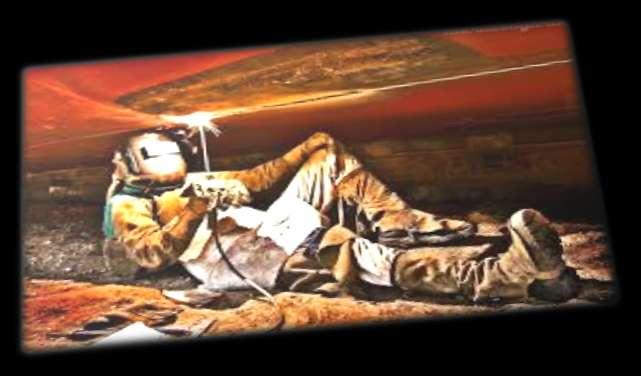
15 minute read
SOLDADURA APLICADA A LA Lo Mejor de la
Contiene Información Acerca de:
El MS Fullagar primer Barco de casco soldado en la Historia La Soldadura en la Construcción Naval. Múltiples proceso de Soldadura que Impresionan en el Área Naval. Cortes Utilizados en la Fabricación de Buques. Nuevos Proceso que se consideran por separa en el Área Naval.
Advertisement
Editorial En portada: Se podría llegar a pensar que desde los inicios de la soldadura moderna, esta ha estado siempre presente en todas las creaciones del hombre. Pocas innovaciones han causado tanto beneficio al ser humano como desarrollo de la soldadura. No obstante, has de saber que por lo menos en lo que a barcos respecta, su incorporación es relativamente reciente a la calderería naval. Hasta los periodos de la segunda guerra mundial los barcos eran fabricados a través de un proceso de unión de planchas a través del remachado. El acero dulce y hierro forjado de los remaches era más que suficiente para garantizar la resistencia y estabilidad de la nave. La Soldadura en Barcos es el nuevo estándar Foto portada: Mantenimiento a un Barco Contenido 3 El MS Fullagar primer
Construcción Naval. 7 Múltiples proceso de
Soldadura que Impresionan en el Área
Naval. 9 Cortes Utilizados en la
Fabricación de Buques. 11 Nuevos Proceso que se consideran por separa en el Área Naval. Redactores: Andy Rivas Cristopher García David Sánchez Diseño y diagramación: David Sánchez Andy Rivas Corrección: Cristopher García Editor: Andy Rivas
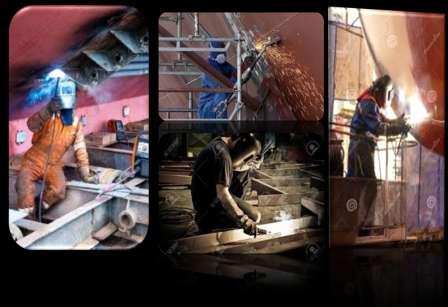
El MS Fullagar
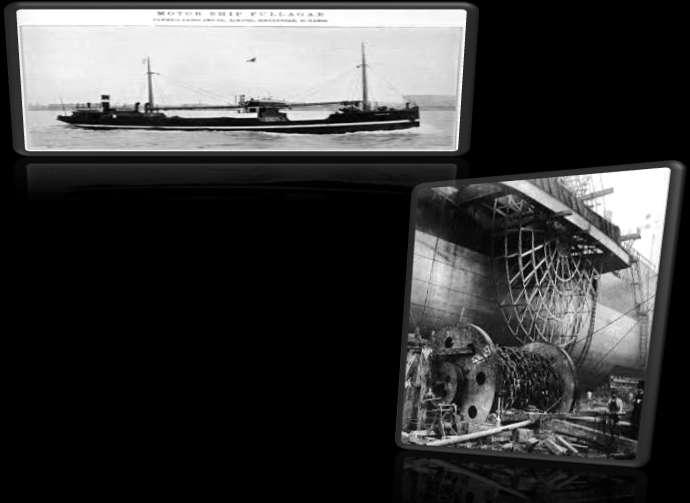
Primer Barco de Casco Soldado de la Historia
Hasta y durante la Primera Guerra Mundial, el remachado era clave en la construcción de grandes buques en todo el mundo. Aunque los remaches eran colocados inicialmente a mano con grandes martillos, la industria de principios de siglo había adoptado ya el uso de remachadoras portátiles, primero hidráulicas y más tarde neumáticas.
A pesar de que la aparición de estos equipos aumentó considerablemente el número de remaches que podían colocarse en una jornada, los astilleros dependían más y más de la dura y difícil labor de las cuadrillas de remachado según los buques se iban haciendo más y más grandes. Pero el número de mayo de 1921 de la revista Popular Mechanics incluyó un artículo sobre un buque revolucionario que utilizaba un nuevo tipo de uniones para sus planchas. El buque era el MS Fullagar, un pequeño carguero que habría pasado desapercibido para la historia si no fuera porque fue el primero en utilizar la soldadura por arco eléctrico en lugar de remaches para unir las planchas de su casco.
La soldadura por arco eléctrico se generaba mediante el paso de una corriente eléctrica a través de una varilla de acero o electrodo recubierta por amianto. La fusión del electrodo y las piezas a unir producían la unión. Las ventajas de la soldadura frente al remachado eran sobre todo la reducción del peso de los buques y la mayor rapidez en la construcción.
La soldadura ya había sido utilizada en la construcción naval antes de la Primera Guerra Mundial, aunque solamente en reparaciones. Por ello
en 1918 el Lloyd’s Register publicó las Provisional Rules for Electrically Welded Ships (Reglamento Provisional para Buques Soldados Eléctricamente). Este primer reglamento marcaba el camino en esta técnica pionera, recomendando la aprobación de electrodos y planes de soldadura, así como la formación y supervisión del personal involucrado en los procesos de soldadura. El Fullagar sería la prueba de fuego para este nuevo sistema de unión. Un año antes de que el Lloyd’s Register publicase su reglamento, el astillero
inglés Cammell Laird había dado un paso clave en el desarrollo de la soldadura en la construcción naval, con la pionera instalación de un equipo de soldadura por arco eléctrico. Así, cuando en 1919 recibió el encargo para la construcción del Fullagar tomaron la decisión de hacer de él el primer buque de casco completamente soldado.
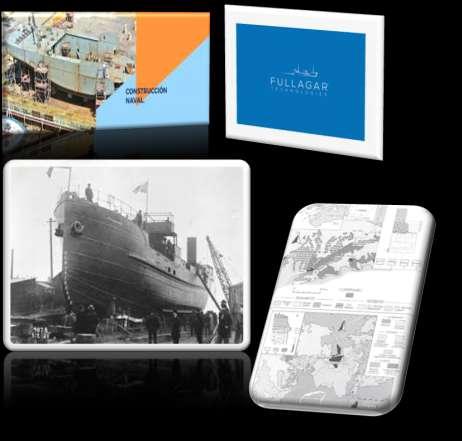
Cuando el buque fue botado en 1920, el Lloyd’s Register, que había supervisado todo el proceso constructivo del mismo, le otorgó la cota de clase +100A1 con la notación especial
Electrically Welded, Subject to Biennial
Survey-Experimental (Soldado Eléctricamente, Sujeto a Supervisión Bianual –Experimental). El armador del Fullagar destinó el barco al transporte costero de mercancías, en el que habitualmente el buque sería varado mientras se cargaba y descargaba, lo que demostraría la resistencia de la soldadura del casco.
Durante su vida útil el Fullagar sufrió diversos incidentes, y aunque algunas de sus partes resultaron dañadas, su soldadura siempre se mostró en perfectas condiciones. En 1937, tras 17 años de servicio, el Fullagar, renombrado como Cedros, se hundió cerca de Baja California, tras chocar con el Hidalgo. A pesar del éxito del Fullagar, la soldadura no fue adoptada plenamente en la construcción naval hasta la Segunda Guerra Mundial, cuando el esfuerzo de guerra exigió la construcción masiva en Estados Unidos de buques de carga, los Liberty Ships.
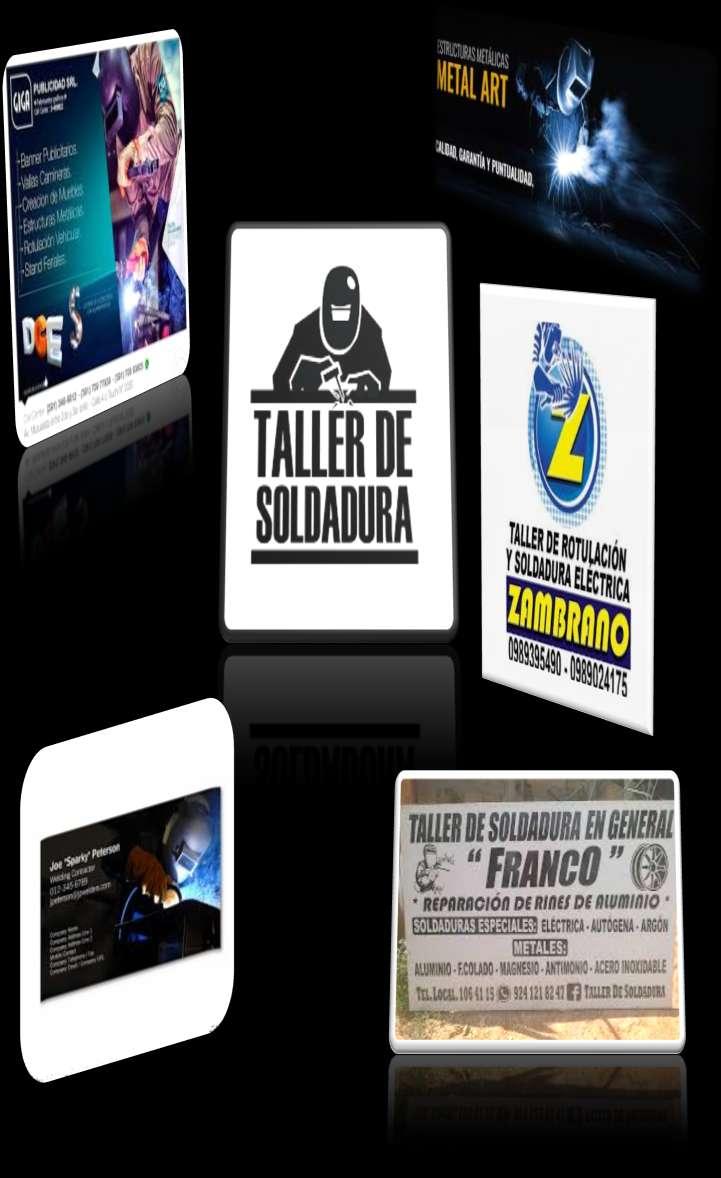
La Soldadura en la
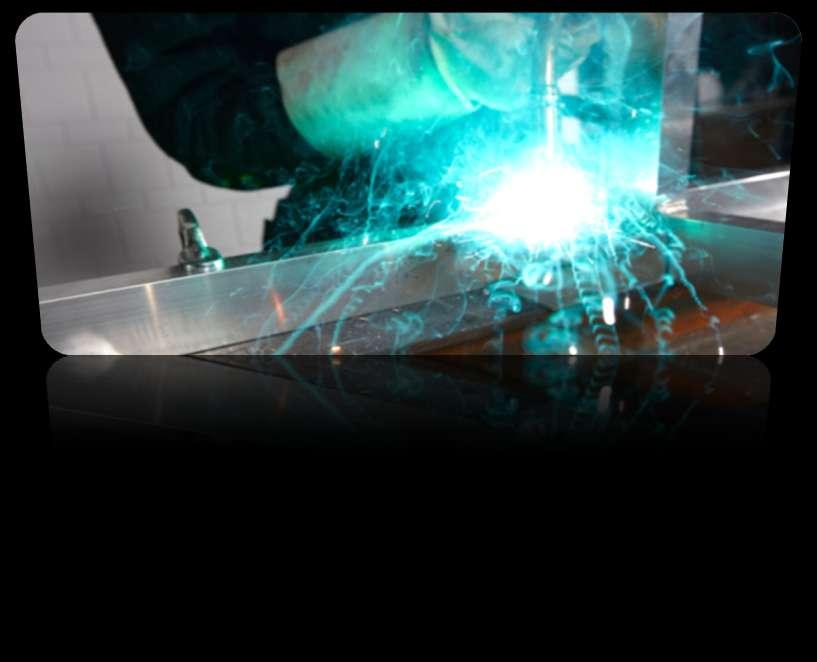
Hoy en día los buques se confeccionan con cientos de planchas de acero, y para llegar a conseguir modelar la forma del casco diseñado es muy importante utilizar un proceso de soldadura adecuado para dichas planchas. El peso de la soldadura en el buque supone entre el 3% y el 5% del peso total de acero del mismo. Para hacernos una idea, en un gasero de 145.000 m 3 de capacidad de carga con unos 270 metros de eslora (más de tres campos de futbol) y un peso en acero de unas 23.500 toneladas, la
Construcción Naval
soldadura supone entre 700 y 1.150 toneladas adicionales, cantidad importante a tener en cuenta en la estabilidad, capacidad de carga del buque y consumo de combustible.
En la actualidad hay muchos motivos que hacen relevante la labor del personal soldador en el proceso de construcción de un buque. Así, por ejemplo, la aplicación de excesivo calor a la hora de realizar una soldadura, debilitaría las propiedades mecánicas del acero que se pretende unir, pudiendo ocasionar a la larga daños estructurales que podrían incluso provocar el colapso de su estructura; o la utilización de un cordón de soldadura mayor al estrictamente necesario, añadiría un sobrepeso de su estructura que aumentaría los consumos de combustible. En este sentido, el sector español de la construcción naval cuenta con personal soldador altamente cualificado, que goza del prestigio y reconocimiento incluso en otros sectores industriales, como es el de la automoción.
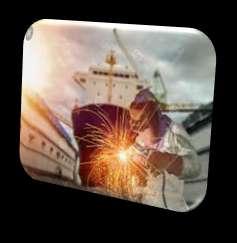
Soldeo por Arco con Electrodo Revestido

Es un proceso en el que la fusión del metal se produce por el calor generado en un arco eléctrico establecido entre el extremo de un electrodo revestido y el metal base de una unión a soldar.
El proceso se inicia con el cebado del arco, operación que consiste en tocar la pieza con el extremo libre del electrodo, cerrándose durante ese corto tiempo el circuito. El paso de corriente genera por efecto Joule el calentamiento del punto de contacto y de las zonas inmediatas, particularmente el extremo del electrodo. En el momento de separar el extremo del electrodo de la pieza, el metal del extremo libre del electrodo produce una fuerte emisión de electrones que se aceleran por la presión, chocan con los electrones de otros átomos del medio gaseoso, Generando una atmosfera ionizada en su entorno que permite el paso de corriente a través del aire. Los electrodos que van del electrodo al ánodo provocan la fusión parcial del electrodo y producen así el salto del arco.
Soldeo Por arco con gas Inerte y electrodo de volframio
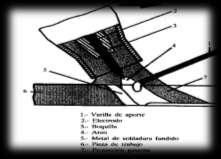
El procedimiento de soldeo por arco bajo gas protector con electrodo no consumible, también llamado TIG (Tungsten Inert Gas), utiliza como fuente de energía el arco eléctrico que se establece entre un electrodo no consumible y la pieza a soldar, mientras un gas inerte protege el baño de fusión. En este proceso de soldadura también es posible la utilización de Varillas como material de aportación. El proceso TIG se puede utilizar para el soldeo de todos los materiales, incluidos el aluminio y el magnesio y los materiales sensibles a la oxidación como el titanio, circonio y sus aleaciones Área Naval
Soldadura por arco metálico con protección de gas (GMAW).
Es un proceso de soldadura en el cual el calor necesario para la soldadura es generado por un arco que se establece entre un electrodo consumible y el metal que se va a soldar. El electrodo es un alambre solido desnudo que se alimenta de forma continua automáticamente, y se convierte en el metal depositado según se consume. El electrodo, arco, metal fundido y zonas adyacentes del metal base quedan protegidas de la contaminación de los gases atmosféricos mediante un flujo de gas protector que se aporta por la boquilla de la pistola, concéntricamente al electrodo.
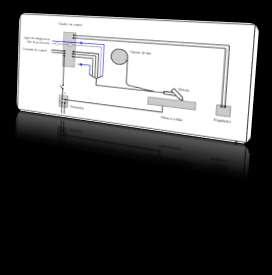
La técnica de soldadura con alambre tubular con flux interior es idéntica a la soldadura MIG/MAG, salvo el tipo de electrodo. Los alambres tubulares también son electrodos continuos, con la diferencia de que son huecos y en su interior contienen un fundente (flux), que tiene funciones similares a la del revestimiento de los electrodos revestidos.
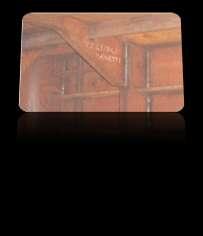
El proceso de soldadura con alambre tubular se utiliza principalmente en la soldadura de aceros al carbono, de baja aleación y de aceros inoxidables. El proceso se utiliza principalmente con CCPI (electrodo al polo positivo) pero también puede utilizarse con CCPD (electrodo al polo negativo) dependiendo de la composición de los elementos del alambre tubula.
Soldeo por arco de plasma (PAW)
El soldeo plasma, también conocido por las siglas PAW (Plasma Arc Welding), pertenece al grupo de procesos que utilizan un gas como medio de protección, y un arco eléctrico como medio para conseguir la fusión del material base y del material de aporte (en caso de ser utilizado). Dicho arco eléctrico se establece entre un electrodo no consumible de volframio, o volframio aleado, y la pieza a soldar (arco transferido), o entre el electrodo y la boquilla interna de cobre (arco no transferido). El soplete en el soldeo plasma consta de dos toberas una interna de cobre por cuyo interior circula el gas que formara la columna de plasma tras ser ionizado, gas de plasma, y otra externa por cuyo interior circula el gas encargado de proteger el baño fundido y el cordón a alta temperatura, gas de protección.
Soldeo por arco sumergido
El proceso de soldadura por arco sumergido, también denominado SAW (Sumerged Arc Welding), consiste en la fusión de un electrodo continuo, que puede ser macizo o tubular, protegido por la escoria generada por un flux, granulado o en polvo, con el que se alimenta el arco
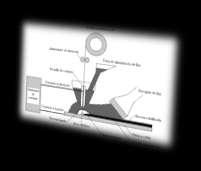
por separado. El proceso de soldadura por arco sumergido permite depositar grandes volúmenes de metal de soldadura de excelente calidad (tasa de deposición de hasta 50 kg/h) a bajo coste para una amplia gama de aplicaciones. El sistema es totalmente automático y permite obtener grandes rendimientos en producción. Se puede usar también como un proceso semiautomático, mediante una pistola manual, similar a la que se usa en soldadura MIG MAG, pero con diámetros de hilos mayores (hasta 2,4 mm) y de forma parecida a como en el proceso MIG se aportaría el flux en vez del gas de protección.
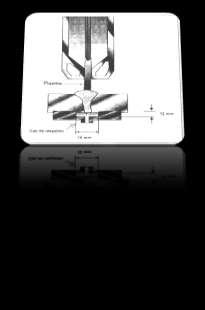
fabricación de buques
Los procesos de cortes para llegar a dar forma en los astilleros, las placas de aceros y sus secciones, en su mayoría, fueron cortadas utilizando la técnica de corte a gas, pero la introducción de la competencia con maquinas de corte de arco de plasma, ha llevado a su uso generalizad o en los astilleros de hoy en día.
Cortes con Gas
Este corte más que todo se logra básicamente un producto químico / reacción térmica que ocurre con las aleaciones de hierro y el hierro solo. El hierro y sus aleaciones o sus aleaciones pueden ser calentados a una temperatura a la que el hierro se oxida rápidamente en una atmosfera de oxigeno de alta pureza. El principio del proceso tal como se aplica al corte de placas de acero y sus secciones en la construcción naval es como sigue. Más de un area del metal pequeña es precalentada a una temperatura dada, con una corriente restringida de oxigeno se hace volar
hacia esta área. El hierro se oxida después de una banda estrecha, el oxido de metal fundido se elimina por la energía cinética de la corriente del oxigeno.

Una estrecha brecha de los lados paralelos se deja entre el corte de los bordes.
Corte con Chorro de Agua
La herramienta de corte empleada en este proceso es un chorro de agua concentrado, con o sin abrasivo, que se libera a apartir de un tobera a 21/2 veces la velocidad del sonido y en un nivel de presión de varios miles de bar. El corte por chorro de agua se puede utilizar en una amplia gama de materiales, madera, plástico, cauchos, entre otros. El corte por chorro de agua es más lento que los procesos de cortes térmicos y no es una maquina portátil.

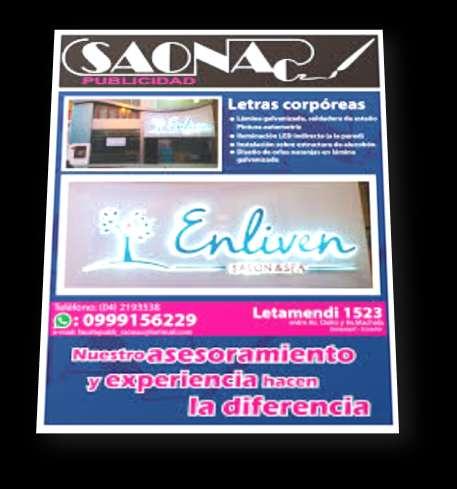
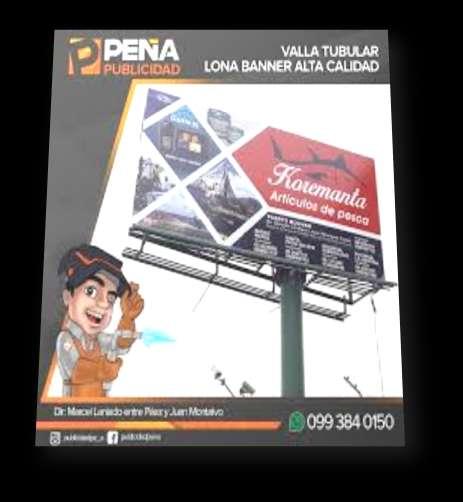
Soldadura de electro-escoria
El proceso de
soldadura electro-escoria se utiliza para soldaduras de estructura con componentes pesados de fundición, como marcos de popa y también se utilizan en una etapa anterior para realizar soldaduras verticales en el forro del costado más pesado cuando se fabrican unidades del casco, en los tramos que se apoyan en el atraque. Con el desarrollo del electro-gas el proceso de soldadura de electroescori a ya no se utiliza para este último propós ito.
Elec tro-soldadura de gas.
Para el constructor es de mayor interés el desarrollo de la soldadura de electro-gas. Esta es de hecho una soldadura por arco, el proceso que combina las características de soldadura de gas apantallado con las de soldadura de electroescoria. Son refrigerados por agua de cobre similares a los se utilizan en el proceso de soldadura del electro-escoria, pero se usa un alambre con núcleo de fundente en lugar de un alambre desnudo que se alimenta en el baño de soldadura. La fusión se obtiene por medio de un arco establecido entre la superficie del baño de soldadura y el alambre, y el CO2 o CO2 con argón, se suministra una mezcla de gas de protección desde las boquillas por separado o por los agujeros situados centralmente cerca de la parte superior de los de cobre. El sistema es mecanizado utilizando un sistema automático vertical hacia arriba de la máquina de soldadura, es alimentada por una fuente de energía que tiene un circuito de bucle cerrado de refrigeración, además de un sensor de nivel que ajusta automáticamente la velocidad de desplazamiento vertical.
El proceso más adecuado para las placas
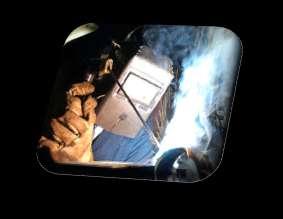
de soldadura es en un intervalo de espesor de 13 a 50 mm con los preparativos para cuadrados o en V, por tanto se utiliza en la soldadura para fines de construcción naval de las culatas verticales al lado del montaje de paneles de concha o de las juntas a topes verticales del terminal, para unirse a los bloques de construcción en el puesto de atraque o muelle. Para este fin es preferible el uso de una culata “w” simple o doble con el proceso de electrogas, ya que manualmente se puede culminar la soldadura si se produce cualquier avería. Uno cuadrado con apreciables diferencias sería casi imposible de superar de
Nuevos Procesos que se
consideran por separado en el área naval
forma manual.
La soldadura por láser
La soldadura láser se utiliza en la industria de la construcción naval y promete tanto como la soldadura que en sus procesos ofrecen la entrada de bajo calor y por lo tanto, tienen una mínima distorsión en las placas soldadas y en los refuerzos. La soldadura por láser pulsado se utiliza normalmente en espesores por debajo de aproximadamente 3 mm.
Soldadura térmica
Este es un método de soldadura muy útil que puede ser utilizado para soldar grandes secciones de acero, por ejemplo partes del marco de una popa. De hecho, es utilizado a menudo para reparar acero forjado de esta naturaleza.
Soldadura de termita es básicamente un proceso de fusión, el calor necesario para iniciar se consigue a partir de una mezcla de polvo de aluminio y óxido de hierro. Los extremos de la pieza a soldar se construyen inicialmente en un molde de arena o de grafito, mientras que la mezcla se vierte en un crisol con revestimiento refractario.
Por Fricción
La soldadura por fricción es una disciplina relativamente nueva, muchos materiales han sido soldados de esta manera en la industria de la construcción naval y es probable que sea más ampliamente utilizada.
La soldadura por fricción es un proceso de estado sólido que ofrece ventajas durante la soldadura por fusión para ciertas aplicaciones. En la producción de las juntas a tope, se utiliza una herramienta no consumible que gira el pasador perfilado, de los cuales se sumergen en la articulación en cono de dos placas y luego se mueve a lo largo de la articulación.
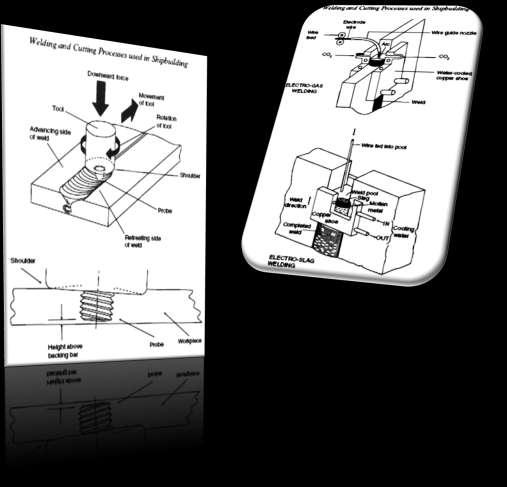
AUTOR: Cristopher García