
3 minute read
Good Density Equals Smoothness Bonus
BY SANDY LENDER
Mayo Construction Inc., headquartered in Cavalier, North Dakota, took on a set of three projects that amounted to one large mill-and-pave project for the state Department of Transportation (NDDOT), placing 166,818 tons of HMA from early August to late October 2022. Despite liquid asphalt cement (AC) delivery challenges, the team completed 82 lane miles in 50 days of paving with no corrective grinds required by the owner. They garnered over $350,000 in bonuses. Here’s how they did it.
Plan For Success
After winning projects 23151, 23377 and 23580 along a 37-mile stretch of Highway 52 for NDDOT, Mayo Construction hired Bryce Wuori as the project manager to assist in the completion of the company’s largest construction project in the almost 100 years of operation. Wuori brought a number of tools along, including the PaveScan® RDM 2.0 device from Geophysical Survey Systems
Inc. (GSSI) and his proprietary Pavewise software system. The PaveScan assisted in quality control/quality assurance (QC/QA). Mayo Construction has also been using the Willow notched wedge system over the past construction seasons to achieve joint density on required projects.
Mayo President Trevor Christianson said, “As a company we try to stay on the cutting edge of technology to be as efficient and successful as possible. I truly believe our crews pave some of the best roads in the state and we are proud of this accomplishment.”
As of April 2019, the Pavescan RDM pavement density measurement technology is an accepted American Association of State and Highway Transportation Officials (AASHTO) specification, PP 98-19.
“Trucking logistics issues and taking advantage of the best paving days for the echelon paving and mainline paving were key in the success of the ride and density on this project,” Wuori said.
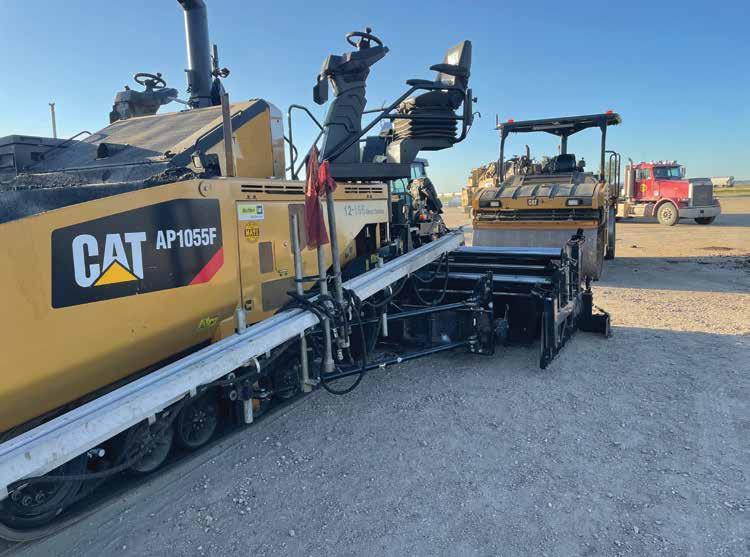
The team had an average of 50 trucks per day from 15 trucking companies on the project. The peak was 70-75 trucks from hired subcontractors and owner/operators. Need- less to say, it took special coordination of all activities, from the full project width milling, to trench milling for the purpose of correcting existing rutting, to 139,438 tons of aggregate base from two pits with two subcontractors for passing lane construction, to echelon paving after trench paving.
“We also planned operations around scheduled rain days. Since this project was over 30 miles long, we were able to work on certain parts of the project even if it was raining on one end and not on the other end. These types of decisions produced in conjunction with data from Pavewise helped us be as efficient as possible with the paving days we had on the project.”
The team also had to be efficient in light of binder delays.
Christianson explained that the asphalt mix—the state’s Superpave FAA 45—was a good design. “The state wanted a virgin asphalt mix design,” he shared, stating it required a PG58H-34 liquid binder.
He praised the plant crew, saying they produced the mix consistently; it gave the field crew no issues with compaction or otherwise. “One of the struggles on the project was consistently getting shipments of AC to the site,” Christianson shared. “Since this [liquid] came from Canada, there were transportation and border crossing restrictions that would fall out of our control on the project.”
Wuori explained, “We did have to shut the project down multiple times because of lack of AC. An extra holding tank was added to the project to keep more AC available.”
Solving that inconvenience, crews received mix at temperatures averaging 315330°F, depending on the weather. “We did start adding an Evotherm in late October,” Wuori said, to take advantage of the additive’s cool-weather paving properties. He explained the state allows operations to continue with lower temperatures when additive is used. “The first asphalt plant location was approximately 16 miles away from the paving operations and the second asphalt plant setup location was 26 miles away from paving operations.”
MILL, FILL, RIDE SMOOTH
“There was approximately 130,693 tons of milling reclaimed on the project,” Christianson said. “Most of the milling was done with a 12-foot mill or a combination of a 12-foot mill and an 8-foot milling machine.”
Three sites accepted excess millings for two local owners. At the peak of production, the crew had five portable scales on site to monitor material.
And as material was taken away and the profiled surface was cleaned and tacked, the paving crew made ready for the finish. The Superpave mix would be placed at a depth of 2 inches compacted, across the width of up to 38 feet, depending on location along