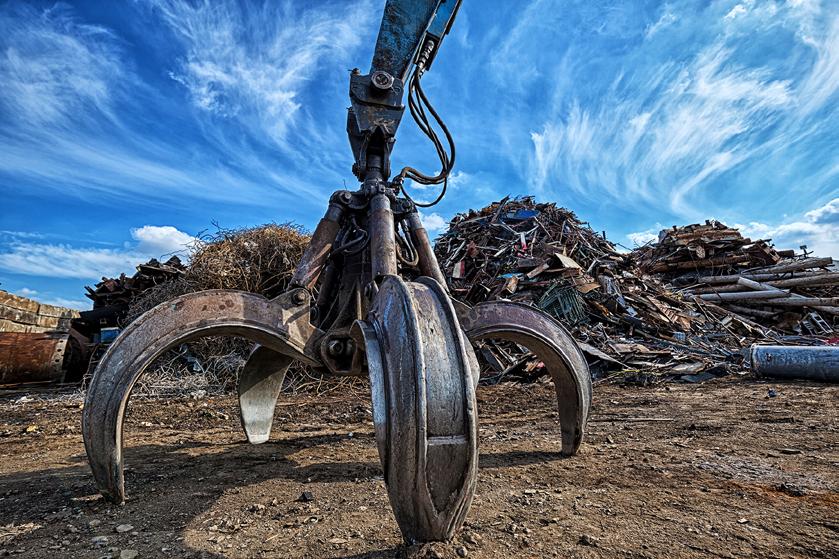
4 minute read
A heritage of engineering excellence
In this issue of Sustainability Today, we are pleased to feature BlakerTech as our Specialist Recycling Equipment Company of the Month.
Blaker, established in 1886 by Alexander Blaker, has a proud history as one of the longest-standing businesses in the Horsham District of West Sussex. Originally based in Islington, the company earned recognition in automobile engineering, including the creation of the award-winning Hallé Spring Wheel, which received a gold medal at the 1905 Liège Universal Exhibition. As the company grew it relocated several times, eventually settling at its current premises in Billingshurst, near Horsham, West Sussex, where it built a thriving business specialising in axle and chassis repairs, heavy plant and equipment repairs, and mobile welding services. Over the decades, the business evolved to meet changing market demands, culminating in the formation of the Blaker Group. One of its key divisions, BlakerTech, now leads in designing and manufacturing specialist metal recycling equipment, continuing a legacy of innovation and engineering excellence.
BlakerTech delivers comprehensive metal recycling solutions tailored to client needs. Beyond manufacturing, services include site audits, design with 3D modelling, proposal development, precision manufacturing, thorough testing, and seamless installation with training.
BlakerTech has produced innovative products like the MagThro eddy current system and SandFlo™ fluidised bed separator, that are used to efficiently separate non-ferrous metals from mixed materials, solving key industry challenges.
The MagThro™ is an advanced eddy current separator, built at BlakerTech’s manufacturing facility in the South East of England. It is known for its exceptional power and performance while delivering precise and efficient separation, ensuring consistent results with minimal effort and downtime. One of its standout features is the positioning of its rotors close to the materials for optimal performance, enabling efficient separation of non-ferrous materials. It has been extensively tried and tested in demanding environments, proving its reliability and robustness under challenging conditions. What’s more, MagThro also stands out for its ease of use, making it a practical choice for recycling plants aiming to maximise recovery rates whilst minimising waste.
A second product worth noting is the SandFlo fluidised bed separator, designed for highperformance material separation. SandFlo is ideal for the recovery of aluminium, zinc, copper and brass fractions from mixed non-ferrous metals in processing plants. Because it produces zero byproducts, SandFlo is a clean solution that requires no disposal of residual materials, and produces cleaner outputs ready for resale. Furthermore, its dry separation process is particularly advantageous in environments where water may be limited.

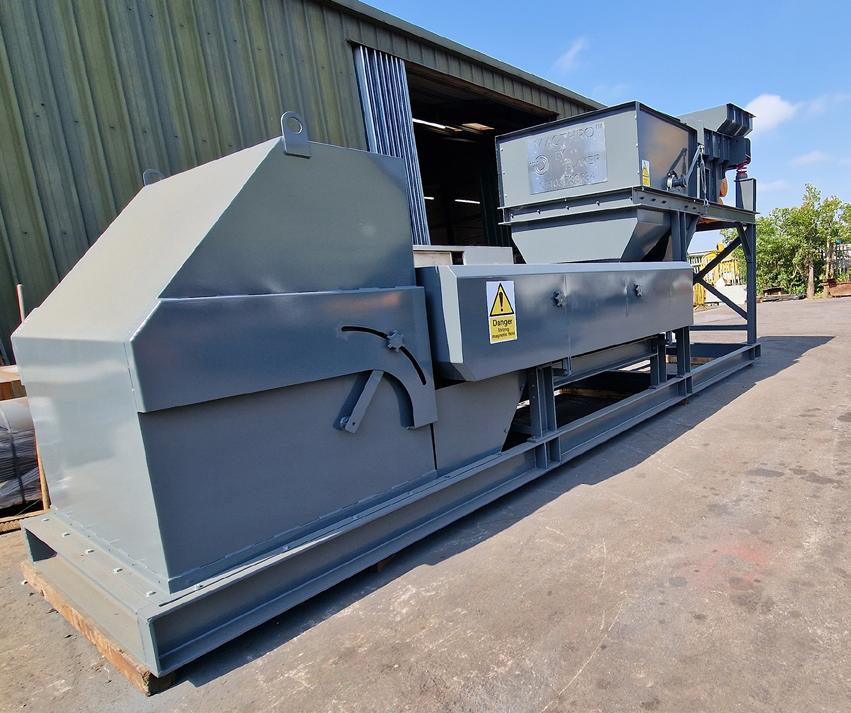
The system is simple and reliable, with no complicated technology to fail, and capabilities of sorting non-ferrous materials by their density screened up to 50mm. SandFlo™ works best when paired with the MagThro , as together, they further refine the outstream, maximising recovery rates. In conclusion, together, these systems save the expense of manual sorting, offering an efficient and costeffective solution for all metal recovery operations.
Following the SandFlo™, BlakerTech has announced that it’s in the final development stages of the Linear SandFlo , which is for more demanding environments and has an operational capacity four times greater than its current model. The Linear SandFlo™ builds on the proven robustness and reliability of the existing SandFlo , ensuring both models remain effective solutions tailored to different operational needs.
Sustainability is a core focus for BlakerTech, that take pride in partnering with local and national UK suppliers to promote responsible sourcing. As the global push for sustainability and circular economies grows, BlakerTech's reliable, robust, and user-friendly systems have become essential for clients striving to meet government-mandated net-zero targets and environmental goals.
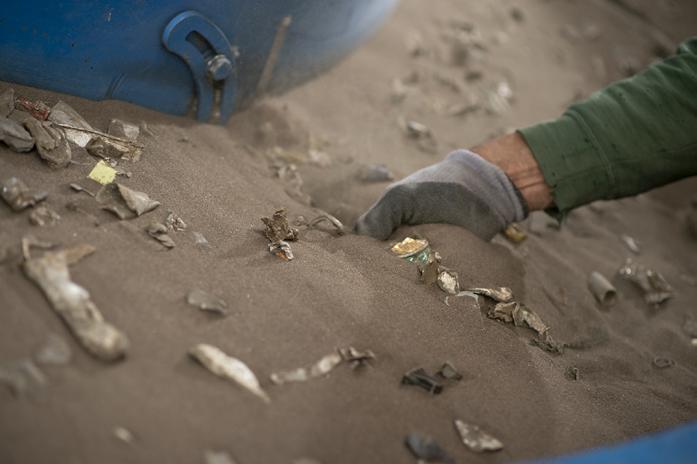
“Our technologies are designed to maximise the extraction of valuable materials while minimising waste. By improving the efficiency of recycling processes, we help reduce the need for raw material extraction and support a more sustainable industrial ecosystem. Additionally, our solutions significantly reduce the amount of waste sent to landfill, providing an environmentally friendly alternative that aligns with global sustainability goals,” stated Robin Plater, Commercial Manager at BlakerTech.
Looking ahead, BlakerTech plans to continue investing in research and development to further refine its technologies and expand its product portfolio. By collaborating closely with system manufacturers and recycling plants, it aims to strengthen its position as a leading provider of reliable and innovative recycling solutions.
T 01403 783634robin@blakertech.comwww.blakertech.com
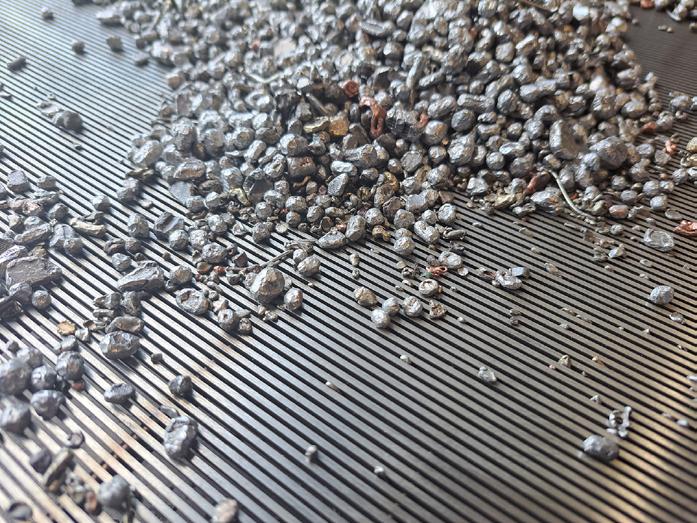