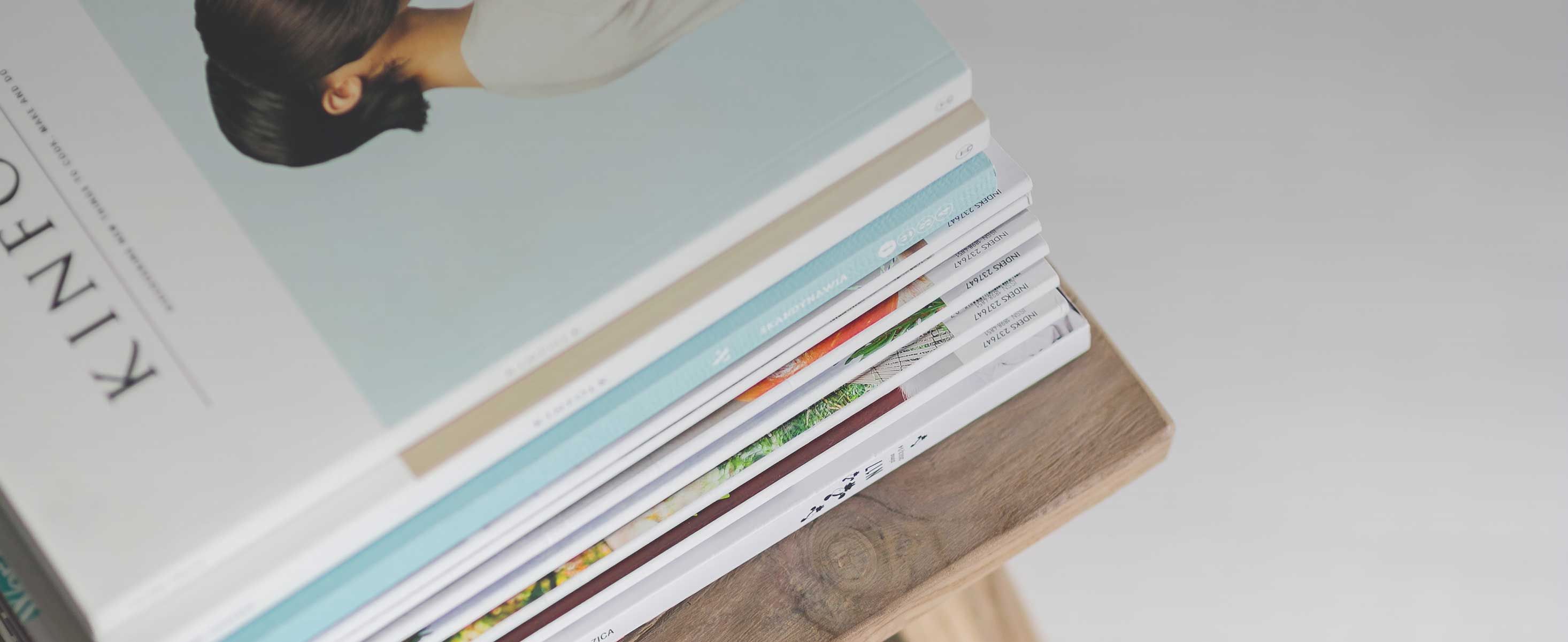
2 minute read
Manual Handling – risk prevention
from AccessPoint Issue 11
by accesspoint
It’s not about how much you can lift; it’s how you plan the lift. Thomas Rhodes, from SMAS Worksafe, highlights some of the key considerations when manual handling.
Scaffolding is complex and important work across a multitude of industries, with the variety and types of scaffold ranging extensively. Time is a precious commodity when it comes to installing and dismantling structures. Clients may set time restrictions around the work or alter their requirements at the last minute.
Advertisement
In 2017/18 the HSE reported there were 469,000 workers suffering from workrelated musculoskeletal disorders, with 156,000 new cases reported.
This meant there was 6.6 million workdays lost across industry.
When undertaking a risk assessment for manual handling operations, it is helpful to use the TILE acronym, as detailed in the Manual Handling Operations Regulation 1992:
TASK
Does the task involve:
Carrying loads away from the body?
Twisting, stooping or reaching upwards?
Excessive movement of the load?
Frequent or prolonged physical effort?
Insufficient rest and recovery periods?
Individual
Does the task: Require unusual strength or height?
Create a hazard to those with a health problem?
Require special information or training?
LOAD Is the load: Heavy?
Bulky or cumbersome?
Difficult to grasp?
Unstable, with contents likely to shift?
Environment
Are there:
Space constraints?
Uneven, slippery or unstable floor surfaces?
Extremes in temperature or inclement weather?
Poor lighting conditions?
As we get deeper into the winter months the inclement weather conditions and lessening natural light, all begin to increase the burden on operatives to get the job done and, potentially leaving them feeling pressured to lift more equipment and overload themselves physically to meet the demands of the job.
A large percentage of the injuries sustained were to the upper limb or neck and then to the back and lower limbs.
The positive news is the rate of selfreported work-related musculoskeletal disorders have taken a downward trend, but more work needs to be done.
You can reduce the risk of musculoskeletal injuries when manual handling by introducing a number of control methods:
ELIMINATION Scaffold workers should try and avoid lifting manually where possible through the use of mechanical means, like using forklifts, telescopic handlers or hoists to move equipment within the work area.
HANDLING AIDS Using a trolley or gin wheel when moving equipment won’t eliminate the manual handling activity however the mechanical advantage will provide additional assistance.
MODIFICATION Modifying the task, load or environment can greatly reduce the risk of injury. Examples include:
The task of repetitive movements or awkward postures can be relieved with frequent breaks
Loads can be broken down into smaller parts
The risks associated with loads over 20kgs should be mitigated through the use of suitable lifting equipment
Maintaining good housekeeping will keep the working environment clear and free from trip hazards
Planning suitable vehicle routes, close to the work area will reduce carrying distances
TRAINING After establishing that an individual is capable of undertaking the manual handling activity providing training on basic lifting practices, and ensuring they have the appropriate PPE are important factors in risk reduction. Lifting techniques for different materials such as boards, ladders and tubes all have their own challenges; even light loads picked up incorrectly can cause injury. Guidance documents like SG6:15 provide workers with the fundamentals when manual handling.
The HSE MAC tool provides three types of manual handling operations to be assessed for single lift, single carry and team handling. You can then develop a risk assessment that will evaluate, for example, how many tubes or boards are sufficient to carry, or the maximum load for a gin wheel (50kgs).