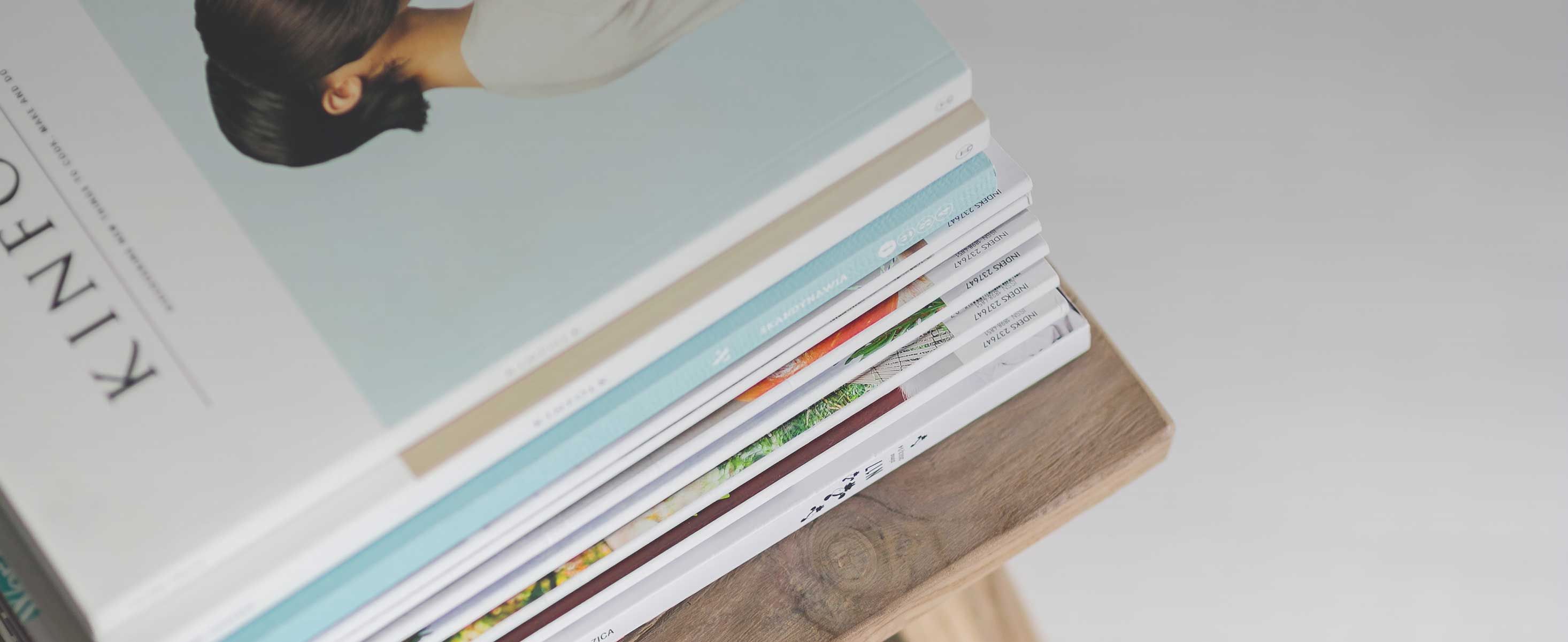
3 minute read
Precision meets miniature
from AMT AUG/SEP 2023
by AMTIL
How a watch-making business started a precision machining company.
Back in 2011, independent watch repair in Australia was coming to an end. Swiss brands restricted the supply of spare parts to Australian watchmakers. Essentially, they thought that Australians should not be trusted to fix their watches. Nicholas Hacko Watchmakers decided they would show the Swiss market that they could make their own watch.
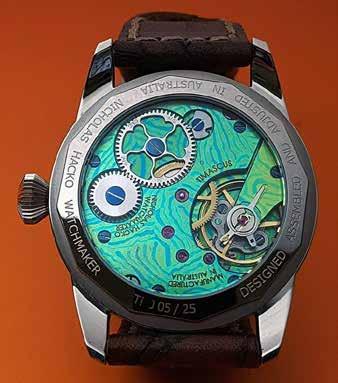
In 2016, they set out to be the first company in Australia to claim that a wristwatch is "Manufactured in Australia". Easier said than done. Working from scratch to build a workshop from the ground up was a difficult but rewarding challenge. With no background in machining and being about 14,000kms from the watchmaking centre of the world, Nicholas Hacko Watchmakers began their journey. To this day, they are the first company in Australia to serially produce a watch from start to finish. Through their expertise in watchmaking and strong determination, they successfully established NH Micro. NH Micro is a machine shop focused on ultra-precision manufacturing. Officially launched in 2021, they created their business based on industry need for contract manufacturing. They are producing parts with high levels of complexity and high precision requirements (below 0.5 µm!). Their heritage and experience in watchmaking has resulted in high value for customers, particularly for those who require the machining of intricate parts.
Josh Hacko (Technical Director) will tackle any industry if the parts fit one or more of these areas: small, tight tolerances and complex. Some of the main industries they service are the medical industry, optomechanical parts and even parts for space!
Josh defines micromachining as, “either feature or part size. You can have large parts with micro-machined features, or you can have some extremely small parts. Once features/parts get below 1mm in any dimension you would start to consider them micro-machined.”
Josh's expertise is in feature sizes smaller than half a millimetre! The smallest part they have made is a flow restriction device: a 0.5mm cube with four holes that are drilled into it at 0.2mm in diameter. When working at that level, you need to consider the precision required.
"The classic attribute of micromachining is high precision,” Josh states. “As the parts get smaller the same tolerances that you'd have on for example a huge dump truck axle change. As soon as you shrink that part down and you shrink those tolerances down, they track to smaller and smaller levels. So, you know ¬± 50-micron tolerance on an axle for a dump truck might scale down to ¬± 5-micron tolerance in something that's about a millimetre small."
High-quality tooling is worth the investment as every link in this precision chain is incredibly critical to get the final result.
NS Tool has gained popularity in the micro-machining industry with a series of cutting tools designed specifically for micro-machining applications. They focus on sub Ø 6mm endmills and offer an impressive selection of high-quality endmills ranging in size from Ø 6mm down to 10 microns!
What Josh finds the most important with NS Tool is that they "produce tools that are not only of incredibly high quality, [but] the reliability of the tool in terms of knowing exactly what you're going to get from the package is imperative. I don't think we could make the parts that we make with the stability and quality we make them without the consistency and reliability of NS Tool.
When you buy 1 0.5-millimetre endmill and you buy one in six months, or you buy like 50 of them and they're all the same. Every single one is the same and the quality is the same. And so that combination of extremely high quality and extremely high reliability amongst the tooling is just essential."
Even the slightest change in one of the endmills will affect everything at that scale.
Josh's top 2 tips in business are: nhmicro.com nicholashacko.com.au livetools.com.au/pages/ns-tool
• Tip #1 is don't get into debt. Or at least if you can avoid debt, avoid it. If that comes with the sacrifice of, you know, slower, more stable growth, so be it. You'll have a better night's sleep.
• Tip #2 is people are everything. Your staff are the most important asset that you have and hiring your first person is always a big challenge, but you shouldn't regret it.
Josh's goal is to grow a team of young people who are passionate about what they do and to give Australians the opportunity to excel in an area that is not currently available to them.
"Precision engineering is very geographically locked. If you want to do those things, you must be in the hubs of the world and there are places all over the world that offer that but there's nothing in Australia that resembles horological precision engineering and being able to offer that to young people is a big goal for us."
Nicholas Hacko Watchmakers embarked on an incredible journey to showcase Australia's ability to manufacture wristwatches independently. Through their expertise in watchmaking and strong determination, they successfully established NH Micro. Australian manufacturing is critical so that companies like NH Micro can keep producing amazing work. We are committed to helping the Australian manufacturing industry by providing high-quality tooling and support.