
4 minute read
Introduction
The research consists of a series of 13 3D-printed prototypes, fabricated with the aid of industrial robots. The series can be classified into groups, dependent on material and scale (5). This text focuses on the larger concrete prototypes and those made using biodegradable materials.
Liquid Rock (4), Coralloid Cocoons (3) and 350/360 Cohesion/Cocoon (1) reach the pinnacle of research into large-scale 3D printing with robots, measured by their size, complexity and impact, including the successful development of industry-ready products. Terrestrial Reef (7) and Pahoehoe Beauty (6) reach the apex of the research into the fragile rapport between technology (robotic additive fabrication) and the environment (materiality and sustainability). These projects, together with Quaquaversal Centrepiece (8) and Porous Cast (50–1), exemplify the author’s transdisciplinary approach as they have been developed with a plethora of partners from other disciplines.
Plastic Clay Concrete Soil
Very Small Quaquaversal Centrepiece
Small Crystal Net tests
vessels; Porous Cast tests
vases tests
Medium vessels Clay Column Liquid Rock; Liquid Curtain Terrestrial Reef
Large Plastic Column Venice Taevatiib Coralloid Cocoons Pahoehoe Beauty
Very Large Guardians of Time; 350/360 Cohesion/ Cocoon
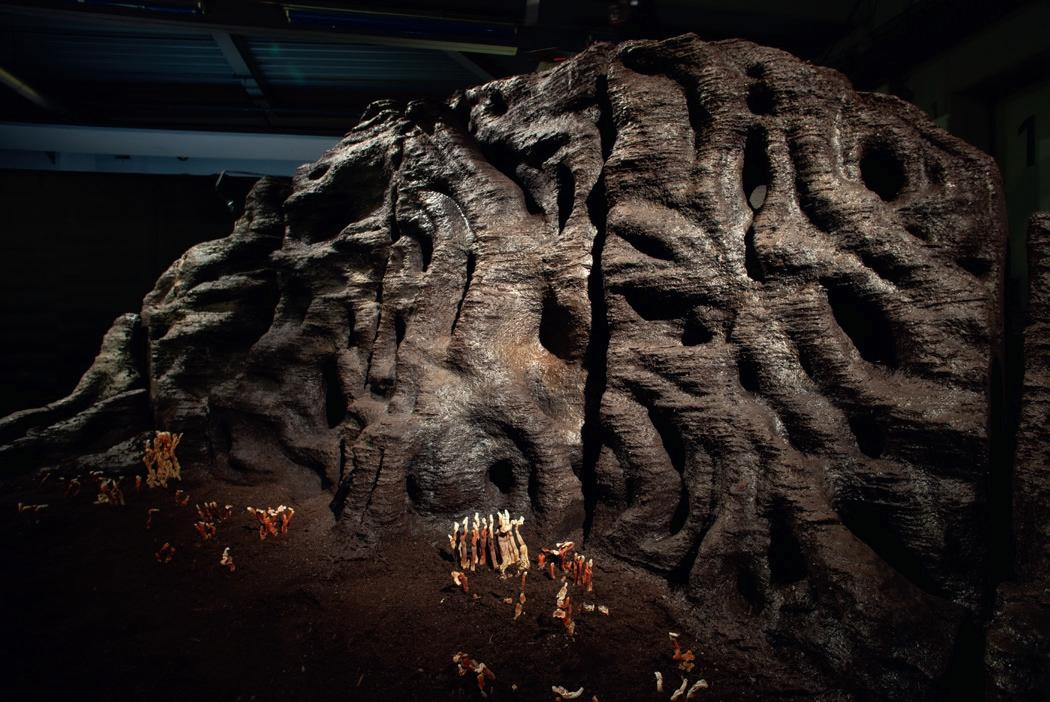
4 Liquid Rock, Galerie GÖttlicher, Krems-Stein, 2018. The organic and complex shapes cannot be manufactured with such accuracy, replicability and feasibility by any technique other than 3D printing.
5 Table categorising the series by size and material. 6 Pahoehoe Beauty, Ars Electronica, Linz, 2018. Robots surveyed a volcanic landscape to create a biodegradable 3D print. A chimera of natural and man-made materials, objects and species.
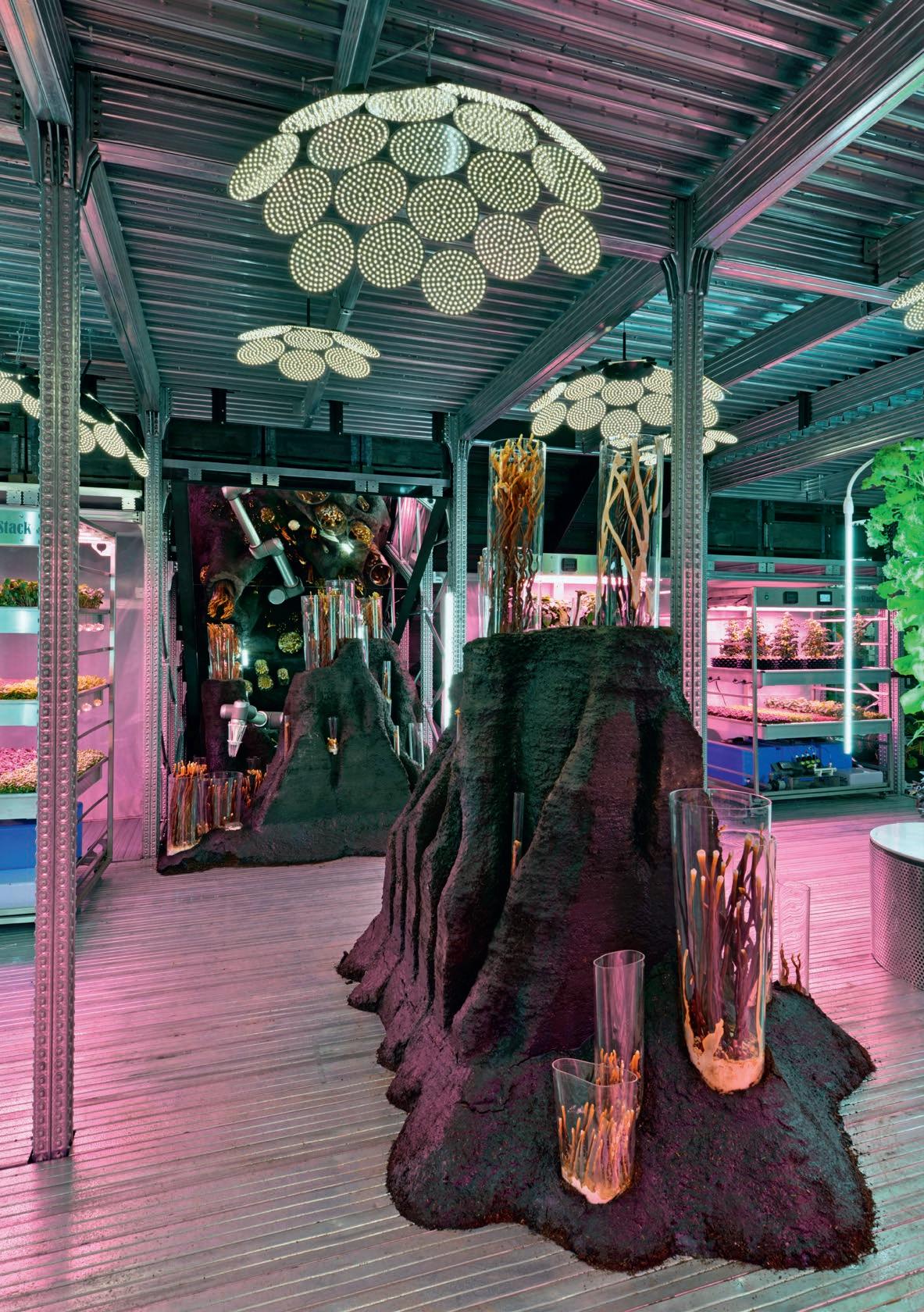
The other prototypes were important in establishing the affordances and constraints of large-scale 3D printing, and of the materials that may be used in the future more successfully than others. 3D printing implies a process of material deposition using a digital model to create a physical object. Arthur C. Clarke predicted the technology in 1964, in the BBC Horizon episode ‘The Knowledge Explosion’: ‘the invention to end all inventions… [a] duplicating machine that can make an exact copy of anything’ (BBC Horizon 1964). The technology gained momentum in the 1990s and 2000s as it became one of the most promising ways to directly realise digital design, geometric complexity, parametric modularity and 1:1 prototyping. With its relatively low start-up and production costs, 3D printing has been adopted in numerous industries, from the arts to healthcare. It is, however, affected by several limitations: machinic, volumetric and material.
7 Terrestrial Reef, RHS Chelsea Flower Show, London, 2019. A hybrid garden reflecting on the binary relationship between the built and natural environments as defined by western modernity. It proposes an alternative to cultural associations of ‘nature’ as ‘green’. 8 (overleaf) Quaquaversal Centrepiece was designed for Iris van Herpen’s Paris Fashion Week show at the Musée d’Histoire de la Médecine, 2015. Throughout the show, three robotic arms, disguised as fable-like creatures, manipulated a dress worn by the actress Gwendoline Christie.


The term ‘postdigital’ was coined by the musician Kim Cascone in reference to the context of glitch aesthetics in contemporary electronic music (Cascone 2000). Postdigital can thus be broadly described as translating digital approaches into more organic hybrid forms of digitally aided design. The postdigital is not an anti-digital movement but demarcates an evolution of digital design and theory that postulates hybridity and plurality rather than standardisation and singularity. The prototypes that constitute this research were developed as 1:1 proofs of concept of the potential of making robotic fabrication more dexterous and varied by inventing novel aesthetics, materials, software and bespoke end effectors. As the research progressed, the material palette changed from polymers and concrete to biodegradable clay, soil and mycelium.

9 The Baumit BauMinator® printing one of the ‘teeth’ for Liquid Rock, 2018.
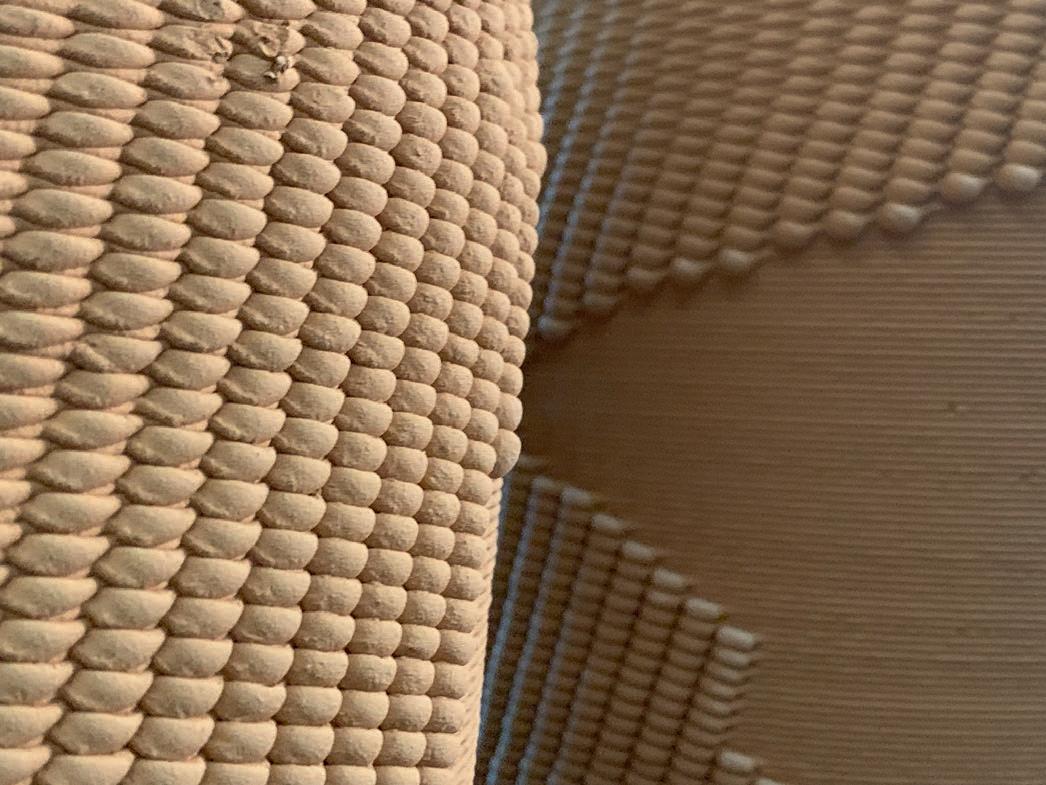
10 Clay Column, 2018. Complex shapes are created using the flexible and agile 3D-printing system.

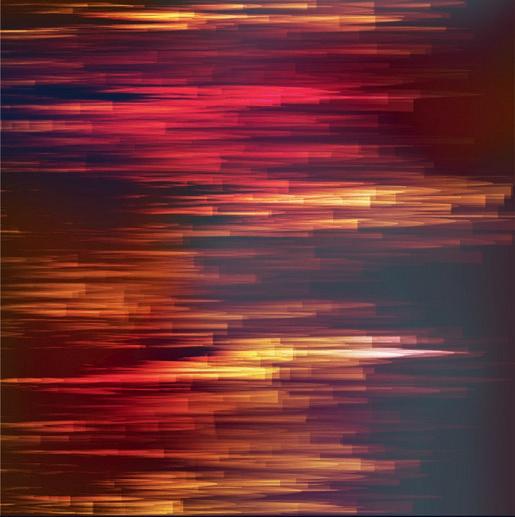
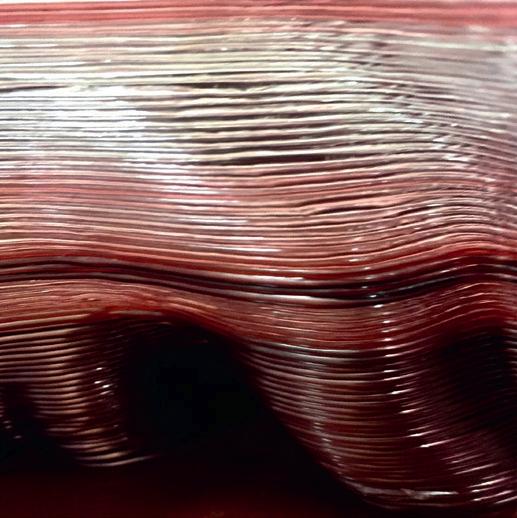
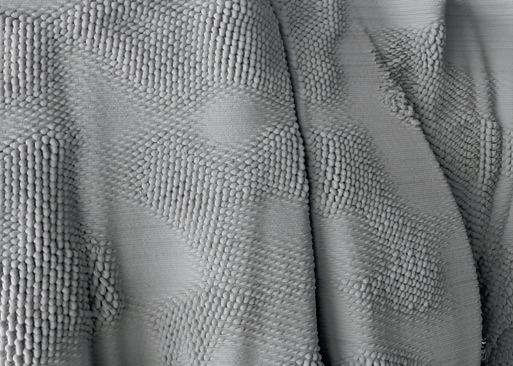
11 Clockwise from top left: television static; Plastic Column, 2018; Liquid Curtain, 2018; glitch background chaos aesthetics of vector. 12 Colour gradients achieved using additive prototyping techniques.
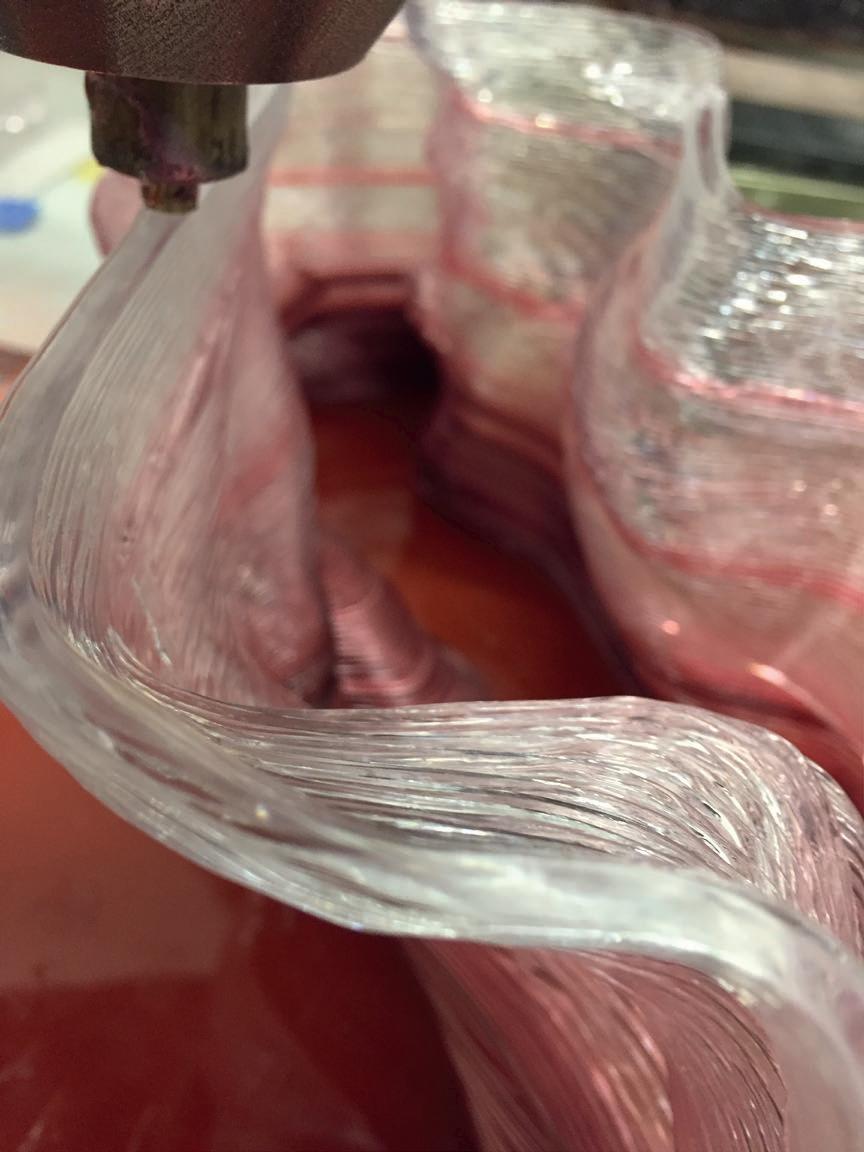
12
As it evolved, the research identified and encountered constraints and affordances, relating mostly to the particularities of the software, hardware, material, weight and influence of gravity, size and shipping logistics, assembly strategies and recycling. A multidisciplinary team was created for each prototype with partners from various fields across industry, science, design, art and fashion. These collaborations resulted in custom-made processes, personalised materials and tailored tools in order to scale-up and push the impact of additive manufacturing rapid-prototyping techniques.
The series challenges architecture’s inertia, in particular the way we think about buildings as immovable, making them ‘nature active’ through various design strategies. Some prototypes do this in a technical way by probing structural constraints and aesthetic potential, while others draw more literally on nature through the use of recycled or biodegradable materials.
13 Plantolith, 2013. Simulating natural processes that blur the boundary between tectonic and natural forms. This unique piece was produced as a uni-material monolith out of silica sand. An additive manufacturing process was used that chemically binds material layer-bylayer into a final shape.
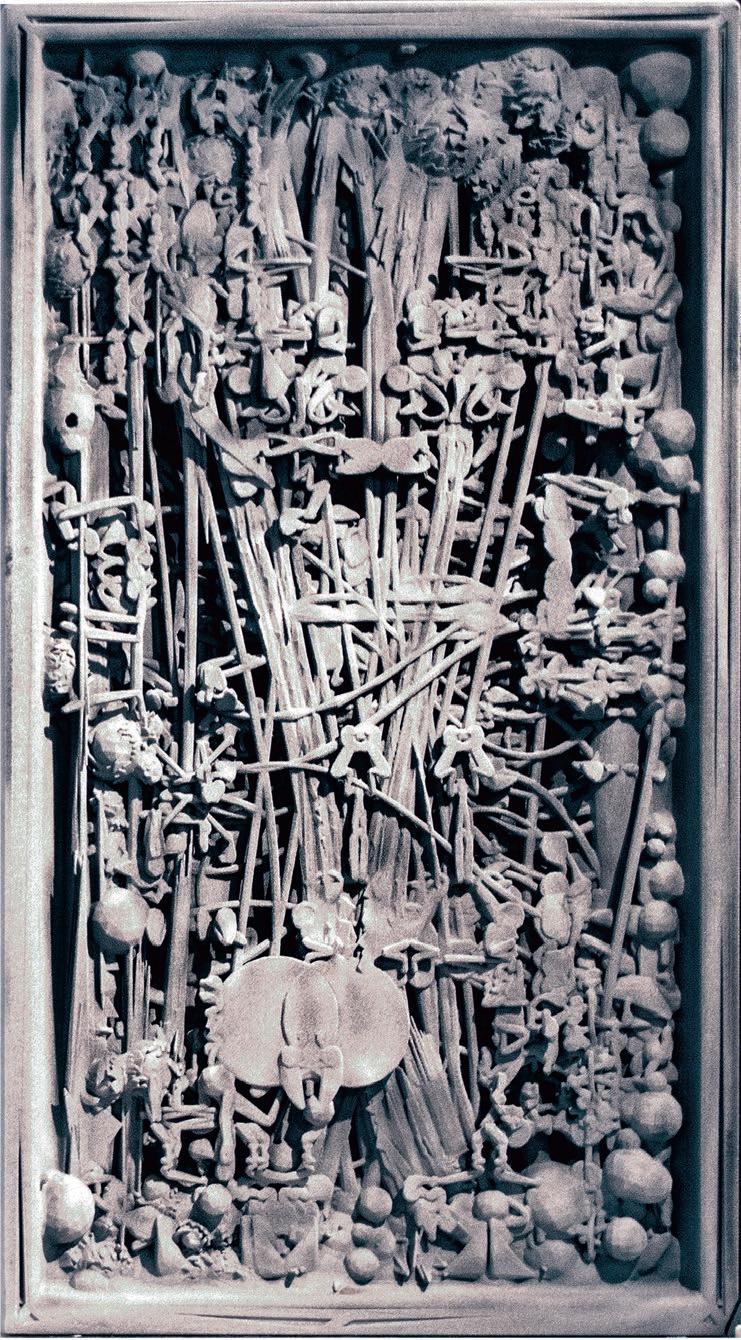
13