
4 minute read
Real time conveyed quality measurement
On-Line Real-Time Measurement Technologies for Bulk Materials
Real time conveyed quality measurement provides unique opportunities to improve process control. A number of proven technologies are used throughout the resources sector that provide significant improvements to existing processes by better measuring and managing bulk material quality.
Advertisement
Composition measurement can be performed using high specification Prompt Gamma Neutron Activation Analysis (PGNAA) for coal analysis in coke-making, sinter analysis in iron-making as well as scrap steel analysis in steel-making. Moisture can also be measured in coal and sinter using microwave transmission and in coke, sinter, magnetite concentrate, and scrap steel using fast neutron and gamma transmission.
All these technologies measure continuously through the full conveyed depth and provide results in real time directly to the plant control system and all analysis data is owned by the client. Remote access ensures onsite time is minimised and support is readily available if needed. All analysers can be installed during planned shutdowns and no interruptions to operations are anticipated throughout the life of the analysers which have no contact with conveyed flows and no wear components or consumable spare parts.
Quality variability
Material quality variability is a key challenge in process control. Despite mining, beneficiation and concentration processes, materials handling and blending there is still considerable variability when materials reach the next stage in the process. Iron ore, coal and scrap steel are typically received from multiple sources, each utilising their own quality control systems. Despite certificates of analysis there is usually significant quality variability within and between shipments received. Where bulk materials are sold on tonnage the risk is that moisture content has been added to increase weight.
Quality variability is well accepted as having a major impact on process performance and managing quality requires appropriate high quality measurement systems, preferably those that minimise sampling error. Rather than taking more samples and not reducing sampling error, the smarter solution has been to measure quality continuous using representative technologies. Real time measurement is an obvious method to achieve this, with typically short paybacks, sometimes a few months and normally much quicker.
Conveyed flows represent the best opportunity to measure continuously as flow rates can be relatively consistent and material presentation to the measurement technology is ideal for penetrative analysis. High specification analysis systems are customised to each application to optimise the quality of the measurement data produced for the process control needs. Measurement of materials in stockpiles, hoppers, chutes or trucks is problematic for a number of reasons, mostly that no technologies will penetrate sufficiently to provide representative analysis and some systems interfere with material flow and can cause plant downtime so these are best avoided. Surface analysis technologies are appropriate for homogenised materials but these are rare in the resources sector. Coal, coke, iron ore, sinter and scrap steel will contain variable composition that is not reflected by the composition at a particular location on the surface of a stockpile or flow of material.
Representative sampling of bulk materials can prove unreliable due to segregation of materials by particle size, layering, or density variations and the required sample size and frequency to minimise sampling errors. Effective sampling is still required for analyser calibration and therefore a suitable sampling protocol should be developed to address these issues. Online analysers require calibration checks every six months so any sampling required can be made manageable through good planning and implementation and need not interfere
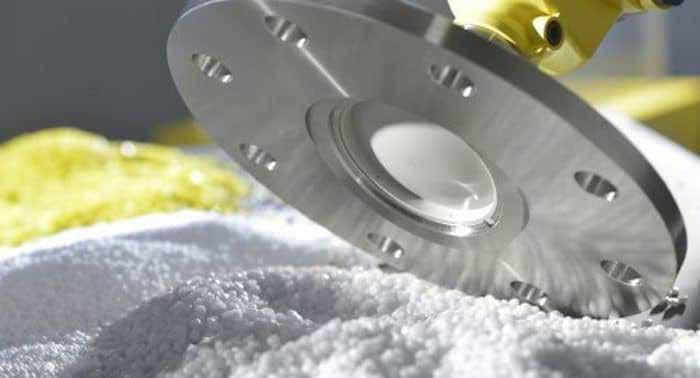
with normal production.
HAVER & BOECKER is one of the leading companies that provides innovative systems for particle shape and particle size analysis that set standards in function, precision and reliability. One of their renowned technology is the HAVER CPA, which is a versatile application for CPA Online measuring devices.
The HAVER CPA Online technology is the optimum basis for a versatile, flexible and reliable solution when it comes to Dynamic image analysis (DIA) in the production process. The modules of the particle analyzer are compactly designed and can be integrated almost everywhere. It is also always possible to retrofit it to existing processes. Moreover, standard distances of up to 100 meters are possible for the connection between the PC system and the measurement instrument.
The modules are resistant against harsh surrounding conditions. This is achieved by its robust construction in stainless steel and automatic pneumatic cleaning of camera and light scource.
The HAVER CpaServ software offers support for the common communication standard via Modbus TCP with plant PLC system. Thus a connection is a mere formality.
Moreover, the software also offers diverse evaluation tools and transfer components, e.g. TXT/CSV-Export. Together with the possible direct control of possibly already existing sample taking systems, the HAVER CPA Online can be operated as an independent system. In this case no process control system or PLC connection is necessary.
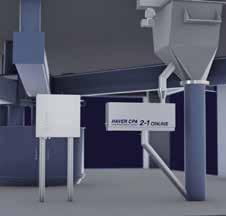
DIE DRAHTWEBER
INTELLIGENT PARTICLE ANALYSIS. BENCHMARK FOR PRECISION.
HAVER EML 200
HAVER CPA 2-1
Germany: HAVER & BOECKER ∙ Particle Analysis Ennigerloher Str. 64 ∙ 59302 OELDE [T] +49 (0) 2522 30-131 ∙ [E] pa@haverboecker.com [W] haverparticleanalysis.com South Africa: WIRSAM SCIENTIFIC & PRECISION EQUIOMENT (PTY) LTD. 23 Menton Road Richmond ∙ 2092 Johannesburg [T] +27 11 4821060 ∙ [E] wirsamjb@wirsam.com [W] wirsam.com HAVER S INLINE
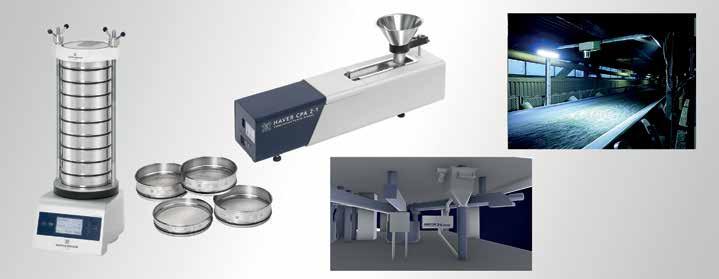
HAVER CPA 2-1 ONLINE