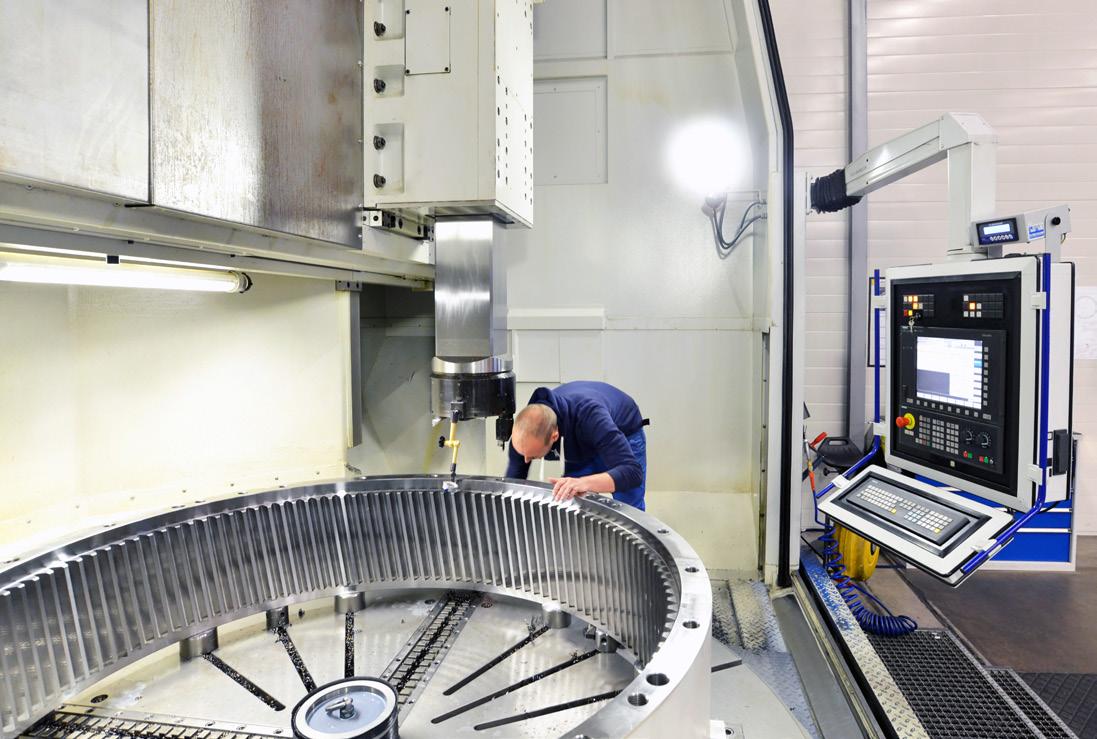
2 minute read
Understanding seals: Pushing the boundaries of gearbox performance
Gearbox trends
The most significant gearbox trend in recent years is increased power density. Gearboxes must output more power without increasing in size, placing components under higher loads and stress. This increases wear potential and shortens lubricant lifetime.
Dynamic demands
Given the fundamental importance of gearbox seal integrity, OEM lubricant specifications include dynamic seal compatibility. OEM testing has undergone a revolution in complexity and challenge in order to keep pace with real world requirements.
Flender test:
Long considered by OEMs to be a core requirement, the Flender test is carried out using radial shaft seals set on a spinning shaft that is half-submerged in lubricant at a fixed temperature, for a specified time.
To meet growing productivity demands, gearboxes are operated for longer periods, even continuously. Having little or no downtime increases the thermal stress on both gearbox and lubricant while the financial penalties for a breakdown climb ever higher.
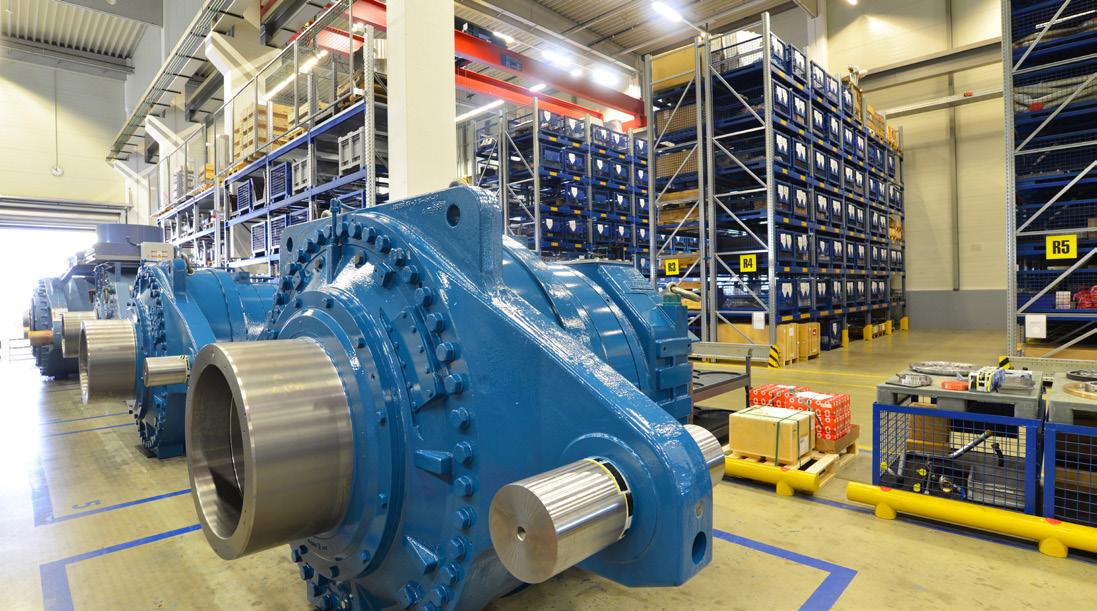
Gearboxes are running harder and faster than ever, on thinner fluids, yet must remain reliable. Lubricants that can deliver the right balance of performance are essential.
After the test the seal is visually examined, the shaft wear tracks measured and any lubricant leakage documented. For NBR seals, the test is shorter and done at a lower temperature. Flender is more challenging for FKM seals, likely due to wetting issues; if the oil does not reach the shaft surface where it meets the seal, wear becomes a problem.
SEW test:
As OEMs pay particular attention to equipment lifespan and lubricant performance, more stringent testing has appeared – most notably from SEW – that closely reflects conditions experienced by gearboxes in the field. SEW specialises in gearboxes for applications such as materials handling, roller shutter doors and airport conveyor systems. These must deliver rapid start-stop motion, both forwards and in reverse.
Reflecting these different conditions, the SEW dynamic seals test lasts twice as long as the Flender method for FKM seals, and nearly 3 times as long for NBR seals. Shaft rotation includes forward and backward motion at constantly changing speeds. These conditions are particularly challenging for NBR seals.
Passing dynamic seal compatibility tests is a top priority: should a seal fail, the volume of lubricant (and the protection it affords) can fall below ideal levels. Oil will also leak from the gearbox and into the local environment, which is highly undesirable. When lubricants can pass this stringent seals test, any failures that do still occur are more likely due to manufacturing issues or poor set up.
© 2023. Afton Chemical Corporation is a wholly owned subsidiary of NewMarket Corporation (NYSE:NEU). 01/23. The information in this bulletin is, to our best knowledge, sure and accurate, but all recommendations or suggestions are made without guarantee since the conditions of use are beyond our control. Afton Chemical Corporation and its affiliates disclaim any liability incurred in connection with the use of these data or suggestions. Furthermore, nothing contained herein shall be construed as a recommendation to use any product in conflict with existing patents covering any material or its use.