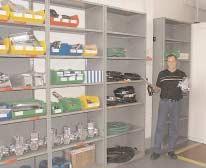
36 minute read
News
line with each customer's specific needs.'
Len Cutugno heads Petrofuse ZP Ltd's operations in the USA and believes the system will be a huge success: 'Petrofuse ZP is the clear leader when it comes to conforming with the specifications in the proposed revision of UL971.'
Advertisement
For further information on Petrofuse ZP please contact: Tim Foster Petrofuse ZP Ltd 4E Sherwood Road Aston Fields Industrial Estate Bromsgrove Worcestershire B60 3DR
T: +44 1527 577866 F: +44 1527 577765 E: timfoster@petrofusezp.com Christian Papenburg T: +49 241 9367 3636 F: +49 241 9367 3637 M: +49 171 4141504 E: christianpapenburg@petrofusezp.com
Len Cutugno T: +1 973 886 9556 F: +1 973 335 6841 E: lencutugno@petrofusezp.com
TQIPS Buys Tanksafe’s installation & contracting Business
TQ IPS the Shoreham-by-Sea based National Forecourt Contractor has purchased the forecourt contracting business of TankSafe Limited. The purchase includes the TankSafe offices at Bromsgrove, the retention of the existing involved TankSafe staff and all plant equipment and vehicles. TankSafe Limited will continue to operate their foaming business..
TQ IPS will operate their Northern based contracting business from the Bromsgrove offices whilst the Southern region office will continue to be located at Shoreham-by-Sea.
According to Richard Quarmby, Commercial Director of TQ IPS, "it's business as usual for TQ IPS based at Bromsgrove and all existing and future customers are assured of continuity of operations".
This addition to the TQ IPS family continues to broaden the range of products and services offered by TQ IPS to the Petroleum Industry ranging from new site construction, complete or partial re-builds, tank refurbishment specialized LPG installations and all the facilities and equipment to support the modern multi-fuel retailing operations of the UK's petroleum retailers, distributors and oil companies.
Recent successes of TQ IPS have been the completion of the unique Tesco Ramsgate forecourt complete with over ground petrol storage and their appointment as the Autoequip UK distributor. The Italian car wash manufacturer has a full range of vehicle washing equipment including commercial vehicle washers which can be customized for specialist vehicles.
All telephone numbers remain unchanged. For further information please contact, either Richard Quarmby of TQIPS on 07966 136903 or Charles Huddleston of TANKSAFE on 07966 292198.
The agreement is part of the Lead Authority Partnership Scheme (LAPS), a principle established by the Health and Safety Executive (HSE) and the Local Authority Enforcement Liaison Committee (HELA).
LAPS is fully supported by the Health and Safety Commission (HSC) and requires Petroleum Licensing Authorities to liase with the relevant Lead Authority prior to significant actions being taken.
The agreement will allow Esso a single point of contact for key health and safety issues and allows Petroleum Licensing Authorities access to information along with the opportunity to
discuss issues raised through out the country.
Representatives from Esso and Surrey County Council Trading Standards have signed an agreement that will promote the consistency of advice on all safety and consumer issues taken at its 750 company owned petrol filling stations throughout the U.K.
Martin Todd, Chief Executive of Esso, and County Trading Standards Officer Peter Denard met at Kingscroft Service Station, Leatherhead to sign the agreement on Thursday 28 August
Peter Denard County Trading Standards Officer said: "I am delighted to be signing on behalf of the service. Surrey takes the responsibility of petroleum enforcement very seriously and this agreement will formalise our partnership approach with Esso and will help to ensure continuity of all matters affecting the regulations of Esso's company owned petrol filling stations.
Martin Todd, Esso Retail Sales Manager UK and Ireland said: "The company has always placed the utmost importance on ensuring that our service stations are operated to consistent and high standards. This one-stop shop with Surrey Trading Standards is most welcome"
Steve Rowe Senior Petroleum Officer for Surrey Trading Standards added:" Esso and Trading Standards have already held one meeting resulting in a better understanding of the company's future proposals and the building of relationships from both parties."
SIRA facilitates compliance with DSEAR regulations
DSEAR is a set of regulations recently introduced to protect people from fires, explosions and similar events arising from dangerous substances used in the workplace. The Dangerous Substances and Explosive Atmospheres Regulations 2002 are enforced by HSE and Local Authorities, Fire Brigades and Petroleum Licensing Authorities. DSEAR is applicable to many industries including chemical manufacture, processing, petrochemical industry offshore and
onshore, handling manufacture and storage of bulk powders, petrol, flammable liquids, mining etc.
These regulations implement the ATEX Worker Protection Directive 1999/92/EC, the Explosive Atmospheres Directive (ATEX 137) and the Chemical Agents Directive 98/24/EC.
To help employers and the selfemployed assess their responsibilities, Sira Test & Certification Ltd has introduced a new brochure, which outlines the requirements of the DSEAR regulations. Risk assessments of workplaces are required under the management of Health & Safety Work Regulations 1999. Existing workplaces must meet the DSEAR requirements by July 2006!
Sira's new introduction to DSEAR provides clear and detailed explanations of all elements of the DSEAR regulations, to clarify companies' responsibilities. Covered in detail are:
- Hazard Appreciation & Risk
Assessment - Area Classification - Inspection of Installed
Equipment - Certification - Training & certification of
Personel - Preparation of Risk Assessment record
A full and detailed paper about DSEAR is available from the Health and Safety Executive www.hse.gov.uk but Sira has produced this simple document to facilitate understanding of DSEAR regulations and how Sira can help.
Sira will offer companies a complete solution to meeting the DSEAR regulations, with the Sira Explosive Atmospheres Management Service (SEAMS). A high level of professionalism and technical support from Sira can ensure clients meet the DSEAR regulations with a high degree of confidence and, if the organization does not require the full SEAMS scheme, a DSEAR Hazardous Area Healthcheck can be undertaken. Sira also offers project management for companies wishing to comply with DSEAR.
For more information or to receive a free copy of the DSEAR brochure please call 01244 670900, email exhazard@siratc.co.uk or visit www.siraservices.com
SIRA introduces hazardous area questionnaire
Sira Test and Certification Ltd has compiled a series of questionnaires which offer companies the chance to test staff on their hazardous area knowledge. Ideal for confined area workforces, process and offshore industries and pharmaceutical and manufacturing plants with potentially explosive atmospheres, Sira has designed the questionnaire to challenge UK businesses about their hazardous area knowledge.
Sira will provide the questionnaire to companies who can then distribute it to relevant sections of their workforce to ensure that their working knowledge of hazardous area procedures is of the required standard. This is particularly important with regard to the imminent deadline for compliance with the ATEX Directive (1st July 2003).
The questionnaire itself is divided into four sections, each intended to be completed by different levels of staff: Process Operators, Management, Instrument and Electrical Technicians, and Instrument and Electrical Designers and Supervisors. The questionnaire is designed to give an indication of the knowledge of both the individual groups and the workforce as a whole. The topics covered include: • Zones • Legislation • Product Markings • The ATEX Directive
Once the questionnaire has been completed it can be returned to Sira who will grade it and collate the results. They can then relay the results to the company and inform them in which areas there is any deficiency of knowledge.
Sira Test and Certification Ltd is accredited to certify to the ATEX Directive, and offer support, training and certification services to companies who are not currently compliant. For more information about the questionnaire or other services provided by Sira Test and Certification Ltd please call +44 (0) 1244 670900 or visit www.siraservices.com
For press information please contact: Kath Darlington/ Debbie Turner/ Liz Ebbrell The Scott Partnership Ltd The Old Barn Holly House Estate CRANAGE Middlewich, Cheshire CW10 9LT United Kingdom Tel: +44 (0) 1606 837787 Fax: +44 (0) 1606 837757 e-mail: pr@scottmail.co.uk
Berry's Announce 'Refresh' of Corporate Image
As part of Berry's on-going commitment to continuously update and improve their services to the Forecourt Industry, they have taken the decision to segregate their business into four integral units, Atlas, Pipework Systems, (in particular featuring Durapipe PetrolLine Xtra), Forecourt Equipment, and a new service, The Pump Spares Depot. This newly established department is
ably run by Jacque Williams. Jacque has a wealth of knowledge available to him, having worked previously as an Area Manager for a leading Pump Manufacturer in his native South Africa, and upon his return to the UK as a Pump Service Engineer.
Jacques practical experience is backed by an updated technical database that allows parts to be easily identified and ordered even if the part numbers are unknown, and with a large range of parts available from hydraulics, hoses, and nozzles through to parts for complete rebuilds, as well as the intention to further expand into commercial pump sales, Berry's are confident that this new service will only be an asset.
This new venture has led them to take a fresh look at their company profile, and they have taken the decision to 're-brand' their corporate image, to reflect the values they consider to be most important; Quality
and Service, combined with the necessity of forward-thinking. The new image was launched earlier this year at the IFFE exhibition, and so far has received very positive feedback.
The company's M.D., Martin Berry commented, " We wanted to create distinct categories within the company, each having their own brand name, to enable customers to identify products and services that are most relevant to them. All of the four brands combine, to provide the best service possible, with everything customers could possibly need available from one source. It also allows us to create distinctive marketing strategies aimed at a specific customer base."
So, with all of these changes now in place, there is a last segment which has recently been put into place - that being a new member to the Berry Team. Alan Fitzpatrick joined the company at the
beginning of August 2003, as Product Sales Manager. Alan will primarily be working for Berry's Sales Director Tom Hocking, and his main role is to liase with contractors and architects, to promote new lines within their Forecourt Products range, as well as highlight the more established products offered by the company.
Anyone who wishes to contact Alan may do so by calling his mobile number, which is: 07717 702817.
Air quality issues associated with motor cars “well on the way to being cracked”
At the fringe event discussion "Pollution free motoring - fantasy or real possibility?" organised by the UK Petroleum Industry Association at the Labour Party Conference, Bournemouth on Tuesday 30th September, UKPIA Chief Executive Malcolm Webb delivered a positive message about removing the main pollutants from motor car exhausts and tackling carbon dioxide (CO2) emissions. "Through a combination of new cleaner fuels and new engine and exhaust clean-up technologies, the main exhaust pollutants from cars were halved in the 1990's and continue to be substantially reduced. We are also at the dawn of sulphur-free fuels, which will become widely available in late 2004. These fuels will facilitate further improvements in engine efficiency and after treatment technologies thus improving the situation still further. So, on Air Quality I think that we are essentially cracking the problem.
Whilst acknowledging that CO2 reduction in vehicles remained a challenge, he emphasised the enormous progress being made with developing more efficient engines and highlighted the substantial gains to be made with currently available hybrid vehicles, which combine petrol or diesel power with electricity generated by the vehicle itself. He expressed confidence that road transport would make its proper contribution to the achievement of the UK's targets for reduction of Greenhouse Gas emissions. "However" he pointed out "emissions from road transport, which have not increased over the last 5 years, account for just 21% of total UK CO2 emissions and so road transport on its own cannot be expected to come any where near to achieving the Government's overall targets for reduction of CO2 emissions"
Mr Webb concluded by stressing the need to continue to make steady progress on improving existing fuel and engine technologies for early uptake in the mass market and the importance of not prematurely picking winners in the technology stakes.
Enquiries to: Nick Vandervell, UKPIA Tel. 020 7240 0289 Mobile 07803 954 090
Minister launches new Energy Institute
Stephen Timms MP, Minister of State for Energy, E-Commerce and Postal Services, joined over 130 invited guests to celebrate the formal launch of the newly created Energy Institute, formed by a merger of the Institute of Petroleum and the Institute of Energy, at a reception in the House of Commons last week.
The reception, co-hosted by the Parliamentary Group for Energy Studies (PGES), brought together leading figures from all sectors of the energy industry, the academic world and government. Speeches were given by PGES Chairman, Paddy Tipping MP, the EI Co-Chairmen, Prof Martin Fry and Dr Pierre Jungels CBE.
Paddy Tipping MP said, "I am delighted to be here today to celebrate the merger of the Institute of Petroleum and the Institute of Energy, two staunch supporters of the PGES. There is no doubt that today's energy system needs a transformation in order to provide for tomorrow's future, but a major concern is that there is not a large enough skilled workforce to deliver what is needed. On behalf of the PGES, we welcome and support the new Energy Institute's work towards ensuring that the development of energy professionals is provided for.
Prof Martin Fry CEng FEI, Co-Chair of the Energy Institute said, "Both the Institute of Petroleum and Institute of Energy had a proud and distinguished heritage developed over many years supporting their particular energy sectors. Increasingly these sectors have converged, creating an integrated global energy market. We recognise the challenges presented in the White Paper and believe that the EI and its members can play an important role in delivering solutions to our future energy needs""
Dr Pierre Jungels CBE CEng FEI, CoChair of the Energy Institute Council said, "We face great energy challenges, nationally and globally - meeting them is fundamental for our future. And with the advent of an integrated global energy sector, the new Energy Institute is needed, not only to mirror developments in our own market, but also to lay the foundations for the foreseeable future. The Energy Institute is a community, a home for energy professionals and an intellectual reservoir for the industry."
For further information please contact Katie Crabb at the Energy Institute on +44 (0) 20 7467 7173 or at kcrabb@energyinst.org.uk
mailto:kcrabb@energyinst.org.uk
APEA2004 Annual Dinner, Conference & Exhibition
By Tony Jenner
Plans are now well under way for the 2004 APEA Annual Dinner, Conference and Exhibition which is scheduled to be held at the ever-popular Metropole Hotel, Birmingham. The date for this event has been set for October 7th 2004 so please make sure you mark this important date in your diary
For this event it has been decided to make the exhibition more modest than in previous years! Those of you who can remember the old days when we used to meet in Dunstable will be familiar with the format, small exhibition stands arranged around the perimeter of the conference hall where attendees can meet suppliers during quiet periods, prior to and between the conference sessions.
The events committee elected for this format because we feel that there are insufficient exhibitors to fill a large exhibition hall. Based on previous experience, we also feel that there are insufficient visitors to warrant a multiday event, so by combining the Annual Dinner, Conference and Exhibition we hope to provide a single focused day for everybody's enjoyment.
Exhibition stand space will be limited to approximately 6 square metres per exhibitor, and invitations will be sent out in the very near future to those companies who have previously supported the APEA. As the number of exhibitors we can accommodate will be limited I recommend reserving space as soon as possible. Obviously, the cost of stand space will be very much reduced from what we have previously charged, therefore, making it a very attractive commercial proposition.
Whilst the conference is in session exhibitors will be required to "shut down" their stands, giving them the opportunity to attend and enjoy the lively and topical conference. Currently members of the events committee are working on a themed approach for the conference, and are in the process of selecting and inviting interesting and informed guest speakers. More details of the conference programme will be contained in future issues of the Bulletin.
The APEA Annual Dinner has become an industry landmark where friends, colleagues, suppliers and their customers get together for a thoroughly enjoyable evening! Last year we attracted almost 400 diners, and judging by the comments I received it was an evening enjoyed by all (even if one table became confused and thought they were at a football match)! We anticipate that this forthcoming event will be equally well subscribed, and as spaces will be limited I recommend booking as soon as possible. Once again, invitations will be sent out to those who have previously supported the association.
We have provisionally reserved 400 hotel rooms at the Metrolpole at a preferential rate. Obviously, to enjoy this discount it will be necessary to confirm bookings directly with the hotel at least 6 weeks prior to the event. When booking, confirm that you are with the APEA and the discount should be automatically applied.
All on the events committee look forward to hosting what promises to be an informative day followed by a fun evening and we look forward to seeing you all in Birmingham next October.
Small fire at petrol filling station - possible cause Thermite reaction
By Roger Marris (Senior Petroleum Inspector - West Yorkshire Fire Service)
On 30 June 2003 the West Yorkshire Fire Service were belatedly notified by the licensee of a small fire involving spilt petrol that occurred on the forecourt of a petrol filling station at Halifax on the evening of 28 June 2003.
According to the licensee, a customer moved his vehicle while the delivery hose nozzle was still in the fuel tank aperture. The safety-break coupling separated and there was a small release of petrol, which immediately ignited and burned briefly.
The forecourt controller stopped all the pumps through the pump controller (but did not operate the emergency stop button) and then went onto the forecourt to see what had happened. After satisfying himself that the fire was out, he coned-off the affected area and apparently reopened the site without contacting the Fire Service or his manager.
On receipt of the late notification, a Petroleum Inspector visited the site to investigate the incident and examine the dispenser hose and fittings. The inner plastic components of the aluminium coupling showed clear signs of charring and there was a sooty deposit on the upper half of the metal coupling, with some melting and slight deformation of the rubber protective sleeve. During the course of his investigation he also noted that coated steel bands protected the edge of the pump island. The coating was damaged in several places, and the exposed steel was rusty. As there was no indication that the source of ignition was a naked light, electrical spark or the petrol driven motor vehicle, the Inspector came to the conclusion that the aluminium nozzle assembly (which fell from a height of approximately 1 metre from the moving vehicle) could have struck a rusty section of the exposed steel band thereby generating a thermite spark which ignited the vapour from the spilt petrol.
The Petroleum Inspector has since written to the licensee to inform him of his conclusions as to the most likely ignition source and also to request that remedial work be carried out remove or cover any rusty or exposed steel on the pump island.
This is not the first occasion that the source of ignition for a fire at a petrol filling station has been attributed to thermite reaction. PETEL circulars1 65/39 65/39a and 65/39b detail a fire investigation and a subsequent research project into this phenomenon. However, up until this incident, it had been perceived that the risk of ignition by thermite reaction (at petrol filling stations) would be associated with the road tanker delivery process where there is a likelihood of aluminium hose couplings impacting with rusty steel. 1 Petrol Filling Stations - Road Tanker Deliveries - Ignition of Petrol by Thermite Reaction. (www.hse.gov.uk/lau/lacs )
This HELA/LACORS PETEL was issued in August 2003 and gives advice to Petroleum Licensing Authorities regarding petrol forecourt activities
Introduction
1. The guidance given in this circular supersedes and updates the guidance given in the HSE letter dated 22 May 19851, paragraphs 121 - 128 of HS(G) 412, the PETEL circulars 65/63 and 65/154 and clauses 9.6.1 and 9.6.2 of the Blue Book5 on the safety control measures to be implemented on petrol station forecourts when dispensing activities take place. It should be noted that the guidance given in this PETEL makes four significant changes to the recommendations given in the above documents insofar as:
- The pre-authorisation of dispensers for attended selfservice operation is now acceptable in certain circumstances and with additional controls (see para 30); - The 50 litre delivery limit for unattended self-service operation is increased to 75 litres (see para 33); - There is no further need to fit an interlock isolation switch to the door of the emergency cabinet at unattended self-service sites (see para 34); - The use of mobile telephones is permitted in the shop, customer's vehicles and in other non-hazardous areas of the petrol filling station (see para 11).
Background
2. The dispensing arrangements can operate in a variety of ways; from attended service, where site staff refuel customers' vehicles through to sites that are unmanned and where customers refuel their own vehicles without any onsite supervision or assistance from the site operator. Some filling stations now function on an alternating system where the site is operated as attended selfservice at busy periods (i.e. day time and evening) and as unattended selfservice during quiet periods when throughput is low (i.e. late evening and through the night).
3. The decision as to the mode of forecourt operation is one for the site operator to take on a commercial basis but after taking safety concerns into account. The latter must be based on a site-specific risk assessment.
4. The recent increase in the number of sites operating in part or as a whole in an unattended self-service mode has highlighted the anomalies that exist in current guidance between the control measures advocated for attended self-service and those for unattended self-service. Although this PETEL Circular attempts to address these anomalies, it should be borne in mind that some sites do operate without any direct supervision and this method of customer service still creates some differences when compared with the forecourt control measures for attended service operations. Such differences that do exist should not be used as reasons to lower accepted standards for attended operations.
General Dispensing Activities
5. Petrol should be dispensed only by means of dispensing equipment of an appropriate standard into the fuel tanks of internal combustion engines (i.e. on vehicles, motorbikes, boats, planes, mowers etc.) or into appropriately marked or labelled portable containers suitable for keeping petrol. The definition of a suitable container includes demountable fuel tanks and fuel retrievers as well as those containers defined by the Petroleum-Spirit (Motor Vehicle) Regs 1929 and the Petroleum-Spirit (Plastic Container) Regs 1982.
6. As far as is reasonably practicable, persons under the age of 16 years should be denied access to petrol.
7. Engines of vehicles should be switched-off before dispensing starts. Dispensing equipment should be operated in accordance with the manufacturer's instructions (e.g. equipment designed to be operated by an attendant should be operated only by an attendant). Delivery hoses should not be kinked or stretched. After dispensing, nozzles should be firmly stowed in their housings to switch off metering pumps and dispensers or, in the case of centralised pump systems, to isolate hoses from sources of pressure. If appropriate, hoses should be draped to avoid damage by moving vehicles. 8. Where portable containers are to be filled, only suitable metal or plastic containers should be used. They should be removed from inside vehicles and be placed on the forecourt and filled with the nozzle-operating lever held open manually. Containers should be securely closed as soon as dispensing finishes. Pedestrian customers should be discouraged from bringing full containers into the shop when paying for petrol.
9. If any equipment develops a fault or if spills, leaks or other emergencies occur during dispensing, those operations should be stopped and the nozzles returned to their housings. The electrical supply should be isolated from faulty equipment. Dispensing should not be restarted until any faults affecting safety have been corrected or any incidents have been dealt with.
10. Irrespective of the mode of operation, forecourt attendants should not be under the age of 16 years and no one under the age of 18 years should be left in sole charge of a filling station.
Mobile Telephones
11. Generally mobile telephones are not designed and certified for use in explosive atmospheres. Their use can also create a serious distraction for people carrying out dispensing activities. Radio transmissions from individual mobile telephones are generally too low to induce dangerous electric currents in nearby equipment and the risk of incendive sparking from the battery is low, however, they should not be used in the hazardous areas that exist when actually dispensing petrol. Neither should they be used in the hazardous areas around the fill and vent pipes during petrol deliveries.
12. Rather than applying a total prohibition on the use of mobile telephones on petrol forecourts which has resulted in some anomalies and frequent abuse to staff, the following controls are recommended:
- Mobile telephones should not be used by customers or forecourt staff whilst actually dispensing petrol into fuel tanks or containers; - During petrol deliveries mobile
telephones should not be used on those parts of the site that have been designated as hazardous areas by the site operator or the driver; - Mobile telephones should not be used during other petrol handling operations or during the maintenance of petrol equipment unless a specific assessment shows the risks are negligible; - There is no need to restrict the use of mobile telephones, with respect to the safe keeping of petrol, at other times or in other areas of the forecourt. This includes in the shop, in motor vehicles parked on the forecourt or in other non-hazardous areas.
13. The use of radio equipment fitted on emergency vehicles and citizen band (CB) radios may create an ignition risk. These types of transmitting equipment do have a power out-put sufficient to induce dangerous electrical currents in nearby fixtures and they should not be allowed to be used at the dispensing points or in the vicinity of the road tanker when unloading. It should be noted that the radio equipment mounted on most emergency vehicles is under automatic interrogation from the base station. This means that radio messages are being received and transmitted without anyone speaking into a hand set. The Home Office has issued the emergency services with separate advice on the use of radios and CB equipment in the vicinity of filling stations.
Management of the Forecourt
14. Whether the site adopts pre or post authorisation of the dispensers the site operator will need to ensure that proper supervision of the forecourt is achieved particularly during busy times or when the site is taking delivery of petrol or other provisions. In carrying out his assessment of the ability of staff to supervise the dispensing operations he will need to consider:
- Appropriate staffing levels - Other duties expected of staff (ie. re-stocking shelves, sales, petrol deliveries) during times the forecourt is open for business. - Management of forecourt staff - Training of forecourt staff (see para. 16)
15. Where the forecourt layout gives rise to poor visibility of dispensers, additional methods of work will need to be introduced for the forecourt staff. It may be necessary to delay authorisation (or to cancel the preauthorisation) of a specific pump until a temporary obstruction to vision has moved away or instructions may be given over the public address system for the customer to move to an alternative pump. When portable containers to be filled are out of the attendant's line of vision it may also be necessary to use the public address system to ask the customer to show the container, prior to filling, so that it can be identified as being suitable.
Training of Forecourt Attendants
16. It is a requirement of the Dangerous Substances and Explosive Atmospheres Regulations 2002 and the Management of Health and Safety Regulations 1999 to provide adequate training and relevant information for all employees involved in the storage and handling of any dangerous substances. It will, therefore, be necessary to identify the training and retraining needs of forecourt staff by an assessment of the risks relating to fire and explosion. Further general information can be found in Approved Codes of Practice6 to these Regulations.
17. Training in matters relating to the dispensing operation should include:
- Procedures for activating and controlling dispensers; - Safe dispensing procedures; - Use of customer information systems, e.g. public address systems; - Safe filling of petrol containers; - Dealing with customers' enquiries on safety matters; - Spillage control and emergency procedures during dispensing including the practical use of the types of fire extinguishers provided; - Recognising the circumstances when it is not safe to authorise a dispenser and when preauthorisation should be overridden; and - Understanding customer behaviour and unacceptable customer practices.
18. It is the responsibility of site management to instruct forecourt attendants not to authorise (or to override the pre-authorisation of) a pump when a situation of poor visibility arises.
Attended Service Operation
operate the dispensing equipment. The attendant should not allow customers to operate the equipment with or without supervision.
20. Trigger latching mechanisms are acceptable on petrol pump nozzles operated by an attendant. However, site operators should be aware that latched nozzles have been implicated in a number of forecourt fires. Static charge is able to build up on users if they let go of the earthed nozzle during dispensing and this can subsequently cause an incendive discharge when they make contact with the nozzle again to complete the transaction. Where trigger-latching mechanisms are installed the site operator should ensure that attendants are provided with, and wear, appropriate anti-static footwear whilst carrying out dispensing operations.
Attended Self-service Operation (ASS)
21. At these sites control over the dispensing is exercised by one or more attendants located at a control point or points. The location and design of the control point should allow, as far as is reasonably practicable, the attendants a clear and unrestricted view of all the dispensers so that they can prevent unsafe practices and if necessary switch-off the dispenser, if for instance:
- inappropriate containers are being filled with petrol, or containers are not placed on the forecourt when being filled with petrol (static discharge hazard); - sources of ignition are present (i.e. smoking, vehicle engine still running, radio transmitting equipment operating); - inappropriate use of the dispenser (i.e. devices being used to hold open the trigger mechanism on the nozzle, the hose being overstretched/damaged due to the vehicle position; and - children (under 16) operating the dispenser or attempting to obtain petrol
Note: Latching mechanisms on nozzles should be removed or disarmed.
22. In practice the attendant will not always be able to observe all details of self-service operations even at welldesigned sites. Observation of the nozzle actually being placed into the vehicle fuel tank or container will frequently be restricted because of the configurations of vehicles, dispensers
and customers relative to the control point. The attendant often needs to make judgements of the customer's intentions based on what can be observed from the control point. What it is reasonable to observe from the control point will vary from site to site, from dispenser to dispenser, and from situation to situation and will not always include a complete view of various nozzle positions.
23. Knowledge that a customer is being observed directly from the control point is likely to ensure customer adherence to commonly accepted practices and instructions.
Other Aids
24. Mirrors may provide some improvement in vision at specific dispensers. Generally, however, their use will be restricted because the small and distorted image will not provide sufficient detail if installed with a total viewing distance (i.e. from control point to dispenser via a mirror) greater than about 10 metres. The effectiveness of a mirror to improve supervision can only be determined by practical trials at specific locations.
25. Supervision of the dispensing operation is likely to be improved as a result of a direct attendant service or by the presence of staff on the forecourt. Use of Closed Circuit Television Equipment (CCTV)
26. CCTV has limited use as a supervisory aid at most filling stations and should not be seen as an ideal way of observing dispensing activities because of the large number of screens and cameras needed to provide full coverage under all circumstances. Also human factors will result in the lack of reference to the screen at most typical or busy sites. Generally the screens of CCTV systems do not provide sufficient definition to determine, without prolonged study, whether ignition sources are present, whether a container is suitable or whether a user is over 16 years of age.
27. CCTV may, however, have applications in the following circumstances when alternative solutions have been explored and found not to be practicable:
- When the dispenser cannot be viewed directly from the control point. For example, a building, car wash or a large stanchion obstructs the view; - Large multi-hose dispensers are installed so that their long side is at right angles to the line of vision from the control point; or - Following change of use from attendant to self-service operation where the pumps are not easily seen from the control point.
28. CCTV should not normally be required at new sites that are designed in accordance with accepted good practice to maximise visibility of the dispensers. Accepted good practice as detailed in paragraphs 4.4.7 and 4.4.9 of the Blue Book5 includes:
Locating the control point and the dispensers at an attended self-service filling station so that an attendant at the control point can see the forecourt and dispensers clearly when no vehicles are present. Arranging the dispensers so that they are in line with the attendant's line of vision rather than at right angles to it will allow a better observation of both sides of the pumps, and will minimise obstructions caused by the pumps themselves. A road tanker or any other delivery vehicle properly positioned for unloading should not obscure the view from the control point.
29. At existing sites or those undergoing refurbishment or modernisation CCTV may be a reasonably practicable solution at specific pumps where the situations listed in paragraph 27 arise. CCTV should not be installed as a matter of course for all pumps.
Pre-authorisation of dispensers
30. In certain circumstances dispensers may be pre-authorised (i.e. removing the need for the attendant to authorise the dispensers for each transaction). The decision to operate the site with the dispensers preauthorised, should only be taken after a risk assessment has been carried out and it can be demonstrated that the monitoring exercised by the forecourt staff will maintain the same level of vigilance as would be the case if the dispensers had to be authorised for each transaction. The attendants will still need to be vigilant to the customers' actions at the commencement of and during the dispensing activity. In order to restrict children from access to petrol and minimise misuse pre-authorised dispensers should only be activated by a credit/debit card payment facility.
31. Other additional control measures for pre-authorisation of dispensers include: set to prevent the continuous operation for more than 3 minutes and a continuous outflow of more than 75 litres - Removal of any latching mechanisms fitted to nozzles; - Readily accessible and conspicuous emergency pumps isolation switch. This may be of the 'push button' design or, if provided, interlocked with the door of an emergency cabinet.
More detailed guidance on emergency isolation switches is given in clause 14.6.4 of the Blue Book5;
Unattended Self-service Operation (USS) Risk Assessment
32. The decision to operate a site on an USS basis for the whole or part of the business hours must be preceded by a risk assessment. The risk assessment should be carried out on a site-specific basis and should be undertaken in two phases:
- Phase 1 should be an assessment of the risks of damage to the dispensing and safety equipment and the intimidation of customers by the actions of vandals and other persons of an unruly nature.
Sites where vandalism has occurred or is likely to occur (if it is open for business without any supervision) should only be considered suitable for USS where effective control measures can be employed to deter damage to equipment and intimidation to customers.
- Phase 2 should comprise a more detailed assessment that covers the following points:
a. The site's location to determine if any incidents arising during dispensing can be contained within the curtilage of the site.
b. The number and the position of the dispensers. The number of dispensers should not normally exceed two allowing up to four vehicles to be refuelled simultaneously (but see para. 32c).
c. Identifying any additional measures to those listed in paragraphs 33 to 40 for sites where more than two pumps are required or where the throughput of fuels is high during the period of time that the site is in USS operation. Such sites will need special
consideration to ensure that the control measures are adequate and the larger numbers of customers that will visit the site do not compromise safety.
d. The range and location of equipment/facilities to deal with foreseeable emergency incidents.
e. Proposed 'management' and 'engineered' control measures including those built into the installed equipment.
f. Road tanker deliveries, but only in respect of deliveries that may take place when the site is in USS operation.
Engineered Control Measures
33. Typically engineered control measures for unattended sites include:
- Limiting devices on each pump set to prevent the continuous operation for more than 3 minutes and a continuous outflow of more than 75 litres (or the equivalent monetary amount); - Restricting the sale of petrol to credit/debit card transactions only in order to limit access to children and minimise misuse; - Removal of any latching mechanisms fitted to nozzles; - Adequate illumination of the dispensing area and the position(s) of the emergency equipment.
Emergency equipment
34. Emergency equipment for unattended self-service sites will include the following items: -
- Petrol pumps isolation switch. This may be of the 'push button' design or interlocked with the door of the emergency cabinet. More detailed guidance on emergency isolation switches is given in clause 14.6.4 of the Blue Book5. See note below; - A means for communicating quickly and directly with site personnel and the emergency services. An adjacent notice should display the site's name and address and emergency telephone number; - Notice displaying the actions to be taken in case of emergency; - An appropriate number of dry powder fire extinguishers and a container of dry sand or other absorbent material to deal with small spillages. See note below. - At sites which alternate between ASS and USS, there should be no need to install an additional petrol pump isolation switch if the existing external isolation switch is conspicuously marked in accordance with clause 14.6.4 of the Blue Book, is of the push button type and in a position that is clearly visible from the dispensing position(s) of the USS pumps.
- When a site is in AS or ASS operation there should always be staff available that are trained in the use of extinguishers, therefore, the number of extinguishers provided should be in accordance with clause 4.3 of the Blue Guide4. The same will not apply when a site is in USS operation and the likelihood that at the time of fire there is a customer or passer-by being on hand who is trained in how to use an extinguisher is remote. For this reason, there should normally be no need to make available more than 2 x 4.5kg dry powder extinguishers when a site is in USS operation.
35. The location of the above equipment should be conspicuous so that it can be seen from the dispensing areas. It should also be at a safe distance from the potentially wetted areas should any spillages or leakages occur when the dispensers are in use.
36. If the equipment is located in a cabinet, the enclosure should be clearly marked to indicate the equipment it contains. Alternatively, the door could be fully glazed so that the customers can see the equipment. The method of securing the door to cabinet should not impede immediate access in the case of an emergency.
37. Consideration should be given to providing an additional telephone (to the one installed for emergency use) for customers to seek non-emergency advice or to notify the site operator of any instances of equipment not working properly etc.
Management Control Measures
38. Management Control Measures for unattended self-service sites would, typically, include: -
- The site operator or a trained member of staff being on-call whenever the site is open for USS operation; - An emergency procedure for responding to incidents and assisting customers (See paragraphs 39 and 40); - A procedure for carrying out inspections whenever the site is open for USS operation. At sites alternating between ASS and USS operation, this procedure should be carried out at the changeover time; - Procedures for checking, testing and maintaining emergency equipment.
39. The extent of management controls will need careful consideration to ensure that any emergency incidents are effectively and quickly dealt with. The provision of remote CCTV monitoring with direct two-way communication with the forecourt will provide an immediate response to advise a person in difficulties and can make an initial assessment of the severity of the incident. However, such a system of remote supervision will not dispense with the need for a trained member of staff to attend the site, within a pre-determined time period, if an emergency occurs.
40. Incidences of sudden coupling and hose failures are a foreseeable event that can result in the customer becoming splashed/sprayed with petrol. The consequences of such an incident occurring when a site is in USS operation has to be addressed in the risk assessment so that effective control measures, to mitigate against serious personal injury, can be put in place.
References
1 Petroleum (Consolidation) Act 1928 : Safety Standards at Petrol Filling Stations - HSDB3/146/1984
2 HS(G)41 Petrol Filling Stations : Construction and Operation.
3 PETEL 65/6 Supervision at Petrol Filling Stations.
4 PETEL 65/15 Control Measures for Unattended Self Service Petrol Filling Stations.
5 Guidance for the Design, Construction, Modification and Maintenance of Petrol Filling Stations. IP/APEA ISBN 0-85293-217-0
6 Management of health and safety at work. HSE L21 ISBN 0-7176-2488-9