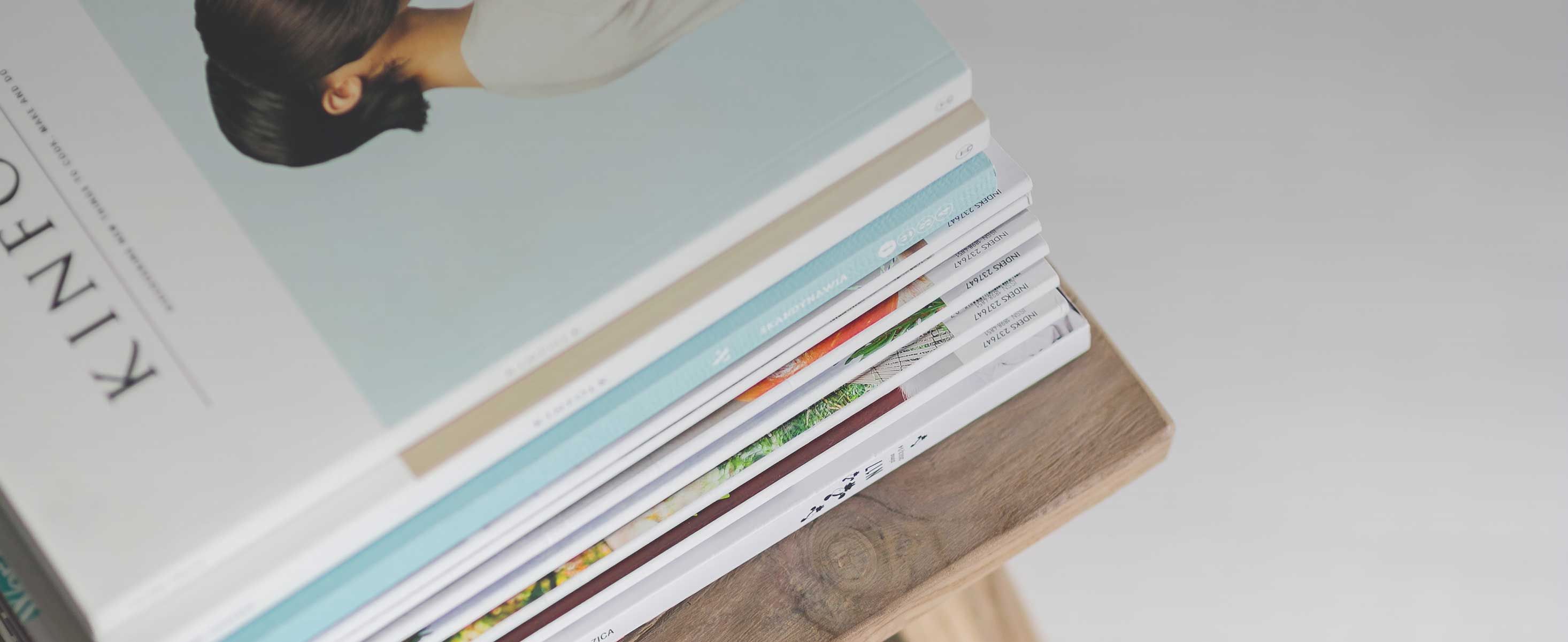
3 minute read
Safely crushing
from AMT AUG/SEP 2023
by AMTIL
Bolted on to safety, quality, and speed – the success formula driving regional crusher service specialist.
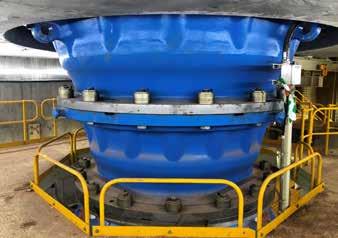
A crusher service specialist headquartered in regional NSW is expanding its interstate success by maintaining these vital heavy machines in exceptionally short time frames while achieving the top safety, quality, reliability, and standards required by mining, quarry, and material handling industry leaders.
Specialised Crusher Services Pty Ltd (SCS), headquartered in Orange, has built its reputation over more than ten years by being scrupulous about safety and compliance while achieving minimised downtime and maximised cost-efficiencies for leaders in the mining, quarrying and materials handling sector in NSW, South Australia and Queensland.
Outstanding bolting practices are core to SCS’s extensive range of technical services and product support, which include installations, commissioning, preventative maintenance, corrective maintenance, breakdown work, shutdowns, upgrades, inspections, technical servicing, and diagnostic fault finding.
“A very big part of our work centres on bolting. Whether we are installing a new machine weighing 100-500 tons – or getting an existing one back into profitable production – safety, quality, and speed are of the essence,” said SCS Managing Director, Peter White.
“Outstanding bolting practice is an essential component of our reputation building, including both the technology we employ, and how we apply it with a rigorous culture of safety, on-site, off-site and 24/7.”
“SCS employs Technofast EziTite hydraulic nuts instead of torque tensioning over our huge range of tasks to get the results we need for outstanding safety and speed, while ensuring that we promote an incident and injury-free culture for our clients and staff.”
Safety is the industry’s number one priority – and it is even better when we can also use this safest technology to boost quality and joint reliability while cutting the time taken to do individual fastening jobs from 15-20 minutes, in some instances, to just one minute.
“Safety, quality and speed work hand-in-hand when you are dealing with crushers that involve scores of different bolt fastening jobs, all of which are vital to production, and many of which require identical tensioning of multiple bolts at the same time to ensure the safest and most secure service life.”
“Technofast hydraulic nuts remove any hazards associated with using conventional radial torque tooling. Large diameter bolts may require torque input ranging between 10,000-20,000Nm, and wrenches therefore have considerable stored energy when in use. That’s a lot to deal with if something goes wrong,” says Peter White.
“Changing out just one really big super-sized nut can take two hours using old methods, which is such hard work, while EziTites can get the job done in minutes.”
“Plus, some large diameter nuts – for example for 160mm diameter threads – can be very difficult to remove and install to specification in some complex crusher applications. We have tried multi-stud jackbolt types. But it is just hard work to handle up to 24 jacking screws at 500Nm.”
“Repetitious manual handling is eliminated during installations and removal with EziTite technology, because no large hydraulic torque tooling is required.”
“We find that safety is enhanced by the hydraulic nuts’ simple operation and speed of removal, which means also that bolt assemblies can tensioned or released in a fraction of the time a conventional nut and bolt can be.”
“The quality of joint is higher, because bolt assemblies are tensioned with direct-pull elongation, which delivers a more accurate final tension, compared with radial torque.”
“Exactly accurate tensioning, with repeatable results to OEM standards, is important to job quality. This precision can be verified with ultrasonic testing to measure bolt elongation, giving further quality and standards comparability and job measurement traceability. The EziTites give a great result every time.”
“Leaders in metalliferous mining and in quarrying are super vigilant about quality, compliance, and safety – which is our focus that earns us the respect of the market,” says White, whose company most typically uses M64mm and M72mm EziTites on major connections. The nuts are typically applied to mainframe connection flanges where multiple large diameter bolts secure flange connections. Smaller M36 types have been used on large structural connections that are disassembled on a routine basis, such as feed chute assemblies. EziTite hydraulic nuts can be tensioned individually to the precise OEM standards required to meet the bolting needs of particular jobs.
“The EziTites are very reliable – operated within their design specification, they provide 100 per cent reliability and accuracy. We have sets that have been delivering trouble-free service for 10 years.
They are very low-maintenance – although regular servicing and lubrication as a preventative measure extends the longevity of the asset even further. And they are easy to overhaul, when this may be eventually required, with excellent parts availability.” technofast.com specialisedcrusherservices.com.au
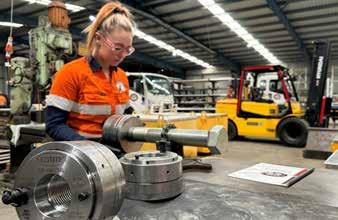