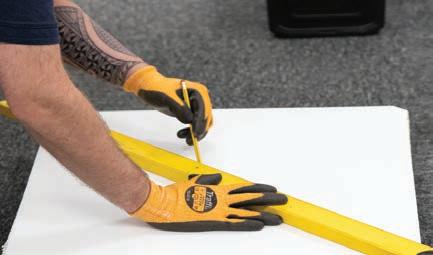
2 minute read
HOW PRE-ASSEMBLED KITS CAN HELP TO ADDRESS INDUSTRY SKILLS SHORTAGES
from ECN April 2023
Few in the industry would dispute the fact that two of the biggest issues facing contractors today are the skills shortage and the pressure to deliver projects for less, without compromising on quality or safety.
A 2022 survey of specialist contractors in the UK highlighted a range of business concerns, with material shortages, a lack of skilled labour, and delays to projects cited as worrying problems. Almost two in every five contractors (39%) named skill shortages as their most pressing business concern.
Advertisement
In addition, research shows that less than a third of contractors consistently finish jobs on time and within budget. In many cases, they lose as much as one full day’s work per week due to setbacks, inefficiencies, and often the need to supervise less experienced site staff and ensure there are no health and safety issues.
In today’s economic climate, this clearly has significant financial repercussions for small businesses and self-employed contractors dealing with the cost-of-living crisis.
Installing cable management systems can be a particularly time-consuming and complex part of any project. Modern MEP suspension systems are quicker to prepare and install than traditional methods, such as threaded rod, channel, nuts, bolts and washers. Using lightweight, pre-fabricated trapeze bracket suspension solutions, such as Fast Trak, means no cutting or hot works are required. By contrast, threaded rod and strut solutions require hot cutting on site, which represents a potential health and safety hazard. It also requires a certain level of ability and experience, or the direction and supervision of less experienced staff.
In addition, suspension systems arrive on-site in kits which comprise pre-cut lengths of wire rope and a fused end fixing to suit the substrate, or as a track-based system compatible with pre-fabricated brackets, making them much easier to install.
Assembly is made quicker and easier with Fast Trak, as the pre-fabricated brackets can be installed in four orientations, with fixing points on every face. The cartridge at the end of each Fast Trak bracket allows contractors to attach and adjust the height of the bracket in 10mm increments easily and tool-free. M4 level markers on the tracks highlight every 50mm increment, so no levelling can be done ‘by eye’ – and there are no nuts to adjust either.
Offsite manufacturing solutions such as this are a major innovation in M&E service installation, creating leaner working methods, with modern systems removing much of the labour-intensive work traditionally undertaken on-site.
It also significantly reduces material use; for example, a length of wire rope weighs less than 1/10th of the equivalent threaded rod needed for the same performance, and is much easier to handle and transport around site.
This delivers important carbon savings, as well as reducing manual handling risks and labour hours through the installation of these systems.
Drastically reduced installation times
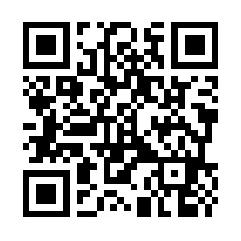
Increasingly, contractors are now recognising the benefits of pre-assembled systems and are routinely specifying them as part of major new build projects.
London Design and Engineering UTC recently invested in a new £10 million campus, with Wates Construction as main contractor. The mixed University Technical College, situated in the London Borough of Newham, wanted to create an inspiring building which embodied its educational ethos.
Due to the strict timescales of the build, Wates Construction needed a proven method of drastically reducing installation times on-site, which would also deliver an aesthetically pleasing finish.
Wates opted to use Gripple’s Fast Trak system, due to the speed and ease of installation.
The total installation time for the project was 349 hours, compared to 1,635 hours for a traditional rod and strut system, while the overall labour cost was reduced by more than 75%. Not only did the use of pre-assembled suspended solutions reduce the labour cost, but it also helped to lower the carbon footprint of the project.
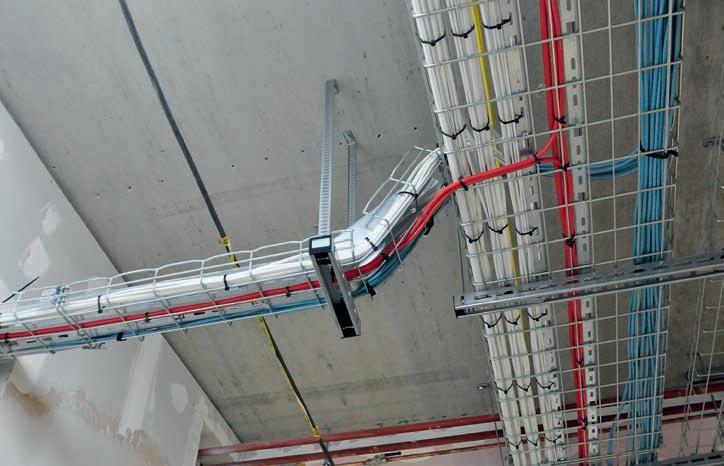
In short, by choosing a pre-fabricated suspension system for suspending MEP services, it can save a great deal of valuable time and money, avoiding lengthy, complex installations and prevent the headaches that can be caused by skills shortages on site.
Gripple, gripple.com