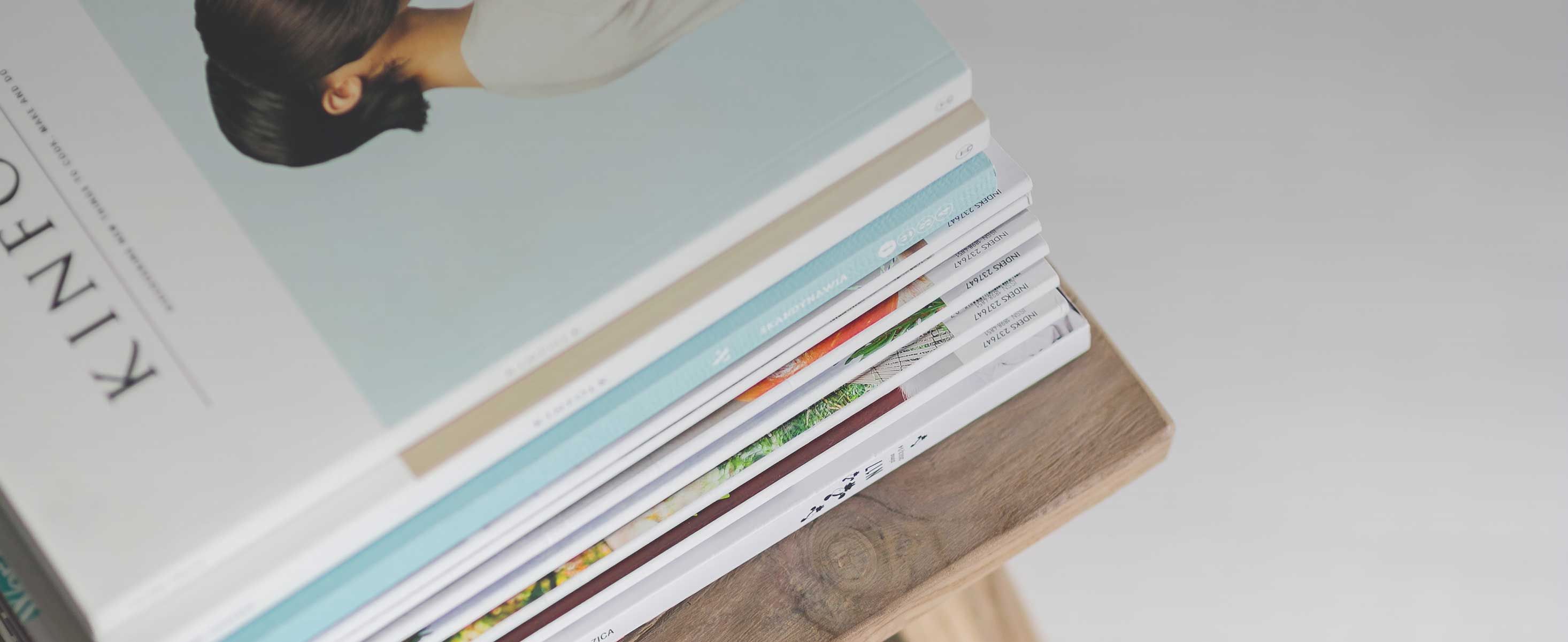
8 minute read
Project Management Paper
Circumstances
The BAE Automated Systems Inc. was responsible for setting up the baggage handling system in the Denver International Airport (DIA) during its construction in November 1989. United Airlines was the initial contractor that was to set up the baggage handling system. However, BAE automated Systems had a reputation for setting up the technology, and the firm had an enormous experience. The DIA's construction location was 25 miles from downtown Denver, Colorado, and according to Applegate et al., the DIA was the first significant airport construction in the United States for over a decade (1996). During the building, the project managers proposed that the airport include a baggage handling system integrated throughout the DIA. The proposed baggage handling system was to increase the airport’s efficiency in handling luggage by facilitating ground time efficiency, reducing the close-out time for hub operations, and reducing the manual baggage sorting and handling.
Advertisement
Buy this excellently written paper or order a fresh one from ace-myhomework.com
The latter was surprisingly time-consuming; thus, the baggage handling system's need to facilitate automated handling procedures. The DIA construction faced delays several times before its opening. The rising pressure from various stakeholders forced Denver, Wellington Webb, to hire Logplan, a German firm, to analyze the automated baggage system. The report from Logplan defined BAE Automated Systems as a highly advanced firm that would succeed in constructing the baggage handling system within the shortest duration. The DIA construction stemmed from the pressure that the Stapleton Airport had been experiencing due to the growing number of passengers and airplanes that demanded the expansion of airport facilities. Stapleton's capacity was limited since it only had four parallel runways, which could not accommodate the growing activities. The airport had also become prone to delays due to many businesses' flocking and could no longer allow for simultaneous airplane arrivals during lousy weather. The Stapleton Airport also lacked runway separation, and the taxiways’ layout caused severe delays during heavy traffic despite the current weather conditions. Due to such factors, the City and County of Denver decided that the airport required expansion or replacement. Cities and municipalities, including Denver, experienced a significant decline in the economy that facilitated the decision to begin a massive construction that would save the region’s economy—this followed after the collapse of mining, service support, and construction jobs.
The City of Denver hired the Greiner Inc. consulting team and the Morrison-Knudsen Engineers to offer their expertise regarding the master plan of transportation and construction. The group considered the site, master plan, environmental assessment, and developing support through educating the public on the economic benefits. The master plan did not indicate any challenges that may disrupt the construction process. The financing of the operations was to come from the issuance of revenue bonds and federal grants. Since the DIA program received its finances from various sources, its administrators balanced the administrative, political, and social considerations to facilitate the airport's construction. The project leaders included the City of Denver and the consultant team; this reduced the efficiency of operations since both parties had duplicating duties. Thus, the City of Denver assumed all the responsibilities of coordinating the resources.
Major Issues
The DIA construction faced several challenges that led to the delays in its opening that the City of Denver had scheduled for October 1993. The uncertainties of the airport opening reoccurred three times within seven months (Applegate et al. 1996). The DIA construction is related to various risks such as the massive project size scale, the extensive system complexity, and new technology. Since many residents benefitted from the system, the constructed faced threats, and there was a high degree of uncertainty due to technicality and project definition. The time allocated for the project was short. The German project assessment firm's report, Logplan, indicated that the project would face mechanical and electrical problems that would hinder a stable and reliable operation.
The DIA construction suffered from inadequate communication between the City of Denver and the BAE Automated Systems. Following the notification from Mayor Wellington Webb to BAE in August 1994, it is evident that there was hostility building up between the two parties. The message from Mayor Webb demanded that BAE faces a $12,000 penalty per day for failing to complete the baggage handling system by October 1993. The initial date that the City of Denver was to open the DIA. Also, Mayor Webb demanded BAE Automated Systems bear the $50 million cost for conventional tug-and-cart baggage system. Following the poor communication among the stakeholders, the President of BAE Automated Systems, Gene Di Fonso, thought of withdrawing from the contract when Mayor Webb sent the notification. Perhaps the delays in completing the baggage handling system's building resulted due to the level of complexity that the master plan stated. BAE Automated Systems had enormous experience in building smallscale baggage technology systems, and it seems the DIA's size must have overwhelmed the firm. The DIA construction project faced delays due to the prolonged periods of its assessment and the negotiations for its approval, and the selected financial plan. The issuance of revenue bonds required bond repayments to begin on January 1, 1994 (Applegate et al. 1996). Due to these factors, the project management team (PMT) had to push the project ahead. One of the DIA’s officials also noted that the PMT had not defined the construction processes in separate stages to make the work easier. The project was complex and required different grouping operations into phases. Such strategies failed due to the lousy communication channels between the City of Denver, the PMT, and the consultant team. The construction team also faced a challenge in keeping track of the changes that occurred during the processes—this resulted from the initial individual tracking where each party had their tracking system, making it hard to combine them into a single, comprehensive report.
The management structure for the DIA construction could not manage the efficient and rapid production of engineering alternatives and support the cost and schedule data. The development of a new airport requires the management to define such an option to facilitate the fast completion of projects and minimize unnecessary costs. For the DIA construction, the sources of funds were diverse, including the issuance of revenue bonds and federal grants, and it was a work program for the public. Due to this, the management had to balance organizational, political, and social factors, making it challenging to manage and control the project through rapid engineering alternatives and efficient schedule. Moreover, when BAE Automated Systems signed the contract to build the baggage handling system, the terminal and concourses construction had begun; hence, the firm had to make several changes to the overall terminal design. Perhaps there was poor planning, which should have included the baggage handling system from the beginning of construction.
Approaches to Prevent Issues
If I were among the DIA construction project management team, we would have conducted a thorough analysis of the issues that may result during the process and defined various measures to implement to reduce the risks. Delays in project construction factors result in significant disruptions of the project time, cost, and quality (Santoso & Soeng, 2016). As a result, we urge the project consultant team to conduct a comprehensive assessment of all possible factors that may result in delays. First, we would divide the construction processes into stages and allocate a reasonable time frame that each phase should take. The consultant team should then concentrate on each phase's activities to ensure the identification of any possible problem. The consultant team's areas include unrealistic project duration, foreign designers, architectural design features, and the administrative offices (Atout, 2016). Right communication channels ensure no arguments or indirect disagreements among the stakeholders; thus, efficient coordination of the construction features. Also, all parties must have an excellent understanding of the project’s objectives. Facilitating good communication among stakeholders would require the enhancement of cultural diversity to ensure maximum interactions.
Our team would ensure integration of the project's planning stages to incorporate building information modeling (BIM) to enable every stakeholder to have insight and access to tools that can facilitate the entire process. The strategy would ensure efficient planning of the activities and consider the baggage handling system before commencing the physical construction. The stakeholders did not plan properly at the initial project stages; hence, the building experienced delays when introducing the baggage handling system. The situation arose due to the massive change they had to make and reconstruct several terminals and concourses points. Also, efficient communication channels would be crucial to enable every stakeholder to share their recommendations on time. Thus, the PMT must ensure cooperation among all the stakeholders of the construction process. Moreover, we would recommend that the City of Denver consider a more uniform financial plan to minimize the project's administration's straining in evaluating more administrative duties. Besides, this will ensure proper budgeting and scheduling of work. The team would ensure that every person has the necessary skills and qualifications that project completion requires. Ramli et al. (2018) identify improper construction methods and the contractor's technical staff's insufficient capability as some of the significant factors that cause construction delays. Since the DIA construction was one of the largest and the first major airport projects in the United States in more than a decade, it required highly-qualified personnel to facilitate its completion. Thus, as the project management team, we would ensure all our technical staff receives appropriate training and assign them to their areas of expertise. The construction of an airport is a huge task that involves several activities with different levels of expertise. Therefore, posting the workers in their areas of expertise will ensure no delays throughout the work processes.
Techniques to Correct the Issues
Addressing time overlap issues during project constructions requires critical attention to several factors that may cause any delay (Ullah, 2017). The first step to correcting the DIA construction and building of the baggage handling system would be to communicate every error with all the team members. The PMT members must understand the problems and the impacts they are likely to cause to other project stages and objectives. Alerting the team and all stakeholders about the issues will ensure every individual takes appropriate measures to minimize damages. Every stakeholder should admit the problems, and the project leaders should assume ownership of the issues. Such a strategy will build trust among the parties involved; thus, facilitating better communication channels that can help inefficient handling of the problems. Also, more than one contractor was involved in the construction of the DIA; hence, the administrators should precisely determine the source of any error. In contrast to Mayor Webb, who instantly blamed BAE Automated Systems for the delays, we would first assess the situation before rushing to any conclusion.
After determining the source of the errors that caused the delays, our PMT would document the details. Through this, we can ensure various practices that will prevent further issues. For instance, if I were the President of BAE Automated Systems, DI Fonso, I would approach Mayor Webster to document the mistakes that led to the delays and explain the actual cause. Communicating in this manner will promote understanding between the parties; hence, ensuring no future buildup of hostility—this is an interpersonal aspect that will provide better relationships between the parties (Khoiry, Kalaisilven & Abdullah, 2018). The stakeholders should also coordinate to outline an appropriate schedule for addressing the issues. The administration should find out if the project's financials can be available at the right time to ensure the efficient running of the operations according to the initial plan.
BAE Automated Systems can contract more workforce to facilitate the building of the extensive baggage handling system. Perhaps the project’s opening had to be pushed several times since the BAE had no experience with such big projects; hence, more workers would enhance the speed of its activities. The City of Denver may also seek a more homogeneous financial plan to ensure no delays in availing the necessary resources—this will ensure proper budgeting for the project and scheduling of work.