snow removal and everything in between. Even better, these versatile and durable machines are relatively simple to maintain. Still, a proactive approach can be the difference between a productive day at work and an impromptu need for repairs.
“Caring for your compact wheel loader should start from the minute you take possession of your new – or new to you –machine,” said Lee Padgett, product manager for Takeuchi-US. “Reviewing your operator’s manual and following all recommended maintenance, including daily checks, is always the best way to go.”
Padgett shared these recommended steps on how to thoroughly care for a compact wheel loader, as well as some common mistakes to avoid.
Daily Maintenance
Visual checks Before starting up the machine, do a quick visual check of the CWL and take these precautions:
• Ensure the machine is free from debris in vital areas like the radiator, AC condenser, and exhaust. If there is a large accumulation of debris in any of these areas, the operator should use compressed air or high-pressure water to remove the debris prior to operating the wheel loader.
• Search for visible oil leaks.
• If applicable, drain the fuel and water separator.
• Look at tire pressure and condition. Punctures or gouges, visible metal, or inadequate tread depths are all signs of tires that should be replaced as soon as possible.
• Check all vital fluid levels – including engine oil, engine coolant, hydraulic oil, fuel, and windshield washer fluid –and replenish if necessary.
• Make sure all driving and warning lights are functional.
“Not all engine or machine manufacturers will have low-fluid-level warnings, so it is a good practice to perform a visual check daily,” Padgett said. “If everything checks out okay, it is time to start greasing. All pivot points will need to be greased either prior to starting or ending the shift, depending on your preference.”
Greasing When greasing pivot points, don’t forget to grease the articulation point, which Padgett says is commonly forgotten. Clean the grease fitting prior to greasing the joint. Failing to do so will push the accumulated dirt on the fitting into the pin boss. The dirt will contaminate the grease and act like sandpaper inside the pin boss between the bushing and pin, resulting in premature wear.
Operator safety Finally, be sure to check all areas related to operator safety. Before climbing into the cab, operators should clean the mirrors and windows, especially if they used pressured air or water to clean debris. Once in the operator’s seat, ensure the brakes are functional and the backup alarm is working.
“After all those daily checks have been performed, operators can get to work,” Padgett said. “And, they’ll have the peace of mind knowing that the machine they’re using is in excellent condition and should serve them well as they get their jobs done.”
Weekly Maintenance
Weekly, or roughly every 100 hours, grease the machine thoroughly at the pivot points, bushing and bearing. Other than additional greasing, weekly maintenance tasks require a deeper dive than daily tasks.
• See if the electrical connections, cables, and plugs have any issues.
• Clean and securely attach the battery contacts.
• Make sure there are no blown fuses or loose connections in the fuse panel.
• If the radiator and oil cooler are dirty, clean them from the inside out with compressed air or high-pressure water. However, tread carefully to avoid damaging anything in the process.
• If necessary, clean and replace the engine air filter. This is especially true for operators working in dusty environments like demolition or site prep applications. Do not use high-pressure compressed air to clean the air filter or hit it against anything to free it from dirt as this can damage the filter.
• Check the lug nuts on each tire and tighten to the appropriate torque.
HOURS-BASED SERVICES
“There’s a reason why it’s important to log hours while utilizing a CWL,” Padgett said. “There are some additional tasks to take care of when the machine reaches 250 and 500 hours, so you need to know when those milestones are approaching.”
250 hours Depending on the manufacturer’s recommendations, the engine oil and fuel filters should typically be changed every 250 hours. Most engine manufacturers require an initial engine oil change after the break-in period. Following this, oil change intervals are usually 250 to 500 hours.
Check the oil level in the front and rear axles, power divider, and all four planetary drives. Initial service for the wheel loader’s planetary assemblies after the first 250 hours is also recommended.
500 hours Change the oil in the front and rear axles, power divider, and all four planetary drives within the initial 500 hours. Following the initial period, these will only need to be replaced every 1,500 hours. Lastly, replace the axle breathers and check battery posts for corrosion and clean if necessary.
Annual Maintenance
The next major service intervals are 1,500 and 3,000 hours. At this point, the oil in the axles and hydraulic system is nearing the end of its service life and should be replaced. The wheel loader should be thoroughly checked to ensure there are no loose or worn parts.
1,500 hours As mentioned before, the oil in the axles, power divider, and planetary drives needs to be replaced. Additionally, change the hydraulic oil and service the brake system.
3,000 hours Every 3,000 hours, replace the hydraulic oil, air filters, and breathers.
“The 3,000-hour mark is also a good time to ensure all bolts and screws are tightened to the proper torque specifications,” Padgett said. “You should also look at hydraulic hoses for fatigue, cracking, or leaks, and replace them if you notice any of these issues.”
Engine
Depending on its manufacturer’s specifications, a diesel engine will likely need maintenance at certain hourly intervals. Some of this maintenance will simply consist of fluid changes, valve-train adjustments, and fuel and exhaust-system checks.
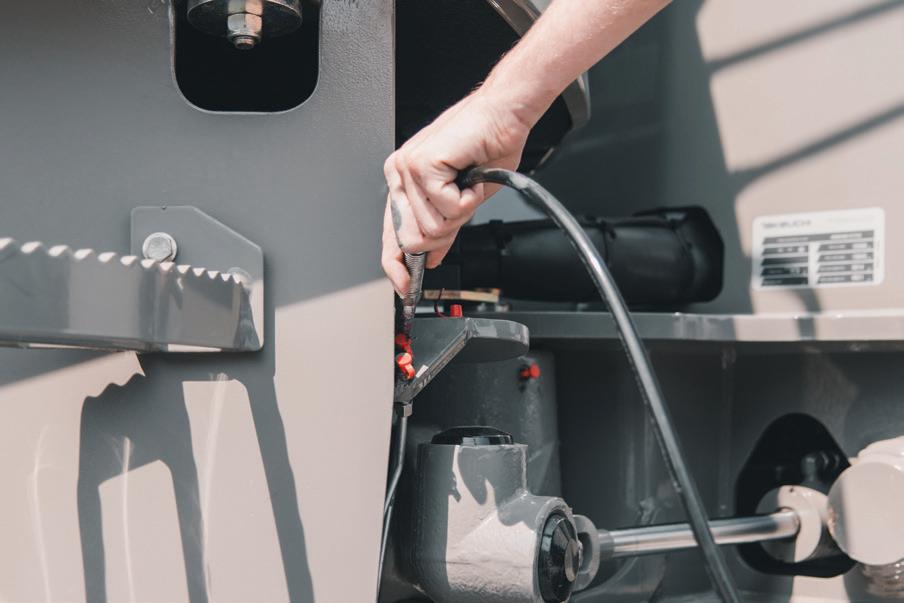
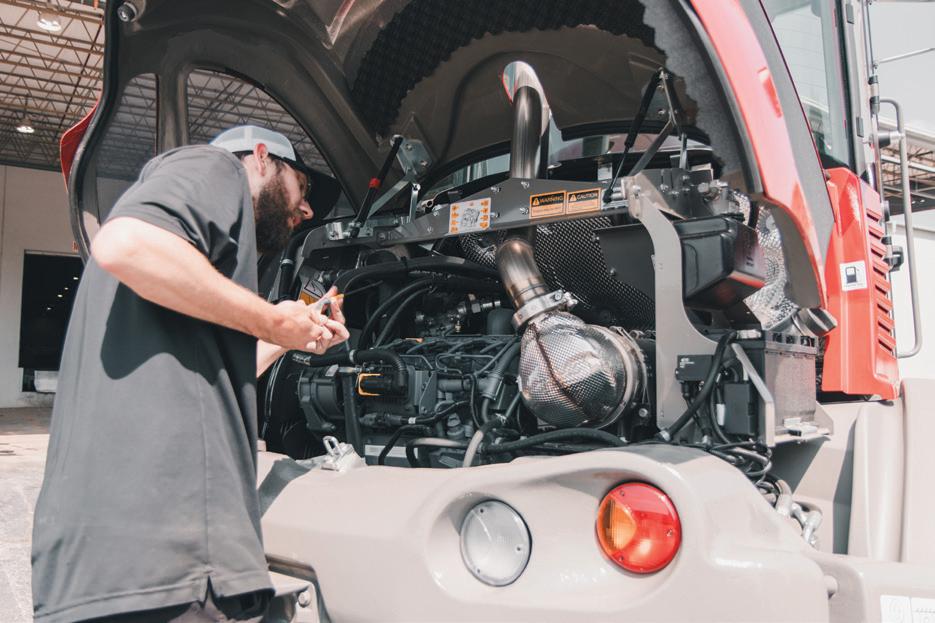
“If your wheel loader has a turbo-equipped engine, one operational technique is vital to its health – the warm up and cool down,” Padgett said. “Allow the engine time to warm up before putting the machine under a load, and let it cool down before completely shutting it off. It’s a common misconception that because the engine is small, cold starts and hot shutdowns won’t hurt it – they will.”
While allowing a Tier 4 Final engine to idle continuously can cause regeneration issues, taking a few minutes to heat it up at the beginning of your shift and cool it down at the end is a painless way to prevent premature turbo failures or engine damage.
“Engine manufacturers will have their own guidelines for service and inspections,” Padgett said. “That’s why it’s important to review the engine service manual for specifics on the best way to maintain your engine over the course of its lifespan.”
Avoid Common Mistakes
Compact wheel loaders are tough machines that rarely break down if they’re maintained properly. Most failures can be avoided with proper maintenance. Padgett says that Takeuchi sees two common issues that will impact a wheel loader’s productivity.
“Because wheel loaders have many articulating and pivoting components, greasing the machine really is key to its longevity,” he said. “The articulation joint moves constantly and is under tremendous stress. Give it plenty of grease to avoid premature wear of the pins and bushings. The wheel loader’s steering cylinders and loader pivot points should also be greased every day.”
Another consideration that may not be readily apparent? Multiple operators. Manufacturers regularly see problems caused by different operators using the same machine at different times – and assuming someone else has taken care of daily maintenance.
“Say a compact wheel loader is left at a job site to load and unload materials,” Padgett said. “One operator finishes his shift and leaves, expecting the next guy to take care of greasing or checking the oil. Or he thinks the guy before him already took care of it. In reality, no one does those very important tasks for days on end. That’s when breakdowns occur.
“Reading and following the procedures outlined in your operator’s manual is a great start. But good communication with all machine users is also vital. Put processes into place that ensure your machine gets the attention it needs, and it’ll serve you well for years to come.”
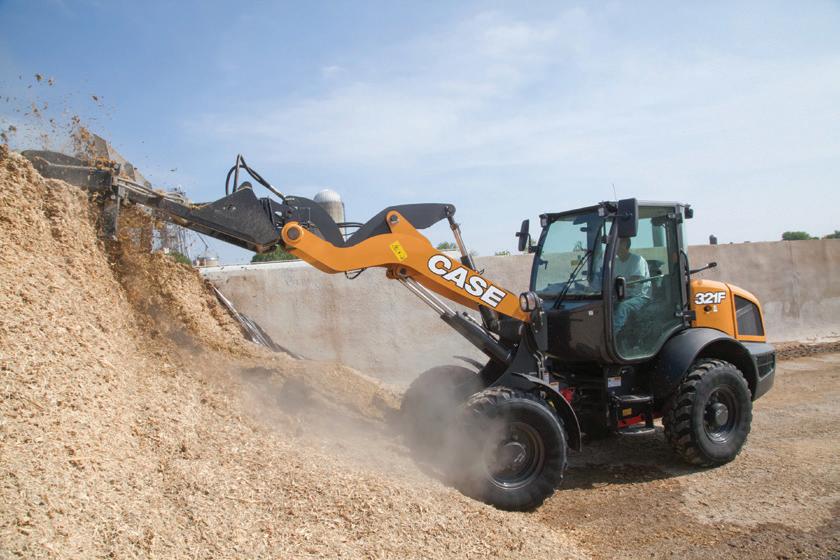
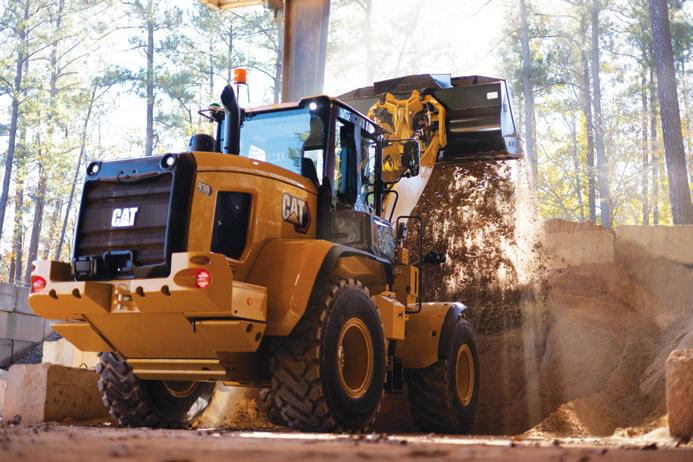
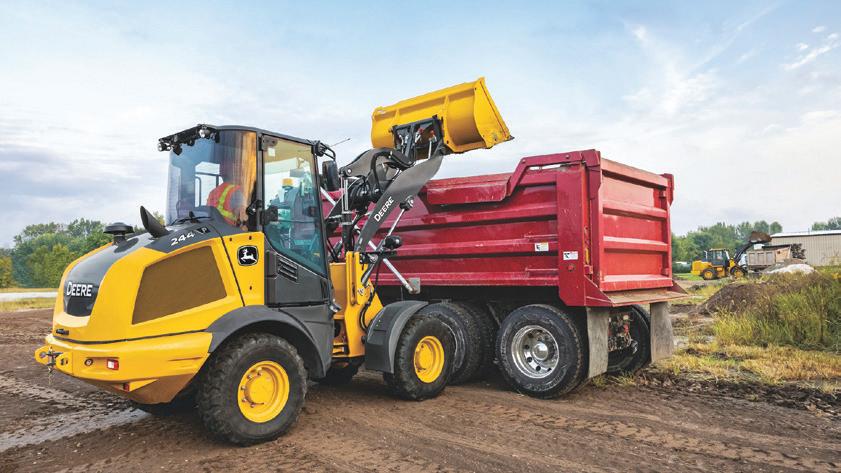
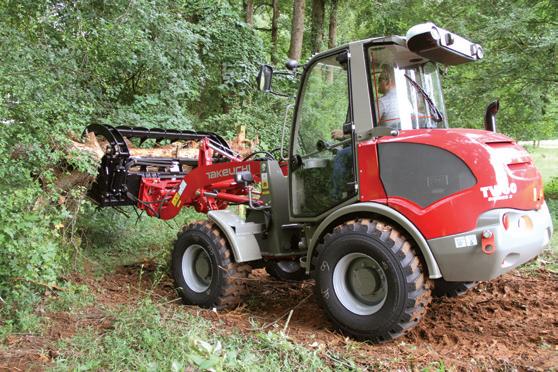
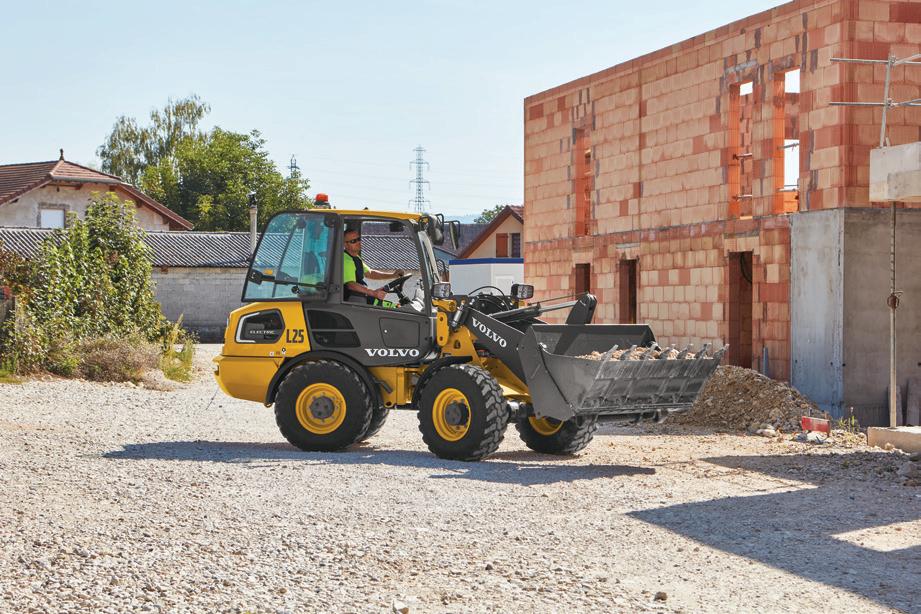
1 throttle lock. Torque mode saves up to 5 percent on fuel by “freewheeling” around corners and on downhills. Hystat mode provides engine braking with aggressive deceleration, acceleration and no travel until the throttle is applied. Ice mode for snow-clearing applications offers soft directional shifts and extended coast-out for improved control.
The updated CASE 321F compact wheel loader features an all-new seven-inch display, updated electro-hydraulic controls that perform and react with more of the premium settings and functionality found on CASE full-sized wheel loaders, and new axles that allow for travel speeds up to 25 miles per hour for easy roading. A new Smart Mode also provides better fuel economy. The added CASE SiteConnect Module improves telematics data transfer and allows for remote access and software uploads to bring together fleet managers, their CASE dealer, and CASE HQ for proactive equipment management and service.
3
New Cat 926, 930, and 938 wheel loaders feature four customized powertrain operating modes. Utility mode is designed for hydromechanical tool use or pick-and-place work, utility vehicle mode delivers fine ground speed control with engine rpm
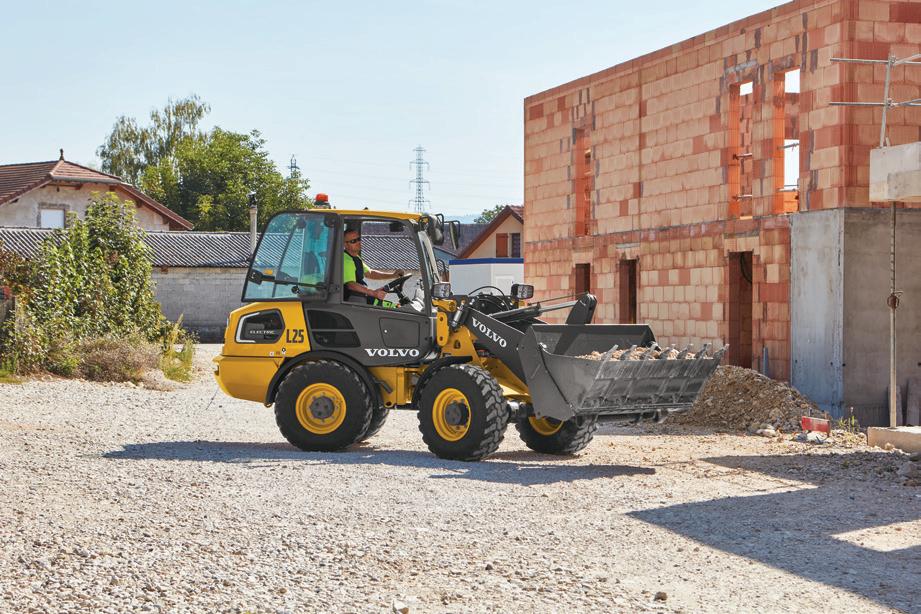
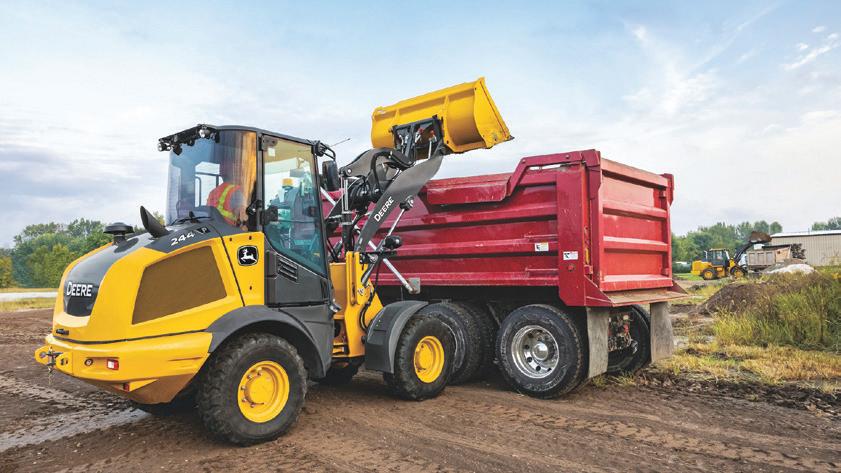
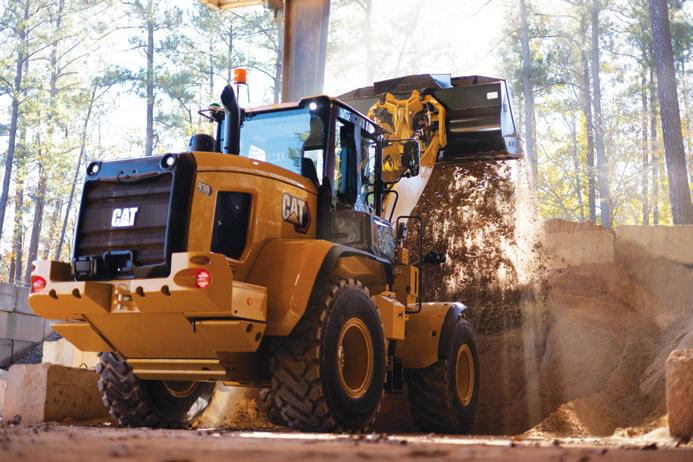
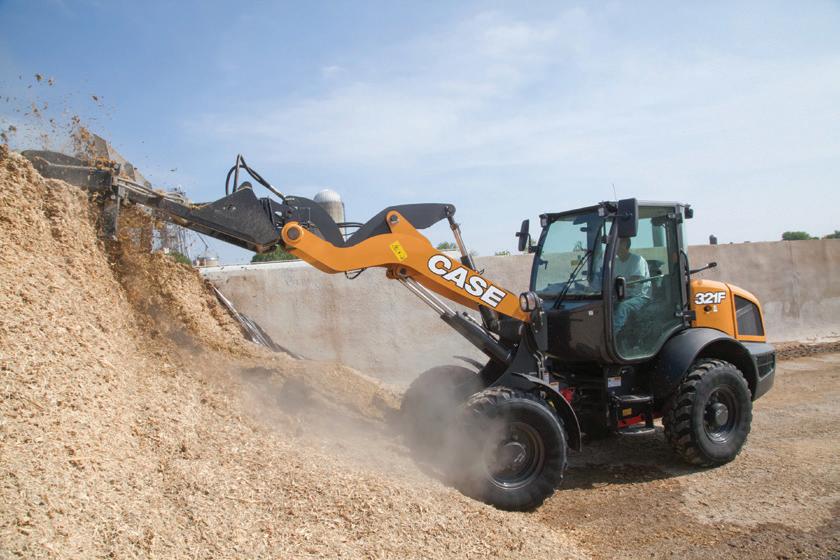
2
John Deere has shifted its L-Series 244, 324, and 344 compact wheel loader models to the P-Tier, carrying over all L-Series features, including Articulation Plus which enables rear-wheel steering to increase full-turn tipping load and improve maneuverability, and introducing new ones. Ride control is now standard on base models and optional factory-installed features include an auto-reversing fan and attachment assist controls which include integrated electrical (threepin) controls for attachments and combined creep control and throttle lock.
4 connect various attachments. A standard pressure-relieving coupler block located on the loader arm simplifies attachment exchanges by allowing the operator to relieve residual pressure in the auxiliary lines. A durable Z-bar loader linkage delivers powerful breakout forces and heavy-lifting capabilities, making the TW60 Series 2 ideal for excavating and stockpile loading. 6
Volvo has updated its L25 Electric wheel loader. A parallel linkage option is now available, and maximum speed is up to 20 kph. A new hydraulic pump and the relocation of the main control valve make this machine even quieter. A programmable cab heater option is available, and the need to reach under the hood to turn a main switch off at the end of a shift is now eliminated when using the machine regularly. Other new features include an electric parking brake with hill-hold functionality, a spring-applied and hydraulic-released wet-disk brake, and a more ergonomic joystick. It now takes only 6 hours to achieve a full charge from zero with the improved 6kW on-board charger.
5
Equipped with a turbocharged, 61-hp Tier 4 Final engine, Takeuchi’s TW60 Series 2 wheel loader can handle a wide range of applications. The machine’s universal hydraulic skidsteer coupler makes it easy to
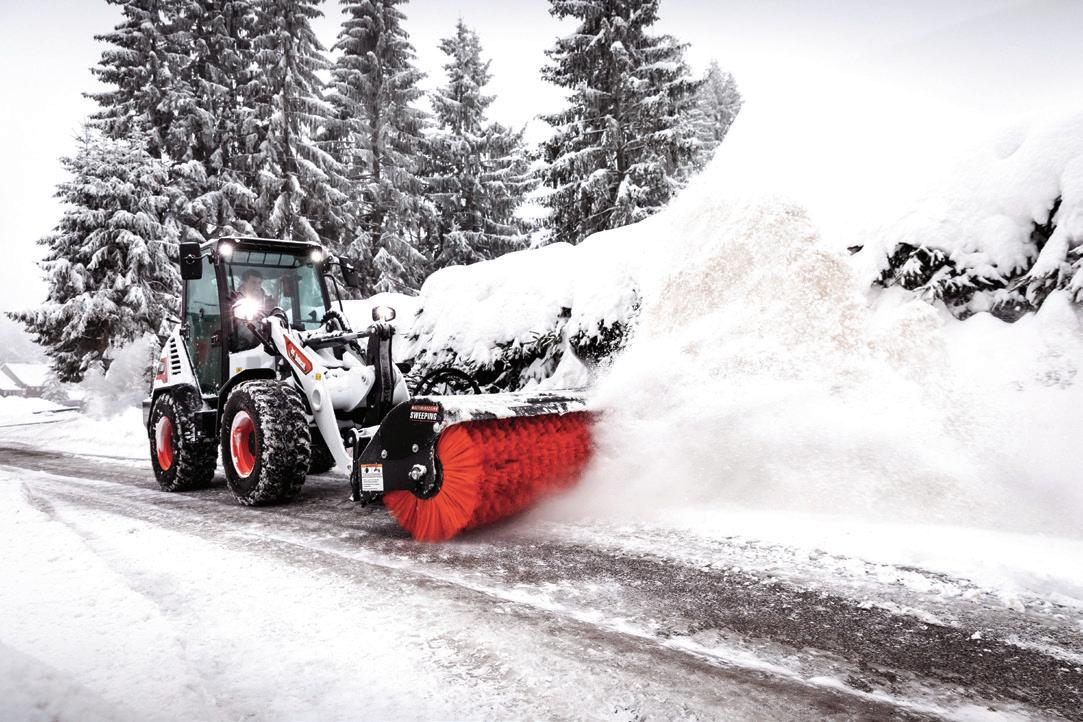
With a high bucket capacity, swift travel speeds, and increased maneuverability, the Bobcat L65 and L85 compact wheel loaders are ideal for lift-andcarry tasks in crowded work zones including construction and landscaping. Standard bucket capacities are up to 1 cubic yard. A range of attachments are available and the operator can optimize the performance of the attachment for the job with attachment control mode. This feature controls the engine and travel speeds separately for optimal auxiliary hydraulic performance.
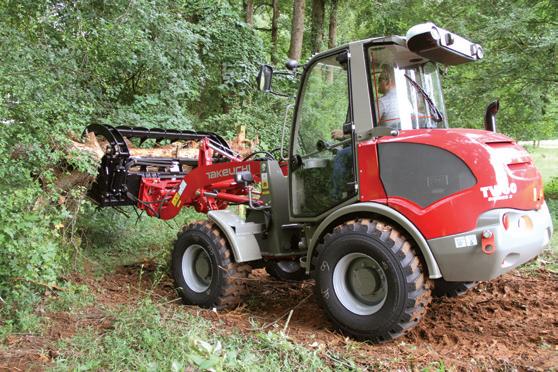
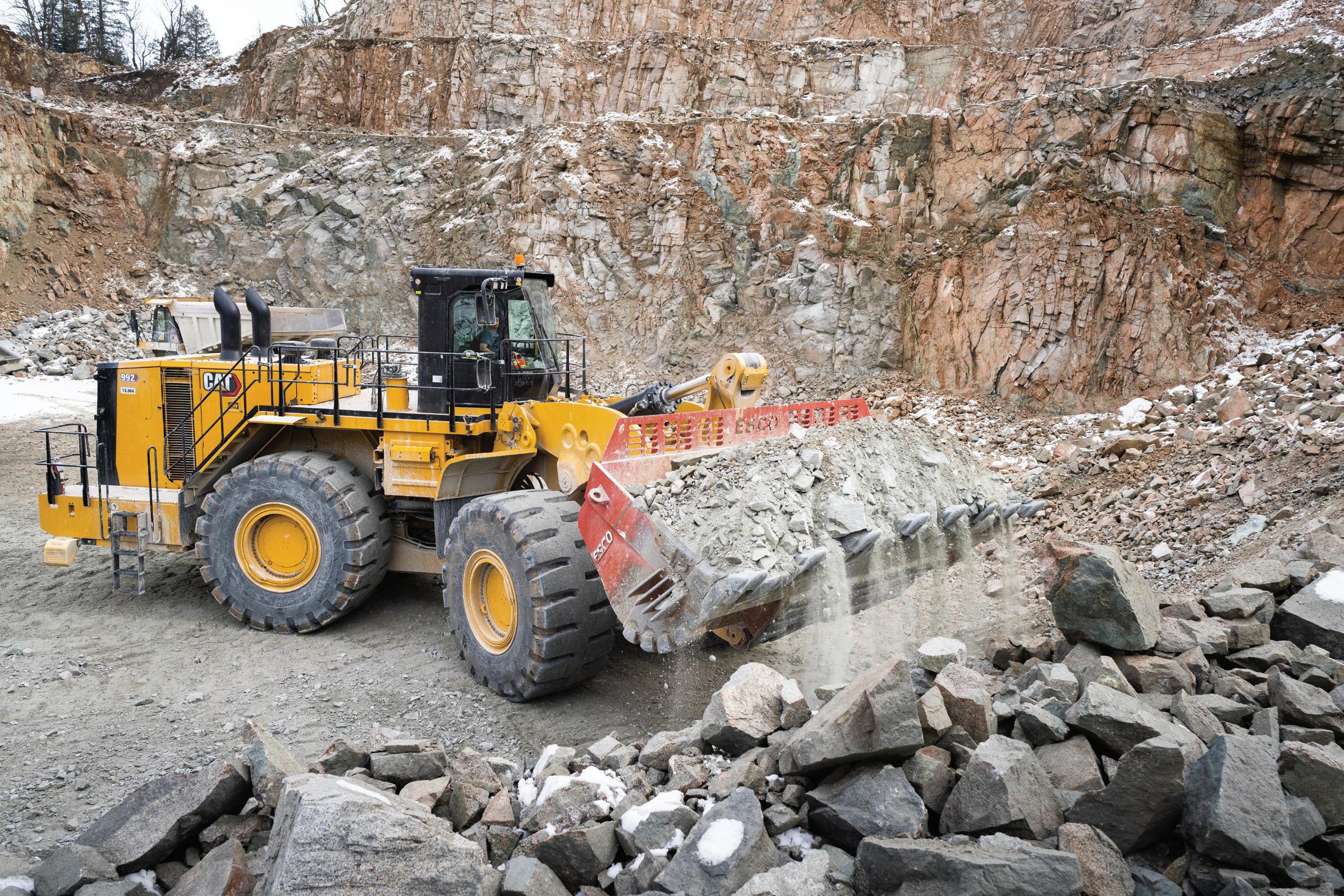