
4 minute read
ANCHORED IN THE BAY
Keller Installs Anchors for the New Howard Frankland Bridge, Spanning Tampa Bay.
Since 1959, the Howard Frankland Bridge has connected Tampa and St. Petersburg, carrying traffic across Tampa Bay. With expansions and widening projects occurring since the 1990s, the most recent Florida Department of Transportation megaproject will expand the bridge once more.
A TRAFFIC CHANGE-UP
The existing crossing consists of two bridges, spanning four lanes each—one southbound and one northbound, providing a passageway between Tampa and St. Petersburg for approximately 500,000 commuters daily. The expansion includes the construction of a new bridge crossing eight lanes wide, including four southbound lanes, four bi-directional express lanes, and a bike/pedestrian lane.
The existing southbound bridge will be converted for northbound traffic, while the existing northbound bridge will be removed after full project completion. Not only will the new construction pattern alleviate traffic concerns, but it will also provide a vital evacuation route during hurricanes.
Building Up
“Before they could begin bridge construction, the shoreline along the Bay needed to be built up to accommodate the new causeway and bridge approach ramps,” said Engineering Manager Casey Shanahan. “This area required infilling Tampa Bay, which was retained by sheet pile and/or combi-wall bulkheads installed by others—11,000 LF.”
Keller designed and installed a permanent soil anchor solution to support bulkheads. Anchor loads were heavily influenced by the fill heights and proximity of the bridge’s MSE approach ramp fill. In the highest loaded areas, the MSE ramps reached nearly 30 ft tall and encroached within five feet of the bulkhead wall, resulting in anchor design loads up to 370-kips.
Casey recalled, “The soil conditions on-site were typically loose to dense sands underlain by clay over karstic limestone,” he continued, “We designed the larger anchors to bond into the limestone, which proved difficult due to approximately 100-ft variances in limestone depth in some areas. Keller’s CAD team modeled the limestone profile to best determine anchor lengths beforehand. In the end, some anchors were up to 200 ft-long.”
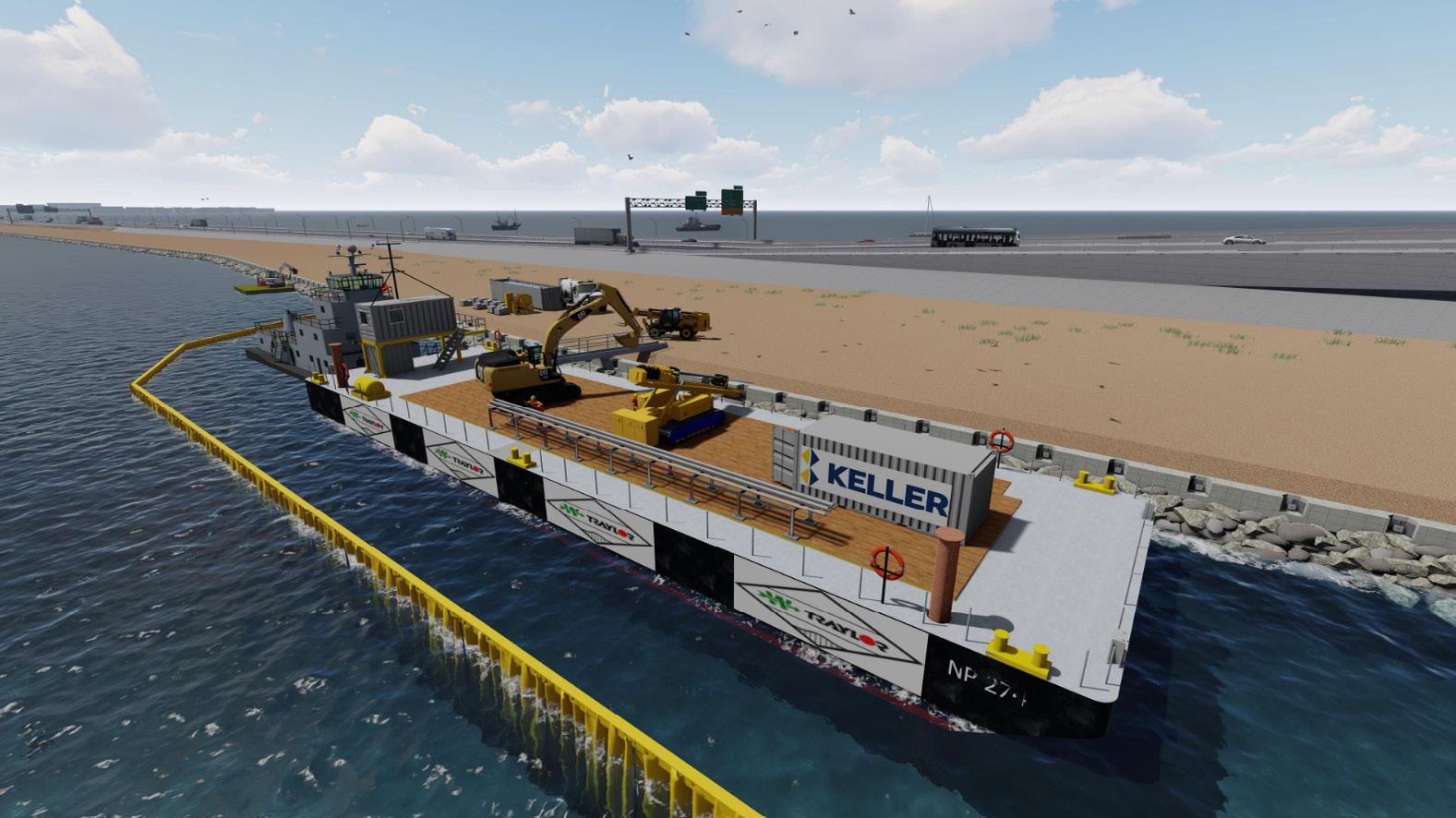
Drilled shaft foundations and other structures were installed before anchor construction. To avoid conflicts with the piping and structures, anchor angles were skewed horizontally and vertically. However, through 3D mapping and coordination with the GC, the project team accommodated all modifications to the soil anchor alignment with minor impact.
A Barge In The Bay
“Most of the anchor work was performed from barges,” said Senior Project Manager Trey Davis, “in some cases, the bay water depth and existing structures created access constraints, impeding barge work; those anchors were drilled landside with an excavator-mounted drill mast.
“Construction went well, but we were at the mercy of the Bay and its tidal fluctuations. The waler work required welding to a dry surface, and anchor elevations were generally located in the zone between low and high tides.”
On average, the bay water levels fluctuate between two to four feet, depending on the lunar stage. Adding to the challenge was the king tide, high winds, and even hurricanes from time to time. “Working over open water is certainly a challenge,” says Trey, “Mother Nature cannot be controlled, and you must learn to adjust your plan constantly. You take what you're given, and the team is committed to being as efficient and productive as possible all the way to the finish line.”
Testing And Success
In total, 1287 anchors were installed. “Alongside the installation, we completed a significant testing regiment,” continues Trey, “1094 anchors were proof-tested, 128 were performance-tested, and 65 were creep-tested. Of these, only three anchors were replaced for low capacity. Considering the scale of this project and the challenging geotechnical profile, I’d call that a major success!”

Casey and Trey agreed that the success came down to knowing the variances for the top of limestone, manipulating the designs where needed, and proper construction sequencing based on the weather and tidal conditions.
“First and foremost,” Trey concluded, “We had a great team on site to make it all happen. When you’re on a project for 18 months, challenging or not, the tasks at hand can be tough to maintain. But our field leadership and employees stuck to the plan and delivered a quality product at the end of the day.”
The bridge construction is still ongoing and expected to conclude in 2025.