
3 minute read
A clean audit
The new National Standards for Cleanliness require NHS trusts and healthcare settings to comply with defined criteria of a 50-point check. The standards specify in detail how healthcare facilities should be cleaned, and a score is given for each area based on meeting these criteria.
It’s up to you, however, to understand the underlying reasons for your scores – whether good or bad. For example, old or damaged equipment – not necessarily medical equipment but even a staff microwave – can harm your score. Relevant data insights will help you to identify cause and effect.
A fully connected system enables healthcare FMs to view data regularly for continued trust in their operations rather than as compliance at the point of audit. Data and a digital transformation system will help FMs to identify recurring issues and provide insight on how best to solve them. For example: ● Plaster falling from operating theatre walls when hospital beds are wheeled in and out? A digital solution enables you to log the location and a photograph of each defect as and when they are seen for faster remedial work before it gets to an audit. ● Streaky floors? The data can show whether it’s a localised problem, how often mopheads are changed, and how much product cleaners add to their water.
Don’t shoot the cleaners
Cleaning failures aren’t necessarily the cleaners’ responsibility. Other departments affect hygiene standards. Cleaning and waste management are intrinsically linked. The standards acknowledge this and emphasise training on clear delineation of responsibilities for infection prevention and control.
Another example is risk of ‘transference’ – when cleaning solutions become contaminated during use and need to be replaced to prevent the transfer of microorganisms between surfaces. Complying with this audit requirement involves not just the act of cleaning but management of supplies and understanding of assets.
The best digital solutions help you to uncover root causes of audit failure by creating feedback loops and visualising data in dashboard reports.
HEALTHCARE AUDIT
A digital transformation solution can help healthcare FMs to meet the demands of the new 50-point cleanliness audit, says Dan Teare
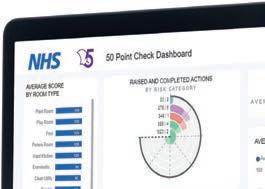
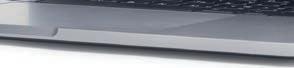
Five recurring issues a digital solution will remedy
1Spillage: If a hospital room has a tag, someone can scan the tag, generate an area-specific task including a photo and comment, allocate it to the right person, who then completes the follow-up action and takes a photo for proof of remedial work. Data is accessible and comparable, so if spillage is a regular occurrence you can alter cleaning regimes or provide new training for staff.
2Staff microwave: The new audits check cleanliness of the staffroom too. If the microwave is broken, for instance, you can check its maintenance history to see if you should fix it or replace it. If it is regularly dirty, you can change cleaning schedules or issue a notice to everyone to take better care when using it.
3Bathrooms: A digital solution integrates with the IoT and works with different sensors so a toilet door sensor can provide data on how many people use the bathroom and when. With rules in place on this data, you can move to dynamic cleaning, automatically scheduling cleaning jobs for the mostused areas. Insights also enable you to change cleaning schedules for busy periods and
DAN TEARE is healthcare and facilities sector director at mpro5, a digital transformations soft ware solution provider
provide adaptive scheduling in response to real-time events.
4HVAC systems: With temperature sensors and door sensors, a hospital can effectively regulate temperature. If a radiator is broken, for example, other radiators can make up for it and someone is alerted to it and can assign the repair as a task to complete.
5Stock/asset management: Add a QR code or barcode to a piece of equipment so its location can be tracked when it is moved. A digital solution also means you can check its maintenance record to see when it was last fixed and by whom. If that person did a bad job or the item is getting repaired too often, you can provide new training regimes or replace faulty equipment.