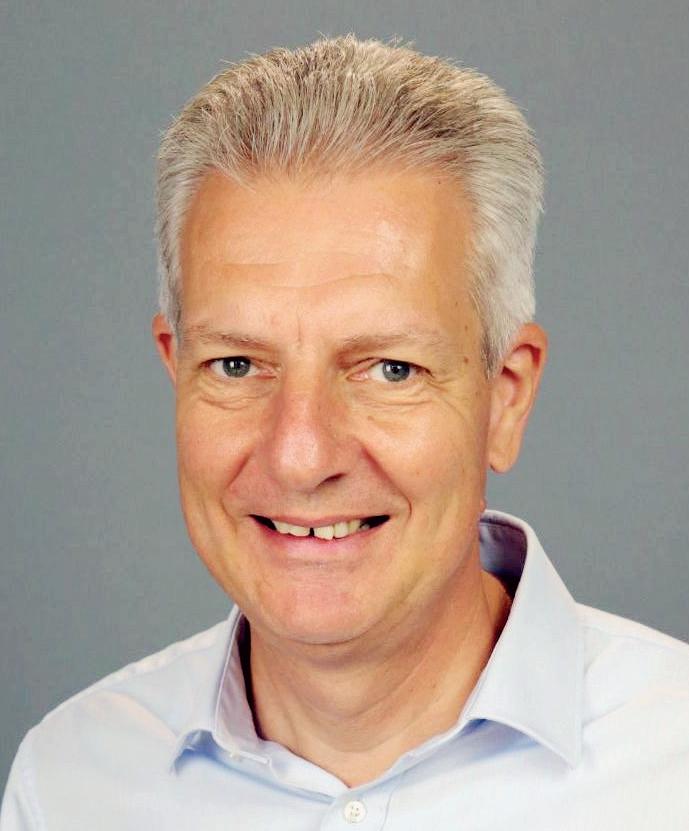
19 minute read
AXELENT SAFETY about standards
Axelent Safety
STANDARDS, STANDARDS, STANDARDS…
Advertisement
At times it feels like we are being haunted by new or updated safety standards. And you may wonder: why are they so important? And how can I find the right standard? 2019 has seen at least the following new or updated “B-Type” standards: » EN ISO 13851 on two-hand control replaces EN 574 » EN ISO 14118 on prevention of unexpected start-up replaces EN 1037 » EN ISO 20607 on instruction handbooks for machinery – This is brandnew and revolutionary, because it is the first standard under the CE regulations to deal with this subject at length.
Additionally, numerous product specific standards (C-Type) have been published last year, for instance on hydraulic and mechanical presses, machining centres etc. Other new product standards are on the way, for instance an update of EN 619 for conveyor systems.
BUT WHY ARE safety standards so important? Simply put, they are defining the minimum safety requirements to be followed. Although only the Machinery Directives and EU Directives are legally binding, the standards have the stronger impact. EU Directives are very general when it comes to the requirements. As an example note the following requirement concerning unexpected movement of parts of a machine: “When a part of the machinery has been stopped, any drift away from the stopping position, for whatever reason other than action on the control devices, must be prevented or must be such that it does not present a hazard.”
This is so general that it raises more questions than it answers: what is mean by “stopped” (shut down or just halted)? What does “drift away” mean? And what situations does this try to refer to? The answers can all be found in product standards (C-Type). They contain information about acceptable operating modes, clarifying what a “stop” is. They
will give information concerning safe shutoff of stored energy that might be released accidentally. That may be the case if compressed air is locked in a cylinder or if a heavy vertical axis could move due to gravity. The C-Type standard names the requirements to follow and then often refers to a B-Type standard for details. That is because many details – such as required safety distances – are applicable to all machinery uniformly. If one would present them in each product standard separately, that would lead to contradictions and cause a lot of double work.
TO FIND THE right standard then, follow the flow chart below. The initial question should always be: Is there a product standard for my product? If there is, take research up from that C-Type standard. If there is no product standard for your product, start with the risk assessment and select the appropriate measures from EN ISO 12100. Both ways you will arrive at the details in the B-Type standards. Read more about this in the Axelent Safety Book.
Y
Primarily apply C-Type Product Standard
Start
C-Type Product Standard available?
N
Perform risk assessment to determine risks
Matthias Schulz
Matthias Schulz is an independent machine safety consultant with 25 years of experience cooperating in a joint venture with Axelent in Sweden and Germany.
Matthias is the author of our popular Safety Book that guides you through laws, regulations, EU directives, requirements and certifications.
Are you interested in a copy?
Contact your local sales representative.
During risk assessment select safety measures from C-Type Product Standard
Research for suitable measures in EN ISO 12100
Research for design details in B-Type Generic Safety Standards
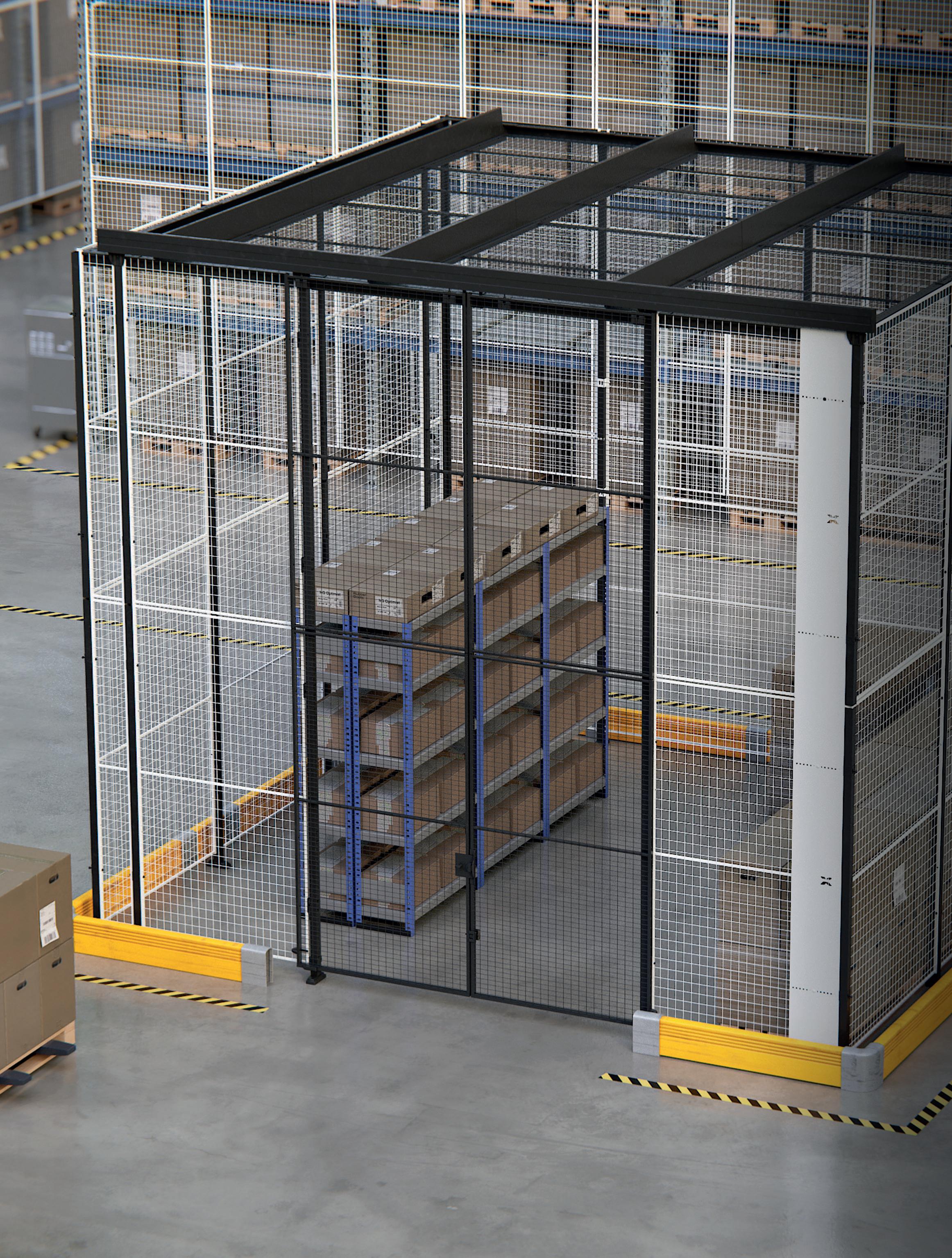
X-STORE 2.0
The new and improved X-Store 2.0 is a flexible modular concept that is easy to assemble and adapt. Let us explain its advantages and how it works.
The new X-Store 2.0 simplifies and ensure stock keeping. But it has several more advantages too. How about the possibility to add a ceiling, dismantling a panel without affecting the panels surrounding it, or by having flexible posts making it possible to build in three different directions including corners?
You can use new X-Store 2.0 either without or with a roofing system:
STANDARD: X-STORE 2.0 - WITHOUT ROOFING SYSTEM
The new X-Store 2.0 replaces the present X-Store and FlexiStore and is perfect to use to when building wall sections within warehouses or other industrial applications. Use it for dividing areas or to build restricted rooms. Many new smart features have been added in order to create more value to the system.
ADDITIONAL: X-STORE 2.0 - WITH ROOFING SYSTEM
When you require a secure way to store high-value items, and/or items which requires extra safety in their warehouse, for example tools, electronics, consumables etc. X-Store 2.0 provides a great solution to make sure the items only are accessible for authorized staff.
The roofing has a maximum width of six meters, but no limitations regarding length. This make it possible for you to choose a system that is optimal for your warehouse.

THE ADVANTAGES WITH X-STORE 2.0
» The possibility to add roofing system in unlimited length » Easily dismantle a panel without affecting the panels surrounding it » A new and unique way to attach the panels to the post » Flexible posts; build in 3 different directions including corners » New joints for smoother and stronger vertical assembly » Since it is available in SnapperWorks, you can easily design it to fit your needs » The X-Store 2.0 wide range of locks and doors are based on X-Guard’s range
More information about the new X-Store 2.0 can be found on our YouTube channel.
Axelent Group
Installation of X-Store 2.0.
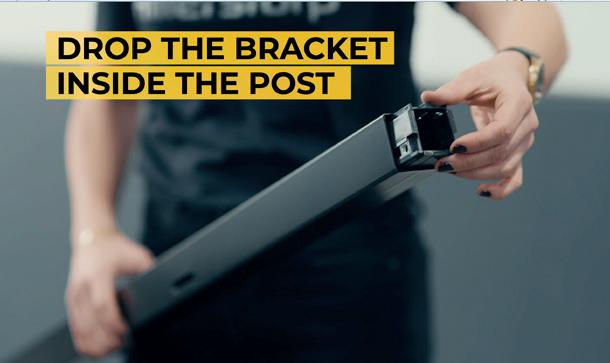
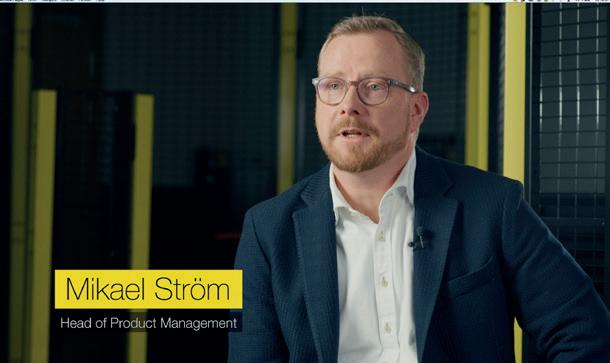
Interview with Mikael Ström.
The new X-Store 2.0 improves your warehouse safety
The new generation of X-Store offers a wide range of improvements and news. All to give you as easy and secure access to your warehouse as possible. Mikael Ström, Head of Product Management at Axelent, gives us an insight.
X-Store 2.0 is the perfect choice for example when it comes to building wall sections within your warehouse or other industrial applications. It may also be used for dividing areas or creating restricted and secure rooms for high-value items or tools and electronics that require extra safety. The new generation of X-Store is a great solution to ensure that these items are accessible for authorized personnel only. – X-Store 2.0 is a completely redesigned product with a lot of new features and improvements. It addresses the same target group as its predecessor, but it is not compatible, says Mikael Ström, Head of Product Management.
ONE OF THE new features of X-Store 2.0 is the unique and quick way of attaching the panels to the post. It is also possible to easily dismantle a panel without affecting the panels surrounding it. The posts are flexible, which means that you now could build in up to three different directions including corners. The floor base on which
MIKAEL STRÖM, HEAD OF PRODUCT MANAGEMENT
the posts are mounted has a new design and can easily be combined with standard height posts for cost efficiency. – The main advantages of X-Store 2.0 are that it is a modular system that is easy to assemble, and that is stable even in superstructure.
The fact that the concept is modular, makes it easy to adapt to a width and height that suits your business. Each individual panel can also simply be heightadjusted and the new joints enable smoother and stronger vertical mounting. Another advantage is that the different colors of the wall and door panels create clear passages. option to add a roofing system or customize the installation with a cutting package and adjustable infill. The ceiling has a maximum width of six meters, but no limitations regarding the length. This make it possible for you to choose a system that is optimal for your warehouse. – The ceiling is easy to assemble and has a good solidity and stability, even though it is not built for walking on. You can choose the roofing solution by a simple click in SnapperWorks.
SINCE IT IS available in SnapperWorks, you can easily design it to fit your needs. The X-Store 2.0 wide range of locks and doors are based on X-Guard’s range.
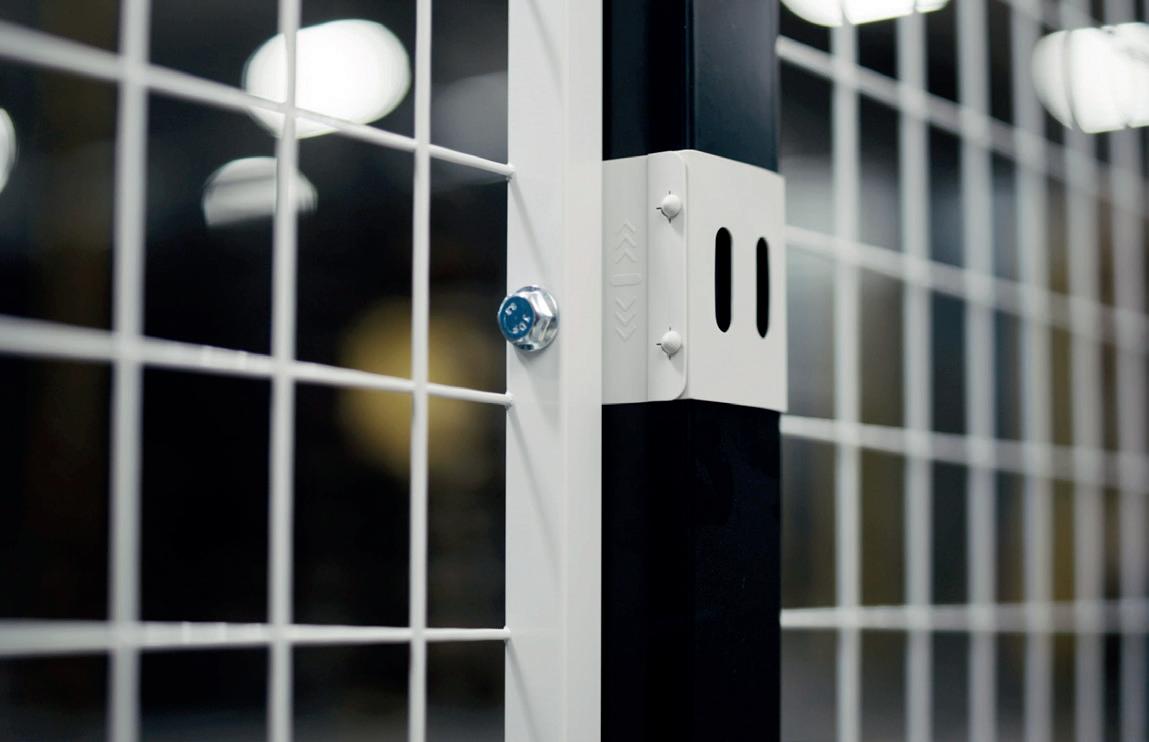
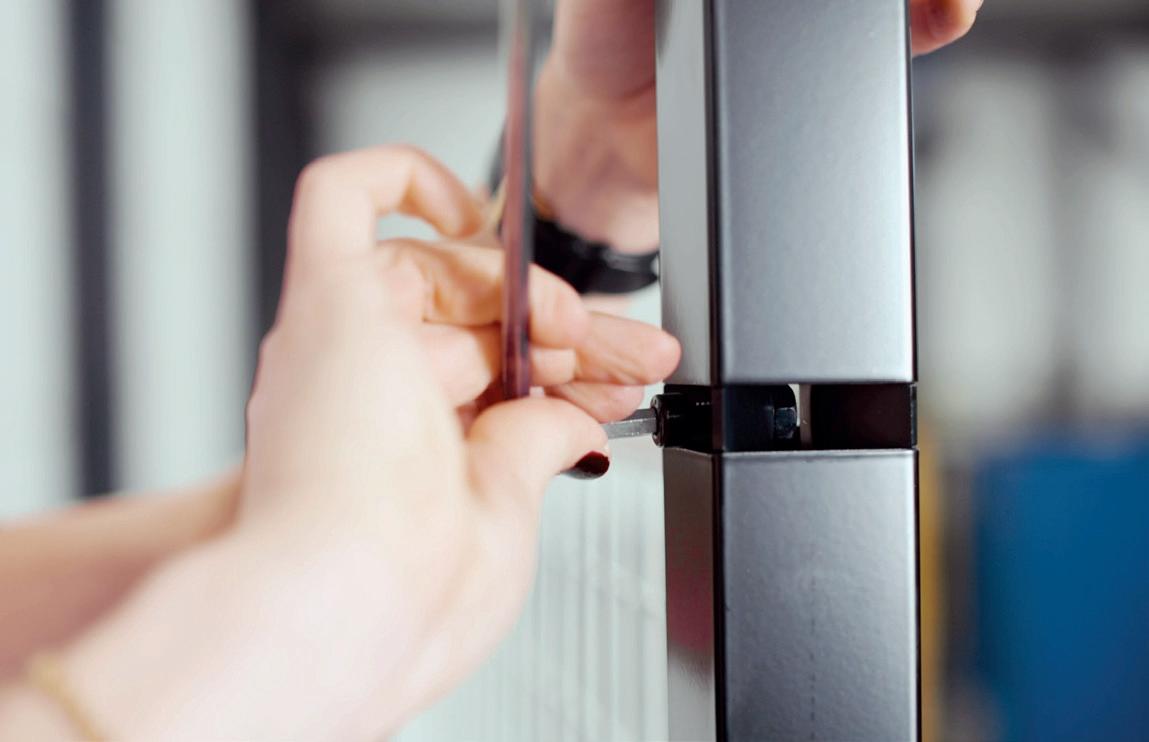
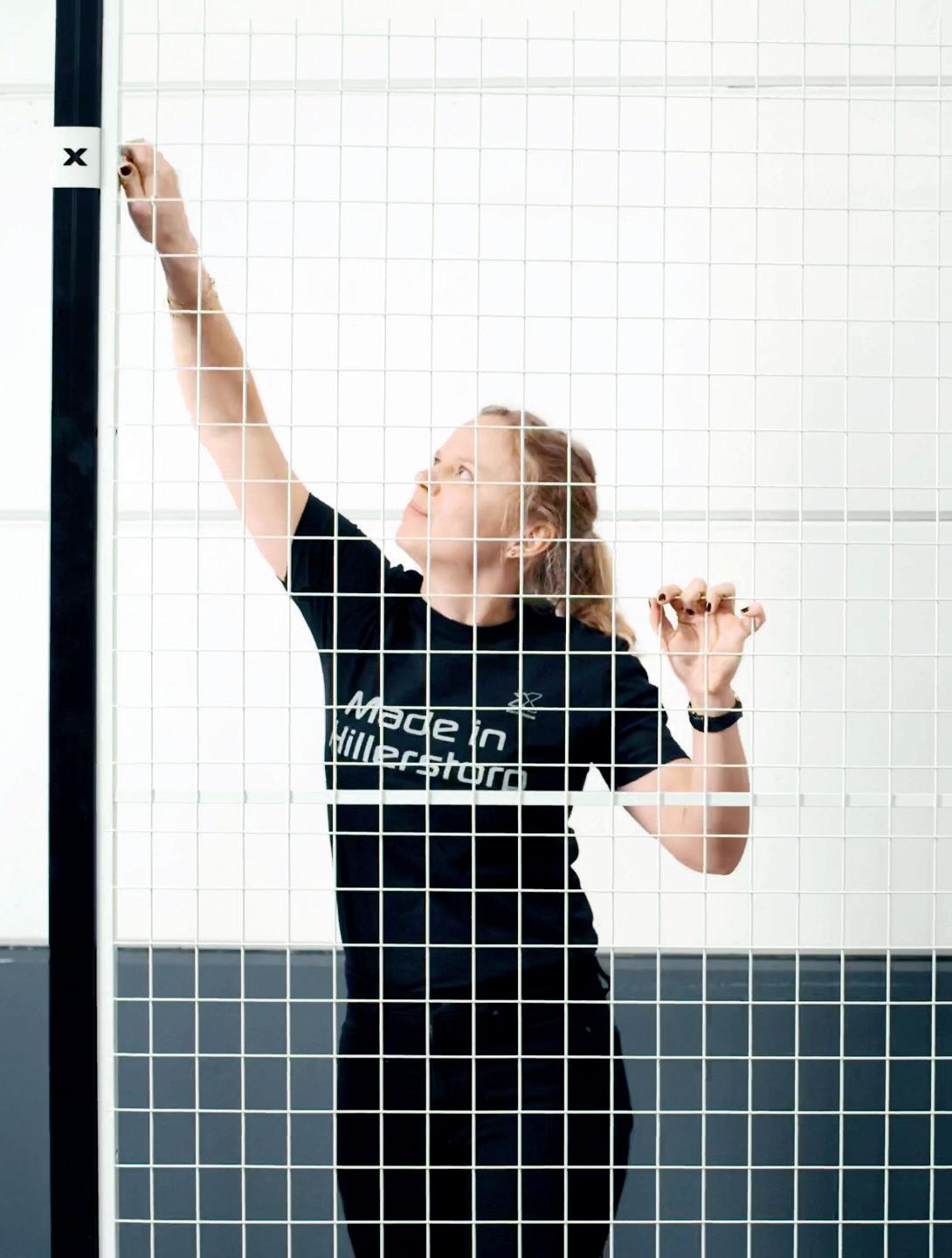
Mikael Ström
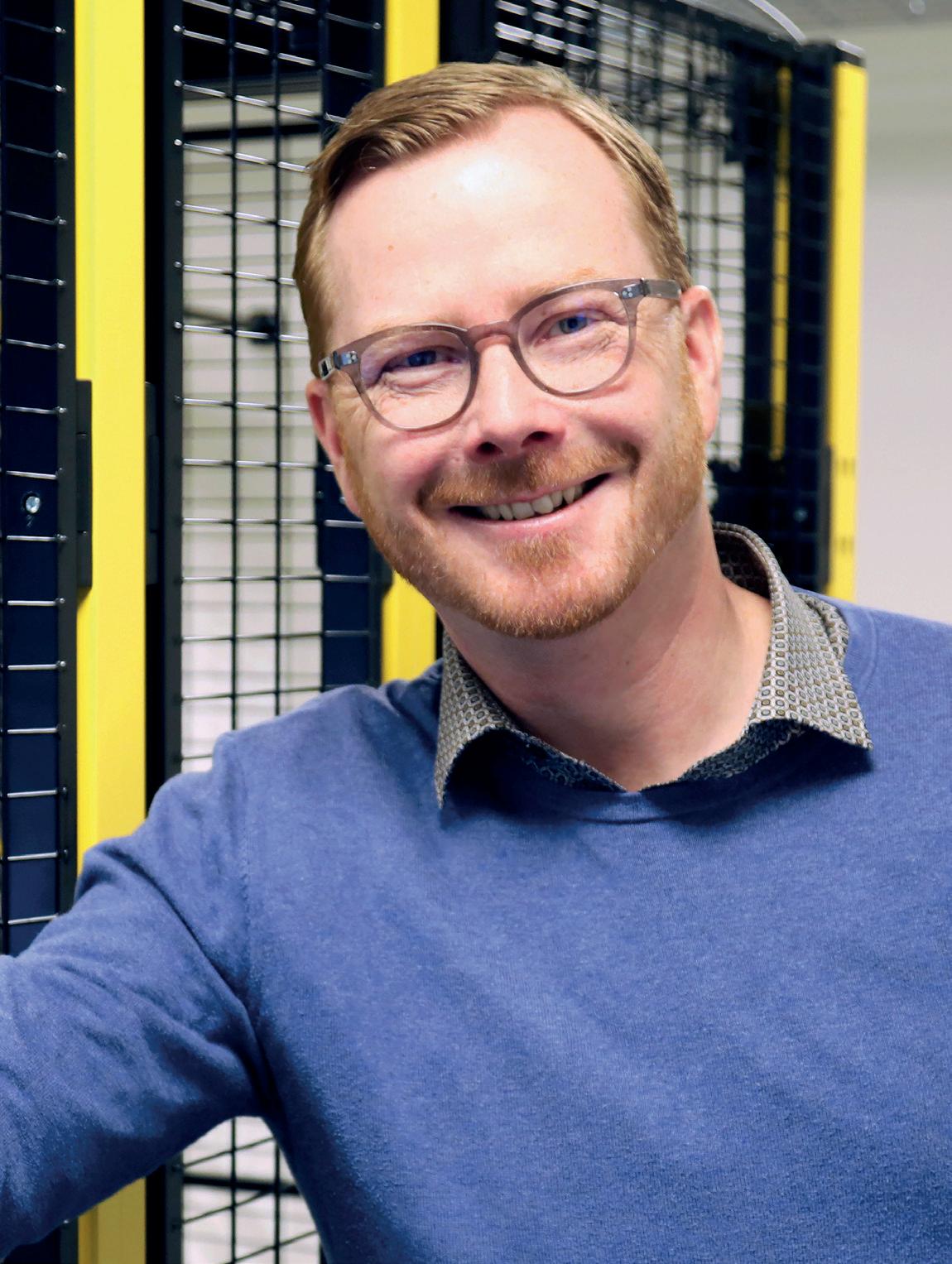
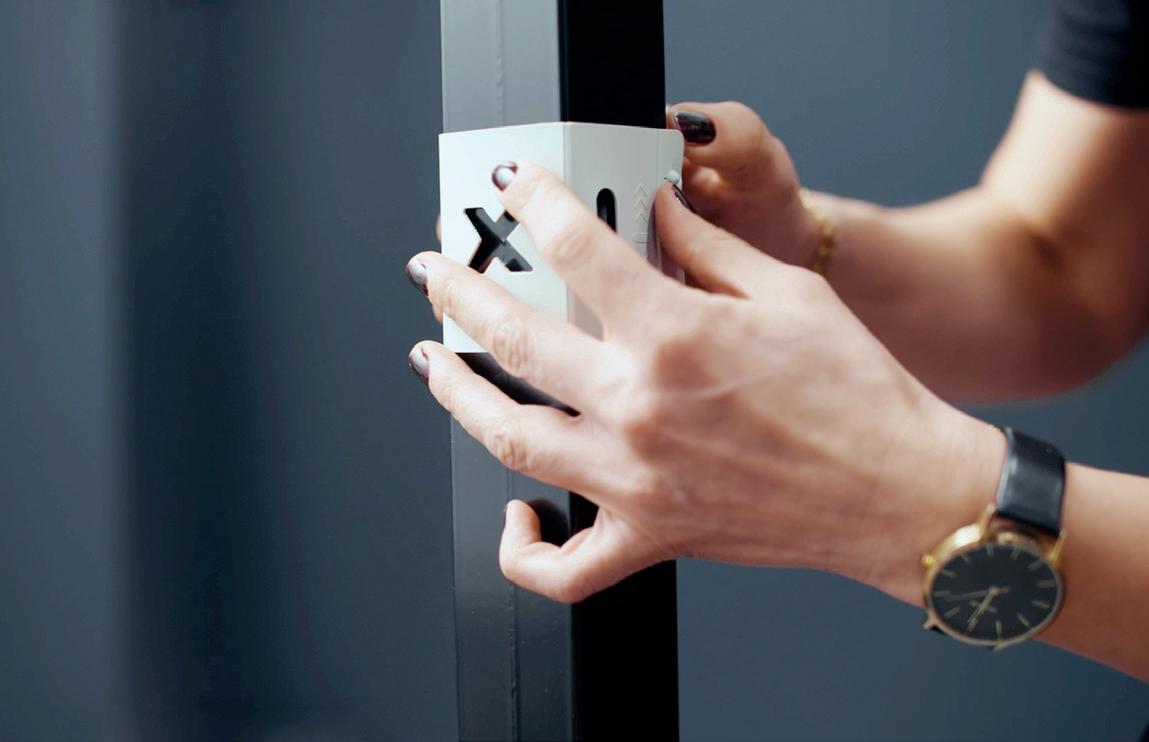

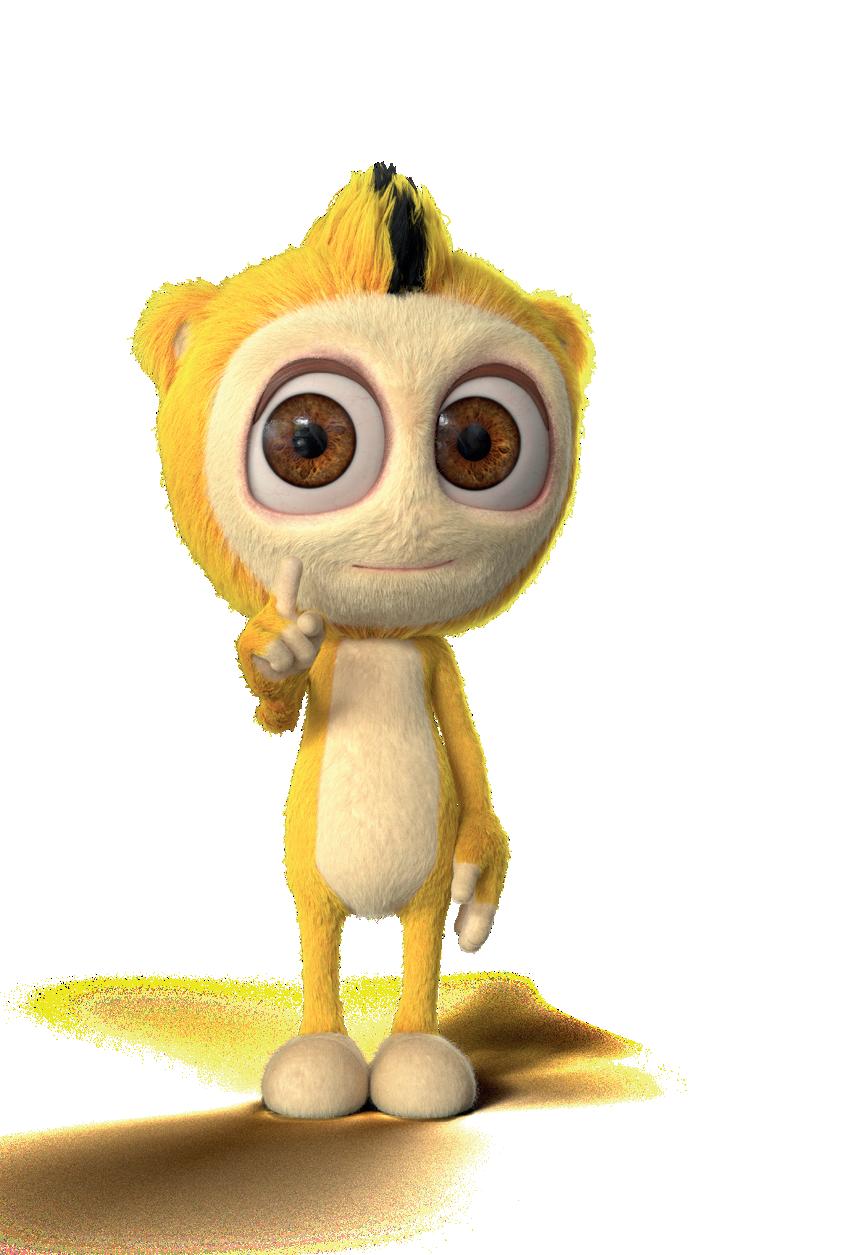

KEEP IN MIND
» Allow for possible future needs and design your warehouse accordingly. » Train and inspire your personnel. » Follow the applicable regulations and enlist help when planning and designing your new warehouse.
BUILDING A SAFE WAREHOUSE
When building a warehouse, there can be many unanswered questions to consider. What are the most important aspects and how do you create a warehouse that is safe for both your employees and your products?
Warehouses can be hazardous environments, especially if designed incorrectly and inappropriately, lacking in safety features or poorly maintained. In Sweden, all companies are required by law to ensure that their employees work in a safe warehouse environment using safe equipment. There are both national and European safety standards to consider when checking whether your warehouse fulfils the requirements.
The Swedish Work Environment Authority has issued provisions (AFS 2006:4), for example, offering guidance on safety as regards pallet racks and other storage racks. The requirements include, for example, racks being marked with maximum loads by section and storage shelf, firmly anchored and fitted with collision and slide-through guards. On an international level, we have the European standards (SS-EN 15635, SS-EN 15629 and SS-EN 15512), stipulating how racking should be sized and designed. These standards describe, among other things, rack design and assembly and the handling of different types of warehouse fittings, from planning to the handling of damaged components.
ALTHOUGH THERE IS still a great deal of variation in compliance with the standards, things are steadily improving. Safety awareness among companies is considerably greater today than it was ten years ago. One of the reasons for this is that today we work at so much greater heights, which means greater demands on safety features. The most common accidents seen in warehouse environments involve collision damage, such as to pallet rack structural components. Goods dropped from forklifts, due to procedural shortcomings or carelessness, are another common type of accident. Poor quality pallets and goods falling from racks due to a lack of safety considerations are other common problems.
WHAT ARE THE most important issues to consider? The key to a safe warehouse is to invest in stable, good quality racking, equipped with upright, collision and slide-through guards, safety netting and, preferably, mesh decking and mesh shelving. Choose a rack that is designed to eliminate the risk of falling goods in the event of a collision. Also keep in mind that the quality of the sheet metal used for the racking can vary greatly between suppliers. Concrete floors and good lighting are essential to ensuring safety as well. As is forklift aisle design, which should be adapted to the operations conducted at the warehouse and the prevailing conditions. Widths and other measurements depend on the type of forklift used.
JUST AS IMPORTANT as having correctly sized forklift aisles is correctly dimensioning the entire racking system. That is, you must use the sizes stipulated in the applicable standards for the intended loads and heights. A common mistake made by many companies is to build a warehouse based on their current needs, without allowing for future developments and flexibility. As such, consider how your business might develop over time and design your new warehouse accordingly. A rack of good quality is a major investment with a long service life and is considerably cheaper if done right from the start, rather than needing to be remodelled, modified and supplemented later on. A rack of inferior quality also requires a greater amount of maintenance and repair, which can prove costly in the long run.
Last but not least, never underestimate the impact of your employees. Committed and well-trained personnel are essential to ensuring safety.
5
TIPS FOR A SAFE WAREHOUSE
1. 2. 3.
4. 5.
Concrete floors. Good lighting. Appropriately designed forklift aisles adapted to your operations. A stable rack of high quality. The right equipment in the shape of upright, collision and slide-through guards, safety netting, mesh decking and mesh shelving.
Globalisation is putting new demands on logistics flows

The world is changing at an ever-increasing pace, and globalisation, digitalisation and technological advances mean we have to be smarter, quicker and more productive. How does this development affect the world’s logistics flows?
According to the World Economic Forum, the pace of change in the world in recent times has been the quickest in 50 years. The past century has seem many businesses step up from regional to global arenas. Physical sales outlets have largely been replaced by webstores. In addition, production and sales in many cases take place in several different countries, which places new demands on supply chains and transport solutions. Globalisation offers many advantages but also poses plenty of challenges. Not least, it requires more efficient and optimized logistics solutions and distribution channels.
GLOBALISATION AFFECTS logistic flows and creates a need to strive for the perfect balance between resource consumption and sales. Delivery service also becomes an increasingly important competitive means. Where we previously competed with other companies we are now competing with the help of material and product flows. This, in turn, places higher demands on ever smarter warehouse and delivery solutions to enable the company to meet the customers’ needs for speed, reliability, adaptability and quality.
As the temporal distance between customer and product decreases, the conditions for the flows in society also change. The right products must be delivered at the agreed time and in undamaged condition. Safer and more efficient transport solutions are thus a must, as well as a rational and resource-efficient logistics system.
AS PRODUCTS ARE produced according to the customer’s wishes and special needs, the logistics chain has also become increasingly complex. This in turn means an increased need for knowledge and technological development within the logistics flow. The same applies to the growing expectations of safety and environmental awareness.
As far as the environmental aspect is concerned, it includes everything from how the products are manufactured and packaged to how they are transported and recycled after consumption.
To succeed in sustainable logistics development in today’s globalised society, we need continued investment in new technology and expertise, environmentally friendly production and smarter and energy-efficient transport solutions.
For Axelent’s part, the environmental thinking and the pursuit of long-term sustainable development permeates all business areas. In addition to its own production of green electricity from wind power and the ambition to supply fully recyclable products, the company uses local suppliers and environmentally certified transport companies as far as possible.
Axelent has also developed its own packaging system, X-Pack 2.0, which utilises a carrier’s cargo space to the maximum, thus reducing the number of transports and minimising transport damage.
90 %

DID YOU KNOW? 90 percent of Axelent’s subcontractors are located within a radius of 100 km.
X-Pack 2.0
A green initiative from Axelent is the new in-house developed packaging system, X-Pack 2.0, which enables customers to have their products plasticwrapped on special pallets along with installation instructions. The packages are tailored to the dimensions of the delivery vehicles to cut down on wasted space and the number of deliveries. The goods are easy to unload and move for speedy installation.
“We developed X-Pack 2.0 in order to find a packaging solution that fully utilised loading space, minimised the amount of transport damage and was easy for the customer to unpack. We also wanted the packaging to leave a good impression on reaching the customer. We are very satisfied with X-Pack 2.0. The amount of transport damage is now next to nothing and we have cut our transport costs while giving the customer a much simpler unpacking process,” says Mats Hilding, MD.
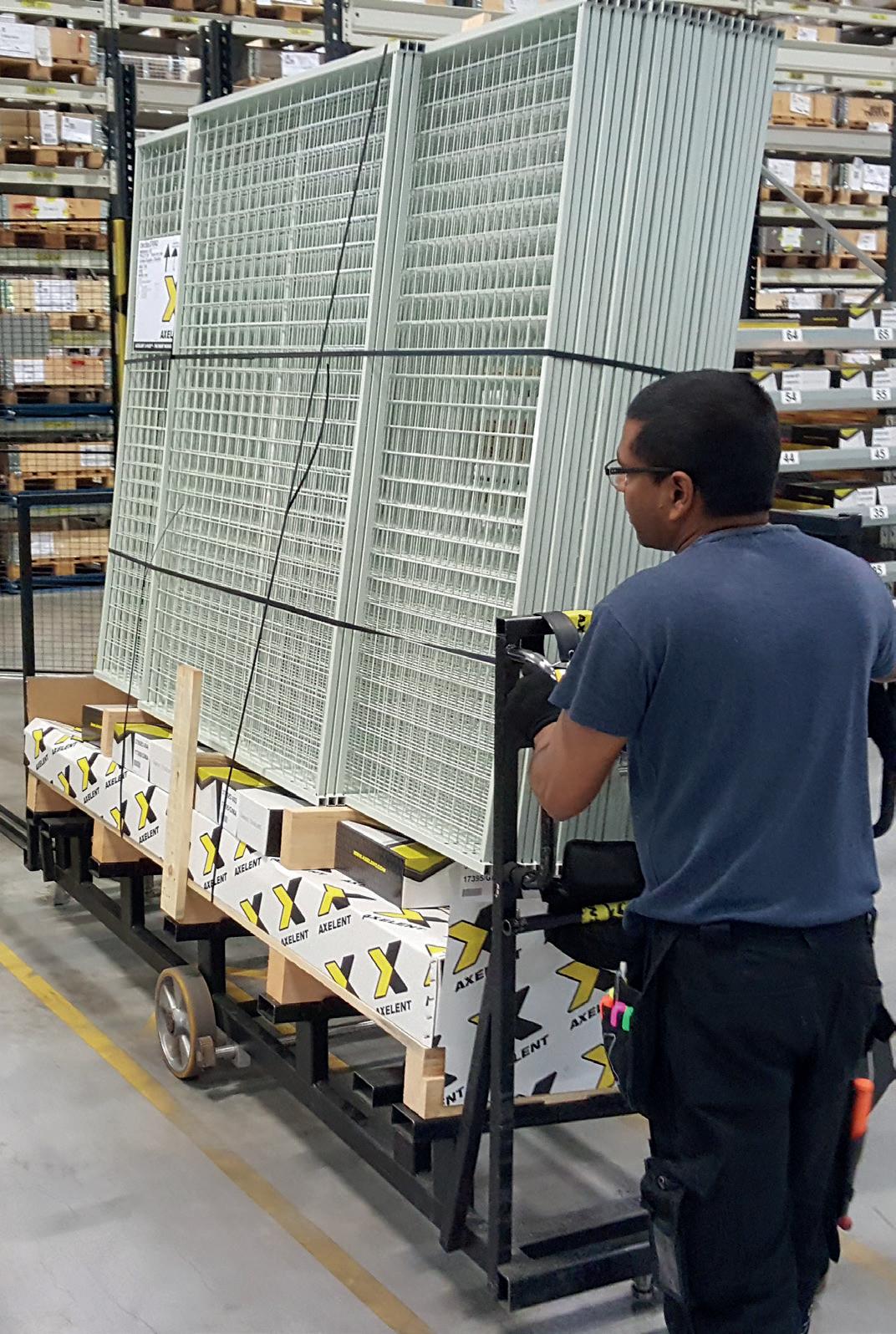
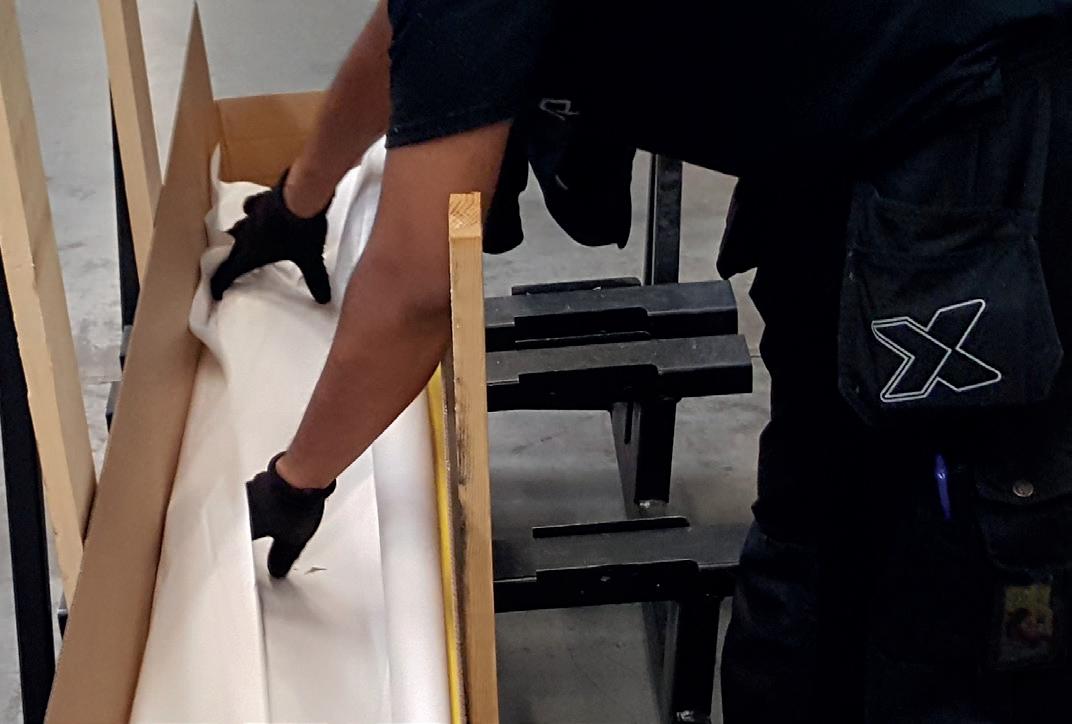

Axelent & EAB ENDURING PARTNERSHIP FOR SAFER STORAGE
Better and safer storage environments comprise an ambition shared by EAB and Axelent. Here we reveal more of the details behind the enduring partnership enjoyed by the two companies.
Erik Andersson, a carpenter by trade, founded the family business EAB in his home village of Smålandsstenar back in the late 1950s. The company was specialised in building interiors forged from metal, starting with banisters. Over the years, the business has evolved to encompass three main product segments – steel buildings, industrial doors and storage equipment.
Although the company has grown and Erik’s sons Per-Åke and Sven-Gunnar have now taken over the day-to-day business, its heart and production remain – as always – in Smålandsstenar.
AXELENT AND EAB have been partners for some 20 years. Axelent is one of the company’s subcontractors in the storage equipment segment, with EAB delivering turnkey concepts to customers. The partnership is mainly centred on products such as mesh shelving, anti-collapse protection and machine guards. ”I guess it all began with a need for the kind of products that Axelent delivers, and we found them to be an interesting and capable supplier. Over the years, our partnership has evolved and grown increasingly stronger, and today they are one of our key suppliers,” explains Magnus Ullerås, project manager and sales manager at EAB. Sven-Erik Andersson, sales manager at Axelent AB, fills in. ”Our partnership with EAB has always been characterised by giving and taking. We help each other out and, in many ways, I guess we’ve developed together. We’ve been open to their needs and those of their customers, striving to resolve any problems as quickly and effectively as possible. And that’s an area where I think we’ve shown great progress.”
THE USUAL PROCEDURE is for EAB to present a drawing or requirements specification describing what they need, in most cases anti-collapse protection or mesh shelving, which Axelent then uses to prepare a quotation. ”For the most part, it involves relatively simple applications and scenarios, but sometimes we stumble upon more complex applications. And in such cases we need to collaborate more closely and intensely. So we cover the whole spectrum, for sure,” says Magnus.
Magnus believes that the underlying reason for this enduring partnership is that Axelent has a good product at the right price. However, speedy feedback and quotations, and the furnishing of solid documentation in the form of drawings and exact prices, also play a decisive role for both EAB and their customers. Sven-Erik Andersson, Axelent

”Understanding and speed are aspects we value greatly, and we always get excellent material to present to the customer.”
As to which trends can be discerned and the future outlook, Magnus believes that increasing safety awareness among customers is a good sign. ”I have complete confidence in increasing safety awareness leading to a growing need for different safety solutions, such as mesh and wire products. So, in my opinion, the future market for these types of products looks very bright.”
Axelent SafeStore at Nowaste Logistics
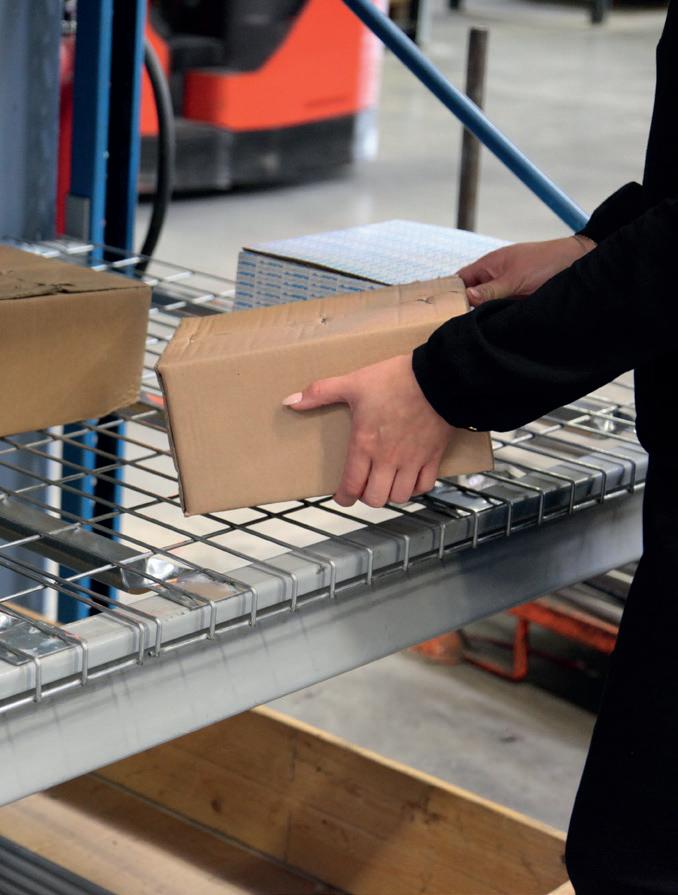
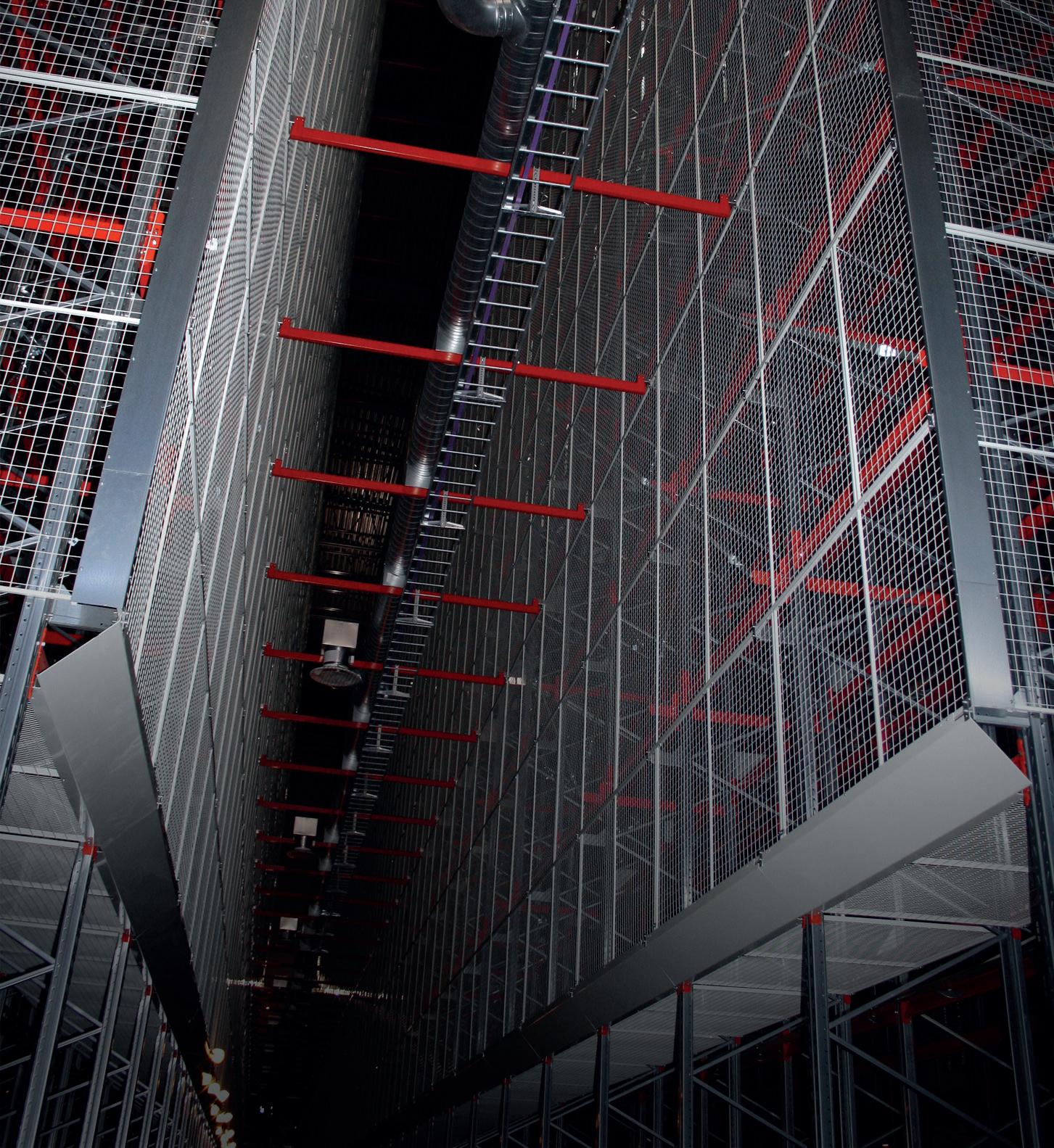
Warehouse interiors company EAB has helped Nowaste Logistics to improve its storage facilities. With SafeStore anti-collapse from Axelent, they’ve created a smarter and safer working environment.
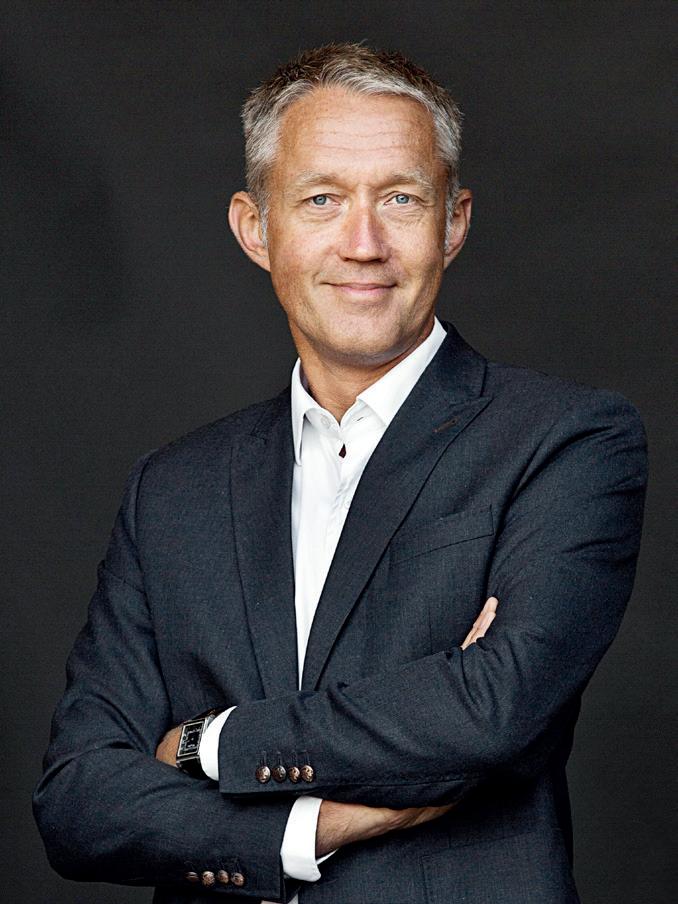
Nowaste Logistics offers tailored logistics solutions to companies in various industries and segments. Customers include Sweden’s largest fruit and vegetables wholesaler, one of the leading hardware store chains and furniture companies.
Since being founded in 2008, Nowaste has grown into one of Sweden’s foremost third-party logistics providers with some 500 employees. On behalf of its customers, each year the company handles 55 million packages and 4.2 million pallets with a total value of over SEK 8.5 billion.
SUCH LARGE QUANTITIES of goods mean strict demands on smart and safe warehousing solutions. So, Nowaste hired EAB to help to make the most of its storage facilities and to adapt the racking to the specifics of each facility as regards, for example, support pillars and roof beams. Among other things, several standalone racks were installed using Axelent’s SafeStore anti-collapse protection. This is to ensure that goods do not fall down the back of the rack, which in this case was facing a forklift aisle.
THE SAFESTORE anti-collapse protection system is based on six standard partitions that can be adapted to most modern shelving and racking systems. The partitions are mounted on brackets fitted to the shelving uprights and are then screwed together to achieve the customer’s chosen height and width. The mesh panels are available with two different mesh apertures and can also be cut to size to ensure a perfect fit. This makes SafeStore equally suitable for anything from a small, manual storage room to a larger, fully automated, high-rack warehouse. Anti-collapse protection ensures a safe and efficient warehouse environment with the risk of falling goods, and hence the number of incidents involving personal injuries and property damage, minimised.
In order to align the mesh panel with the top of the goods, upright support extensions from Axelent were also installed. Magnus Ullerås, EAB
Axelent is one of our regular suppliers for projects such as this. Axelent products combine high technical quality, easy installation and attractive pricing. Together with EAB’s offering, we achieved a good final solution that met the end customer’s requirements.
MAGNUS ULLERÅS, PROJECT MANAGER AND SALES MANAGER, EAB
A MAGAZINE FROM THE AXELENT GROUP
AXELENT AB www.axelent.se teamxtray@axelent.se sales@axelent.se
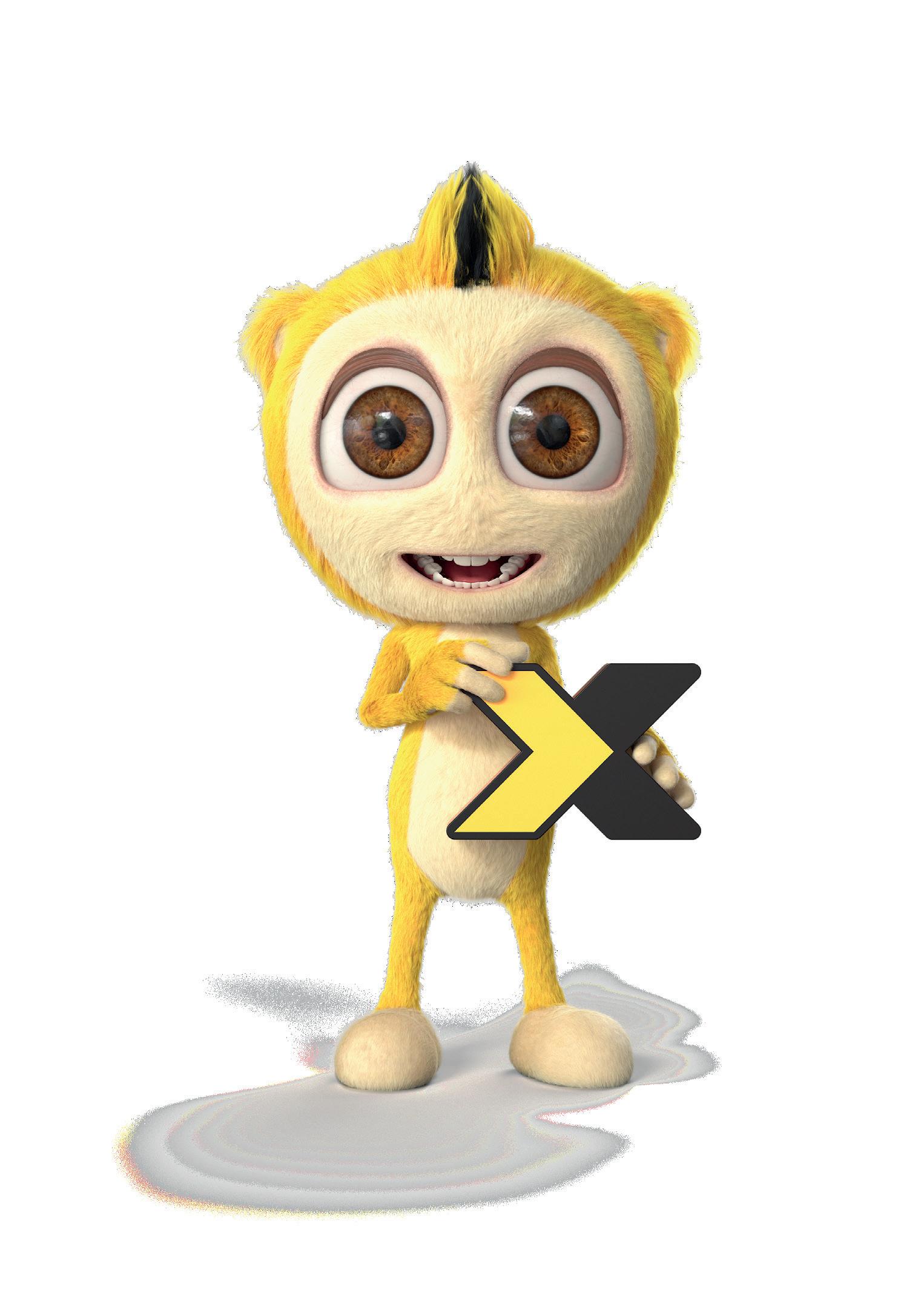
AXELENT ENGINEERING AB www.axelentengineering.se info@axelentengineering.se AXELENT SOFTWARE AB www.axelentsoftware.com info@axelentsoftware.com AXELENT SAFE-X AB www.axelentsafex.se sales@axelentsafex.se