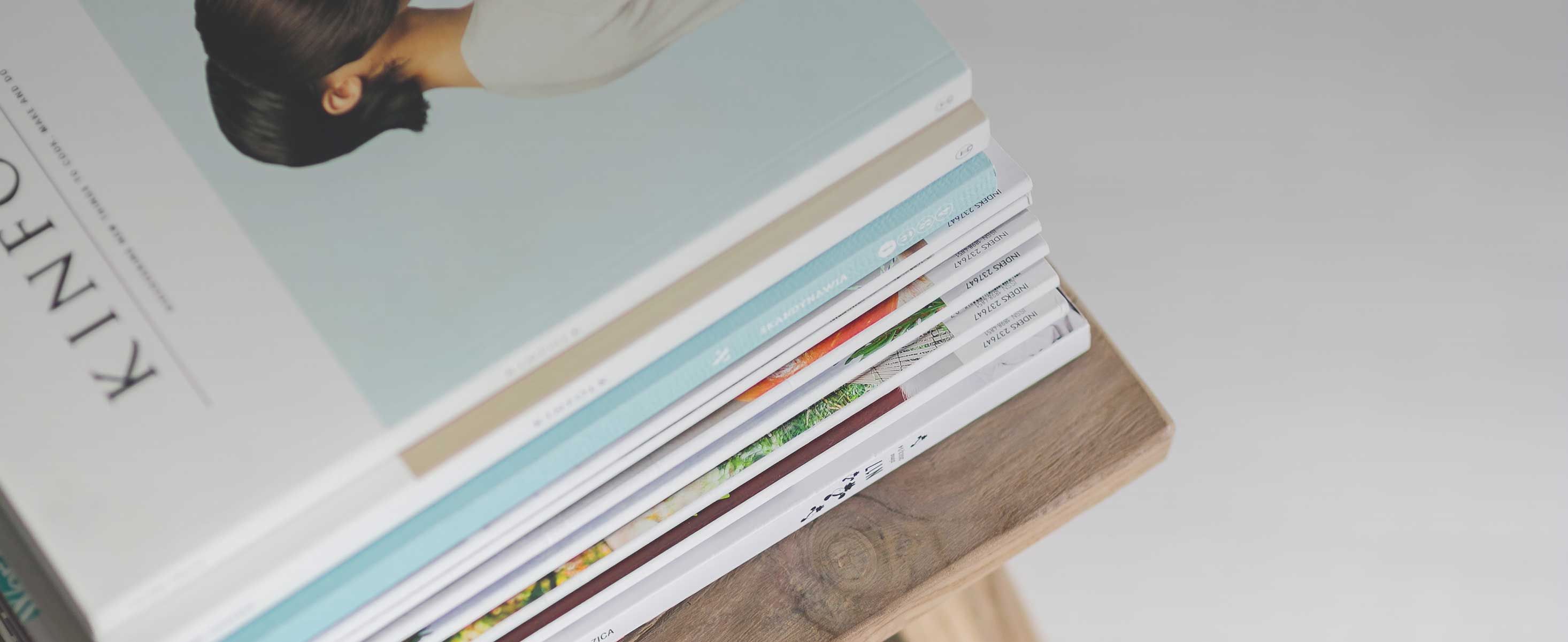
3 minute read
KEEP THEM MOVING

by EndeavorBusinessMedia-VehicleRepairGroup
Improve your shop’s layout to help keep cars flowing through
By NOAH BROWN
IN THE AUTOMOTIVE REPAIR INDUSTRY more so than most, speed and efficiency are key in running a productive shop.
As shops continue to develop and expand, many managers and owners focus their resources investing in state-of-the-art equipment, hiring and training technicians and other sources to improve their overall shop efficiency.
However, Ann Salazar from Avant Garde Interiors, a design firm specializing in space utilization planning for collision repair shops, says the physical layout of a shop can also be a hindrance to a shop’s efficiency if it’s not organized correctly.
“If the physical layout is inhibiting production due to lack of careful consideration of some key factors from the beginning, it’s not just production efficiency that suffers,” Salazar says. “Loss in business capacity adds up over time.”
Having the ability to complete repairs safely and with as little downtime as possible and making sure cars are moving through your shop as efficiently as possible can go a long way in boosting the productivity of your shop.
Keep Moving Forward
The overall layout and flow of a shop is critical in making sure that the repair process goes as smoothly as possible.
Johnny Simpson, co-owner of Simpson Collision Repair in Florence, Alabama, and his family have been in the collision repair business for four generations, going from his grandfather to his daughter. Simpson Collision Repair just opened a new location designed by Salazar and Avant Garde, and he says just a simple rearrangement of some of the shop has made a huge difference in overall efficiency.
“If I need to sell a job, I don’t hesitate to walk them out into the workspace. When a customer sees how clean your shop is and how organized your process is, they love it,” Simpson says. “Cars shouldn’t be just parked wherever.”
Simpson also says he understands that not every shop can afford to make massive renovations and might have to find smaller ways to improve overall workflow. Over everything else, he recommends one thing: Tape.
Having layout lines, direction lines and work areas marked out with layout tape has helped improve the overall workflow of his shop. Every location that a car is going to be is marked off, and if there’s a space that a car is going to drive through, there are no obstructions in the driving path.
“So many shops you see have cars needing to back in and back out,” Simpson says. “You’re always concerned about that car having to go backward. Keeping it moving forward is critical.”
Ripple Effect
Salazar says improving workflow can start with small changes. Oftentimes, she’ll see a shop make a change to address an immediate concern without thinking of the overall shop flow, and that change will cause a ripple effect into nearby workstations.
However, that ripple effect can have a positive impact on your shop if you plan for it correctly. Addressing where vehicles and parts enter the building and how that gels with customer parking can affect where you place vehicles and equipment inside.
Simpson also adds that making sure you have the appropriate equipment can help reduce overcrowded workspaces. Some tools, such as OEM-specific ones required for certification, can’t be negotiated, but Simpson says there are other places where you can downsize.
Everything from switching to a walk-behind floor cleaner instead of a riding model to getting the smallest air compressor that fits your needs can help reduce clutter in your shop.
“You don’t want your shop to be a big box that you shove everything into,” Simpson says. “Make sure your equipment fits your space.”
Though it may not seem like it at first, small changes can add up to quicker turnarounds on repairs, and that means more cars flowing through your shop. Customers may not notice every single detail and change, but Salazar says they are savvy enough to pick up on the overall feeling of a shop when they walk in. Making sure every part of your shop is as clean, organized and efficient as possible makes for an overall better customer experience.
“Good design invokes the impression of a professional operation. When amenities are provided to increase conveniences, it shows detail matters,” Salazar says. “Screening for unpleasant odors, unsightly storage areas, inadequate space for supplies and coats … the retail industry ran studies how all these factors and more could impact sales.”
Simpson says even if his business hadn’t built a brand-new shop from the ground up, making some efficiency changes would have helped the old building quite a bit.
“It helps us to push so many cars through, and you’re not just pulling cars in and out all the time,” he says. “Keeping that car working through the shop until it leaves.”
And though it may seem like a major undertaking depending on how much you want to change in your shop, Salazar says the overall result is well worth the cost.
“Over the past 20 years, I would say it’s a lot more important than most people realize, or I would be out of work by now,” Salazar says. “The obvious difference is the overall customer experience and shorter turn-around.”