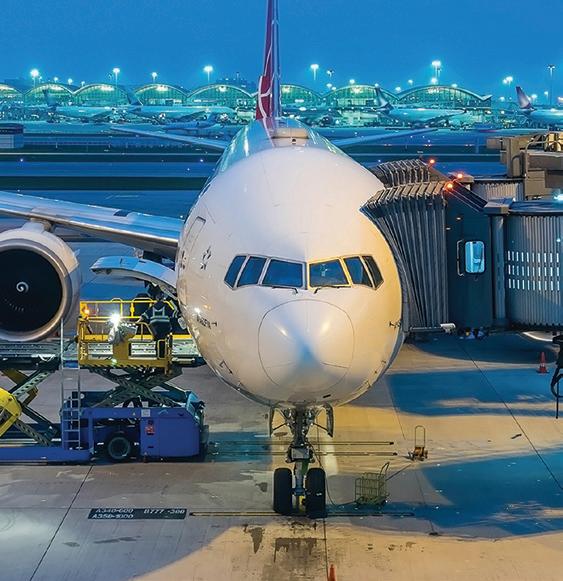
16 minute read
Time to upgrade
ENVISION and its mobile apps combine intuitive user-interfaces with streamlined workflows to help your teams work faster and more effectively.
The time saved on day-to-day tasks coupled with efficiencies gained from intelligent planning and analytics, allow you to increase profitability across your operations.
So if you’re ready for an upgrade, why not discover what ENVISION could do for you
Rusada
The software business in this case study, Rusada, was founded in 1987 as Russell Adams Ltd. then re-branded to Rusada. The company has offices around the globe with a US office in Colorado, a recently opened office in Toronto, and development centers in the UK as well as India and Sri Lanka. There are client services operations strategically placed in Australia, U.A.E, Singapore, USA and the UK to cover all locations. Rusada offers one main solution which is ENVISION, a modular system with ten main modules covering everything from fleet management and airworthiness through to base maintenance, line and component maintenance, inventory management, Flight Ops, and crew management, as well as support modules such as quality, auditing, safety occurrence reporting, human resources and finance.
As ENVISION is a modular system, customers can opt to take all modules to support their business or they can opt to take individual modules and they all integrate with one another. The options are available to be selected in accordance with what the user wants to do with the system.
Growth Challenges
One of the main reasons for Chrono and WAAS deciding on a new system was that they were experiencing problems as a result of the growth of the business. The biggest challenge was to bring everything together — sales, maintenance, the DMO, the ground service, HR, quality, inventory… That was the big challenge and was why Chrono and WAAS were looking for a solution that could bridge across all of those. With ENVISION, all of those options were available and so the goal is to have all employees onboard using the same data and the same platform. Sales will be able to have a good insight into what is coming, for instance, in terms of maintenance events and maintenance can know what is happening with sales. This bridging is the most important feature as far as Chrono and WAAS are concerned in order to support the company’s future growth.
The other challenge was linked to the 737 having a more complex component tree than, for example, a Pilatus, which meant that aircraft management was a consideration; to have good maintenance status reports and forecasts, and inventory management. It was necessary to be creative with the old system in order to track everything that the business wanted to track. That was another reason for the business to be looking for a new software tool and ENVISION had all of the features and capabilities that Chrono and WAAS were looking for. One example is a Fleet Serviceability Dashboard with real-time data to show several items, defects, upcoming maintenance, etc. The Work Package build up was also improved with the new system because it is more efficient. Despite being a part of the Chrono Group, the different operations are all individual companies with their own financial reporting; so Chrono Aviation is a customer of WAAS. The tracking of maintenance work performed was one thing that does not only work for WAAS but also for Chrono Aviation. It was a challenge because the new solution had to account for that structure and that required attention in order to segregate what is internal from what is external. The group had to make sure that customer work orders for similar aircraft and types did not get mixed.
The last challenge was the inventory management which is a significant matter. In the past, inventory had not been so well managed, so slowly WAAS was catching up. With the new system they have the transaction log as well as more features in the inventory management module than was available with the old system. ENVISION addresses every gap that there was on the inventory management side; the workflow helps the store personnel to be more disciplined as well as the requisition process helping a great deal the operation.
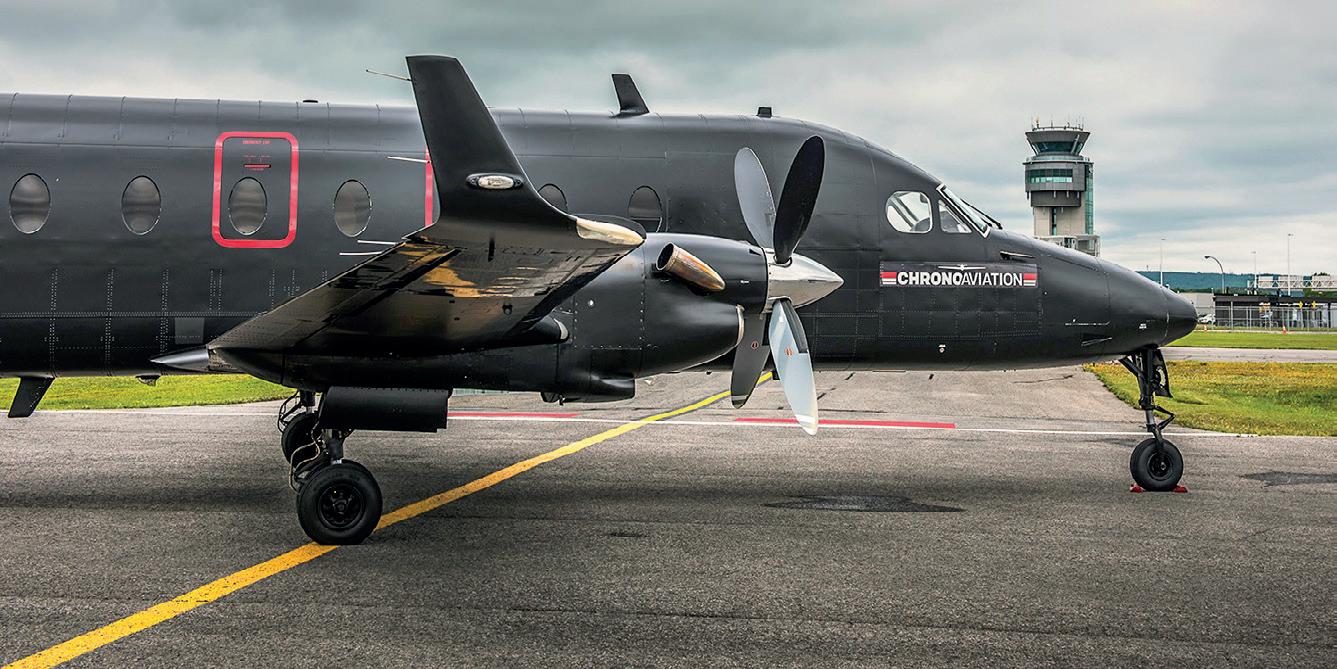
Envision Implementation
What was needed, for the implementation of ENVISION, was to break the task up into a number of areas, a standard implementation approach (figure 1).
Envision Implementation
§ Implementation began late 2019
§ Project followed Rusada’s 5 stage proven process
§ Carried out by their in-house deployment teams
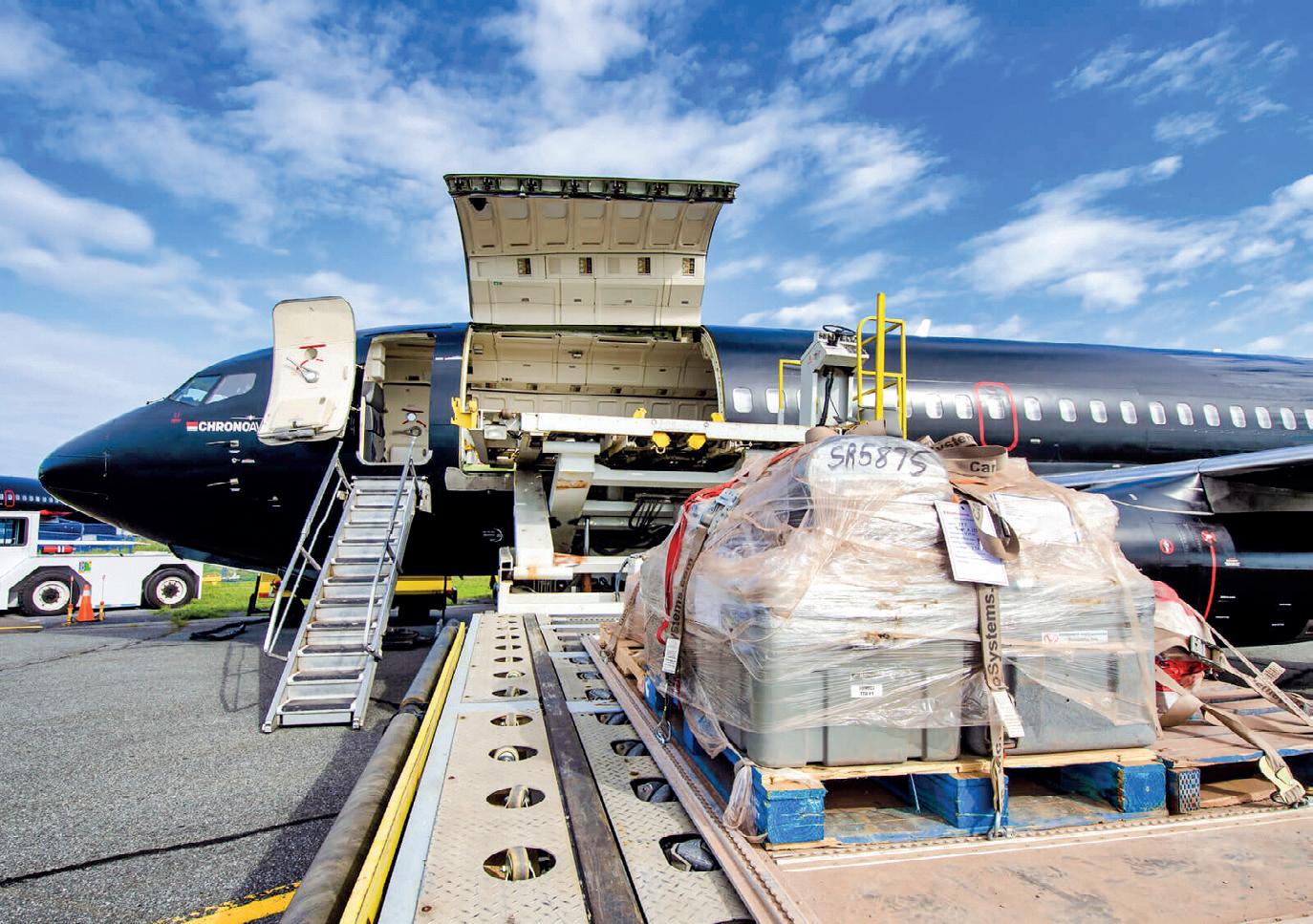
The project planning and installation phase ensured concentration on a lot of those issues referred to above and making sure that each of those issues could be translated into a solution within the system. That meant analyzing the existing process, converting it into an improved process and then considering how that new process could be carried out within ENVISION. It’s something that Rusada does at the beginning of every project, sit down with the team at the customer business. The first thing they look at is the existing processes, how things are done currently. That allows Rusada’s team on the ground to understand how the business currently works, what it needs to do and then convert that into how to achieve it within ENVISION, yes, but hopefully with some improvements to the original process.
That then follows into the training of personnel which goes hand-in-hand with the data import process. Initially, Rusada tries to combine those two stages so that the users are being trained but alongside that, the project is getting deep into the data and how to get the data from a legacy system into the new system. That can quite often be a painful process if there is no means to take data electronically or, for example, there’s a lot of work to be done to that data. Quite a lot of Chrono’s data needed to be cleaned and/or adjusted. So, that process quite often has to be done during the implementation which can mean that the process takes a little longer. However, the teams know by then that the data being put into the new system is good which is the most important thing; the last thing that anybody wants is to take data that isn’t correct from a legacy system or have to fix up any potential issues with it. As part of that process, ENVISION will help with that but there’s only a certain amount that it can do so there is sometimes the need for some manual intervention which was what had to happen on the implementation at Chrono; to make sure that the data was as perfect as it could be before importing it into the system.
Following the data input process, the project moves into the preparation for Go Live phase with multiple phases of UAT (User Acceptance Testing) before the final Go Live and any refresh training that’s required.
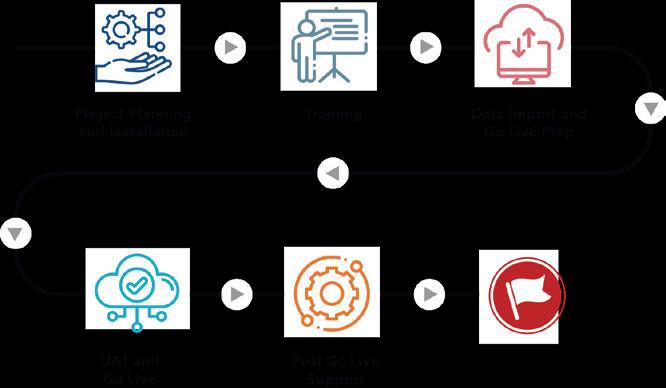
That’s Rusada’s standard approach to an implementation and was the approach used for the Chrono case. However, COVID-19 hit and that was a challenge as many readers will know who were engaged with projects or even just running their business during that time. The project in this case started in 2019 and quite quickly, after a few on-site meetings and progress with training sessions, everything had to go fully online. Rusada had to adjust in order to deal with that; it was something that they weren’t used to as a vendor which had always tried to do as much as possible on site but that was simply not possible.
It caused some problems but the implementation team managed to get around them and companywide, having to take a step back and look at how implementations are done completely remotely now, was a learning curve. It was actually quite positive because, to bring us back to the present day, although Rusada still does go on site to do implementations and it’s important to do that, there is an element that can still be conducted from off site that might not have been so easily accepted before. For instance, if the team were called into a meeting that does not necessarily require face to face. By working remotely, a lot of time is saved and cost for the customer. When the vendor is on site doing an implementation, it can quite easily fill a day with meetings and the time between meetings as well as training sessions. By doing things a little more off site, times can be set, there is no travel time involved so that meeting or training can be achieved within a certain timescale. Also, if a refresher is needed, it can be done but it tends to be less than when the vendor is on site.
The transition was quite hard and fast, Rusada had to learn how to go from on-site implementations to 100 percent remote which all happened within the first few months of this Chrono project. It was necessary to utilize a number of different technologies and it allowed Rusada to expand on the existing technologies that they were using to offer more online training, as well as developing a full online document training site that any of their customers can access.
Challenges
COVID-19 aside, we’ll just look at some of the challenges that have been mentioned and the solutions to those.
Challenge 1 — Visibility across Operations
Chrono’s Operations had their own in-house planning software, including flight booking and maintenance tracking, but there was the need to bring those two together. Rather than changing everything at the same time and because people don’t like change, the decision was to go with an API (Application Programming Interface) to make that happen faster and make the software solutions talk to each other. That gave Chrono the possibility to interface ENVISION with the existing platform. Once that has been done, the system allowed users to group tasks efficiently, to do work orders between flights; Chrono does charter not scheduled flights. As soon as maintenance is booked, Sales can be aware that there is maintenance booked for the aircraft in question.
This (figure 2) is what is in ENVISION for work package creation and tasks on the calendar.
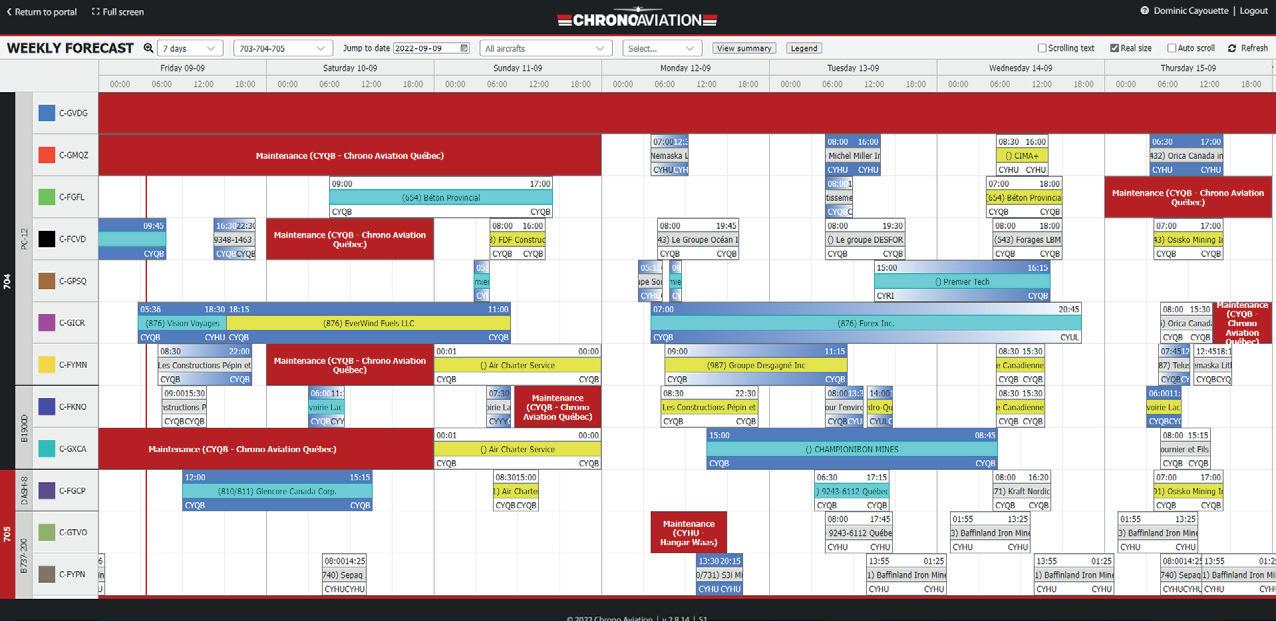
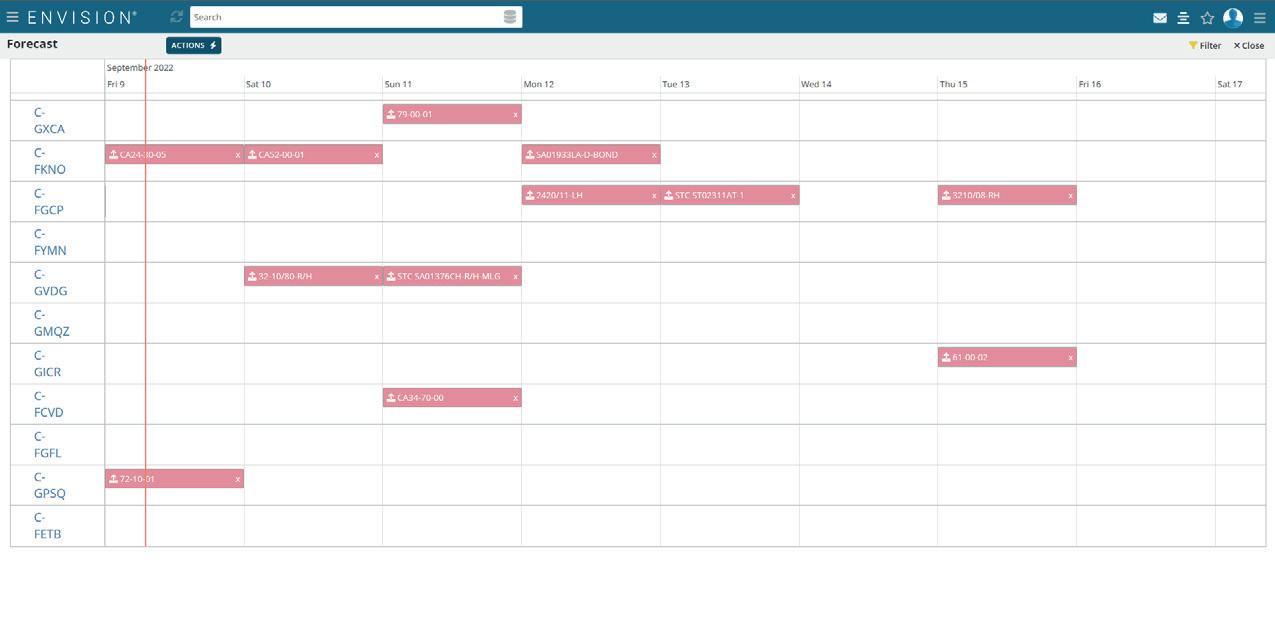
CHALLENGE 1 - Visibility Across Operations
Figure 2
Figure 2 is from ENVISION and shows the forecast of maintenance events coming due. In this initial challenge, Chrono didn’t want to move away from the existing Ops system that they have so ENVISION has a really flexible capability for APIs. Moving on (figure 3) we can see Chrono’s existing legacy system which has been combined with the maintenance inputs.
CHALLENGE 1 - Visibility Across Operations
With this, Chrono was starting to enjoy a more unified platform but what you see in figure 3 is the old system and some inputs from ENVISION. This combines the maintenance requirements when an aircraft is due into maintenance or has been planned into maintenance alongside the flying schedule — the charters. This can all be achieved in one system if you’re using ENVISION for monitoring flight operations and maintenance. In this case, two solutions have been combined into one platform with the aid of an API (Application Programming Interface).
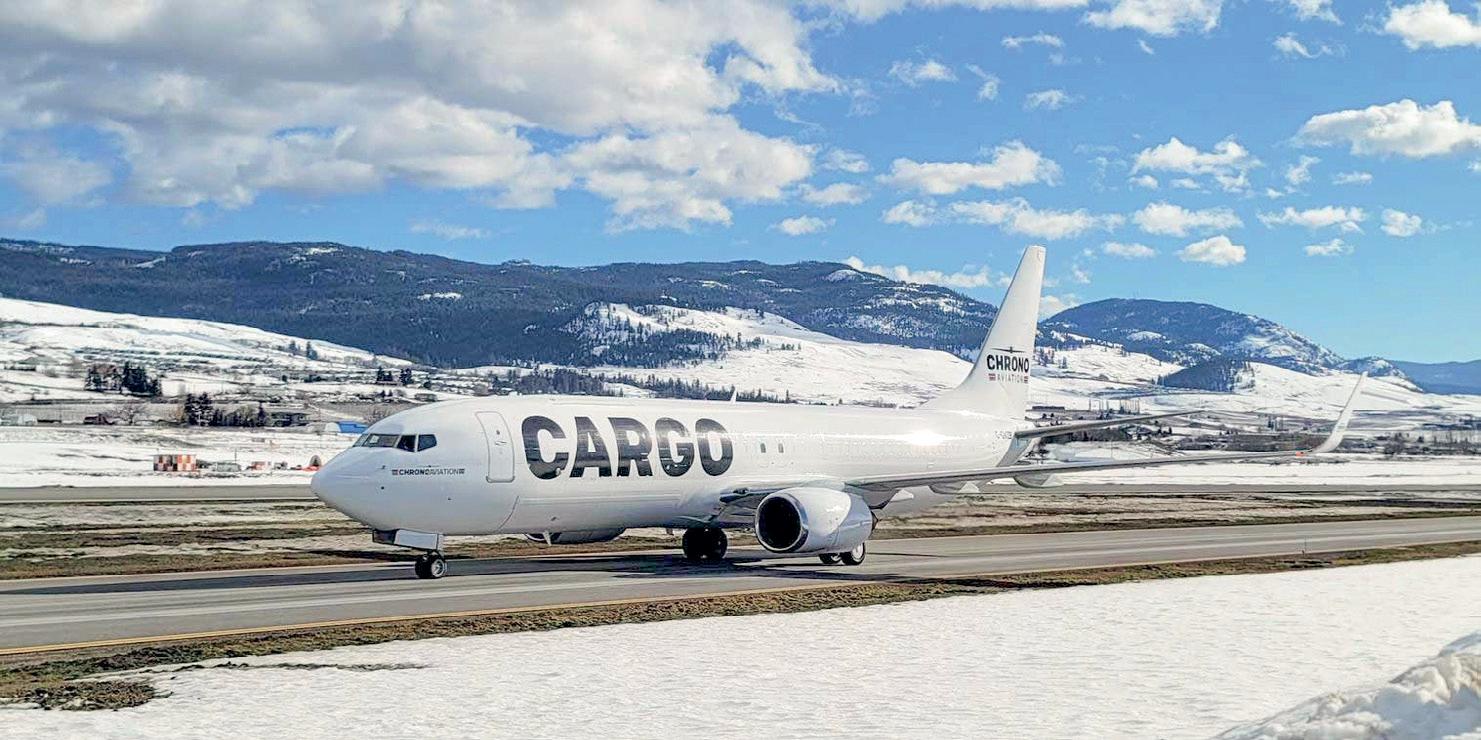
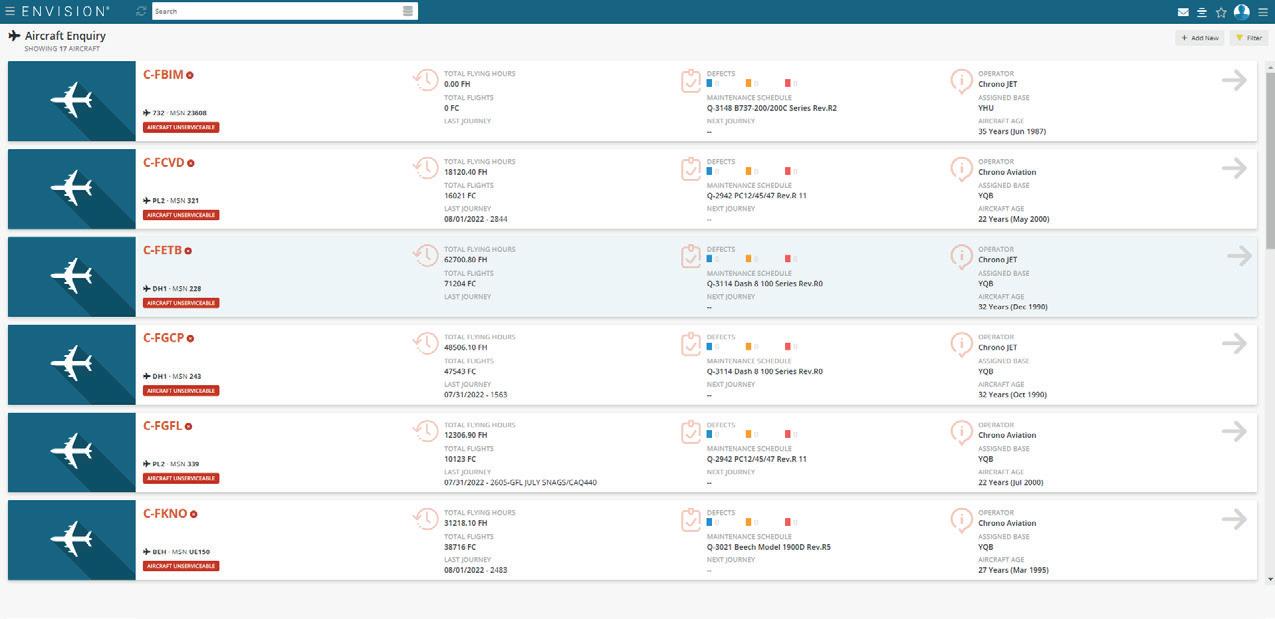
Challenge 2 — Controlling Regulatory Compliance
With larger aircraft joining the fleet, Chrono had more complexity and more things to track. ENVISION was able to offer Chrono a way to do what was needed and, for a precise example, on the maintenance side, it can be seen that the operator is now more in control of incoming maintenance. Additionally, there is a great dashboard to be able to quickly see the status of each aircraft (figure 4).
CHALLENGE 2 - Controlling Regulatory Compliance high-level summary of the fleet including that red status for ‘Aircraft unserviceable’. That ENVISION capability can be configured with a rule set that each business can define, according to what they deem as being unserviceable, for the system. So that might be that, if there are any open defects or if there are any overdue maintenance events, flag the aircraft as unserviceable. Or the airline or MRO might say that if there’s a deferred defect coming due today, then classify the aircraft as unserviceable. It’s entirely up to the customer as to how that is defined. This is part of the flexibility that customers using ENVISION have within the system for defining those rule sets and that definition process is part of the implementation. This page also gives a summary of flying hours, cycles and the three-color coded red, orange and blue boxes signal a summary of defects, are there any open defects? (there shouldn’t be but sometimes it happens), are there any deferred defects? and are there any overdue defects? one is a complex example, each of the links also allows users to assign rule sets so that the workflow of maintenance inputs really can be tailor-made. The user can say that only certain employees or team members can change the status or, in a purchase order example, only people in a particular team can approve up to this value with anything above that value needing a second level of approval or even a third level. This is a really powerful tool that isn’t only for tracking maintenance but is available throughout the whole of the system too, although it’s an ‘out of the box’ solution, you are still able to tailor and adapt the processes in the solution to match the processes of the business using it.
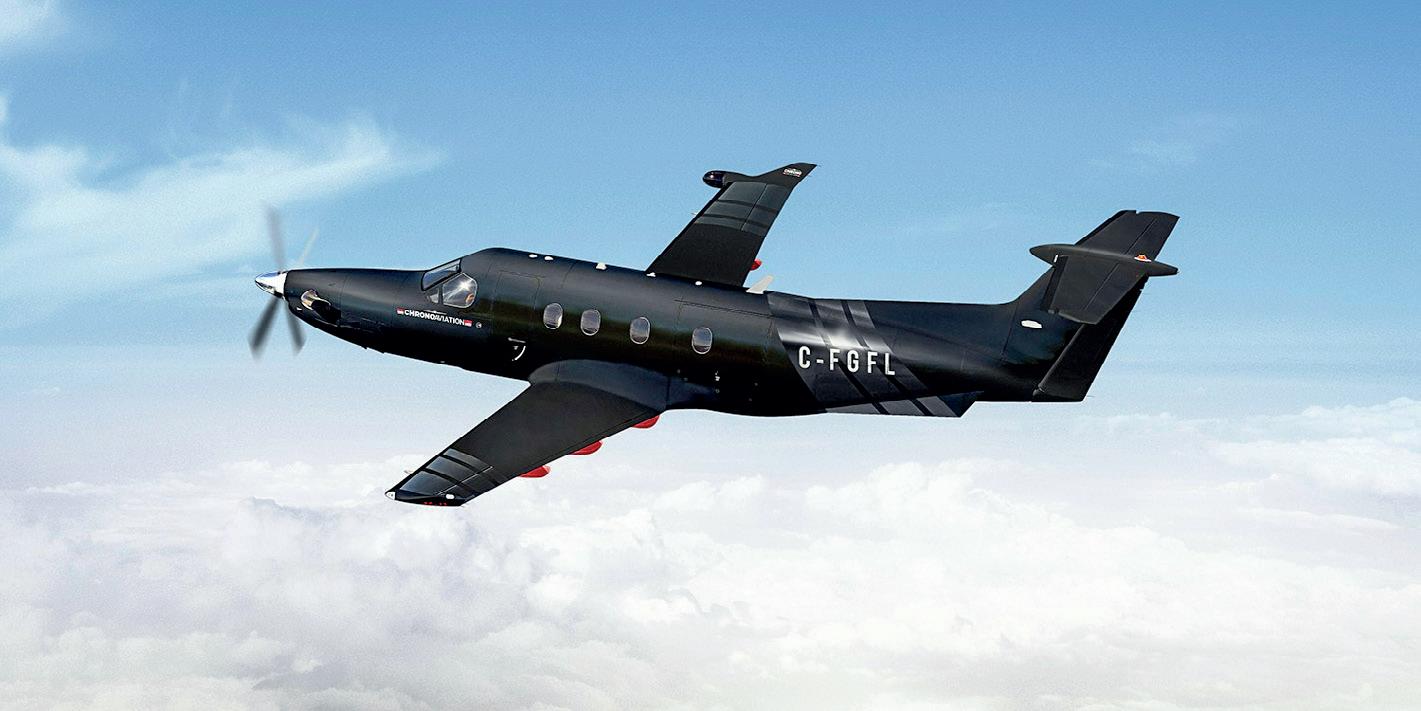
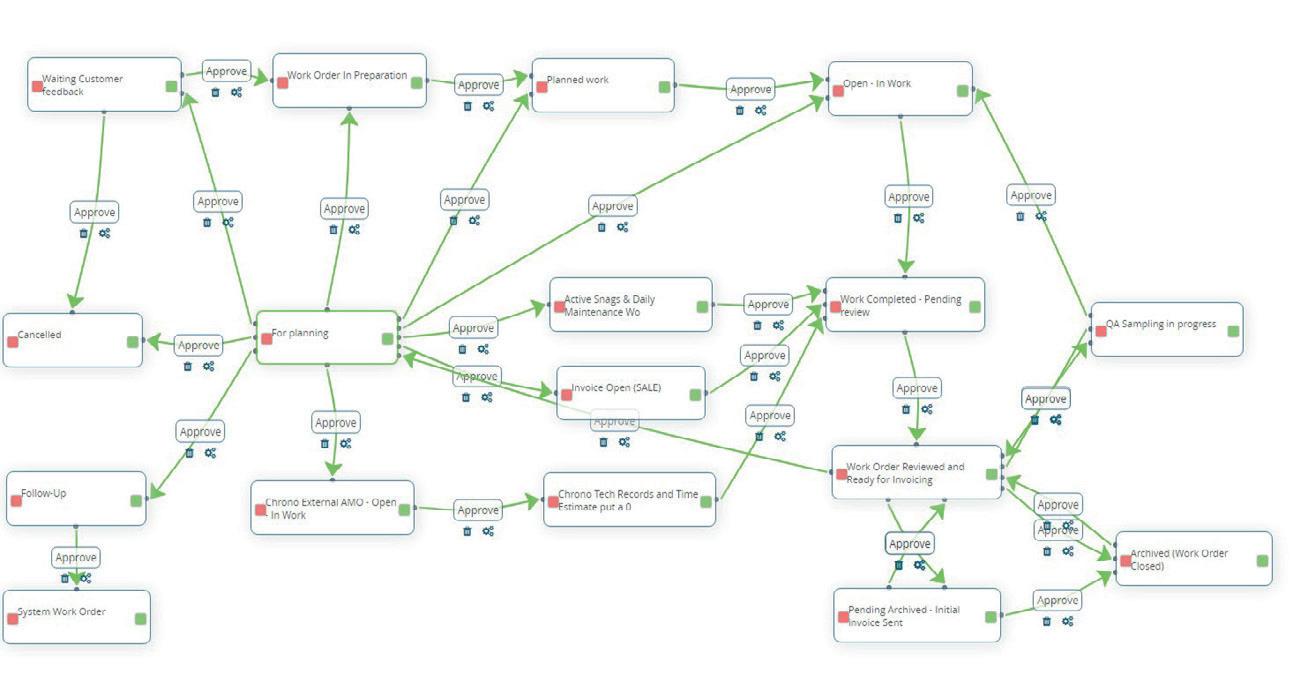
In addition to the order workflow, Chrono and WAAS can do a dashboard (figure 6) making it easy to categorize everything that every individual needs to do.
CHALLENGE 3 - Tracking of Maintenance Progress
Challenge 3 — Tracking of Maintenance Progress
Tracking a work order (figure 5) was important for WAAS who deal with several different customers. Knowing what is where has been achieved with a fully customizable workflow.
CHALLENGE 3 - Tracking of Maintenance Progress
Each dashboard is different because it’s fully customizable so, the way the dashboard is seen for planning won’t look the same as the dashboard seen for QA (Quality Assurance). The benefit of that is that, as a business, users can define mandatory dashboards, i.e., ‘anyone with this job role has this dashboard.’ That way, the business knows that everyone is getting the information that the business wants them to have, as soon as they log-in to the system. Alternatively, it can be left open-ended for users to design their own dashboard have their own charts, it can link into Power BI, they can have their own custom dashboards
WAAS was able to make that fit with the daily operation, not just an open and close work order but something ENVISION offers users is that it’s fully customizable for what Chrono and WAAS needed. Although it looks complex, for WAAS it enables them to know what is where and to effectively map out the workflow for, in this example, a maintenance input, but it could be any workflow. It could be a purchase order approval, annual leave approval… the system allows users to map how a work order moves through a workflow and, although this exactly as they want them. This screen is there to draw the eye to what has to be done including color coding alerts that can be set. If the user goes in and everything is green, they’ll be happy: if everything is red, then maybe there is some work to do that day.
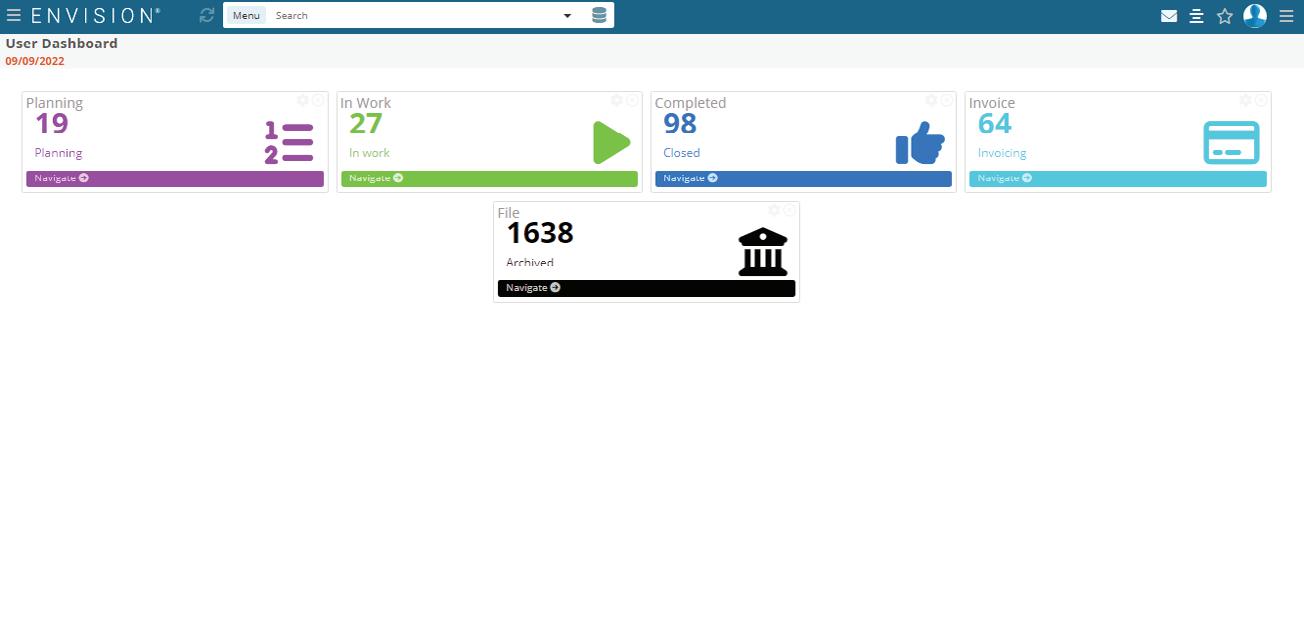
Challenge 4 — Management of Inventory
From the part number control list to the automatic inventory reservation and acquisition, ENVISION has offered Chrono and WAAS a huge step forward. Let’s look at an example that covers a big gap that WAAS had (figure 7).
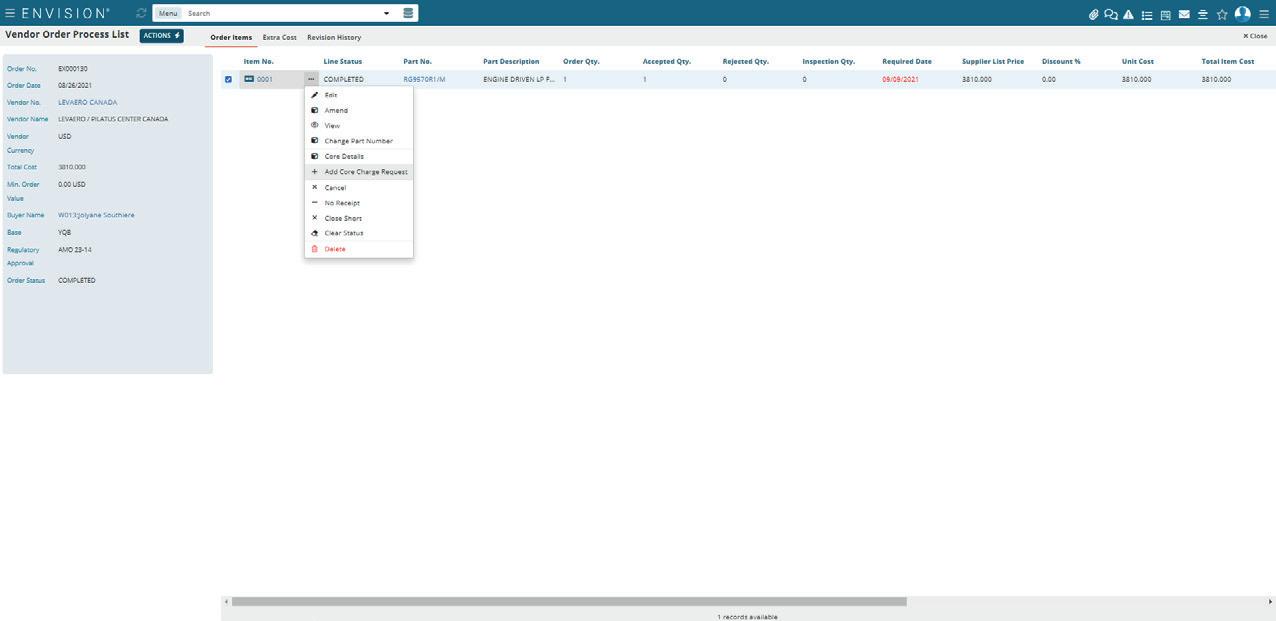
CHALLENGE 4 - Management of Inventory
In smaller operators, there are a lot of exchanges — buy the parts, receive them, return the unserviceable cores, and get the invoices a month later for example. In the past, WAAS was doing all the back billing and administration manually but now, there is the ability to go back to the original order and re-do the billing from there. In the figure is a vendor order which allows users to check fees charged against costs incurred.
Other Benefits
To finish up, let’s just look at a couple of other benefits that Chrono and WAAS gained when switching over to a modern system.
Improved data collection: data collection was not really done at Chrono and WAAS prior to the arrival of ENVISION but its availability now has been very helpful in the past year, especially in financial affairs with better reporting on costs and profit. The goal is that, by 2025, pretty much everything will pass through ENVISION in order to ensure good visibility and traceability. That will make possible some proper KPIs with the right tool with which to run the business. Many reports can also be done from all the information that ENVISION unlocks: it’s a super tool to present any kind of data which is a great improvement for Chrono and WAAS.
Modified work flows: Chrono and WAAS have some specific needs, so the fact that they don’t fit any standard mold means that ENVISION helped them to adapt and define the real work flows that fit the needs of the business.
Going paperless: a hot topic today and the aim of most businesses in aviation is also the aim for Chrono and WAAS with the support of the regulator. Paperless is more efficient and better for the environment, especially trees, when compared with people printing a task card and scanning it back into the system. Chrono and WAAS are pulling together the requirements for things like electronic signature and other features that need to be secure. It’s just a matter of time and getting the approval from Transport Canada.
In the near future, many readers will be facing similar decisions to that faced by Chrono and WAAS so we hope that sharing the experience of this case will help with those decisions.
Dominic Cayouette
Dominic started in aerospace 2007 and became a licenced Avionics technician in 2012. He started his career at Aeropro where he was an apprentice avionics technician for five years, and later joined Discovery Air Techncial Serivces where he specialized in aircraft avionics modifications. He joined WAAS in 2015 and helped grow the company from inception to 100 employees today.
Peter Mortimer
Peter Mortimer is an Executive VP at aviation software provider Rusada. He has been working on aviation projects for the past 15 years having begun his career at Hawker Beechcraft. In 2015 he moved to Rusada, managing implementation projects before moving to Client Services Manager for the Middle East. From there he transitioned into a Sales role for the company, and now works with existing and prospective customers in the Americas and APAC.
Chrono Aviation
Chrono Aviation Inc., and its wholly owned subsidiary Chrono Jet Inc., is a charter airline headquartered in Québec. It operates aircraft in passenger (9 to 120), cargo and combi roles from its three main bases in Canada. There are more than 265 employees in the business with a fleet of 15 aircraft including Boeing 737-200 and -800, Beechcraft 1900, De Havilland Canada Dash 8 and Pilatus PC-12.
Rusada
Rusada is a leading provider of aviation software with over 35 years of experience in the industry. Its ENVISION software manages over 2,000 fixed and rotary wing aircraft for 150 operators, maintainers, and manufacturers in 45+ countries. With its headquarters in Switzerland and offices in the USA, Canada, UK, UAE, India, Singapore, and Australia, Rusada provides global support for a global industry.
Patrick is the CEO and leading network and data integration specialist at IAS. He has worked mainly in airlines and financial institutions over a long career in the IT industry. Patrick holds a bachelor’s in electronic engineering from Dundalk Institute of Technology in Louth, Ireland.
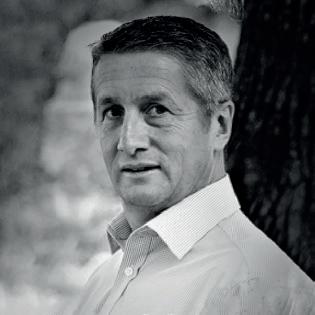
Aircraft IT: Your name, your job title, and the name of the business
Patrick Clancy: Patrick Clancy, CEO, Integrated Aviation Systems
Aircraft IT: How did REDiFly get started?
PC: REDiFly is the brand name of the software products created by Integrated Aviation Systems (IAS). IAS is the project of our late Managing Director and aviation guru Ari Vihersaari who sadly passed away in July 2021. Ari had a vision for the creation of a streamlined modular and configurable Aircraft Electronic Technical Logbook that would replace the paper-based Aircraft Technical Log (ATL) in commercial and business air operators. We continue to implement his vision. Our core product the REDiFly eTechlog brings to life the previously static data from the paper logbooks thus creating real-time visibility of airworthiness for CAMOs, Fleet Managers, MROs and Maintenance Controllers.
Aircraft IT: What is the guiding business principle that drives REDiFly?
PC: We at REDiFly have always said that we are software experts in the aviation industry rather than the other way around. Our guiding principle has always been to deliver a highly customizable application by keeping the end-user at the center of our design process. We aim to establish and nurture relationships by providing a service to our clients alongside a solution that suits them.
Aircraft IT: What has REDiFly’s greatest business achievement been to date, and why?
PC: I have to say getting our initial customer over the line was a great achievement for us as a start-up company. Industriflyg Stockholm has been with us throughout the pandemic, and we have built a very strong relationship there. We are proud to call them a customer.
Aircraft IT: What have been your disappointments and what have you learned from them?
PC: We are very excited about the world of aviation software and the potential we can reach with digital data. We have thought about this from the very start. I have been working in the field of electronic logbooks since 2010 and have always been interested in the possibilities of a data-driven industry. However, we have had to be quite patient. As we all know, aviation can move quite slowly when it comes to change. From what we have seen in the market, operators are much more comfortable starting small and establishing trust with software vendors before committing to a solution. We have found that a flexible system which integrates with current processes, yet is scalable to future needs, can offer a much easier step to take. This is particularly true for an eTechlog application as it touches many areas of an Air Operator’s business.
Aircraft IT: In a sentence, how would you summarize what REDiFly does for aircraft operations customers?
PC: At REDiFly we add value and increased efficiency to our customers’ daily operations through the delivery of real-time data for CAMO, Maintenance and Planning. Our accurate digital data delivery and integrations enhance or replace existing workflows leading to company-wide visibility of fleet status.
Aircraft IT: What do you feel will be the next big thing in MRO Aviation IT?
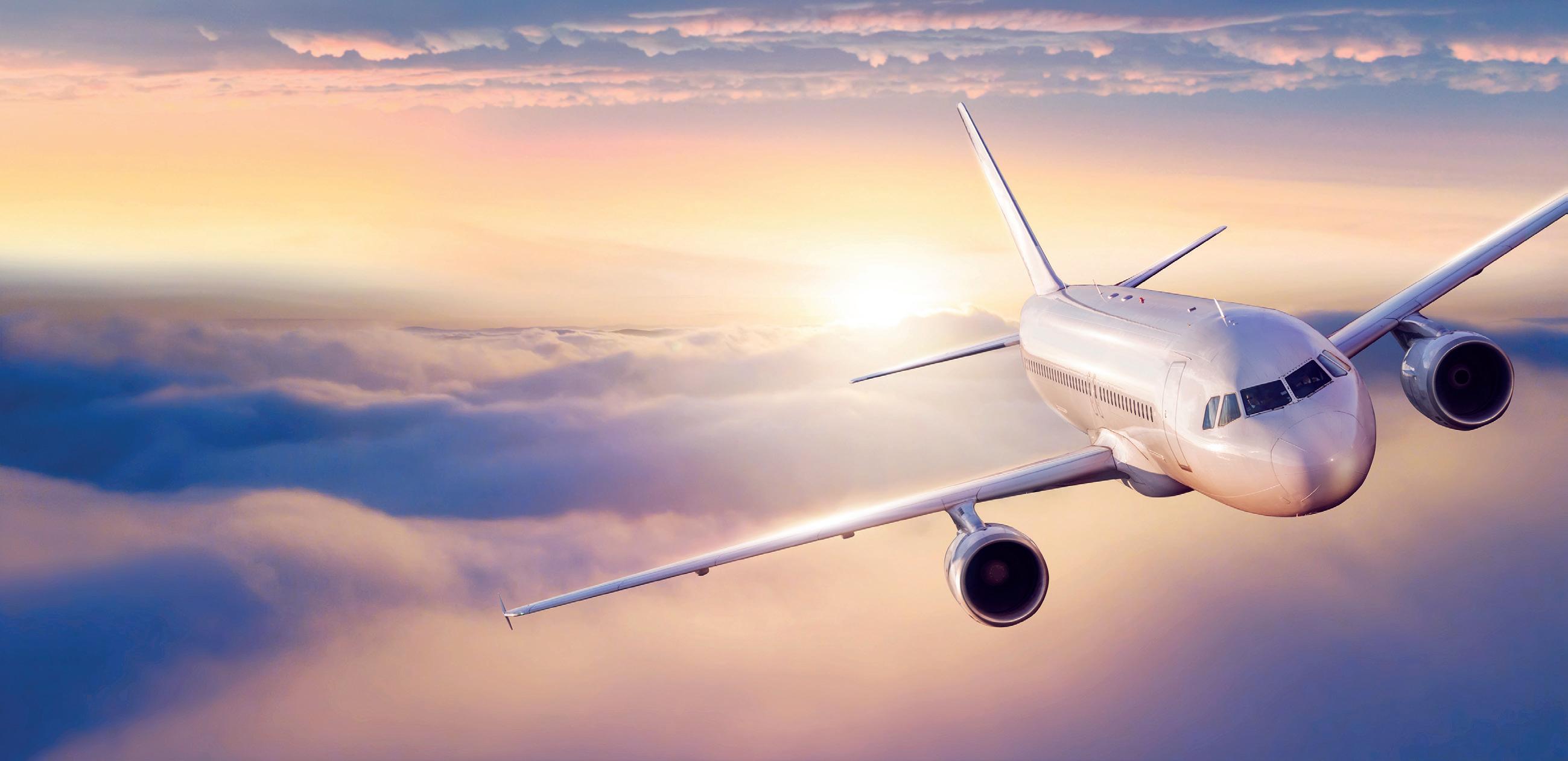
PC: There are many developments in Aviation IT such as Blockchain, AI (Artificial Intelligence) and Predictive Analytics, all of which we are interested in. However, for the small to medium operators, these concepts may still be a while down the road. I think the next ‘big’ thing in Aviation IT will be for digital aviation vendors like ourselves to break down the barriers of competition and communicate effectively with each other, to provide a more informative and accessible landscape for the operators that we cater for. There are many companies out there providing value to different areas of aviation through their software. If we can create communities in which to share our individual services, we can begin to offer our end users a more complete and consistent solution.
Aircraft IT: What do you want your customers to say about REDiFly?
PC: We would like our customers to say, “Why didn’t we have this before?... REDiFly has enhanced our daily operations by being adaptable to specific