
4 minute read
Engineered Films Manufacturing Plants
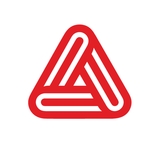
from AD Connect Magazine Q4 2022
by Avery Dennison Materials Group
Avery Dennison film facestocks offer a compelling combination of performance, aesthetics, and sustainability. These products are manufactured at our two Engineered Films Plants (EFP) located in Painesville, and Concord, Ohio. Both sites are just a few miles away from the Label and Packaging Materials headquarters in Mentor, Ohio.
John Kovalchuk, plant manager - principal engineer, has been with EFP for most of its history. The Painesville site opened in 1985, followed by Concord 10 years later. John came on board in 1989, progressing in roles from process manager, to technology manager, and finally to his current position.
“EFP’s origins go back to the early 1980s and a company division called Fasson Specialty Materials,” says John. “A pilot extrusion line was installed at the Fasson’s Painesville plant to make liners, then eventually film facestocks. This business spun off to become EFP, and really grew with the PRIMAX® and FasClear® products.”
EFP by the numbers: 92, 24/7, 4, and 2.3 million
Today, with 92 operators and support staff, EFP runs 24 hours a day, seven days a week. Their four extrusion lines manufacture not only the current version of High Performance PRIMAX® and FasClear®, but products such as Global MDO. These films are used primarily in Health and Personal Care, Food and Beverage, Durables, and other industries.
The plants also have a repellitization line to recycle scrap film. Installed in 2004, the line has helped EFP divert more than 99% of waste from landfill. Much of the scrap is put back into Avery Dennison films, while a portion is sold to recycling vendors. Annually, the repellitization line prevents more than 2.3 million pounds of material from being sent to landfills.
A strong culture built and maintained by a great team
John insists that the growth and success of EFP reflect its people. He stresses especially the importance of some of the team’s longest-tenured people in maintaining the EFP’s culture of engagement and workplace safety. This feeling is shared by the team.
“EFP has definitely changed throughout the years,” says Elizabeth Booth, shift team leader. “When I started in 1994, we were called the Extrusion Business Team, or ‘EBT’ It's hard to believe that was 27 years ago. My coworkers are like a second family. We strive as a team to make our plant stand out in performance. We do this through our MDI meetings and improving our process, whether it is safety, quality or production. I’m very proud of what we have accomplished and look forward to my continued involvement in our future.”
“I joined EFP in 1995, and it’s been through many changes throughout my career,” said Jim LaGanke, operations manager. “It’s matured in the areas of productivity, quality, & standard operating procedures in an effort to deliver consistent products to customers with increasing demands. Safety standards have grown tremendously as well. Expectations to work multiple years without recordable injuries in either plant have been achieved repeatedly through training and ‘watching out’ for the safety of coworkers. It’s a family-oriented culture based on honesty, trust, and teamwork. The plant floor is full of employees that want to make this business unit stronger, and they generate and implement great ideas to make this possible. This is a great place to work!
“Many things have changed since I started at EFP in 1997,” says Bill Marrison, line operator. “I’ve seen machine upgrades, safety improvements, and new faces. But what’s stayed the same is Avery Dennison's commitment to safety and quality. I'm proud to be part of that.”
The Avery Dennison EFP team is proud of the work they do to produce solutions for our customers. To learn more about Avery Dennison film label products, visit label.averydennison.com.