
4 minute read
BENEFITS OF SINGLE-SOURCED MODULAR INSTALLATION
As science and technology advance and competition heats up, life sciences companies need their cleanroom facilities up and running quickly. There’s no time for error. Single-sourced modular cleanrooms offer many benefits over traditional building methods, reducing overall risks for the life science market.
1. FASTER TIME TO COMPLETION
Modular cleanroom installation can reduce time to completion by 20% to 40% because of parallel installation activities, according to AES historical data.
AES uses pre-engineered components and manufactures materials off-site, to the client’s specifications. It also uses a dedicated team that installs the system rapidly with snap-together components.
AES approaches cleanroom installation top-down. When the HVAC ductwork and MEP utilities are roughed in, the installation team installs the walkable ceiling. The crew uses that walkable ceiling to connect lights, sprinkler systems, HEPA filters and other finish work. While that’s happening, another team installs walls and components. The process happens simultaneously, not sequentially--another time-saver.
FaciliFlex™, AES’s fast-track HVAC and architectural design build modular cleanroom delivery program, has worked well for cell and gene therapy facilities. FaciliFlex™ provides rapid design and installation. “Because it’s an inclusive package, we are able to get into procurement and fabrication quickly and right into installation, Trista Hager, Vice President of Sales said, “You have a lot of overlap with a modular method compared to traditional plan and spec methods of building.” A biotech company in Santa Monica, California, chose AES for its new 5,000-square-foot cleanroom. The project moved from design to completion in only nine months.
2. LOWER COST
A single-sourced modular approach usually provides a lower total cost of ownership than stick-built installation. Facility costs don’t differ dramatically; however, when you compare costs over 10 years, you’ll see a different picture.
3. SUPERIOR, RELIABLE QUALITY
Single-sourced modular materials are manufactured in the same controlled conditions every time. Manufacturing cleanrooms in one place ensures repeatable, predictable results.
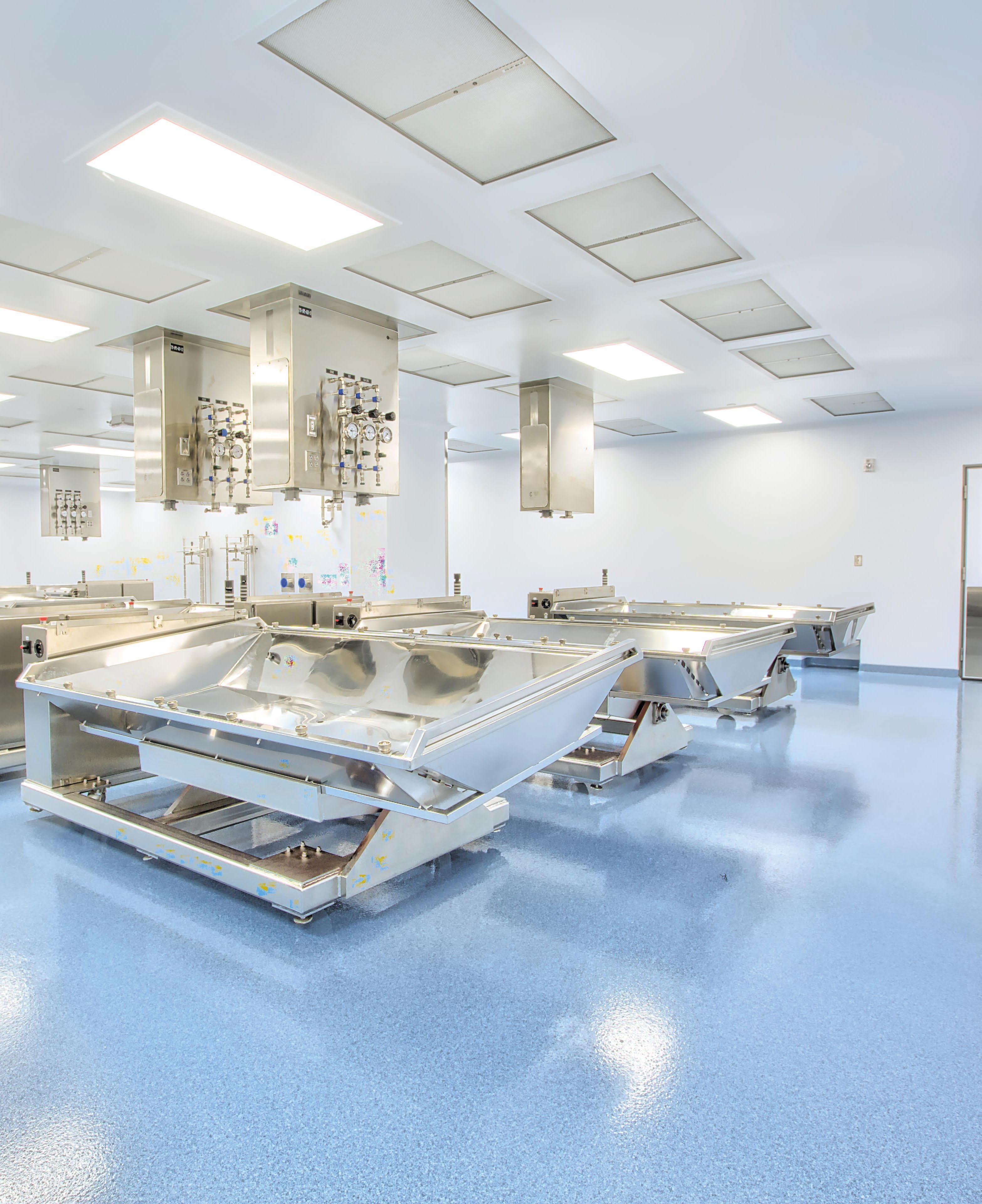
Single-sourced modular systems offer the following:
• Robust materials mean reduced maintenance, which means less downtime.
• A lower risk of microbial contamination means a facilities’ lifespan is longer with reduced risk to product and patients.
• A shorter time to completion, with no disruption to existing work, means more time to focus on drug development.
• Specialty installation teams ensure no costly mistakes.
• Integrated plenum return walls eliminate the need for a duct drop.
• Integrated electrical raceways eliminate the conduit drop.
“Many pharmaceutical products have to be processed aseptically,” said Patrick Poison, Executive Vice President of Technical Operations for United Therapeutics, a biotech company in Silver Spring, Maryland “You don’t have room for error. When the facility doesn’t perform as it should, the money you may have saved with substandard construction immediately goes out the door when you throw away that first batch.”
“There’s a better line of communication when you do have that single source,” said Brian Weed, Vice President of Partner Solutions at Controlled Contamination Services, which provides comprehensive controlled environment cleaning, decontamination and technical services for the life sciences and other industries. “We know it’s a better design and it passes certification quicker. I know all my HEPA filters are going to be the correct size. We know how the prefilters and HVAC are going to perform. Some traditional construction projects have either failed certification or our customers had to order new equipment because the room wasn’t designed correctly.”
The materials themselves also ensure quality. AES uses a 2-inch composite system with a uPVC-finished skin and a two-inch-thick honeycomb aluminum core. These materials don’t absorb moisture or humidity. PVC chemically welded seams bond panels together-there’s no caulk, which can deteriorate over time. “What we offer clients is a composite panel that’s easily cleanable,” Merrill explained. “A traditional stick built metal stud, gypsum drywall construction opens up a host of potential issues.” www.aesclean.com
4. FLEXIBILITY IN INSTALLATION AND SCOPE
Some life sciences companies may assume cleanrooms manufactured off-site wouldn’t accommodate unusual design needs, late changes and equipment changes. To the contrary: single-sourced modular cleanrooms can adapt to last-minute changes and a host building’s environment.
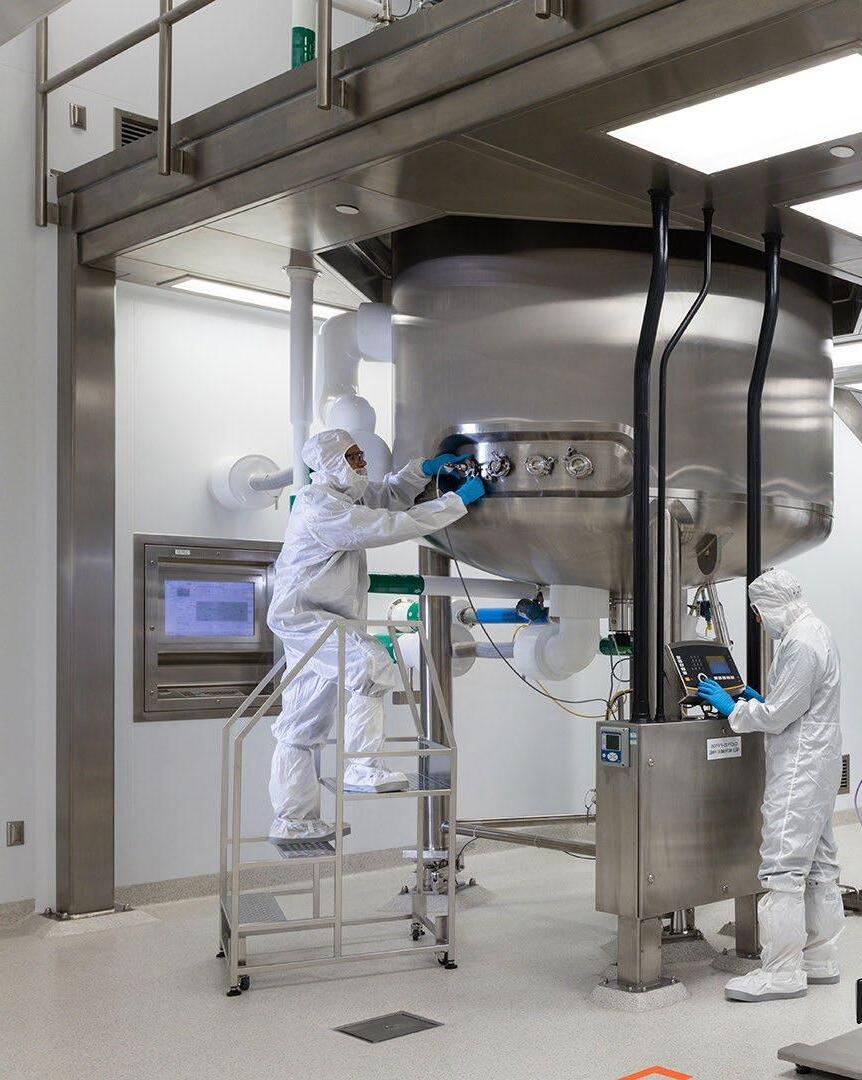
“With traditional cleanrooms, sometimes you’re trying to fit a square peg into a round hole “ Weed said. “You need to have good personnel flow, material flow and product flow for a properly designed contamination-control program. To change a traditional cleanroom, you may have to redo the HVAC, figure out where to place HEPA filters ... it can cost a lot more money to change a room designed 30 or 40 years ago.”
If a company has a unique building or facility design, a single sourced modular approach can adapt to that environment. “Because we’re in control of design, we would know up front if a client has a unique space,” Hager said. “Our project architects work through the programming requirements with our clients. We’ll talk with our installation team to ensure they can readily build what we need in the field. Then we alert our manufacturing plant that we will have an order coming with nonstandard pieces. Because we control the whole process, we can handle out-of-the-ordinary projects.”
5. DURABILITY OVER TIME
Cleanrooms have to withstand daily exposure to harsh sanitizing and decontaminating. Any crack or slight deterioration in materials is a place for mold-causing water or humidity to enter or for microbes to grow.
Modular systems tend to use more durable materials that withstand heavy-duty cleaning. “Some clients use Spor-Klenz, which is one of the harshest chemicals, to clean their walls,” Hager said. “The finish on our system resists Spor-Klenz. Traditional stick-built facilities require a special coating system to be able to resist those harsh chemicals. That coating has the potential for abnormalities, which necessitates recoating. That’s both costly and requires facility shut down.”
The AES PVC finishes stand up to the harshest chemicals over time. PVC liquid-welded joints and expert engineering provide seamless transitions between ceiling, walls and floors.
“The AES design of nice rounded corners and smooth surfaces is easy to clean,” Weed said. “That means you’re providing a nice surface not only for the chemical agent but also for the physical removal of it using our microfiber mop heads.”