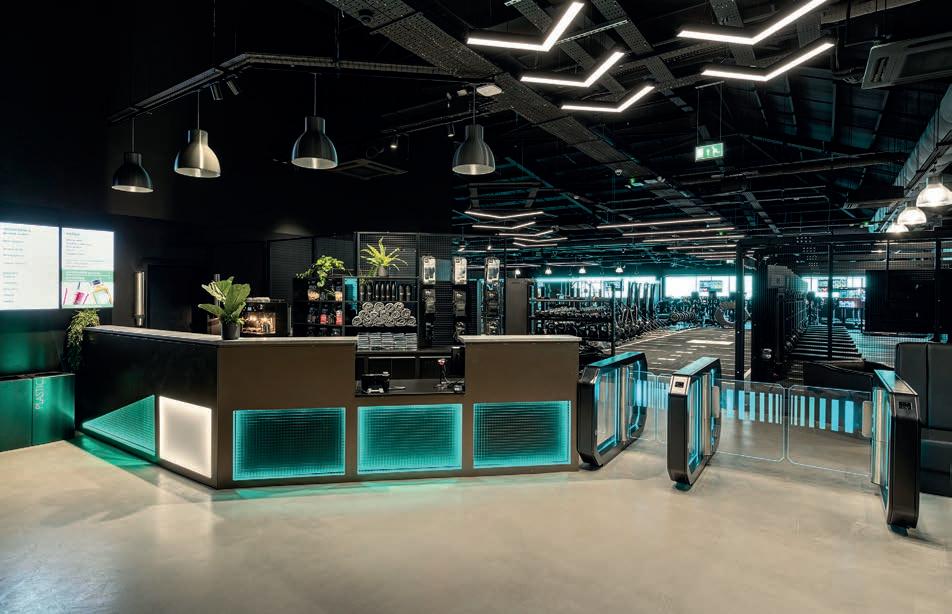
8 minute read
Contract News
from ECN October 2022
SIGNIFY’S LIGHTING SOLUTIONS INSTALLED IN EVERY EVERLAST GYM ACROSS THE UK
Signify has been appointed by Frasers Group to design and supply the lighting for all 69 Everlast Gyms across the UK.
Advertisement
Designing the gyms with LED lighting dramatically cuts energy consumption by about 80% when compared to the traditional technologies that were deployed earlier. Added controls will help manage and reduce energy consumption by creating and managing uniform light schedules for all 69 gyms from a single dashboard, reducing operational costs, ensuring compliance, and efficiently planning maintenance.
Everlast gyms at Denton, Shirebrook and Preston have already been upgraded and offer members a variety of different environments – or ‘innovative zones’ – to train in, creating unique gym experiences. Contemporary luminaries from the Modular range distribute a soft yet functional light that is designed for hospitality venues, public, retail and other large spaces. These lights use minimalist design principles that add to the visual appeal of the space. To compliment this, the Keyline range, from the Philips portfolio, creates chevrons, lines and squares in the ceiling, directing members to the different zones and identifying the individual areas.
As part of the redesign, the Interact connected lighting system provides centralised lighting control for all the gyms. Agreed scenes and schedules ensure a consistent look and feel, as well as providing increased visibility, flexibility, and control of the lights. The cloud-based platform collects data from all light points via a connected lighting infrastructure and is displayed on a centralised dashboard. This enables better comparison, monitoring and management of lighting across multiple locations for improved efficiency
The gyms also feature tailor-made pendant and projector lights, which are 3D printed luminaires designed and developed to suit the exact needs of each individual location.
Signify, signify.com
REDUCING THE FINANCIAL BURDEN OF LIGHT
TRILUX has impressed rauch Möbelwerke, Europe’s largest bedroom furniture manufacturer, with its high quality and energy efficient lighting and tailor-made financing service for its headquarters in Freudenberg, Germany.
As a full-service provider, the lighting expert retrofitted the entire site with innovative LED solutions. In close collaboration with rauch, TRILUX developed a customised financing concept. After the retrofit, the energy costs for lighting will fall by approximately €74,000 per month, and CO2 emissions will reduce by 2,200 tons per year.
Finding the right lighting solution for the five production halls was challenging. These house vast hall aisles in which huge machines, called ‘all-rounders’, perform all the woodworking, such as sawing, milling, drilling, and gluing, creating significant air pollution.
The perfect luminaire for these demanding environments is TRILUX’s E-Line NEXT LED. Lighting technology and protection class of the highly versatile light strip are precisely adapted to any application.
To maximise efficiency and transparency, the continuous rows are networked with TRILUX’s LiveLink Premium lighting management system and combined with sensors for presence and daylight detection. This enables the luminaires to be monitored online via a cloud interface and the TRILUX Monitoring Services.
Creavo LED recessed ceiling luminaires and the Finea LED light channel have been used in the office and administration areas. Looking outside the facility, in the delivery zone, rauch relies on the Jovie LED post-top luminaire. In the covered loading zones, powerful Mirona Fit LED high-bay luminaires provide excellent, energy efficient light and greater safety.
TRILUX, trilux.com
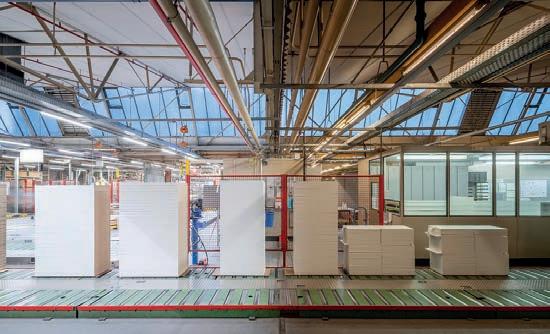
WB POWER DELIVERS COMPLETE SOLUTION FOR THE NHS
Power generation provider,
WB Power Services
(WBPS), has completed a multimillion-pound project for a hospital located in the South West of England.
Working with a third-party building services contractor, WBPS was asked to scope, design, install and commission a critical power solution with the objective of providing valuable back up power for the hospital if a power failure occurred.
The project requirements called on WBPS to devise bespoke strategies to enable the project to complete on time whilst delivering a range of services. The installed solution comprised of incumbent equipment removal, civil works and the installation of two 1650kVA Kohler-SDMO generating sets in an existing plant room. These were installed along with accompanying ancillary equipment such as fuel management solutions, plant room attenuation equipment, exhaust systems and full commissioning/testing.
WBPS Managing Director, Andy Wilmott comments: “There were several pieces of the jigsaw to complete with this huge project, with each element dependent on the success of the other.
“The project team overcame huge challenges with issues around space and access, but by implementing a bespoke solution, which included the removal of the old generators, we were able to meet the exact requirements of this project, delivering a complete solution on time and on budget.”
Andy concludes: “This huge project has literally made the difference between life and death for patients using this hospital. The work that went into this project will secure the power of the whole site using best in class generators and technical expertise from the WBPS team.”
WB Power Services, wbpsltd.co.uk
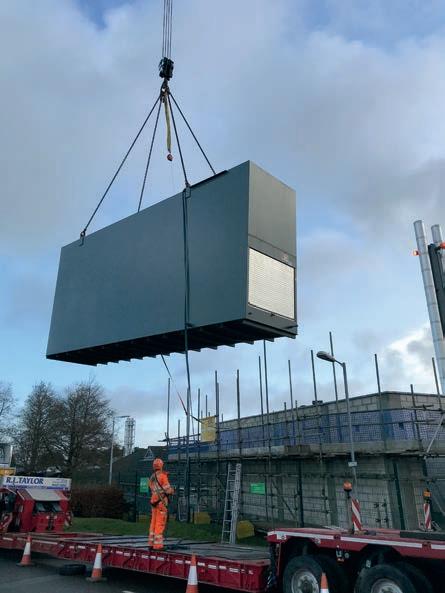
TRANSPORT FOR LONDON BANKS ON ELLIS PATENTS’ CABLE HANGERS
Transport for London (TfL) has installed Ellis Patents’ innovative Pegasus cable hangers in its £500 million Bank Station Capacity Upgrade project.
Specified through the North Yorkshire manufacturer’s UK distributor, ETS Cable Components, the hangers were chosen because their modular design meant they could be manufactured to the project’s very specific requirements.
Noman Shabir, Ellis Patents’ National Sales Manager, says: “TfL wanted hangers that could be supplied to meet a variety of radii because of the changing curvature of the operating tunnels running in and out of Bank Station. In addition, they needed a product that featured pre-drilled holes so that they could accept cable cleats for signal cables.”
“Traditional cable hanging systems wouldn’t have coped with these requirements on the basis that they come in set sizes and configurations. Our thinking when we designed Pegasus was that no two rail projects are ever the same and, as such, project-by-project flexibility was vital.”
Pegasus was designed and developed completely in-house by Ellis Patents. Featuring an aluminium spine that can support any number and configuration of polymer cable hangers, the modular cable hanging system is not only more adaptable than similar products, it’s also stronger and lighter; making it quick and easy to install. Ellis Patents’ Pegasus cable hangers use LUL approved materials, which are suitable for installation underground and within tunnels, as well as UV stabilised materials for installations above ground and trackside.
The Bank Station Capacity Upgrade project is due to be complete and fully operational in the autumn.
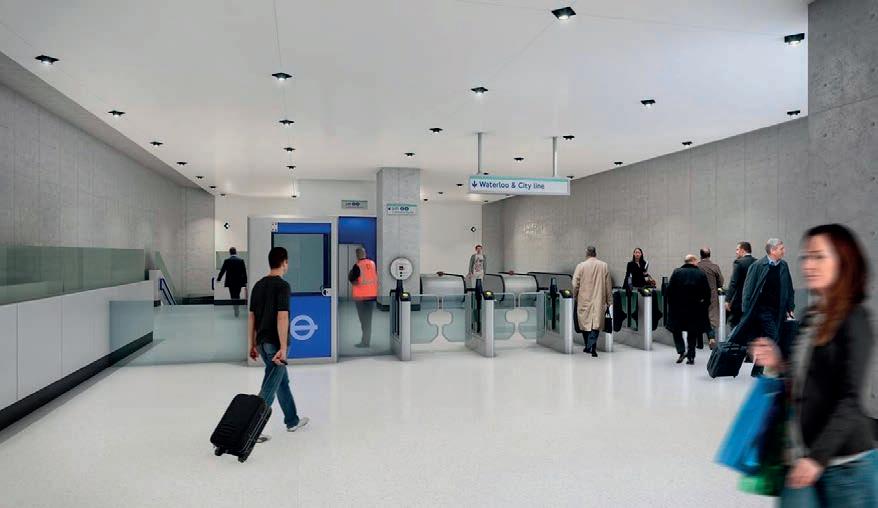
Ellis Patents, ellispatents.co.uk
BUILDING SERVICES FIRM CELEBRATES TOPPING OUT OF LATEST PHASE OF HALLSVILLE QUARTER
Building services and engineering consultant, FHP, has celebrated the completion of a key phase of a £150 million residential development in London with a ‘topping out’ ceremony.
The move sees the end of work on Phase III of the Hallsville Quarter in Canning Town, which is a mixed residential development consisting of 620 units across four blocks and varying in storey heights from nine to 14 floor levels.
Part of a wider £3.7bn urban regeneration programme, the Hallsville Quarter is a new £600m town centre for Canning Town, being created in conjunction with Linkcity, Newham London Borough Council and other project partners.
Completion of Phase III will also deliver a range of new healthcare facilities and provide 378m2 of new offices, over 1,500m2 of leisure and community space, 259 car parking spaces and extra public spaces and landscaped gardens.
FHP has provided a comprehensive range of mechanical, electrical design and plumbing (MEP) 3D Revit services for RIBA Stages 2-6 of the scheme.
Heating and domestic hot water for the building will be provided from the already completed first phase of the development, through an intermediate plate heat exchanger sub-station located in the building’s basement to serve all blocks.
As the project was designed in 3D Revit, FHP was able to provide construction setting out information early in the design and build process with the knowledge that all imbedded services and recessed outlets were in the correct position at the time of the concrete pour.
FHP, fhpp.com
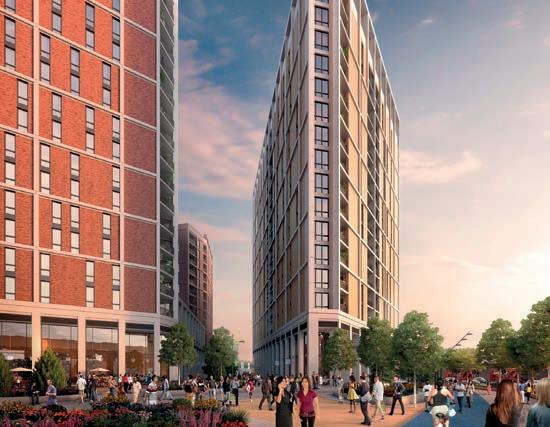
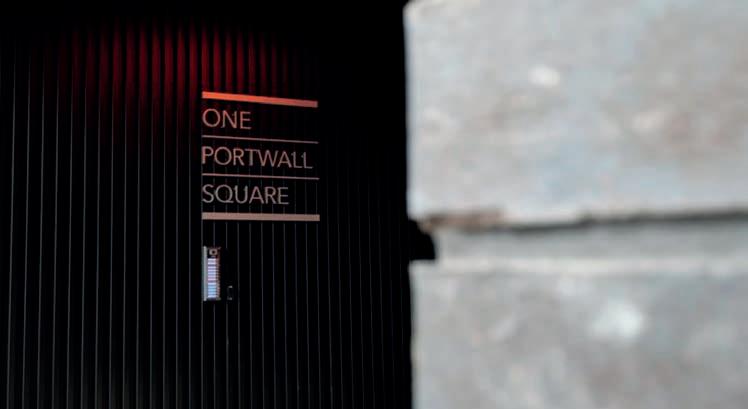
SKANSKA COMPLETES INNOVATIVE BRISTOL OFFICE
Skanska has completed One Portwall Square, a healthy and sustainable new workspace in the heart of Bristol.
The building, which provides more than 33,000ft2 of Category A commercial office space, is located in the heart of Bristol’s prime commercial zone, close to Temple Meads Station. It is being handed over to Nord, ready for the first tenants to move in.
The space is built to a BREEAM Excellent and Energy Performance Certificate A rating, Wired Score Platinum – recognising the building’s excellent digital connectivity.
A range of construction innovations have contributed to its healthy, energy efficient credentials including:
• Concrete core cooling – using chilled water pipes embedded in the concrete slabs to cool internal spaces • A mixed mode ventilation system – intelligently monitoring external conditions to enable use of natural ventilation wherever possible to save energy from mechanical ventilation • A high-performance building fabric and its connection to the Bristol Heat Network also supports reduced energy demands
Charlie Norris, Operations Director at Skanska, says: “Since beginning work on the building in 2020, the workspace landscape has evolved as tenants’ priorities have changed with new working patterns and COVID-19 safety concerns. What I’m most proud of is that the building more than fulfils occupiers’ needs in the post pandemic environment, providing flexible spaces, plus light, airy and intuitive spaces for tenants, while offering carbon-smart building infrastructure that reduces long-term running costs.”