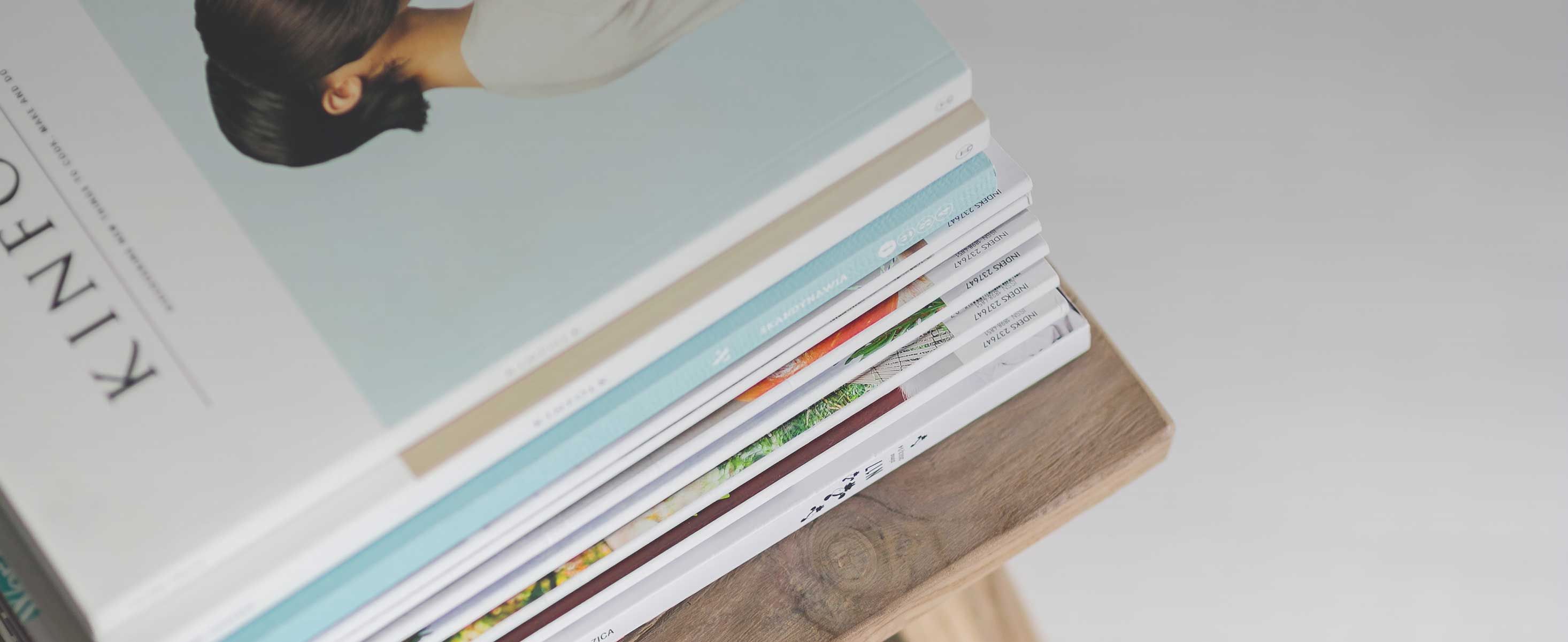
2 minute read
HAPPENINGS ONLINE
Multidisciplinary research team works with Toyota to explore creative safety devices
Two Auburn Engineering professors, Russell Mailen, assistant professor in aerospace engineering, and Chad Rose, assistant professor in mechanical engineering, are partnering with Toyota Research Institute North America to develop a potential solution that might trim emergency reaction time and save lives.
The goal of their project, “Conducting Polymers as Non-Woven Fabric Sensors to Enable Novel User Interfaces,” is to create smart, flexible human interfaces with embedded sensors capable of measuring key information from the wearer or operator and using the signals to adapt their environment. In other words, wearable technology capable of capturing a motorist’s tension in real-time and delivering this information to the automobile so it reacts accordingly to the environment.
“The proposed research seeks to significantly improve the human-machine interface of these next-generation devices through the integration of conformal and unobtrusive force, surface electromyography and electrodermal activity sensors,” said Mailen, the project’s principal investigator. “These nextgeneration devices will be poised to overcome fundamental challenges that exist at the physical and neural interfaces between humans and machines. A machine which can detect both gross control inputs – a turned steering wheel, a button or voice command – will be able to better respond to the human as well as the environment. Tighter coupling between the human and the machine will enable faster, higher resolution communication from the human’s advanced sensors and highly refined internal models, meaning the eyes, ears and experience currently not available to smart devices such as exoskeletons, prosthetics and vehicles.”
Junior 1 of 3 selected nationally for 2023 Women in Motorsports initiative
Raegen Moody, a junior in mechanical engineering was one of three chosen for the 2023 Women in Motorsports (powered by PNC Bank) initiative with Chip Ganassi Racing. This isn’t just any internship with just any NTT IndyCar Series team. A powerhouse in open-wheel motorsports, Ganassi Racing fields cars used by defending Indianapolis 500 champion Marcus Ericsson, six-time series champion and 2008 Indianapolis 500 winner Scott Dixon, 2021 series champion Alex Palou, and twotime Indianapolis 500 Takuma Sato, among others.
“I’m excited to have the opportunity to learn from team members within this organization,” said Moody, a Cedartown, Georgia, native. “I can’t wait to learn from the other women coming into this program with me and from the incredible women mentors at Ganassi Racing. I grew up playing competitive sports. This is a chance to combine my engineering skills with that competitive spirit as part of a team.”
Aerospace engineering research team wins Solid Rockets best paper
Two aerospace engineering professors, Roy Hartfield and Joe Majdalani, along with doctoral candidate Griffin DiMaggio and alumnus Vivek Ahuja, were awarded the 2022 Solid Rockets Best Paper award at the SciTech ’23 forum, held in January in National Harbor, Maryland, and sponsored by the American Institute of Aeronautics and Astronautics. A record 2,700 papers were presented.
The paper, “Solid Rocket Motor Internal Ballistics with a Surface-Vorticity Solver,” introduces an innovative and robust computational approach that is capable of translating panel codes, which have been traditionally developed for the purpose of predicting the external aerodynamic performance of air vehicles, to the internal flow field characteristics of solid rocket motors.
“This study shows that an enhanced panel code can resolve internal rocket flow fields with a striking level of fidelity and with such a degree of computational efficiency to make it valuable in the conceptual and preliminary design of rocket motors,” said Majdalani, the Hugh and Loeda Francis Chair of Excellence. “In this process, the vortex paneling approach embodied within FlightStream is refined using boundary conditions appropriate for solid rocket rotational flows. The simulation results are then compared to existing analytical solutions for simple chamber configurations exhibiting small taper and uniform headwall injection.”