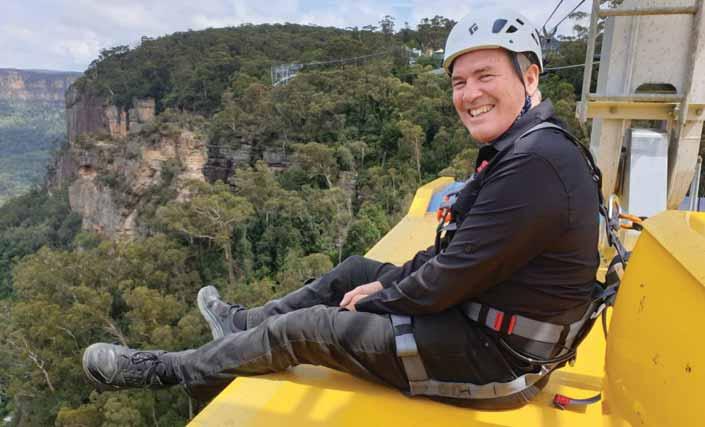
11 minute read
Striving for Safety
David Randall outlines Australia’s legislative requirements for Amusement Devices
Although Australia is not a major manufacturer of amusement devices, there are strict legislative requirements in each state and territory regarding the manufacture, operation and maintenance of amusement devices. AS/NZS 3533 Amusement Devices and Attractions series was developed as a guide for the requirements for managing amusement devices.
Advertisement
In some states, this guide is mandatory, such as South Australia and until recently Western Australia, as it is referred to within their legislation and in other states and territories, it remains a best practice model as it is referred to in Codes of Practice which are again enforceable by law. There are various requirements imposed upon users and importers of amusement devices and I have summarised these as follows.
Design Registration For an amusement device to be operated in Australia, it must
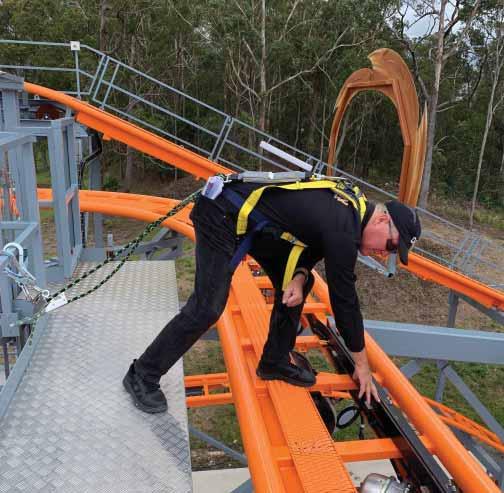
David Randall at work (and below).
have a design registration number. To get a design registration number, the purchaser must have the ride independently verified that the ride is compliant to the standard to which it was manufactured.
In Australia, we can use European, Australian or American standards as the reference documents. To achieve design verification, the process should be that the owner engages registered professional engineers within each discipline to review the various functions of the ride. In most cases, the following engineering professionals will be required: •A safety engineer to review the overall compliance of the ride against the relevant standard to which it was manufactured. The safety engineer will be a qualified engineer in a discipline such as mechanical engineering with an auditing and safety qualification. •A mechanical engineer to review the design of the mechanical components using finite element analysis modelling to ensure appropriate factors of safety have been achieved in the design. •A structural engineer will be engaged to determine the appropriate foundations for wind loading and that the structure is suitable for the loads imposed upon it during operation.
This is a verification against the designer’s specification. •A control systems engineer will be engaged to ensure the control systems are compliant with the relevant standard.
Significant work has been undertaken by the Regulator to ensure that any ride over 10 years of age has had its control systems reviewed to bring them up to current requirements. •An electrical engineer will be engaged to ensure that all electrical wiring and circuits are compliant with local regulations which refer to AS/NZS 3000.
As part of the process, the DRA Safety engineer develops the following documents to ensure the maintenance requirements of the ride satisfy both the Original Equipment Manufacturer (OEM) and AS3533 requirements: •A critical components list (a component that if it fails will lead to damage of persons or property) with full non-destructive testing (NDT) requirements detailed for the user. •Restraint risk assessments to ensure the restraint complies
for the acceleration forces experienced within the ride. This is a critical assessment, as failure to comply will prevent the ride from being granted design registration and thus operation in Australia. •Inspection checklists based on the OEM and AS3533.3 requirements. If variations from the OEM maintenance requirements are requested by the owner i.e. greasing monthly instead of weekly, then this must be approved by the Safety Engineer and documented in a management of change process.
Once this work has been undertaken, each specialist engineer will complete a design verifier’s statement which is attached to the application for design registration. This is then scrutinised by the Regulator (state government workplace health and safety departments/agencies) to ensure all elements have been completed appropriately before a design registration number will be issued.
Once a design registration number has been issued, then the user can apply to the Regulator for a registration number which can then allow the ride to be operated. In some states, registration is required annually such as in Queensland, in other states it is a five yearly requirement while in Victoria, registration is no longer required.
In some cases, with the design registration of amusement devices, the above process is not adhered to, and the design registration is completed by a single engineer who is not competent in all technical aspects of the ride. The Regulator in some states will accept the single engineering sign off on the Design Registration application form. This may result in amusement rides being potentially operated which are not compliant with the relevant standards.
DRA recommend that owners of rides arrange to have structural, electrical, mechanical and control systems sign offs for all rides as part of their Design Registration application with the following mandatory documentation developed and submitted with the application: •Restraint risk assessments to provide evidence the restraint is a suitable classification for the amusement device. •The Non-Destructive Testing (NDT) and Critical Components List for the ride for annual inspection requirements. •Inspection schedules to the OEM with any variations justified and approved by the relevant Engineer.

Annual Inspections State Regulators require that every operator of a ride have an annual inspection performed by a competent and qualified engineer to ensure that it has been maintained and operated to the OEMs and AS/NZS 3533 standards. There are specific criteria within the Regulation which must be assessed by that Engineer. The criteria are as follows: •That the operational history since the last annual inspection has been checked. •The amusement ride logbook is up-to-date. •That maintenance and inspections have been undertaken and recorded within the logbook. •That non-destructive testing and other tests have been conducted and records are maintained. •Electrical inspections in accordance with AS3533.3 clause 11.4.3 have been conducted and there is an electrical statement provided by a qualified person stating compliance with that requirement.
The annual inspection requirements, although specified in legislation, are completed differently by the various engineers in the industry. This lack of consistency is concerning, and it is the Regulators responsibility to audit these reports to determine whether or not the Engineer has completed the task competently.
In the case of DRA, a detailed report is developed which is 80% auditing of records and 20% inspection of the ride. For a large class type 5 roller-coaster, two days for two engineers may be required to complete the inspection and report and with a smaller class type 2 merry-go-rounds, a half to three-quarters of a day will be required.
Issues that are recorded and reported in DRA reports are as follows: •Full review of the logbook including all items recorded for the past 12 months. •An asbestos register review and review of flammability tests of materials (if applicable). •An audit of instruction and training for operators of the device. •An audit of training and assessment of maintainers of the device. •A review of all maintenance records that have been completed and authorised appropriately. •A review of any repairs and alterations that have been made to ensure that engineering principles have been followed and engineering sign-offs completed where required. •That a critical components list has been developed and reviewed including the development of non-destructive testing requirements. •A review of the NDT records developed by the testing authority.
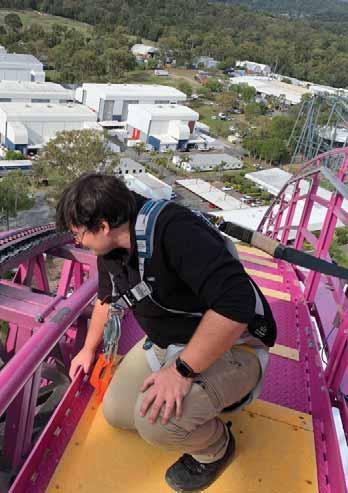
Rollercoaster Credit: pexels via min an.

Once the information has been identified and recorded in the report, the inspection of the ride is conducted during its operation along with the performance of the daily inspection with staff. The report will then include the following elements: •That the ride is operated as per the manufacturer’s requirement. •That the patron restraints are effective, and the loading plan is followed. •A critical inspection of key elements of the ride i.e. envelope intrusions, suitable foundations, patron access, controls, interlocks operational, signage is clear etc. •Emergency plans are current and staff records are available for training in those procedures. •Noise level assessments have been completed at least once every five years and appropriate control measures taken. •That all electrical equipment is compliant with standards with no double-adapters, RCD protection is in place, switchboards are well labelled etc. An electrician will be required to provide a report that they have inspected the ride and it complies with the electrical requirements detailed in AS3533 Section Clause 11.4.3. •Control systems function as designed and a full functional test is conducted.
This report with recommendations for continuous improvement is provided to the owner and a summary report in a one-page format is provided to the Regulator for registration purposes. Unfortunately, as the above process is not mandated by Regulation, some engineers may only provide an inspection of the key elements of the ride. This creates an unlevel playing field for engineers, as the diligent engineer who ensures the ride is being operated and maintained safely cannot compete effectively with an engineer that gives the ride a quick visual inspection and certificate.
David Randall at work.
In the past, the Regulators who should be ensuring standards of inspection are maintained would generally only look for the logbook entry that an annual inspection has been completed by an Engineer without any consideration of the completeness of the inspection process.
However, in recent times, Regulators during their inspection of amusement rides, have demonstrated that they review the annual inspection report provided by the engineer to ensure it is complete with appropriate electrical signoffs and covers off the elements detailed above with evidence provided. If no report is available to back up the annual engineering certificate, then the Regulator has the ability to prohibit the ride from operation.
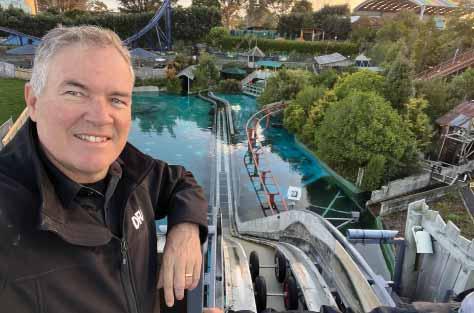
Major Inspections There is now a legislative requirement in Queensland for major inspections to be conducted every 10 years or upon recommendation of the consulting engineer. For a mobile ride, a 10 yearly inspection will require the ride to be completely dismantled and all components inspected, repaired or replaced as required.
In many cases, this will require the ride to have its basic structure abrasively blasted, full non-destructive testing completed on all welds and repairs made before being reassembled.
This process if completed properly will ensure any potentially hidden defects which are not detected during annual inspections can be addressed to ensure continued safe operation.
An annual inspection certificate cannot be issued by an inspecting engineer if a major inspection has not been completed in the past 10-year period and hence the ride cannot be registered and therefore not be operated.
In other states and Territories, this requirement is not mandated by Regulation but as the major inspection requirements are detailed in AS3533.3 and this standard is referred to in the Code of Practice - Managing the Risks of Plant, the requirement to comply is a “should”. A ride operator would be hard pressed to prove due diligence if an incident with their device occurred and the major inspection had not been completed.
Major Inspections Recommendation Legislate the requirement for all amusement devices in all states/territories to undergo the 10 yearly major inspection as is required in Queensland.
Engineers The legislation in each State requires the person performing the inspections to be competent, i.e. possess the skills and knowledge to perform the task, but this is self-regulatory. There is no requirement for engineers to demonstrate their competency to perform inspections of amusement devices.
An engineer in QLD must simply be a Registered Professional Engineer Queensland (RPEQ), and will be able to conduct inspections and sign off rides with minimal knowledge of the ride complexity. To practice in this area, it is a requirement for the engineer to hold valid professional indemnity coverage in the area they practice, and very few ride operators check the validity of the engineers insurance.
It should be standard practice for all amusement device operators to request a current copy of the engineers insurance policy and check that it covers amusement devices, has $10 million coverage and is covered by a reputable company.
Within the Board of Professional Engineers Qld there is an area of specialist classification for inspection of amusement rides and devices, but the requirement to hold this area of competence is not yet mandated. Unfortunately, being a new category of classification, the criteria for the competency assessment is still in development.
Engineers Recommendation The Board of Engineers develop assessment criteria and experience requirements for entry into the professional area of “Inspection of Amusement Rides and Devices”.
The Board of Professional Engineers require the engineer to provide a copy of their professional indemnity insurance as evidence as part of their application and the Board checks it covers the relevant area of practice.
Summary Australia has very detailed legislative requirements for the operation and maintenance of rides to ensure public safety. Regulations apply to both fixed and mobile rides and are enforced by the Regulators of each state and territory. Harmonisation of the legislation across Australia has ensured a consistent standard, however there is still variations that need to be addressed.
The Engineers inspecting the rides are inconsistent with their approaches to annual and major inspections, and this inconsistency can lead to key inspection criteria being missed resulting potentially in accidents.
Any accident is bad for all operators in the industry and hence standardisation of the inspection process, regular audits of the inspecting engineers by the Regulator and better assessment requirements for inspecting engineers coming into the industry could only improve the current situation. David Randall is Chief Executive of DRA Safety Specialists He can be contacted on 0438 268 279, E: davidr@drasafety.com.au

Amusement rides. Credit: pexels via Pat Whelen.
Latest installa on at the City of Sydney’s Gunyama Park Aqua c and Recrea on Centre

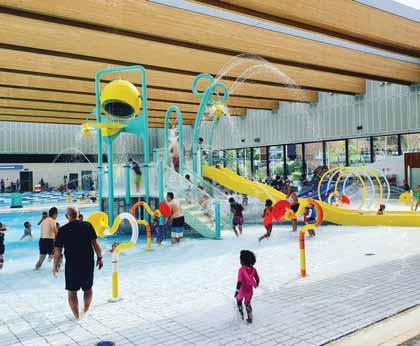

We love designing and delivering aqua c playgrounds and customed themed waterparks
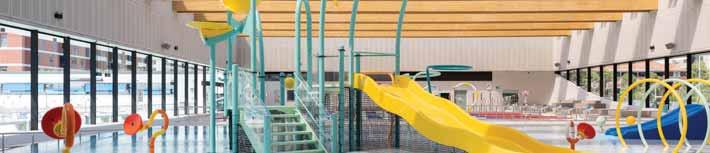