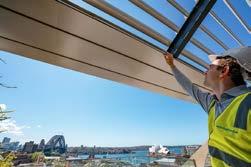
6 minute read
Boosting confidence in safety-critical products
BOOSTING CONFIDENCE IN
SAFETY-CRITICAL PRODUCTS
A focus on compliance instead of safety puts people and properties at risk. Despite the safety-critical nature of fire protection systems in the built environment, they are afforded no more guidance in Australian building legislation than areas such as weatherproofing or acoustics. For Australia to build a safer future, passive fire construction products and materials must face increased scrutiny to ensure they perform safely and effectively in the event of a fire.
1. For Australia to build a safer future, passive fire construction products and materials must face increased scrutiny.
2. Product certification provides traceability for future risk assessments and maintenance.
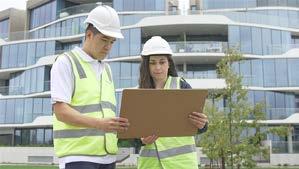
3. Certification ensures that correctly installed fire protection products and systems will perform.
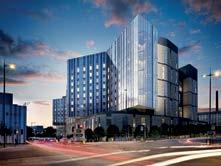
1 2 3
CHAD McLEAN
Warringtonfire
The impact of fires on both residential and commercial property over recent years has put fire safety back on the agenda. At its heart sits the integrity of building materials and components, and central to this is appropriate product testing, assessment and certification.
A brief history
Legislation is used the world over to impose increasingly stringent requirements on specific products to ensure they are fit for purpose. Passive fire product certification is one of the world’s most prevalent certification fields, and it dates back to the early 20th century when standards for fire doors were developed in the US. Testing of fire wall systems commenced in 1913, leading to testing in a furnace—a process that is used around the world to this day.
Current legislation in Australia calls for a single fire resistance test for building components, including passive fire protection products, but there is no requirement for recurring testing. This is because certification is not a mandated pathway. As such, a single successful test of just one product sample enables the manufacturer to sell that product indefinitely, based on the original performance, without declaring any changes.
In some cases, components may be manufactured based on testing conducted many years prior, raising questions about quality. While this is not guaranteed to cause issues, changes may affect the performance of the end product. Even without intentional alterations within manufacturing, changes in equipment, staff and raw materials could all have effects over time, and there is no way to quantify this gap without a more robust system in place. Therefore, certification is an ideal way to provide confidence in product quality and performance.
Is certification the answer?
Certification demonstrates that a product or system has undergone the relevant fire testing and the manufacturing process has been audited to assess the reliability of the quality procedures and traceability of the product. For manufacturers, this demonstrates that the product for sale is the same as tested. It also provides added assurance to the building industry that passive fire products and systems certified under the scheme comply.
Robust testing of all products incorporated in the construction of a building will help to ensure it remains fit for purpose. Third party certification brings additional benefits. Firstly, it is ideal for manufacturers seeking a competitive edge because it allows them to differentiate their products and processes from non-certified equivalents. Secondly, certification provides reassurance to the end user of ongoing reliability and traceability and builds confidence. And finally, for architects, specifiers, contractors and building owners, certification provides the reassurance that fire protection products and systems, correctly installed, will perform as required.
Alongside consistent quality, product certification also provides
traceability for future risk assessments and maintenance. Some schemes require products to meet established test performance criteria, as well as ongoing production manufacture audits. Independent certification schemes, such as the Warringtonfire ‘Certifire’ scheme, provide the regulator, specifier, customer and end user with confidence in the stated performance of a product and offer them an informed choice when selecting and purchasing it.
The process
To achieve product certification, regular auditing of the production process is required. In doing so, any changes to the quality and performance of the product based on these fluctuating factors can be identified.
In general, prescriptive standards or codes satisfy the requirements of regulators or approval bodies. However, these standards do not explicitly address concerns such as safety of life or the integrity of a structure through its lifetime. With the adoption of a less conventional engineering approach in modern designs, the more fundamental fire safety designs face an even greater challenge.
It is critical that fire protection products perform as intended, and product certification dramatically reduces risk and avoids costly mistakes further down the line. While it may not currently be a requirement in all regions and territories, there is an increasing trend globally towards specifying third party-certified products, so it represents a sound investment for businesses to future proof their products by certifying them now.
Introducing certification
To support the need for change in Australia, the Building Confidence report (BCR), published in April 2018, made 24 recommendations to building ministers to address systemic issues in the building industry. Recommendation 21 states: “The Building Ministers’ Forum agrees its position on the establishment of a compulsory product certification system for high-risk building products.”
The term ‘high-risk’ should refer to any product installed to restrict the spread of fire from one space to another. This includes separating elements such as wall/floor systems, doors, wall and ceiling linings, fire collars, sealant, structural steel protection, hardware and so on.
Some state and territory governments have agreed to consider the implementation of all BCRendorsed responses. As such, it is anticipated that Australia’s building industry is likely to adopt stricter legislation and product certification requirements in the coming years. Many third-party product certification providers are already operating in Australia, so the sooner manufacturers and installers begin the process, the easier it will be to comply if and when new regulations are introduced.
In review
While testing is a critical step in a product’s development, building products require a robust method of ensuring ongoing quality and performance over time. This is where product certification comes to the fore. It can protect both reputations and lives by mandating best practice, something that is beneficial for stakeholders across the built environment. Moreover, there may well come a point when all products around the world require product certification, so now is the time to get one step ahead and ensure that products are high-quality, highperformance, compliant, traceable and—most of all—safe.

Each and every day, we deliver technically complex solutions in an increasingly complex world – to build the assurance that our clients and their end users need.
Warringtonfire offer a comprehensive range of fire safety engineering, independent fire testing, fire assessment and product certification services. Our unique ability to deliver a full suite of services provides confidence and certainty throughout the entire building cycle.
Although part of a global organisation, we take a local approach to each and every project. Our staff have an excellent reputation for integrity and providing the highest level of care and expertise on all our projects, regardless of size or location.
We have an established and extensive presence in Australia including at our NATA accredited laboratory in Melbourne and our offices in Sydney, Melbourne, Brisbane, Canberra and Perth.