
4 minute read
Lime Plaster - Material Study
Lime Plaster - Material Study
Advertisement
Lime plaster is a mixture of traditional lime, sand and water. It may also contain a reinforcement fibre such as animal hair which can serve to strengthen the material and bind it tightly to the underlying structure.
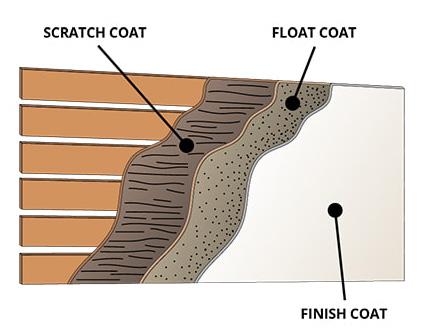
Lime plaster is breathable, It allow moisture to escape and evaporate from the structure and it effectively draws moisture out from the structure due to its capillary properties.
Types of Lime Plaster
There are three types of lime plaster:
Hydraulic Lime Plaster (Water Lime, Hydraulic)
Made with hydraulic lime, this will set in damp conditions and may be required in extremely damp conditions such as cellars where a non-hydraulic lime plaster would not carbonate
sufficiently. Hydraulic lime plaster is less fatty than other lime plasters and may require more effort to apply to laths and ceilings. However, it cures in around 90 days (typically) which means it can be painted with a breathable coating much sooner than other lime plasters.
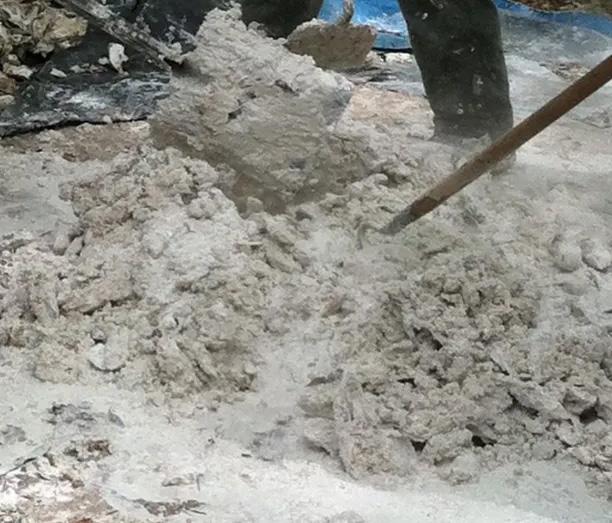
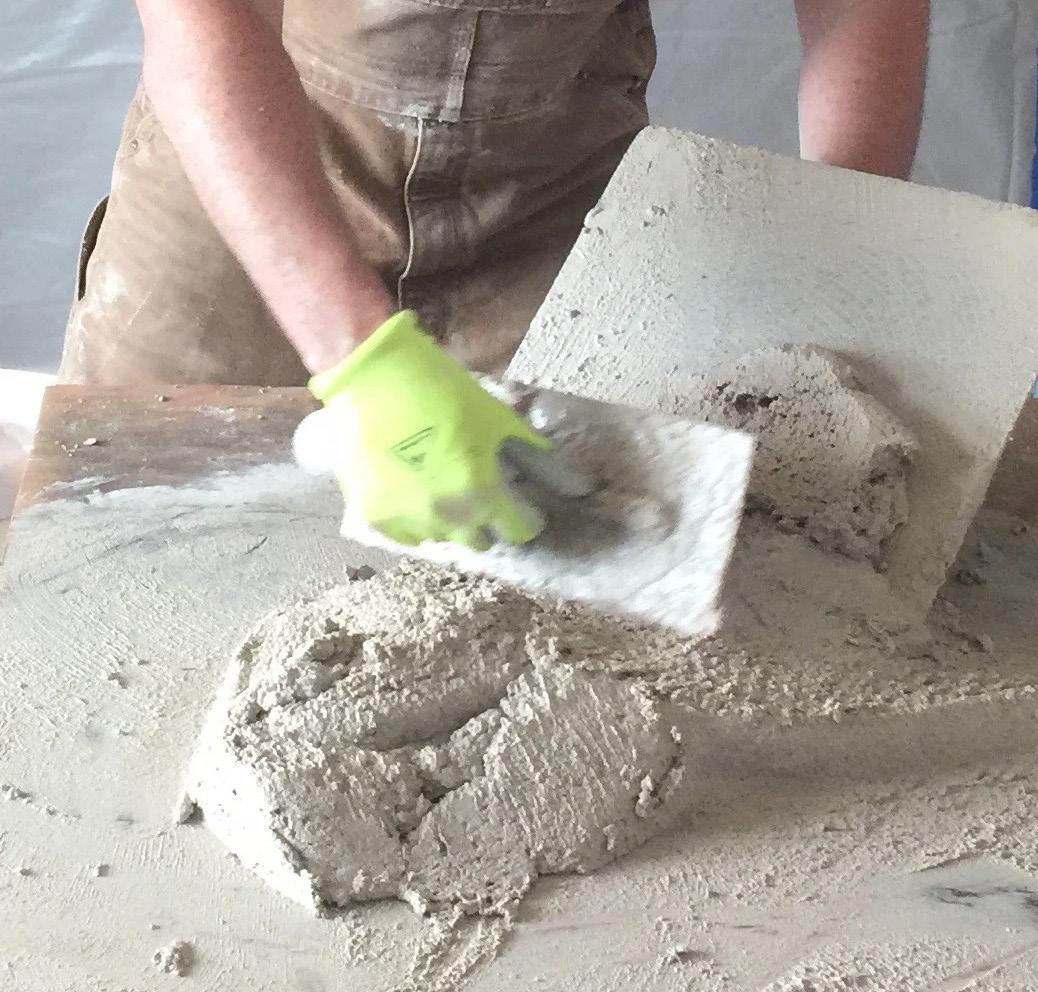
Non-Hydraulic Lime Plaster (Air Lime, Non-Hydraulic)
Made with non-hydraulic lime, commonly known as lime putty. This plaster is extremely soft and flexible, perfect for conservation of delicate masonry. It sets very slowly by carbonation and typically cures in around 12 months. Non-hydraulic lime plaster can stay wet indefinitely in damp conditions where there is no opportunity to carbonate. However, it is quite “fatty” and therefore sticky, it is easier to apply to ceilings and laths.
Lime plasters are always applied and built up in thin layers called coats, the traditional three coat system is the recommended method:
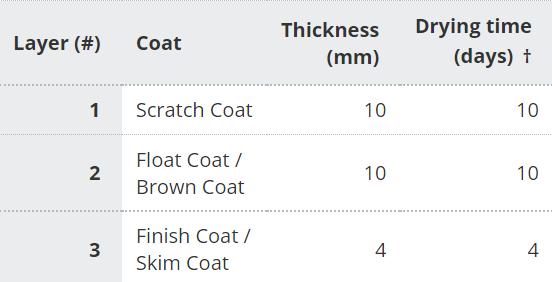
Scratch Coat
The scratch coat is the first coat applied to the substrate, this could be bare masonry or laths. It is made with a coarse aggregate to leave a rough surface, this is then heavily scratched (hence the name scratch coat). The rough scratched finish provides a good key for the following coat to adhere.
Float Coat / Brown Coat
The float coat (also known as brown coat) is applied on top of the scratch coat and is also made with a coarse aggregate. The surface is ruled to a relatively flat finish and is scratched lightly to leave a key for the finish coat.
Finish Coat
The finish coat is the final, visible surface. It’a purpose is decorative and is made with a fine aggregate to produce a smoother, flatter finish.
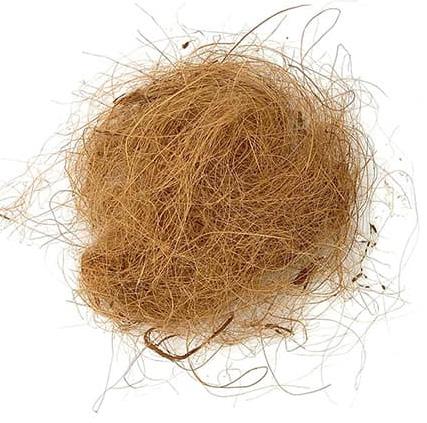

Lath and plaster walls. Lime plaster is typically applied to timber laths which provide a strong key and help to gauge the material keeping it relatively even.
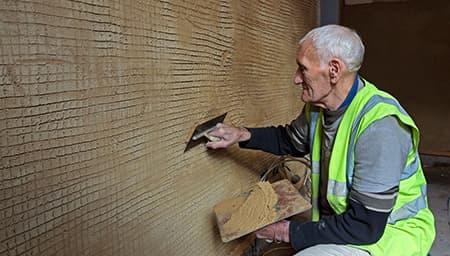
A traditional lime plasterer applies the scratch coat with a steel trowel. The scratches provide a key for the next coat which is applied after the recommended drying time.
Key for first coat
A plaster won’t bond well to smooth or dense surfaces. It may be necessary to provide a suitable key for the first coat - there are several techniques at your disposal.
Raking out
Where masonry is reasonably porous, a sufficient key may be established by raking out joints. At least every other course of brickwork would be raked out. This may not be adequate for larger units of dense masonry.
Key coat
Key coat (also known as a “stipple coat” or “slurry coat”) is a product we sell separately on request.
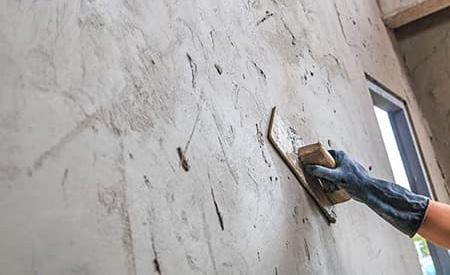
Lime plaster finish coat, finished with a wooden or plastic float to produce a relatively smooth and even finish.