
23 minute read
INDUSTRY NEWS
from AMT OCT 2022
by AMTIL
Creating in engineered wood
Henkel embarks on local production of Loctite PUR adhesives in Australia.
Henkel is slated to produce Loctite polyurethane (PUR) adhesives in Australia from the first half of 2023. The adhesives will be manufactured in Kilsyth, Victoria, to serve the engineered wood industry across Australia and New Zealand. “Purbond adhesives are used globally and have long been the benchmark for innovation and reliability in the engineered wood industry. Producing Purbond locally is an exciting endeavor that opens many opportunities for us to help our customers in Australia and New Zealand to grow,” said Brad Simpson, Sales Manager and Business Unit Manager, Adhesives Technologies, Engineered Wood, Furniture and Building Components. Henkel’s adhesive experts at its Innovation and Application Labs in Sydney and Auckland, help customers explore ways to expedite the time to market and optimise their own production processes for the development of engineered wood solutions. With the production of Purbond in Australia, adhesives production can be customised for specific performance requirements such as fire resistance and for use with modified timbers. “By localising the production of Purbond adhesives, our customers will benefit from reduced lead times from order to delivery, as well as greater supply chain security. This reflects our commitment to putting our customers at the centre of what we do,” said Warren Grigsby, Business Development Specialist, New Zealand. Purbond adhesives for engineered wood construction With a growing environmental awareness surrounding construction and material use, engineered wood has become an increasingly popular design choice for load-bearing mass timber and high-tech structural engineering applications. Approved for use in all major engineered wood construction markets, Loctite Purbond adhesives make it possible to manufacture glued wood components that are free from harmful industrial solvents and formaldehyde. In addition, they can be specifically engineered and controlled to enable the use of engineered wood in ever-new ways. Henkel holds leading positions in many markets and categories around the world. Founded in 1876, Henkel looks back on more than 140 years of success. In 2021, Henkel reported sales of more than 20bn euros and an adjusted operating profit of about 2.7bn euros. The company employs more than 52,000 people globally – a passionate and highly diverse team, united by a strong company culture, a common purpose, and shared values. henkel.com
Dandenong has an advanced future
Manufacturing the advanced future in Dandenong with Nissan Casting Australia, BWX, Spee3D and more.
The Andrews Labor Government is backing advanced manufacturers in Dandenong to expand, shaping the south-east Melbourne region into a hub for production excellence and a magnet for investment and high-skill jobs. A growing list of leading companies are choosing to expand or base their global operations in Dandenong, including automotive component producer Nissan Casting Australia, 3D printing manufacturer Spee3D and skincare giant BWX and many others. With support from the Labor Government, these advanced manufacturers are injecting a combined investment of more than $150 million into the region and creating 230 new local jobs. Dandenong hosts almost 1,400 manufacturing businesses and more than 21,000 workers. They transform a range of advanced materials into new products, creating high value components for the next generation of space, aerospace, defence, mobility and medical technologies. The highly skilled jobs that have been created in the region include engineering, production and technical roles in mechanical, mechatronics, electrical and digital technologies. Nissan Casting Australia has invested $15.5m to expand its Dandenong South facility, which produces aluminium die-cast components used in Nissan’s electric vehicle models sold around the world. “With nearly 40 years of operations in Melbourne’s south-east, this will help us to expand our production of Australian-made electric vehicle components to the global market,” says Peter Jones, Nissan Casting Australia Plant Managing Director. The investment will create 41 local jobs in engineering, management, and production and allow the company to boost its automation and robotic operations, building Victoria's skills base. The locally made parts will be used at assembly plants around the world, including in Japan, Thailand, and the USA. Nissan Casting Australia's Dandenong South facility produces aluminium die cast components used in Nissan's electric vehicle models sold around the world, including the LEAF. Greater Dandenong is located approximately 35kms from Melbourne’s CBD and is the most culturally diverse community in Victoria with residents from over 160 birthplaces around the world. Victoria is the manufacturing state of the nation. The industry is worth around $30bn to the Victorian economy each year, providing more than 27% to the nation’s manufacturing output. The Government is helping the state’s advanced manufacturers to grow, innovate and stimulate job creation through initiatives including the $2bn Breakthrough Victoria Fund and the $40m Victorian Industry Investment Fund, which was included in the 2022/23 Budget. “We support advanced manufacturers in Dandenong and around the state so they can expand and create secure jobs for Victorians,” the Minister for Industry Support and Recovery Ben Carroll said. “Dandenong is a success story of innovation and good investment – and we will continue to back the region so it can fulfil its cement itself as one of the key advanced manufacturing precincts in Australia.” djpr.vic.gov.au
Australia’s ECI ranking falls
Australia’s Economic Complexity Index (ECI) ranking has fallen to 91st on the global index, the lowest of any OECD nation. Manufacturing is the answer to address Australia’s declining ECI ranking by helping transition the economy from raw commodities trade to valueadd manufacturing. The Advanced Manufacturing Growth Centre (AMGC) advocates for greater focus on helping local manufacturers to transform and scale, to increase global competitiveness, and secure the nation’s future prosperity. The latest data released by the globally respected Harvard Business School reveals that Australia’s Economic Complexity Index (ECI) rating has slid to 91st, down eight positions in the last ten years. The Harvard index systematically ranks 133 countries by their ability to manufacture and export diverse and complex things and has been a global benchmark of a nation’s global impact since 1995, when Australia ranked 55 on the index. The result places Australia in the bottom third of monitored nations for complexity, between Kenya and Namibia, and also means Australia is the lowest ranked OECD country despite its high level of wealth. The Index brings into sharp focus Australia’s economic reliance on exporting items of low complexity in the form of commodities, and highlights the immense opportunity the nation has to improve the complexity of the items it exports, by adding value to its abundant natural resources or making more complex items in areas of relative strength. The report states that: “Australia is less complex than expected for its income level" and goes on to say that: “Australia has seen a troubling pattern of export growth, with the largest contribution to export growth coming from low and moderate complexity products, particularly Ores, slag and ash and ICT products.” Since its inception in 2016, the Advanced Manufacturing Growth Centre (AMGC) has advocated and demonstrated the potential of Australia to grow the complexity of its exports through co-investing in local manufacturing excellence. AMGC’s Managing Director Dr. Jens Goennemann said, “The latest ECI rankings are a damning reflection of Australia’s reliance on raw commodities trade – or luck. If these ECI results were reflected in the elite sporting world, we would be mortified.” “Why is it that we accept such a poor result in our global complexity ratings when it is directly tied to our future prosperity? At some point the ‘Lucky Country’ will run out of luck; now is the time for us to act and begin to increase the complexity of the things we manufacture and export,” said Goennemann. The Harvard report goes on to state that: “Australia has not yet started the traditional process of structural transformation. A key source of economic growth, this process reallocates economic activity from low to high productivity sectors. It broadly moves activities out of agriculture into textiles, followed by electronics and/or machinery manufacturing.” Raising the nation’s manufacturing profile requires long-term policy and co-investment from the government as well as private sources. Multiple micro-investments matched dollar-for-dollar by industry participants incentivises Australia’s largely SME-based manufacturing companies to innovate and scale. To meet this national challenge, AMGC has successfully managed over $57m in co-investments directly to Australia’s manufacturing industry and encouraged manufacturers to scale and export. AMGC’s targeted co-investments into 141 projects, are expected to generate 4,000 new, highly skilled, and well-paid roles and on completion will return $1.6bn to the economy.
atlas.cid.harvard.edu/countries/14 amgc.org.au/projects/
Replace awkward ballscrews with Lifgo innovative gear units and precision racks
When fast, precise and synchronised linear motion is required, our Lifgo rack and pinion gear units have proven to be reliable in many industry sectors around the world.
Smart and robust modular units offer designers the opportunity to tailor projects to meet unique needs at low cost. Lifgo enables rapid design and ease of system development for complex projects. Offers reliability and capabilities that transcend traditional product designs and boundaries, securing a competitive advantage.

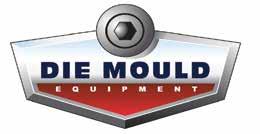
Lifting, Guiding and PositioningMaximising operational efficiencies and unlimited
combinations for various applications.
Industry sectors include: • Foodservice • Medical • Warehousing • Transportation • Forestry • Automotive

Converting wave energy into electrical energy
Harnessing power from ocean waves is a complicated endeavour into which a South Australian-Chinese research team is diving deep to take into a new direction.
A prototype system designed by Flinders University researchers delivers a robust generator made from recycled material that promises to help address small-scale local energy requirements and environmental pollution issues with further R&D. The ‘green machine’, designed around a wave-driven triboelectric nanogenerator (WD-TENG for short) model, integrates two small generators inside a recyclable tube to make cost-effective electricity in water from continuous immersion in waves. A new study published in the journal Nano Energy, by researchers at Flinders University and Beibu Gulf University in China, evaluated the low-frequency energy output of the TENG unit under various ocean wave conditions. “The experimental testing result indicates the WD-TENG can almost reach the rated output at Hz with 1.05 W/m2 power density,” says Flinders University College of Science and Engineering PhD candidate Mr Yunzhong (Steven) Wang. “Our modelling indicates that the new WD-TENG has decent durability and robustness under continuous operation and has potential to provide electricity to remote or rural properties close to the coastline, or on islands.” The experiment also showed the WD-TENG can sustainably charge a 47 μF capacitor to 0.496 V in a minute. The exchange charge density of the used triboelectric materials arising from the triboelectric charge exchange is 19.81 nC. The R&D will expand with support from the State Government’s Green Industries SA via a ‘circular economy’ student award for the research into ‘a wave-driven generator constructed from recycled materials’ presented last week. Lead researcher, Flinders University Professor Youhong Tang, says the team will now test the design in a watertank system, which integrates a self-designed wave creator to simulate actual ocean conditions as much as possible before the devices are tested at local metropolitan beaches. “This study shows the potential speculation approach to estimate an approximately best response wave amplitude to determine the suitable ocean state to obtain the optimised output performance of the wave-driven triboelectric nanogenerator,” says Professor Tang. “The 3D printing technology provides a cost-effective and relatively convenient approach to fabricate multi-shape triboelectric nanogenerators to satisfy the different ocean wave states,” adds co-author Mr Anh Tran Tam Pham. Associate Professor Xiangxi Han, from the College of Mechanical and Marine Engineering at Beibu Gulf University, says ocean engineering and technology have great potential in creating clean energy from wave power, or ‘blue energy’. China and other countries have been looking at various TENGs to convert the irregular kenetic energy of waves into electrical energy, including to electrochemical water splitting to produce zeroemission hydrogen. flinders.edu.au
Leussink appointed as Omega Sinto distributor
Leussink has been appointed the sole distributor for Omega Sinto Foundry Machinery for Australia and New Zealand.
Omega Sinto is a global manufacturer of chemically bonded sand equipment used in the foundry/metal casting industry. Originally established in the UK, Omega Sinto now operates around the world offering a wide range of products which includes sand mixers, mould handling equipment, core making machines, shakeouts, sand reclamation plants, coating plants, and more. Leussink Sales and Marketing Manager, Stuart Ward, says that the partnership with Omega Sinto takes Leussink into a new area of Australian manufacturing. “Under our new partnership, we will supply Omega Sinto’s equipment off-the-shelf, but provide installation and modifications where required,” he said. “After joining Leussink last year I began to look at new business opportunities and approached Omega Sinto. My professional background is in the foundry industry so it made sense for me to look at that area.” “At the time I began speaking with them about fabrication and engineering work, the local business manager they had in place had decided to retire so they needed new representation in Australia and New Zealand. It fell into place from there,” added Ward. Omega Sinto has almost 40 years of experience in the foundry equipment manufacturing industry, specialising in chemically bonded mould production equipment. The Australian metal casting/foundry industry produces iron, steel, and non-ferrous product for every major industry, including rail, defence, mining, construction, manufacturing, agriculture, water, automotive, health and energy. “At Leussink we don’t just sell products and walk away. We work with our clients to make sure the equipment we provide works for them by tailoring a solution to their needs and providing onsite visits and training sessions. “With the Omega Sinto products added to our range will work with clients to make recommendations about which item will suit their needs, as well as undertake modifications in our Illawarra state-ofthe-art workshop,” Ward said. leussink.com.au

All Energy Australia
All-Energy Australia, Australia’s largest clean energy event, is taking place this October in Melbourne to continue supporting the industry’s growth and to help accelerate Australia’s transition to a renewable energy future. This is a free-to-attend exhibition and conference from 2627 October 2022 at the Melbourne Convention and Exhibition Centre. With energy being at the forefront of many discussions with the government’s ambitious climate change bill being pushed through at the moment and countries across the globe realising that they can no longer rely on fossil fuels for their energy needs, it will be a welcome return for All-Energy Australia. All-Energy Australia is the country's largest and most anticipated clean energy event in Australia, which opens up a world of opportunities for industry suppliers and experts as well as those involved in renewable energy and energy storage sectors to expand business networks. All Energy Australia is organised in partnership with the Clean Energy Council and is where renewable energy professionals can get exclusive access to the latest technologies and trends and discuss the opportunities and challenges facing the sector. As the industry’s largest all-encompassing clean energy event, the expo floor will feature over 290 leading companies including Enphase, Fronius, GoodWe, Growatt, Nextracker, Sungrow, Longi, TrinaSolar, Shoals & More. And for the first time, there will be a dedicated Energy Management Zone within the All-Energy Australia exhibition. This dedicated zone will host its own theatre with sessions running throughout both days on sustainable solutions that facilitate improved energy management and increased cost savings. Clean Energy Council Chief Executive, Kane Thornton said, “Our industry stands ready to electrify Australia and establish our nation as a global clean energy superpower. We are on our way into the electric age, an age where Australia can be proud and powerful. It’s an incredible time of change and opportunity for our industry. All-Energy brings us together.” These sessions will also highlight innovative energy management technologies and services that support the reduction of energy bills and emissions. Session topics will be in agriculture, food and beverage manufacturing, metals and other materials manufacturing, residential buildings, commercial buildings and Government operations. “The 2022 event takes place at a crucial time in our country where Australia’s clean energy transition is more important than ever,” noted Robby Clark, Portfolio Director at All-Energy Australia. “AllEnergy Australia provides a platform for the industry to connect visitors with leading suppliers on our exhibition floor and drive conversations about the future of renewables at our multi-stream conference.” With the conference agenda to be announced in September, this year’s program will have more than 200 expert speakers discussing the latest in solar energy, energy storage, hydrogen energy, electric vehicles, bioenergy, distributed energy resources and more. Registrations are now open. The Exhibition and conference is colocated with Waste Expo, forming the largest gathering for waste and recycling management, clean and renewable energy and energy storage professionals in the country. all-energy.com.au

Kingsway Confectionery kept up and running with Enmin
Enmin’s quality, service and support the key ingredients for Kingsway Confectionery.
Founded in 1985 and acquired in 2004 by Phil Wicks and his son Ray Wicks, Kingsway Confectionery has cemented its reputation as a supplier of quality wholesale and retail confectionery products along with being a prominent co-packing partner for branded and private label products in the confectionery and snack food industries. In 2016 the business relocated to their current premises in Melbourne’s bayside suburb of Seaford. This move facilitated the immediate expansion of the operation and provided the necessary scope for further growth opportunities. In 2020 the need for additional capacity became apparent and the installation of their third production line was commissioned. Ray Wicks has taken over the mantle of General Manager from his now semi-retired father overseeing the day-to-day operations. Ray is supported by partners Jason Keegan (Production & Warehousing), Niki Totton (Sales & Development) and what they all agree are amazing and committed production and warehousing crew. “While our recognisable expertise is packaging goods, behind the scenes we are problem solvers and a valuable knowledge centre. We pride ourselves on being a trusted and agile business partner, and we are absolutely committed to the long- term growth and success of our customers’ products and brands,” Ray said. “We operate on an ethos of safety, quality, honesty, reliability, performance, innovation, cost competitiveness & efficiency. As Enmin’s values are aligned with ours, they have been awarded our new equipment contracts,” he added. Kingsway Confectionery’s association with Enmin commenced 15 years ago when a top cross feeder was installed to an existing production line. This was rapidly followed by an order for a hopper feeder to further modernise the line. “This installation was crucial and extremely time sensitive to our business and any delay would have created significant issues. For them to have got our new line up and running on time and on budget in the middle of the Covid lockdown last year, is testament to their abilities,” Ray concluded.
enmin.com.au confecpackaging.com.au

Green hydrogen company Hysata’s Series A funding exceeds $40m
The Clean Energy Finance Corporation, Kiko Ventures, IP Group Australia, Vestas Ventures, and Hostplus are among the top-tier investors supporting Hysata’s capillary-fed electrolyser.
Australian company Hysata’s world-leading hydrogen electrolyser technology has been supported by renowned global investors, as the organisation closes its oversubscribed Series A funding round of $42.5m. Virescent Ventures led the funding round on behalf of the Clean Energy Finance Corporation (CEFC), with participation from Kiko Ventures, IP Group Australia, Vestas Ventures (Denmark), Hostplus and BlueScope. Assembling such a high profile and high impact list of investors underlines the significance of the transformation that Hysata is bringing to the green hydrogen industry. The Hysata electrolyser operates at 95% system efficiency (41.5kWh/kg), delivering a giant leap in performance and cost over incumbent technologies, which typically operate at 75% or less. This high efficiency, coupled with the simple approach to mass manufacturing and low supply chain risk puts the company on a path to delivering the world’s lowest cost green hydrogen. “Our mission is to redefine the economics of green hydrogen production through our innovative proprietary electrolyser technology. The support of this international syndicate of clean energy practitioners and investors validates our core technology and our approach to scaling and mass manufacture,” said Paul Barrett, CEO of Hysata. “Green hydrogen is a vital energy vector on the world’s path to net zero, critical to decarbonising the hard-to-abate, yet vital, sectors of our economy such as steelmaking, heavy transport, and the chemical industry. The extensive end use cases for green hydrogen translate to a greater than trillion-dollar market opportunity. “Over the last 12-18 months, Hysata has been interacting with dozens of major customers globally. The impact our efficiency and system simplicity delivers to customers’ project economics truly moves the needle. We look forward to continuing to work with our shareholders and customers to bring this much needed technology to market as soon as possible.” The CEFC invested $10m into the Series A funding round, building on its initial $750,000 investment in the early commercial development of Hysata’s research. CEFC CEO Ian Learmonth said that backing a company like Hysata and its cutting-edge electrolyser technology is vital in helping to grow Australia’s clean technology ecosystem. “The CEFC is proud to continue our support for Hysata, which is set to be a major player in the global electrolyser industry. Green hydrogen will be essential to addressing the hardest to abate sources of emissions, and we’re excited to see Australian ingenuity providing the technology solutions that will help this industry reach scale. The CEFC has a strong focus on hydrogen related investments through both our Innovation and Advancing Hydrogen Funds and we are delighted to see Hysata continue to advance hydrogen to help meet future energy needs and reduce emissions in more sectors of the Australian economy,” Learmonth said. The CEFC investment is via its specialist Clean Energy Innovation Fund, which is managed by Virescent Ventures. “Hysata continues to make rapid progress and we are pleased to support such an innovative company with an outstanding team,” Virescent Ventures Partner Blair Pritchard said. “The continued growth of Hysata is an important pointer to the enormous potential of hydrogen to our net zero future.” Kiko Ventures’ Founding Partner, Robert Trezona, said Hysata has real potential to become a major global clean technology player. “Having assessed scores of electrolyser technologies in my 20 years in cleantech, Hysata’s technology stands out as a true breakthrough. The company has redefined the core cell architecture for alkaline electrolysis, producing a practical and scalable solution with game-changing efficiency. Hysata has the potential to be a globally significant company in the hydrogen economy and we look forward to supporting its growth, especially here in Europe,” Dr Trezona said. BlueScopeX’s General Partner, Michael Quinn, agreed that Hysata’s technology could play a significant role in the development of commercially viable hydrogen production. “BlueScopeX is pleased to be investing in Australian technologies coming out of our local communities, with Hysata being born in the Illawarra. Our industry requires smart, affordable technologies like Hysata’s to help progress the broader goal of decarbonisation, and we are excited to be supporting them on their path to commercialisation,” he said.
hysata.com virescent.vc bluescope.com

Mineral enrichment
IperionX successfully develops low carbon titanium enrichment process.
IperionX has successfully developed an innovative low carbon titanium mineral enrichment technology that upgrades lower content titanium dioxide ilmenite minerals into a high titanium synthetic rutile product. The company’s synthetic rutile product has been tested and evaluated by customers, which has confirmed the potential for a high-quality, high grade titanium feedstock with scope to be a superior and more sustainable product than other upgraded titanium feedstocks, including titanium slag. IperionX’s low carbon process eliminates the use of carbon reductants, including coal, which are typically used to upgrade low grade titanium feedstocks into high value, high grade titanium feedstocks. The low carbon synthetic rutile production process is the result of exhaustive R&D by Dr. Zak Fang and his team at the University of Utah on upgrading and purification methods for titanium feedstocks to produce titanium metal. Patent applications have been filed for this innovative synthetic rutile process technology, adding to IperionX’s valuable patent portfolio. Co-products of IperionX’s synthetic rutile process include a purified iron powder for potential sales into lithium iron phosphate (LFP) battery applications. IperionX intends to commercialise this low carbon, high grade titanium synthetic rutile product and has commenced feasibility studies for a synthetic rutile production pilot plant at the Titan Project in Tennessee. IperionX Limited has successfully developed high quality, low carbon titanium mineral enrichment technologies, having upgraded ilmenite titanium minerals from the Titan Project in Tennessee into a high-grade titanium synthetic rutile product. High grade titanium dioxide (+80% TiO2) feedstocks include natural rutile, synthetic rutile and titanium slag, and are primarily used in creating inputs for titanium metal in the form of titanium tetrachloride and paint and pigments in the form of purified TiO2. Natural rutile is a mineral with TiO2 content of 92%-95%, while synthetic rutile and titanium slag are upgraded high grade TiO2 feedstocks produced from ilmenite, with a TiO2 content of 88%95% and ~80% respectively. Given their relative scarcity and value in use, high grade TiO2 feedstocks are higher priced products than the more commonly found lower grade ilmenite. Importantly, the global supply of natural rutile is in significant decline, with other high grade titanium feedstocks including synthetic rutile and titanium slag expected to fill the widening supply gap. Synthetic rutile commands a price 4-5x that of ilmenite, which has a typical TiO2 content of 45%-65%. Long term price forecasts for synthetic rutile are ~$1,000-$1,200 per ton, compared to ilmenite with a long-term price forecast of ~$200-$300 per ton. This price multiple allows for the potential to significantly increase the value of the Titan Project resource base through upgrading of ilmenite to low carbon synthetic rutile. The majority of global synthetic rutile production occurs in Western Australia by the world’s largest titanium mineral companies, Iluka and Tronox, via processes based upon the Becher Process. The Becher Process consists of roasting low-grade ilmenite using coal in a rotary kiln at temperatures of more than 1,100°C to convert the iron oxide in the ilmenite to metallic iron, and then ‘rusting’ the kiln product in an aerated salt solution to remove most of the metallic iron. Titanium slag is a widely adopted method to produce high grade titanium feedstocks, which occurs via open arc AC or DC smelting of ilmenite with electricity, using a carbon reactant in the form of coal, to produce titanium slag and pig iron products. The development of IperionX’s low carbon synthetic rutile is the product of exhaustive R&D by Dr. Zak Fang and his team at the University of Utah, which originated around development of purification methods for titanium feedstocks for use in HAMR titanium metal production. Over the last year, Dr. Fang, his team, and IperionX’s R&D division have worked closely together to adapt the titanium purification methods to produce a low carbon, standalone synthetic rutile product. Anastasios (Taso) Arima, IperionX’s Managing Director and CEO said: “We are delighted that Dr. Fang’s research and development, in collaboration with IperionX’s engineers, has successfully delivered an innovative process technology to produce a high quality, low carbon synthetic rutile product. This patented technology has the potential to significantly enhance the value of the Titan project by manufacturing a low carbon, high grade titanium feedstock for a market that is increasingly demanding a low carbon supply chain.”
iperionx.com
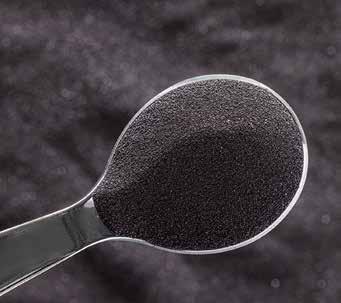
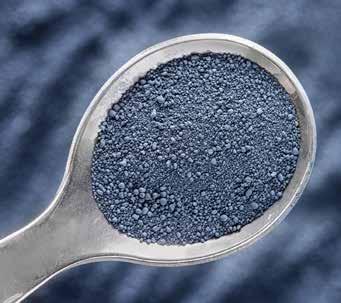