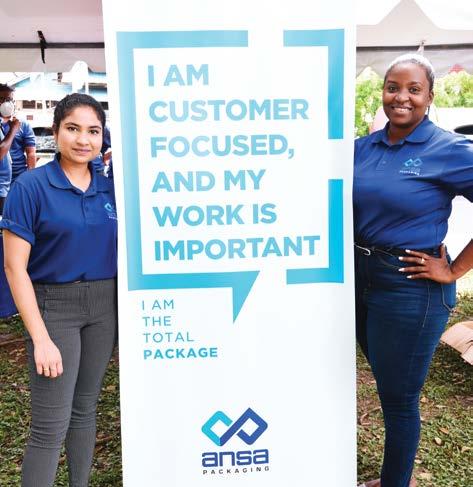
2 minute read
WASTE REDUCTION
THERE ARE ALSO VARIOUS PROCESSES ALREADY IN PLACE OR IN THE IMPLEMENTATION PHASE, THAT FOCUS ON REDUCING MATERIALS IN THE BUSINESS PROCESSES:
Reduction Of Raw Materials
ANSA Polymer of ANSA Packaging made some notable progress in Materials Reduction in 2022:
• Switch to solvent free lamination. This more environmentally friendly approach will reduce the use of solvents by 500kg per year for the lamination process.
• Between 2021 and 2022, a project was undertaken to review the designs of products to make them lighter in weight without compromising quality. 40 bottle designs were successfully reviewed and updated for manufacturing with less raw materials. This is an ongoing process to achieve design weight and optimal quality.
Efficient Use Of Raw Materials
By design, ANSA Packaging’s plastic production processes at ANSA Polymer involve the use of flash (excess material produced with each product) which is ground and used in the production of new products to maximise on the use of the raw materials.
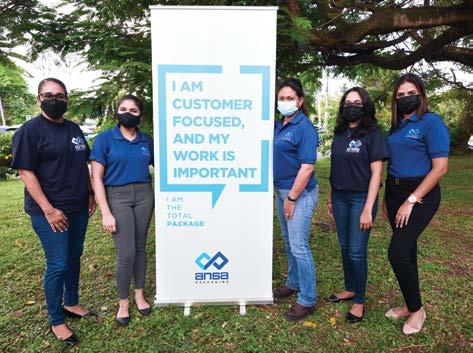
THE VOLUME OF FLASH MATERIAL USED TO MANUFACTURE NEW PRODUCTS IS 29% ON AVERAGE.
This is except for one of the products; the construction bucket, which is produced from 100% regrind from a mix of products and is known for its strength.
Similarly, the manufacturing of Bestcrete cement blocks in the Construction Sector involves the grinding of any broken blocks, or blocks that do not meet the quality standard for reuse as raw materials in the manufacturing of new blocks.
Waste Reduction
THERE ARE ALSO VARIOUS PROCESSES ALREADY IN PLACE OR IN THE IMPLEMENTATION PHASE, THAT FOCUS ON REDUCING MATERIALS IN THE BUSINESS PROCESSES:
Paperless Systems
The upgraded Group Human Resource Information System (HRIS) and Payroll System, will move many paper-based processes to an electronic system, saving paper used for HR approval processes for more than 5,859 employees. This transformational project will facilitate the automation of manual processes, leading to greater efficiencies and empowerment of employees and managers.
ANSA Packaging introduced a paperless reporting system in 2022 for the plastic bottle blow moulding production. All departments, Film and Moulding will soon become paperless.

ANSA McAL Chemicals Limited also reduced paper usage in 2022 by moving some HSE services online including: the Safety Orientation, Covid-19 Screening forms, and site inspection forms.
In the Construction and Manufacturing sectors, the Behavioral-Based Safety Observation programme was converted to an electronic system to reduce this source of paper use. Through this programme employees are required to actively observe and report on their observations to continuously improve site safety and safety culture. There are only a few locations in the manufacturing and construction plants that require the use of paper cards based on safety requirements that do not allow the use of electronics.
The Construction sector’s programme W.O.W.S (We Only Work Safe) was tested at Caribbean Clay Processing Services Limited in 2021 and then rolled out to the rest of the sector locally and regionally in 2022. ANSA McAL Chemicals Limited (Manufacturing Sector) also implemented a paperless system for internal submissions for the Behavioral-Based Safety Observation programme in 2022. Similarly, the Beverage Sector has a UC-UB Reporting System for reporting Unsafe conditions and Unsafe Behaviours on site. This system is also paperless and has been in place for all the breweries since 2019 and more recently in Guyana.
NEW TECHNOLOGY, FEWER RAW MATERIALS, LESS WASTE
In Grenada, CARIB Brewery installed a more sustainable beer filtration system. This membrane filtration system reduces the materials required for filtration by moving away from a Diatomaceous Earth (D.E.) coated stainless steel plate system. As much as 1,500kg of filter aid were used on average per month. The new filtration system eliminates the need for D.E., hence less materials required for the process and less solid waste output. An added benefit of this system is the enhanced beer quality for consumers. This same system will also be installed at the Trinidad Brewery, further enhancing the Group’s sustainable production of beer.