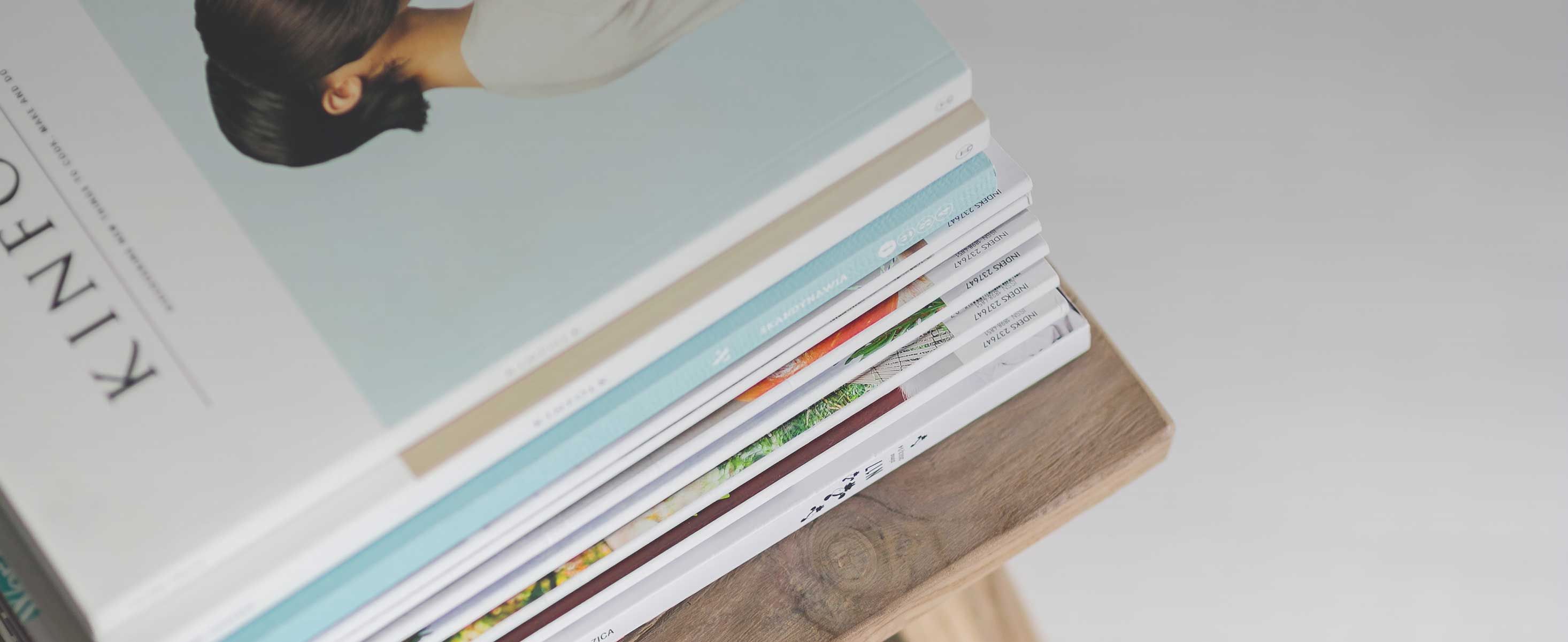
5 minute read
SCARLET-a
from AMT AUG/SEP 2023
by AMTIL
welding: robots that work collaboratively alongside human welders in a collaborative environment.
Collaborative robot welding - the welder’s mate and what we call the “Weld Mate 355” - is ideal for low-value, repetitive welding tasks, and keeps your weld team focused on higher-skilled and complex work. The cobot welders work side-by-side in collaboration with human welders, and are ideal for short-run, high-mix welding applications, allowing your operations to overcome skilled labour shortages by enhancing your existing welding capabilities. Cobot welding bridges the gap between skilled human welding and industrial robot welding, is easy to program, fast to deploy, and significantly boosts your welding productivity, quality, and consistency. diverseco.com
SmartSat Cooperative Research Centre (SmartSat), Australia’s leading space research centre, has launched a $7m project to develop new autonomous spacecraft using AI.
The three-year project, Spacecraft Autonomy and Onboard AI for Next Generation Space Systems, known as SCARLET-a, will bring together eight SmartSat partners: Airbus, Asension, Deakin University, Defence Science and Technology Group, Leonardo Australia, Saab Australia, Swinburne University of Technology, and University of South Australia (UniSA) in a collaborative research effort. SCARLET-a aims to create a set of autonomous algorithms that will enable small and distributed spacecraft to make decisions independently, optimise the use of available resources and capabilities, adapt to changing conditions, and handle critical situations, without intervention from Earth.
SmartSat CRC and partners commit $7m to develop AI-enabled spacecraft that can operate autonomously. communications and earth observation will be achieved using integrated systems of satellite constellations operating autonomously and performing multiple tasks in real time. Such AI-enabled technologies promise to transform the major sectors of our economy, such as agriculture, farming, and mining, and better serve our defence and national security objectives. This investment is possible through the great support of the Federal Government CRC Program Australia and will help develop cuttingedge technologies in space autonomy.”
The project will focus on high impact areas of spacecraft autonomy and onboard AI as identified and prioritised with the industry and defence partners, including:
• Onboard processing and actionable intelligence
• Small spacecraft and constellation resilience
• Dynamic optimisation of constellation resources
• Real-time tasking and resource allocation
SmartSat CEO Professor Andy Koronios (pictured), says that to date, onboard processing has been limited to data collection, but researchers hope the algorithms they develop will allow spacecraft to perform many tasks with less intervention from human operators.
“As autonomous technologies advance and are embraced, their place in space will expand and present new opportunities for applications here on Earth. The next generation of satellite
“With next-generation space systems on the horizon, the possibilities for science, discovery and innovation are endless. SmartSat is well placed to progress Australia’s spacecraft autonomy capabilities to help our nation remain innovative and at the forefront of technology.”
SCARLET-a is the flagship of a suite of projects SmartSat will deliver under its SCARLET lab (laboratory), a SmartSat initiative to develop innovative technologies across spacecraft autonomy, onboard Artificial Intelligence (AI) and data analytics. The lab provides a collaborative platform to bring together researchers and industry to advance autonomy and produce tangible outcomes for Defence and Civil pursuits, enabling Australia’s next space missions. smartsatrc.com
Industry 4.0, are we there yet?
Nathan Gower, Director ANZ at Boomi says even after a decade of talks, we’ve not yet reached the next manufacturing revolution, despite the technology being available.

If there were a formal agreement, the ‘fourth industrial revolution’ – Industry 4.0 – would be defined as the nexus of advanced production techniques and digital technologies, integrated to create a connected facility leveraging data to drive intelligent manufacturing. But the agreement wouldn’t have a start date.
Industry 4.0 is a term manufacturing has been discussing for almost a decade. Yet, many are still working to achieve the golden nexus.
In a 2020 KPMG report, of all Industry 4.0 technologies, only cloud computing had reached an advanced – though still incomplete –level of implementation.
But since COVID-19 exposed gaps in global supply chains and down came renewed calls to ‘re-shore’ manufacturing, the industry scaled quickly and many caught up on their digital transformation efforts – much to the tune of the broader economy.
In a bid to cement resilience and improve competitiveness on the world stage, we are now seeing a more promising future in the amalgamation of digital technologies and manufacturing operations on the production floor. Autodesk’s latest State of Design & Make report, which included surveying manufacturing organisations among others, suggests 36% of Australian makers regard themselves as ‘more digitally mature’ than their competitors. Of that group, 15% stated they have completed their digital goals. That means the manufacturing industry still has some way to go.
In the same report, a promising 73% of Australian companies indicate they will increase their digital investments in the next three years. The appetite for technologies such as robotics, AI, and Internet of Things (IoT) is expanding.
And the Federal Government is counting on it. In last month’s 202323 Budget, the Government promised to support 20,000 jobs over the next 30 years in advanced manufacturing. Further, it committed $14bn to the National Reconstruction Fund – one of the largest investments in Australia’s industrial history.
The emergence of generative AI – the technology exemplified by ChatGPT – is also expected to spur Industry 4.0 along. The technology has certainly captured the public’s imagination with impressive human-like conversations, and its advancement will be the best seen in the industry. After all, that is where technology has its greatest potential to solve real-world issues and build strength into the economy.
As Australian manufacturers steam ahead in building production strength and uplifting sovereign capability, we expect emerging technologies to become more common. Beyond cloud, AI and machine-learning, 4.0 technologies will include Internet of Things sensors, virtual reality, 3D printing, and digital twins – these are virtual models that replicate real world environments to test behavioural changes of new equipment or processes.
Together, these technologies create an endless trove of data. And their ability to communicate will be most crucial in establishing accuracy, reliability, and visibility over operations.
According to IBM, the value of data sharing in manufacturing process optimisation is estimated to reach over $100bn. Yet only 28% of manufacturing organisations are tapping data from their equipment, processes, and systems.
Approaching data connectivity in this way will only result in 4.0 technology investments failing before they even start.
Why? The thousands of sensors and systems running a manufacturing facility work best when the technology can communicate and operate together. When these technologies work in silos and access to their data is fragmented, the applications and devices operate alone, blind to what is happening across the entire ecosystem.
If Australian manufacturers are to capitalise on the fourth industrial revolution, they need to recognise data as their greatest asset. As new technologies come through the roller doors, they should not be plugged in and left alone. Sensors, apps, and systems must be synchronised to ensure every string is connected and accounted for. A connected manufacturing facility would, for example, unlock trapped data from manufacturing systems, allowing workers to quickly resolve issues before they escalate. Benefits extend to having the ability to link R&D and production systems to customer service and warranty claims, allowing the manufacturer to track, understand, and remediate problems with a more comprehensive view of the environment. Ultimately, a connected 4.0 facility eliminates guesswork and accelerates time-to-resolution for production and customer service issues.
By bringing together technology assets to unlock the data they contain, Australian manufacturers will be better equipped to reduce error risk, make better real-time decisions, and ensure technology investments provide true ROI.
The goal is to reach destination 4.0, without a hitch. And that is best done with a connective data tissue, acting as a layer of assurance in the future of manufacturing. boomi.com