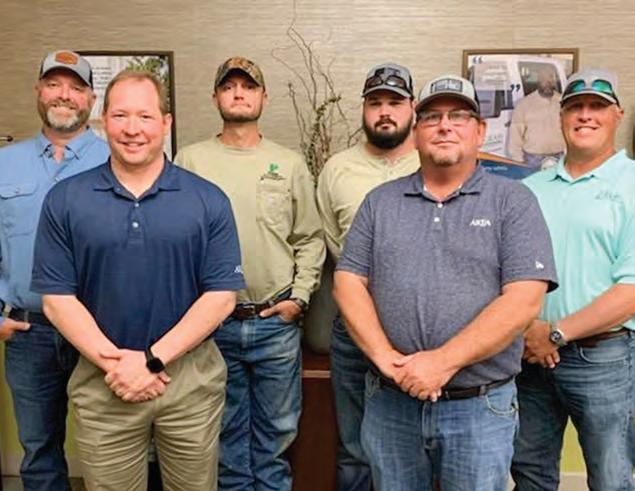
1 minute read
Safety cer WEC’s dedication shines through inspection
As the sun’s first rays brighten the sky, Wiregrass Electric Cooperative lineworkers arrive at headquarters in Hartford. Many visit the break room for a cup of coffee, where they are greeted by safety posters on the walls. The posters bear the faces of their co-workers and families and serve as a gentle reminder to prioritize safety, wear protective gear, stay focused and lead by example.
After loading their equipment and safety gear, the lineworkers head out with a shared purpose — to safely provide reliable and quality electric service to the communities they serve.
This routine captures the essence of Wiregrass Electric Cooperative’s sense of duty. Safety is not just a checklist — it is an integral part of the cooperative’s identity. Recently, WEC celebrated a significant milestone by completing the Rural Electric Safety Achievement Program, or RESAP, safety assessment.
The RESAP inspection is a comprehensive evaluation of safety and loss-control efforts, administered by the Alabama Rural Electric Association. Every three years, an inspector assesses the cooperative’s adherence to safety regulations and commitment to continuous improvements. It is an opportunity for WEC to demonstrate its dedication to protecting lineworkers and ensuring the safety of members.
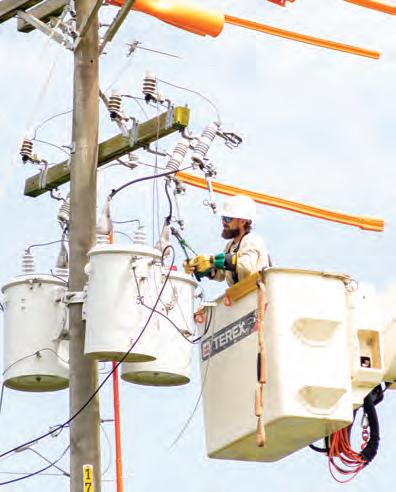
“It’s a top-to-bottom checkup of the cooperative as a whole. We’re looking at their facilities, fleet, equipment and procedures to make sure everything is up to standard,” says AREA Safety Coordinator Jeff Whatley. “We’re also looking at the big picture, the culture of safety. Are employees involved in safety conversations? Is leadership committed to their safety? How does the co-op communicate safety, and is it effective?”
Lineworkers brave high-voltage electricity and hazardous conditions daily. That’s why the safety posters throughout each of WEC’s four offices are more than just decoration. They represent WEC’s commitment to pro- viding a safe working environment where lineworkers return home to their loved ones at the end of the day.
From forming the safety committee, composed of lineworkers and representatives spanning various departments, to implementing comprehensive safety training and education programs, WEC cultivates a pervasive safety culture.
“We encourage open communication, so employees can report safety concerns and provide suggestions,” says Bethany Retherford, human resources and compliance manager. “We’re not just ticking boxes. We want everyone on the same page with an understanding that safety is a shared responsibility and that we’re all looking out for one another.”
Lineworkers’ voices are heard, their insights valued and their firsthand experiences are shared, allowing WEC to identify safety issues, share best practices and implement improvements. Through rigorous safety audits and inspections, WEC ensures