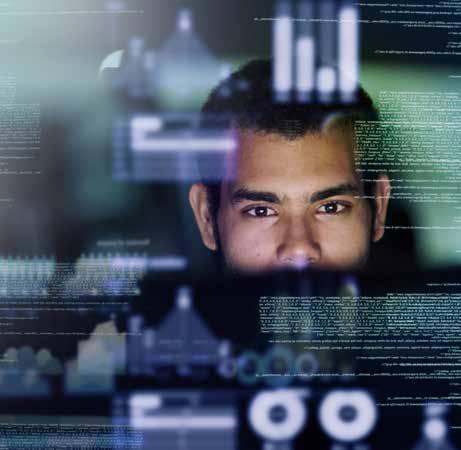
3 minute read
Our future, our skills
from AMT AUG/SEP 2023
by AMTIL
When Marty McFly hopped into the DeLorean in 1985 to head back 30 years, he was confronted by an analogue world, at least to his eyes – and ours.
McFly struggled through and, most importantly, ensured that the guy got the girl, notwithstanding his ham-fisted efforts. Our skilling needs have changed significantly, as has the way in which those skills have developed. If we go back 30 years, like Marty did, what would we see?
In 1993, we were in the second full year of the manufacturing industry restructuring process. Fundamentally, the changes focused on obtaining new skills to deal with those technologies coming on stream and, just as importantly, recognising the skills workers already had. This recognition was done on the job.
As part of the process, the AMWU and AiGroup trained over 5,000 representatives in the fundamentals of recognition of prior learning and recognition of current competencies procedures and Tradespersons’ Rights regulations. This ensured that those skills essential to the new realities in workplaces arising from new production techniques and technologies were recognised. At the same time, workplace consultative arrangements were enhanced; the notion that “managerial prerogative” (what is now called the C-Suite) would solve all the work organisation and productivity issues was given short shrift.
The result of that hard work was the massive 25-year long trajectory of productivity increases. The wealth of Australia was increased and, through better jobs and pay and superannuation, that productive wealth was shared.
The basis of this was the strong and effective partnership between workers (and their unions) and employers. Although it became politically contested in a rash of “IR reforms” from 1996 onwards, those productivity increases were permanent.
But, like the DeLorean, the technologies of 1993 are now outdated. Innovations like the CD-ROM have been replaced by the cloud; robotics and AI are now incorporated in many workplaces. And the skills to operate them are changing as well.
While the basic skills of manufacturing remain, as ever, the knowledge of and ability to use tools, form materials, read a drawing, and machine and manipulate the variables necessary to produce the finished product, the nature and complexity of those skills have changed. Radical technologies like CNC – automatically and digitally controlled machining processes –in the 80s have been enhanced by robots and cobots, augmented reality and digital twins (though, to date, AI has frightened more than it has informed).
Yet in Australian manufacturing, investment in new plant and equipment still lags. Worse, skill development and recognition is an uphill battle. While the AMWU welcomes developments like the creation of Jobs and Skills Australia, where I am one of four ACTU representatives, we need greater action and investment on skills if we are to meet the challenges of 21st Century manufacturing.
This is especially true after what we’ve seen in the past decade or so. Tony Abbott might have been adamant that WorkChoices was “dead, buried and cremated” but the vindictive anti-union philosophy at its heart was borne out by the changes which occurred in training and skills. From being industry-led, with business and unions as equal partners, the Abbott government could not wait to abolish the Australian Workforce and Productivity Agency and remove unions from oversight arrangements, which devolved on the
Australian Industry Skills Committee. The upshot was that VET became the realm of experts, although they were most adept at telling us what we would have rather than working with us on what we need.
The heart of our approach, especially on skills, is cooperation. The AMWU has reached out to the AiG, not because we want to recreate the “good old days” of the 1990s but because we need a new cooperative approach to skilling and reskilling manufacturing workers. When we were able to do the seemingly impossible in the 1990s, all Australians benefited. Isn’t it time that we saw real, sustained investment in training and technology, consultation, and work processes to improve our national competitiveness?
We’re not hankering for a DeLorean to take us back but focused on the need for a future-facing manufacturing industry which combines the best of that cooperative 1990s approach with the skills and technologies of the digital age. It might just lead us to another productivity boom and set up a new manufacturing industry for the next 25 years. amwu.org.au