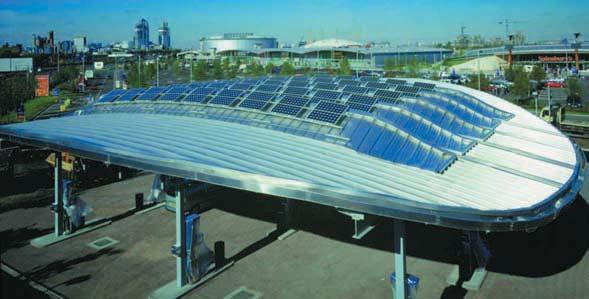
17 minute read
Press Releases
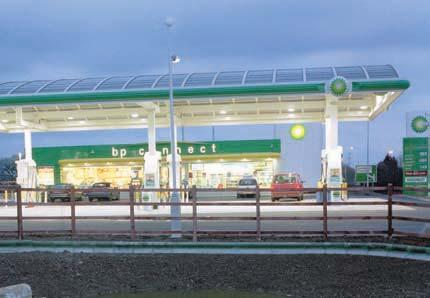
Further examination after the fire revealed that extruded acrylic had been used and as a result national guidance was amended as well as the UK’s building regulations.
Advertisement
It was the late 1980’s that saw a shift in the UK fuel market with the emergence of the supermarket and a move away from town centre retail shopping. This single act was to change the fuel market forever with cut price fuel on offer like nothing before.
The response of the mainstream oil industry was to fight back in recruiting retailers that could heavily promote what each of the oil companies could offer by a more imaginative use of branding and
image by a fresh appeal. The BP “Helios” logo is just one example as the canopy and the pole sign was made to become more of a dominant feature than ever before.
Solar power also made its appearance in the late 1990’s at a
BP site at Bedford using an imaginative way to capture energy from the sun by using photo-voltaic panels clipped together to obtain direct current that can be converted to alternating current by means of a transformer on site. A further development u s i n g alternatives happened in 2005 when wind turbines were introduced onto two canopies by Sainsbury’s and BP respectively.
The issue of canopy ignition occurred again in 2002 when a fire broke out on a canopy at Western Lane, Hammersmith in London when 16 metres of “Bull Nose” fascia ignited and again, molten plastic fell onto the forecourt with potentially disastrous results. The same issue was found where Light Emitting Diodes (LED’s) were used i n s i d e polycarbonate tubing clipped onto the canopy fascia. Rainwater had entered the polycarbonate tubing causing an ignition that spread to extruded acrylic.
Today canopy designs have become more ambitious as evidenced on the cover page of this issue that make an interesting variety that either pleases the eye or becomes an eyesore. Either way let us allow innovation to continue.
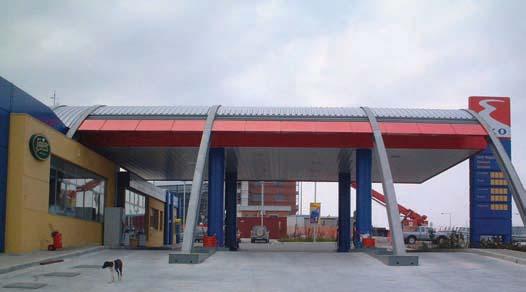
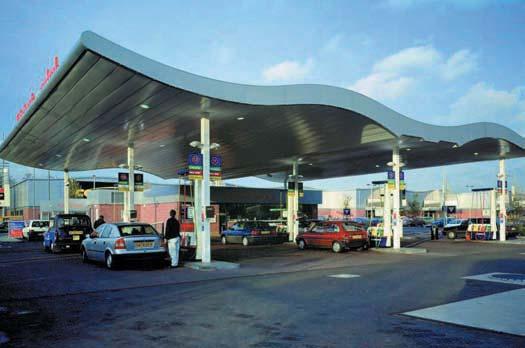
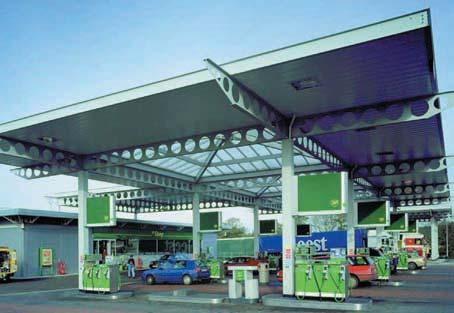
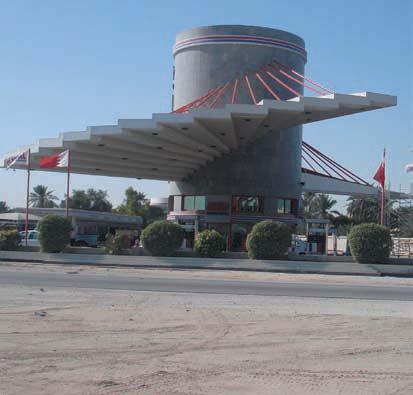

By Patrick Smith, Suffolk Trading Standards
So just what is a typical day for someone working in Trading Standards? I have to tell you that there is no such thing.
For me a day might be spent dealing with food past its “Use By” date or farmers wanting advice on what paperwork they need to move their livestock or “I have trouble with this credit agreement is it legal ?” Or a raid on a house full of dodgy DVDs, iffy characters and bundles of £20 notes. And this is a small proportion of the enforcement that we do. In the nearly 40 years of working here in Suffolk I don’t believe there have been many days that were repeats. Then somebody says they want to sell E85 at their petrol site and can they have permission …… and apparently I’m the expert !!
So, we will select a day out as a Petroleum Officer. This is not an exact day, this is not even a typical day, this is merely one representative of the work that we may cover. These events have happened in Suffolk and continue to happen.
I switch my phone on and immediately receive a call.
“Sorry for the late notice the new tanks are going in today”. ”When?”
“At about 12.00”.
Thinking hard I put together a days work in that direction. I had expected this call of course but not knowing when to plan my work is always disruptive. I need to be at the site when the tanks go in but I need to be able to justify other work in the area. Suffolk is a big county and from my base some sites are a 4 hour round trip. Why cant they give me more notice? After all somebody must have known that this was likely to happen today.
I do find generally there is a failure of those managing the work to keep Petroleum Officers informed. Worse they mess us about by giving wholly spurious dates for work and then fail to tell us that this has changed so we turn up to find that the events have been put back to next Thursday or some such. On the whole PO’s are practical ordinary people and we understand the difficulties faced on a work site. However we would not be human if the level of cooperation did not go down the more we are messed about.
I find generally the bigger the company the worse and the more arrogant they are at talking to you. One company sent me plans recently for a new site in Bury St Edmunds. What they actually provided for me to approve were for another site in Bristol. After 90 minutes looking at the plans and finding several major problems I sent an email back listing the defects only to be told by return that the specifications had changed from the proposals they sent me yesterday.
However I don’t say that just about petrol retailers, I find that across the board of all companies. Give me the bloke or lady who runs their own business over a multinational anytime. Because they are in touch as they personally have something to lose.
In the event I am able to formulate a days work and this is it.
First stop is a full inspection at a site that we have not been to for a while. It is a dealer owned petrol station who sell cars for their main business and fuel as a secondary concern, just to get punters in. The Environment Agency website revealed that they had a river 100 yards away, with water extraction boreholes half a mile down stream. The tanks are single skin steel and about 1990 vintage.
I called them and gave an hours notice that I was to turn up and was greeted by the site manager.
The inspection revealed they were only dipping their tanks once a week if that and they were relying almost entirely on the dead reckoning of the pump readings for their loss adjustment. The accountant had not been happy with the wetstock records they previously kept and had set up a new system. He now was happy that it prevented theft and had gone no further.
Where is the petrol interceptor? No answer. They don’t know. Apparently from the records it has been checked but they don’t know where it is.
Is there a site plan? Yes, but it does not cover the interceptor.
“So can you show me Pete’s (the competent person in control at the moment) training records.
“No.”
“Where are they”
“Some where in the office”.
“Can you find them please”
While they search I wander around the shop. If I were a retailer I would do all I could to prevent somebody from Trading Standards roaming bored around my premises. 5 Minutes later “I’ve got them”
“Thanks, by the way I have found some sandwiches and yoghurt beyond their use-by date and you have lost your tobacco under age notice. Can you show me what checks you make to ensure your food stock rotation works and your tobacco refusals list? Now let me see the training records”.
Further discussions reveal that a DSEAR risk assessment has been made by an independent body 3 years ago. This sits pristine in its envelope it is clear that nobody has actually looked at the results or attended to any of the recommendations.
I count at least 4 major breaches of legislation any one of which could line them up for a court appearance.
I have a choice of what action to take:
•I could issue an Advice Notice requiring the remedial work to be done. This notice has no legal standing and cannot be used to compel any work.
•I could issue a formal
Improvement Notice detailing the work to be done. Failure to comply with this is an offence.
•I could issue a formal Prohibition
Notice. These are used mostly for imminent dangers and require immediate action. Again failure to comply with this constitutes an offence.
For 99% of the work we do we issue the Advice Notice because it is more informal. If however that is not complied with within the time stipulated then other action of a less easygoing nature will be adopted.
They get their Advice Notice. (Two weeks later I receive a letter telling me that they have had a new Risk Assessment done, that they have located the interceptor and that they are to have tank gauges installed. They are now considering having their tanks relined.
I am then off to the rebuild. I introduce myself and sign in. The bright orange tanks are there and the first is just receiving the strapping ready for the lift. I examine the tank for dents & scrapes etc. Ok I wander over and look at the shuttered hole before me. All is as it should be and now for the lift. Its always interesting watching but no doubt very nerve wracking for the crane operator. When the first and second are strapped down the last tank soars into the air and swings across. However this time the lift is not high enough and as the crane swings so the underside of the tank gives a parked dumper truck a hefty scrape. The proceedings stop and the tank is examined. The protective covering is broken up and there is bare metal beneath. Fortunately it is not punctured. I call for the repair kit. Ahh, there is a problem. The kit was on the first lorry which is now on its way back to Lancashire. In situations like these everybody looks at the Petroleum Officer. But I can’t allow a damaged tank to go in so they have to get somebody to drive from the producers down to us with a kit before the work can proceed. However that is going to take some time and the A47 is not the best road. I can tell that I am not the most popular bloke there and I just wonder what would have happened if I had not been on site.
Any way I have an unexpected bit of time so I clear off to somewhere else.
The next visit is to a nearby golf course. They had contacted me a couple of weeks ago because they too had completed a risk assessment and had come to the conclusion that storing petrol for their grass cutters in Jerry cans was sometimes a bit iffy and they were considering the use of an over ground tank. I had purposely delayed my visit knowing the rebuild tank delivery was coming up soon.
At the course I discussed with the Secretary what their plans were and we came to an agreement as to the best siting for a new 1000 litre, double skin, over ground tank for their grass cutters. Security was a problem as the area was all common land. However we settled on keeping it in a very well ventilated remote shed, laid on a concrete pad, in a compound which could be locked at night. Fine.
The next call was to a farm site. 30 Years ago 70% of Petroleum Licenses issued in Suffolk were to farm sites. Now that number is down to only 35% of a much reduced overall total.
Old records seem to suggest that during the second quarter of 1943 there was a massive increase in the installation of petrol tanks in Suffolk. So much so that by 1960 50% of all our sites across the county had been put in during that quarter. Almost all of them at about 2270 litres or 1135 litres capacity. That is 500 & 250 gallons for those of us who don’t speak French.
There are still a few left, mostly with hand pumps, Gilbert & Barker, Tokheim, Beck, Vickers and a few others, put in when the ubiquitous grey Fergy ruled. Tractors now are a different matter entirely and many tanks have been converted to diesel or lost out through leaks.
Farm sites present their own problems.
How can you do wetstock when you don’t have a clue how much has been delivered by the pump.
Dipsticks of wood or rubber or not at all.
“Well I run her dry and then order”
“An assessment? What do you mean by an assessment?”
“Training, well I suppose I know what to do. Mother uses it of course as she has done for 50 years.”
This one is to be disposed of and not before time. I examine the vent pipe. It is thin and soars up to the majestic height of about 6 feet. It ends in a small “T” piece and is held up by the adjacent wall. I notice
that the base where it goes into the ground is rotted away completely and it has been venting to air at an approximate height of 1 inch. However they want to extend the barn and that there tank has to go. I advise on what needs to be done and who they need to do it. “No just digging around the tank and hooking the fill pipe to the John Deere is not an option.” Later when the excavation is completed you can see why this tank lasted. Like other things produced by “Austerity” Britain it is basic, simple and built like the proverbial brick out house. The metal must be half an inch thick. Try asking modern tank builders to come up with steel of those dimensions on such a small tank too. Then off to a revisit at a petrol site that had problems especially with its interceptors. Somebody had found that when the tankers arrived their tyres had damaged the channelling near the off-sets and had the bright idea to fill them in with tarmac. I had left an Advice Note in the usual way but now when I return I am told that the company that owns the site will no longer do remedial work that is not on an Improvement or Prohibition Notice. Fair enough I thought if they want to play hard ball I can do that as well. I could issue an Improvement Notice but I would have to give them 28 days to do the work and that is far too long to allow unintercepted deliveries. I could issue a Prohibition Notice but perhaps not allowing deliveries and thus closing the site down until the work was completed would be too much after all the place is in the middle of nowhere. So in the end I faxed them a Special Licence Condition the following day requiring the site to be closed entirely while the tanker was present until the work had been completed. The work was done before the end of the week. Funny that. Finally back to the rebuild. Some bright spark had employed a bloke on a sports bike to get the kit here and as I arrive it is being applied to the effected area on base of the tank. Eventually that tank is being nicely strapped down and all is well.
APEA tel/fax 0845 603 5507 www.apea.org.uk 47
LPG Leak and Explosion Darwen
By Mark Mellodey Blackburn with Darwen Borough Council
Incident description
The premises involved in the incident is a service station constructed on a green field site in 2002 and commissioned in November of that year. The current licensee took over the running of the site in early 2008.
On 17th August 2008 at 15:44 an explosion occurred in or immediately adjacent to the electrical distribution cupboard in the back office area of the shop building.
The explosion destroyed the electrical cupboard, the VeederRoot tank gauging system and the site alarm system. The wall separating the back office from the shop was blown out along with the fire exit door and the roof. Extensive damage was caused to the office store room and the back office areas. The resulting fire caused additional damage to the building.
The customer assistant working at the time immediately isolated the two firemen’s switches and contacted the emergency services. The fire brigade arrived within 10 minutes and put out the fire using the site’s own CO2 fire extinguishers and then cooled the electrical cupboard with their own equipment.
There were no injuries to staff and no customers were on site at the time of the incident.
Following investigation, it was found that the explosion was caused by the ignition of LPG vapour in the electrical meter cupboard which had entered via a duct that ran under the forecourt and through an area contaminated by LPG. The LPG was present in the ground as a result of a failure of a damaged Brugge LPG supply line running from the tank to the dispenser. The damage had been caused during previous site works at the premises, most probably at the time of installation of the line during the construction of the site. The Petroleum Licensing Authority have no records of any work in this area since this time. There was no history of any LPG leaks on the site prior to the summer of 2008.
Following a number of reports of gas smells on the site, an LPG engineer attended on 30th June, 7th July and 22nd July.
During the first visit, the engineer repaired a small leak on a bypass union but specified other pipe work as leak free. On the second visit, the engineer tested the pipe work in the compound and on the forecourt and found no leak. He did however, report smelling gas on the forecourt near the air and water but as the wind was blowing from an adjacent industrial estate, it was questioned whether this was coming from off site. On the final visit on the 22nd July, on the completed report, the engineer reported that there was no leak found. The same engineer attended on each of these visits.
The investigation by the petrol company identified the pipe as damaged under the landscaped area to the west of the LPG tanks. Certificates for tanks and electrics were available although no such testing was carried out in respect of the underground pipe work. It is not currently standard or common industry practice to carry out routine testing of underground pipe work.
There was also no warning tracer tape installed above the pipe nor was there sand surrounding the pipe as recommended in the installation instructions. Both of these are measures which would have reduced the risk of mechanical damage. An access chamber installed at the time of construction of the site to supply a proposed Driver Controlled Delivery (DCD) box was located within a few meters of the area where the leaking part of the pipe was detected. This duct was not sealed prior to the incident. This chamber connected directly with the electric meter cupboard where the explosion occurred. It is almost certain that this was the path by which the leaked LPG entered the building.
The manual recording method of monitoring stock was not sufficiently sensitive to identify leaks and was intended only to identify stock losses for financial purposes. Using this method, the analysis of the stock could have taken up to 7 weeks.
The engineer visits regarding the LPG smells are reported above. Although generally appropriate responses were made and leak tests carried out on accessible pipe work, no such tests were undertaken on underground pipe work. In terms of reasonable practicability, although it will depend on the circumstances on a case by case basis, it appears that on repeat calls to reports of gas smells, consideration should be given to undertaking purging and testing of the whole system.
Action since the accident
• The premises has been renovated with additional safety monitoring and control systems as follows:
- All ducts have been sealed with RAISE insert Sleeves and FIWA sealing putty.
- A flammable gas detector has been installed in the electric meter cupboard set to alarm from 25 % of the LEL.
- remote compressed air isolation valves installed at either end of the LPG line with the compressor located in the electric meter cupboard. Any fire would burn through the air lines releasing the pressure, closing the valves.