4 minute read
Mitchell International, Inc.
Next Article
by Autobody News Staff
As a dealership-owned collision repair shop, Larry H. Miller Collision Center in Boise, ID strives to be “forward-thinking. We always want to be on the forefront of innovations in the collision repair industry,” said James Clark, body shop manager.
When Clark joined Larry H. Miller Collision in 2008, “We were just getting by. Our workload wasn’t the best, and the shop was struggling for an identity in the market,” he recalled. “We began working with more insurance companies and looking at OE certifications to see what they could do for our business and growth. After 13 years, we have increased our sales by over 125%.”
One of the tools Clark largely credits for those successes is the Mitchell RepairCenter™ shop management solution from Mitchell International, Inc. Larry H. Miller Collision Center began using RepairCenter in its efforts to enhance its professionalism as the business grew.
“Mitchell and Larry H. Miller worked hard and put this together collaboratively. We use the scheduling feature daily to note the date and time for the car’s arrival, repair processes, completion and delivery, so we can compare our cycle times,” Clark said. “The scheduling function is useful during our production meetings with the technicians and as we move cars throughout the day, so we always know where they’re at during production. We’ve also been using the accounting side of RepairCenter, which connects with CDK for our financial statement. This product has been immensely helpful with growing our collision center and with our daily operations.”
Customers at Larry H. Miller Collision know “that we keep up on the latest technology so that there is no doubt that their vehicles are being repaired correctly,” Clark said. “Our estimators and technicians are I-CAR Gold Class certified and take all training due from our OE certifications so that we know what is needed to repair the vehicles back to pre-accident condition and to also have all the vehicles’ technology working properly at delivery; however, technology is changing with each make and model, and keeping up on it has had its challenges.”
ADAS calibration presented a variety of complications for Larry H. Miller Collision.
“We were sending it out to the dealers and losing the control of the repair. We couldn’t control cycle time or really even the cost of the calibration,” Clark noted. “Offering ADAS calibrations in-house with diagnostic solutions from Mitchell was a no-brainer. Having the prescan, post-scan and calibration reports uploaded in RepairCenter allows easy access for the tech and estimator to review them.”
Investing in Mitchell’s MD-500 and MD-TS21 target system allowed the repair facility to manage its own calibrations, increasing efficiencies and profit.
“Once the vehicle is prescanned and our scan tech notes if there are any codes in the system or if there are any ADAS components on the vehicle, it is noted on the windows so that the technician is aware that it will need some sort of calibration,” Clark said. “Having the information at our fingertips is nice. The scan tech performs the pre-scan and notes any DTCs and also looks up OEM repair information, if needed, before handing it off to the body man or letting shop management decide what to do next.
“The MD-500 will automatically upload the pre-scan, postscan and calibration reports to the open RO in Mitchell RepairCenter, where the estimator can see and review them.
“Having the OEM repair information at post scan is crucial because sometimes a code may be for a sensor that was not plugged in or something that may have been missed,” Clark continued. “With the MD-500 scanning vehicles, we are able to access Mitchell TechAdvisor from the device and look at integrated repair procedures in the technician’s stall if needed.”
“Having access to that device in the shop has been a game changer. This allows a higher quality repair and increased efficiency. In the first two months after implementing Mitchell’s diagnostics tools, we generated significant additional revenue. We have also seen a reduction in cycle time by approximately one day, which means we are controlling the repair and cycle time.”
Larry H. Miller Collision Center relies on Mitchell technology to streamline repair workflows and improve the shop’s efficiency, profitability and cycle time. Most importantly, Mitchell solutions have helped Larry H. Miller Collision Center gain control of the repair.
“It’s beneficial to be able to trust one provider to meet so many needs, because communication is always open,” Clark noted. “I know that I can reach out and get any questions resolved in a timely manner. Larry H. Miller and Mitchell have had a long-term commitment to make our jobs as easy as possible, and through our collaborative efforts, it has worked for both of us.”
Mitchell’s diagnostic scanning and calibration solutions have helped Larry H. Miller Collision Center “gain control of the repair.”
Larry H. Miller Collision
Location: Boise, ID
(208) 947-6578 www.lhmauto.com
Company At A Glance...
Type: Collision Repair, Auto Group Facility Employees: 27 In Business Since: 1996 Number of Locations: 10 DRP Programs: 10
Combined Production Space:
25,000 square feet
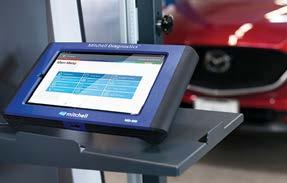
Larry H. Miller Collision Center relies on Mitchell’s technology to streamline repair workflows and improve the shop’s efficiency, profitability and cycle time.
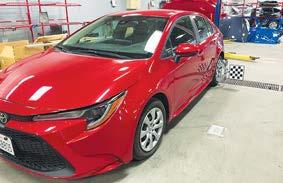
Customers of Larry H. Miller Collision Center have no doubt their vehicles are being repaired correctly since the body shop uses the latest technology, allowing for a higher quality repair and increased efficiency.
Mitchell International, Inc.
6220 Greenwich Drive San Diego, CA 92122
www.mitchell.com
Twitter: @MitchellRepair LinkedIn: @mitchell-international/ YouTube: @MitchellIntl