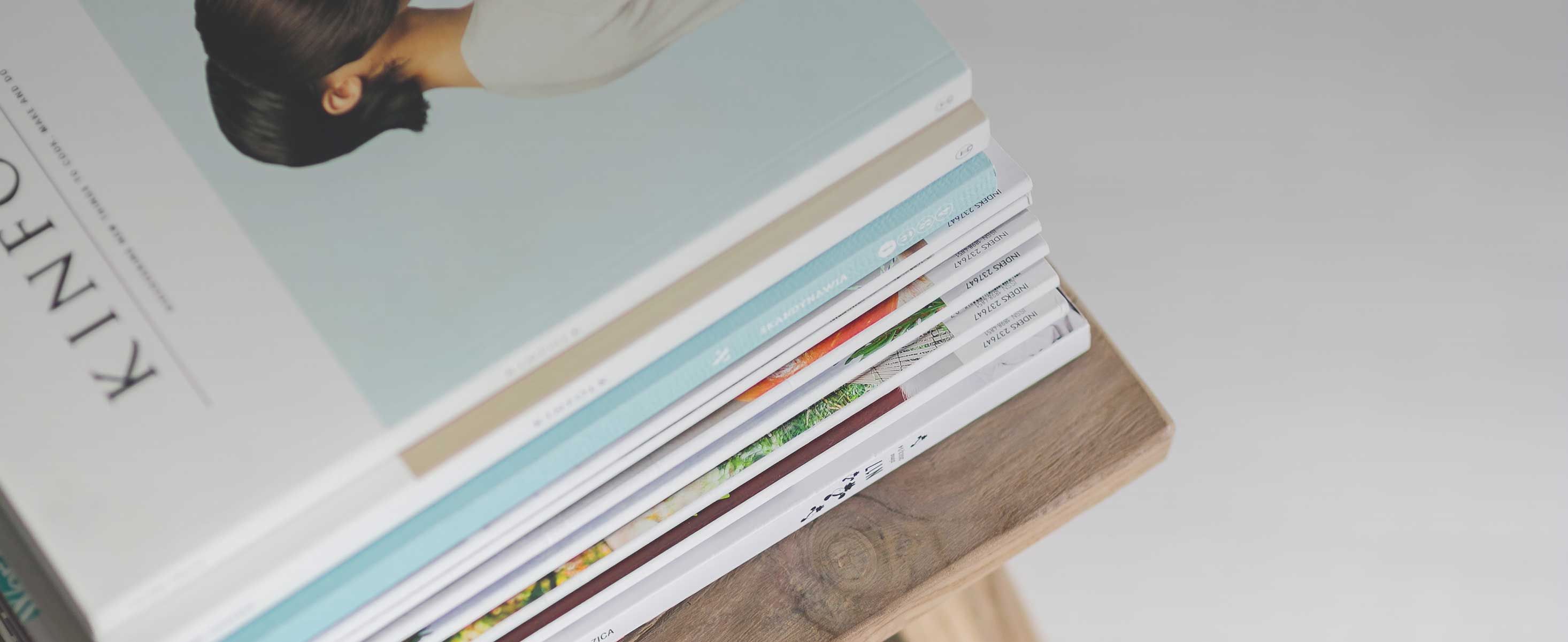
10 minute read
Operations at the L&J.G. Stickley Furniture Company
Introduction
L&J.G. Stickley is a furniture company established in 1900 by entrepreneur brothers Leopold and George Stickley. The firm is based in New York and has other shops in Connecticut. It deals in furniture fashioned from different timber types, but it has become synonymous with its flagship brand, the Mission oak furniture. The company has faced high and low moments, almost sinking into bankruptcy in 1974 (Clark & Thomas-Clark, 2002). It was salvaged when it was bought by new owners. The company has since grown and boasts of 1350 workers and five showrooms across the US. A record number of 120 distributors retail its products. Buy this excellently written paper or order a fresh one from acemyhomework.com
Advertisement
The production process used by Stickly Furniture
The Stickley Furniture Company employs a continuous processing model in the production of its various furniture components. This type of processing involves an uninterrupted series of activities that result in production of goods or services. In light of the definition appended to this aforementioned model of production, it suitably fits the one in adoption by Stickley. Various wood products are received into the workshop floor, where the quality of the boards is checked. The boards are prepared for a process of sawing to end up with various shapes and sizes of wood that will end up in finished products as oak furniture. The events that take place after that include knitting together of the wood such that there is no disconnect in all the work activities on the factory floor. Sawing is done by the workers, but the company also employs a computerized system where the boards are mapped out and cut by computer controlled saws. The pieces resulting from sawing are flexibly designed such that they all end up with a role in producing different furniture types. Some of the pieces are reserved in inventory to be used on special orders that will be fashioned as per the client requirements and custom preferences. To ensue from here is gluing of the pieces to form reinforced boards, which are later pressed to achieve compactness. Having achieved the desired shapes and sizes, these pieces are then smoothened by sanding; this is the first step in achieving aesthetic aspects of the furniture. Drilling of holes and mortising is guided by what is being formed out of each bit. Grooving is also done and is inspired by customer specification and creative designs of the skilled workers. Assembly is part of the final and most important work to be performed. From this assembly process, different products such as dressers, tables and cabinets are produced. Both skilled and unskilled workers aid in achieving this paramount job of fixing together the various pieces to come up with finely crafted furniture. The completed furniture is moved to a temporary inventory area for unfinished items, and from here the final polishing is done to attain superb pieces of artwork. It is observed that there is no break in the flow of work throughout the processes in the workshop; therefore, an affirmation that the continuous model of processing is employed. The rationale behind the Stickely management using continuous processing is for the reason that it saves time and resources. Because of the repetitiveness of work and consistency in the sequence of steps, workers are generally good at what they do. Efficiency is also achieved because there is a flow in steps of production. To a small but notable extent, batch processing is applied. During the non-peak season where production surpasses demand, furniture is stored as inventory. This stock is later used to cater for the excesses in demand during peak seasons (Blevins & Nixon, 2011).
Keeping track on job status and location
Stickely furniture is a busy organization and it is important to monitor the progress of work. It can be difficult to monitor each piece of furniture item on the workshop floor because of the large numbers involved. The management has a prudent way of keeping track of the status of each particular piece of job. Technology comes in handy as a micro management tool. Each and every stage of production at the factory floor has a special barcode assigned to it. When the boards are in the sawing stage, for example, a barcode is assigned to it. When the worker has worked on this piece, he removes the barcode and takes it to the scheduling office. In this office the code is scanned into the computer to reflect the position of the item in the production line.
Furniture in the inventory stores also has separate bar codes that show in the system that they are complete pieces. This helps the management to know the number of products in their stock at each instance.
The process of keeping tab on the stages of production helps in regulating production to ensure inventory is matched to the demand from customers. A level of stock will be aptly kept to ensure that the company does not have deficits when customer orders increase. Keeping track of job status also assists in performance evaluation. If an item is found to stay for an unusually long time at a particular stage, then proper evaluation can be done to find out the problem and provide remedy. Each of the workers has their work cut out, and the quality they add to the sets is their responsibility. When furniture leaves the workshop premises, their codes are swiped over barcode readers and checked out of the system as sales. Through this process, management keeps a record of what type of furniture are in stock, and which ones have left the shop. Keeping a database of inventory is useful in operations. For example, if from the inventory there are many tables and no dressers, then more staff and workstations are dedicated to making dressers and production of tables is slowed down. In isolated unique cases, however, inspection personnel check the operations at the various stages to ensure that defects are corrected.
Production scheduling for 40 mission oak dining room sets
An order of the magnitude of 40 mission oak dining room sets will warrant that the company does a thorough internal benchmarking to find out if the workshop can handle the order adequately. A key aspect before rushing to production would be to look into the finished items inventory to ascertain how many oak dinning sets are in stock. The deficit that the inventory will have not met will have to be assembled. It is important to find out which work stations will be dedicated to meeting these orders. The workers who will deliver this order will have to be identified based on their capabilities and skills they possess. The timeline within which the order will need to be made available will dictate the amount of machinery resources that will be dedicated to delivering the finished pieces. This is the essence of production scheduling (Lopez
& Roubellat, 2008). Proper planning should also be done to lay out all the procedures that will be performed, and in what order they will be performed. Having laid the framework plan for the work that will be involved; the plan has to be put into practice to achieve results (Scallan, 2003). Follow ups and monitoring will also have to be done to ensure that the work is following the plans that had been mapped out.
Once the oak boards are received from the lumber supplier, they are inspected to ensure that the quality will meet the standards required by the client. The boards will then be sent to the next section where computer managed saws will cut out the pieces that will be used as the upper part of the dining sets. The sizes of the top pieces that are produced are cut according to the size specifications that the customer has given. From there, workers glue together the boards which will later be pressed to achieve compactness of the pieces. Having achieved the desired shapes and sizes as dictated by the order details, these pieces are then smoothened by sanding. This is the preliminary step in achieving the fine aspects of the furniture that are customized to meet the customer expectations. Drilling of holes and mortising is done with guidance by the fact that these are dining sets. Grooving is also done as per customer specifications and creative designs of the skilled workers.
The oak wood pieces are then forwarded to the subsequent work station where they are assembled into complete sets. Prior to this, they have to be checked to ascertain that they are of high quality, and are the exact type ordered by clients. That makes sure the end product is also of impeccable features. Workers have the duty of assembling the pieces into fully finished dinning sets. This is done by the vastly skillful employees who determine the final products’ look and compliance with the client’s specifications. Throughout the processes, the sets are attached to bar codes to keep track of the job status and to aid in quality control and conformance to standards.
When the sets are completed, the bar codes are removed to record in the system that the items have undergone all the processes and are now complete pieces. This enables the shop to track the location of the items at all times.
The client whose 40 dinner sets have been duly completed is then informed in order to facilitate collection of the furniture from the shop. Before the furniture dining sets are dispatched to the owner, the owner must first perform an inspection to verify whether those are the items he ordered, and whether they meet his specifications. After affirming that the dining sets are in conformance with his specifications, the furniture can now be dispatched to the owner. The bar codes are removed from all the sets and entered into the computer to reflect that they have left the premises of the shop. With adequate information on the full customer requirements, capability of the equipment and workers to handle the order, Stickely furniture company can adequately deliver the 40 mission oak dining room sets.
Benefits and problems given the company’s production level policy
The company’s policy is heavily geared towards selling furniture that has already been completed and in the shop’s inventory. During the first quarter, demand for the furniture is usually low. Production at this time does not slow down, but a large number of the pieces produced during this time are stored under finished goods inventory. Other partially complete items are kept in the “white” inventory. During the other quarter when demand is high, the stock from the low season is used to cater for the deficits that would have occurred. If a client places a unique order, then the items in the white inventory are modified to fit their specifications. This policy of batch processing bears great advantages to the company because it increases the speed of service delivery to customers (Reklaitis, 1996). Orders can be met in time and this attracts a clientele of loyal customers and inevitably provokes them to refer new buyers to do business with the company. There is an achievement of consistency and balance in the workflow. During the off-peak times, workers and equipment are not left idle. On the other hand, the company does not face overstretch in capacity to handle consistency following orders during times when demand for furniture is at an all time high. There are setbacks to this mode of operation since the eventualities anticipated may not lead to the results expected. The company may stock excess inventory when demand is low, with the expectation that demand will rise. However, if this does not happen, the company's workshops will be left underutilized or even idle. Workers may need to be laid off when work is low, and this destabilizes the company. The partly complete inventory may present a problem if most of the pieces cannot be modified to fit client specifications. These situations expose the company to unprecedented losses. It is prudent for the firm to carry out extensive research to determine the market dynamics. Key focus should be directed towards meeting the present market needs, with attention also going to the expectations of the near future. Caution should be exercised when dealing with partially complete inventory. This cadre of stock should be limited because most customers tend to prefer standard furniture items rather than insisting on elaborate customization.
Changes that might be beneficial to the company
It is recommended that the company desists pegging overreliance on its flagship brand of mission oak wood furniture. It is prudent to delve into using other types of wood and do market research to find out which other products would be preferred by the new crop of clients. TQM approach should be applied to ensure that it is not only the quality of materials used that is given emphasis. Management should also ensure that a highly skilled and motivated labor force is used. Instead of storing excess inventory, the company should seek for more distributors to stock its products. Moving in pace with the changing technology will also be a step in the right direction. Computerizing most of the processes will ensure that there is consistency in the end products and efficiency in the work processes. Stickely furniture has employed continuous and batch modes of processing; however, the two should be used appropriately. Continuous processing should be used to meet orders in good timing, and batch processing should be used to cater for the needs that are expected in the future. There should be focus on meeting current needs efficiently, rather than concentrating too much on laying strategies to cater for the expected demand.
Conclusion
The continuous processing model employed in the production process in Stickely Furniture is fitting for the operations at Stickley since it ensures production of quality products, and products that are customized to customer's needs. The fact that the continuous processing model saves time and other resources is reason enough to make Stickley management continue using and enhancing this process. Employing technology, such as bar coding, for purposes of keeping track of processes and location of pieces is a positive move that has shielded the company from inefficiencies and maintaining an up to date inventory. There is need for Stickley to continue adopting technology in its process in order to keep abreast in the industry since technology is a great micro management tool. The company needs to make sure that it can deal with unexpected eventualities without halting its operations or disadvantaging its employees. It is advisable for the Stickley to research more on market dynamics in order to continue producing relevant products in an ever competitive furniture industry.