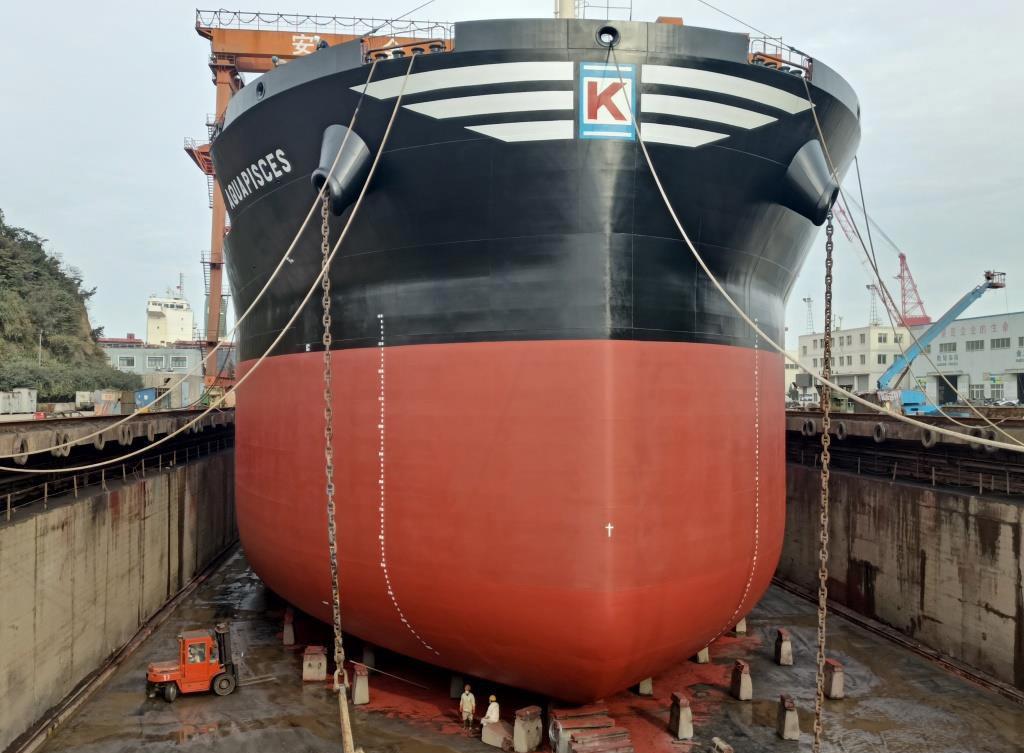
18 minute read
Repairs
Greek drydockings*
The end of 2021 and the beginning of 2022 is a crucial point for the shiprepair market. Throughout 2021, it was thought generally that the problems with COVID-19 would be over by 2022 and the shiprepair market will face much better days.
Advertisement
This report will look into the shipyards where Greek vessels have been repaired during 2021. By Greek vessels, we mean not only vessels under the Greek flag, but also vessels under the management of Greek shipping companies.
For the last years, China has been the main shiprepair base for Greek owners. However, the main problem for shiprepair during 2021 and especially for shiprepair in China was the COVID-19 restrictions posed by local authorities. Due to these restrictions, the vessels were obliged to stay quarantined for many days prior to entering the yard. The superintendent engineers or other necessary technicians required special permissions to travel to China and had to stay quarantined at dedicated hotels for 14 days, which was increased to 21 days in the second half of 2021.
This problem caused a lot of Greek owners to get drydocking/repairs postponements from vessel classification societies, hoping that the restrictions will be eased later and taking advantage of the good freight markets. The postponement was initially for three months but there were many cases where drydockings were postponed for six or even nine months.
Greek owners started to search for other countries in which to repair their vessels. The problem was that shiprepair yards in other Far East countries are not ready to replace Chinese shiprepair yards. A few Greek vessels have been repaired at yards in Korea, Vietnam, Philippines, and Thailand, but the shiprepair facilities there are small or with poor quality or higher prices than China. These shiprepair facilities were also, most of the time, occupied by local vessels.
The shipyards in Singapore, which had the chance to get a big part of Greek vessel repairs, also faced problems with manpower due to COVID-19 and they were obliged to reduce the number of the vessels that they repaired during 2021. Only the yards at the Persian Gulf have increased the number of Greek vessel repairs.
In this respect, most Greek vessel repairs (around 52% of the total Greek vessel repairs) were carried out in China. In South China, the most Greek vessel repairs were carried out at Fujian Huangdong, followed very closely by Yiu Lian, Wenchong and Cosco Guangdong. In the Zhoushan area, the most repairs were carried out at Cosco Zhoushan, Changhong, Huafeng, Jinhao and Xinya. In the Shanghai area, the most repairs were carried out at Chengxi, Cosco Nantong, Chanxing and Huarun Dadong. Finally in North China, the most repairs were carried out at Shanhaiguan Shipyard, which was also the most successful shipyard for Greek vessels in all of China (more than 11% of all Greek vessel repairs in China), followed by CUD Weihai and Cosco Dalian.
In the Far East outside of China, the most Greek vessel repairs were carried out in Singapore and especially at Sembcorp Marine and Keppel Shipyards.
The number of Greek vessels which have been repaired at the Persian Gulf within 2021 has increased as COVID-19 restrictions were not as strict. Most repairs were carried out at Dubai and Oman, with the yards at Bahrain and Qatar to follow in third and fourth place respectively.
In Europe, 2021 like 2020 was very successful for the shipyards in Greece and it seems they are fully booked until the first quarter of 2022. Almost 10% of the Greek vessel repairs were carried out in Greece, mainly at Onex Syros, Chalkis and OLP shipyards. The question for 2022 is when the shipyards of Elefsis and Skaramangas will open again in order to attract more Greek vessels to Greece for repairs. Turkey remained as the first choice in 2021 for repairs of Greek vessels in Europe with the majority repairs carried out at Kuzey, Besiktas, Desan, Tuzla, Gemak and Sefine. However, a lot of Greek owners have started to worry about the political and financial stability in Turkey during 2022.
Regarding the Black Sea area, the most repairs were carried out at Constanta and Mydia in Romania, followed by the Odessos Shipyard in Bulgaria. The number of Greek vessel repairs in other European countries has increased slightly with the majority carried out at Portugal’s Lisnave.
The lack of shiprepair facilities in Africa and America has persisted into 2022 and very few Greek vessels were repaired there. The most Greek vessel repairs at Africa were carried out at Nigerdock – Nigeria.
Regarding Greek vessel modifications during 2021, the era of scrubber retrofitting is over, with very few scrubbers retrofitting modifications to be carried out. However, many vessels have proceeded to install BWM systems within 2021 and many others are predicted to be carried out within 2022.
Central China – Zhoushan area – 15.43% Central China – Shanghai area – 14.60% North China – 13.68% Arabian Gulf (including Oman) – 11.46% Turkey – 11.00% Greece – 9.98% South China – 8.60% Black Sea – 6.10% South East Asia (including Singapore) – 5.63% Europe – 2.40% Others - 1.20%
*This report has been compiled for SORJ by Antonis Kalofonos, a shiprepair broker based in Greece for the past 20 years.
Carras Hellas’ bulk carrier Aquapisces during her drydocking in China.
FPSO work at Navantia
Spain’s Navantia Shiprepairs’ Ferrol Estuary undertook a total of 28 repair projects of merchant vessels in 2021, featuring the repair of 14 LNG tankers and one LPG tanker, which positions the facility once more as the key Atlantic reference for gas tanker repairs. These 14 LNG projects represent 50% of the commercial vessels repaired during 2021, and approximately 70% of the total turnover of this shiprepair centre.
The facility is involved in the life extension project on-board the FPSO Terra Nova, the first phase of which started with the contract signature in mid-October, and which has subsequently been focused in the organisation, co-ordination, planning, management and logistic preparation works required for the second phase of the project, with an estimated duration of around seven months as from the arrival of the vessel at the yard in early 2022. The magnitude of this project is the largest ever contracted by Navantia Shiprepairs Ferrol Estuary, therefore representing an unprecedented challenge.
This year (2020) has seen Sinokor Tanker’s
126,750 m3 LNG tanker Bering Energy continue alongside a repair berth in Fene awaiting a second drydocking. Once its reactivation process has been resumed, which is foreseen for 2022, she will move into drydock.
During December, Navantia Shiprepairs Ferrol Estuary started the repair projects of Jan de Nul’s 7,531 gt pipe-burying vessel Adhemar de Saint Venaqnt, which was drydocked in Drydock No 5 in Fene, with delivery carried out in January 2022 and started the repair of Prestige Ray’s 11,196 dwt ro/ro vessel RCC Prestige, drydocked after each other in Drydock No 5 in Fene, and delivery in February.
After the departure from Navantia Shiprepairs’ Cadiz Bay facility of Carnival Corp’s 102,853 gt Carnival Sunshine, RCCL’s 90,090 gt cruiseship Radiance of the Sea arrived in drydock, previously berthed at Armamento Pier, for the repair of her bow thrusters.
Columbia Cruises’ 69,472 gt cruiseship Marella Discovery 2 has been drydocked in Puerto Real since early January, where she has been undergoing complete overhaul of the starboard stabiliser and two bow thrusters, steel renewal of the bulb, complete blasting and painting of underwater area, sweeping, patching and the complete coating of verticals and superstructure, and removal of the aft macrodome structure.
Holland America’s 91,627 gt cruiseship Island Princess docked alongside the Cadiz South pier on January 17th where Navantia assisted technicians in the repair of her davits and carried out logistical work, during a short drydock period of five days.
V Ships’ 30,277 gt Azamara Pursuit, which recently left Navantia’s facilities after a general drydocking, returned during December to be berthed at Armament Dock due to the need to install a new anchor.
During January, two research vessels from US-based Ocean Shipholdings arrived in the Cadiz shipyard - USNS Maury and Ocean Intervention II. USNS Maury remained berthed at Arena Pier in Cadiz since late November. During January she underwent pipe replacement work detected during her last days of drydocking. Meanwhile, the Ocean Intervention II, docked at the Armament Pier since early December, remains alongside undergoing maintenance works.
Holland America’s 91,627 gt cruiseship Coral Princess arrived in Cadiz during late November and berthed until early January, when she entered our Dock 4, where she remained approximately 20 days. The main work carried out during her stay in dock have included hull treatment, complete preparation of the underwater area by hydro-blast. Complete renewal of the paint scheme in the underwater area. Regular drydocking works, bottom valves, anodes and inspections of components on the hull, major mechanical overhaul, work on bow thrusters and stabilisers and maintenance work on the lifeboat davits. Navantia has also assisted in logistics, as well as other assistance in various works. This is Princess Cruises’ first contract with Navantia.
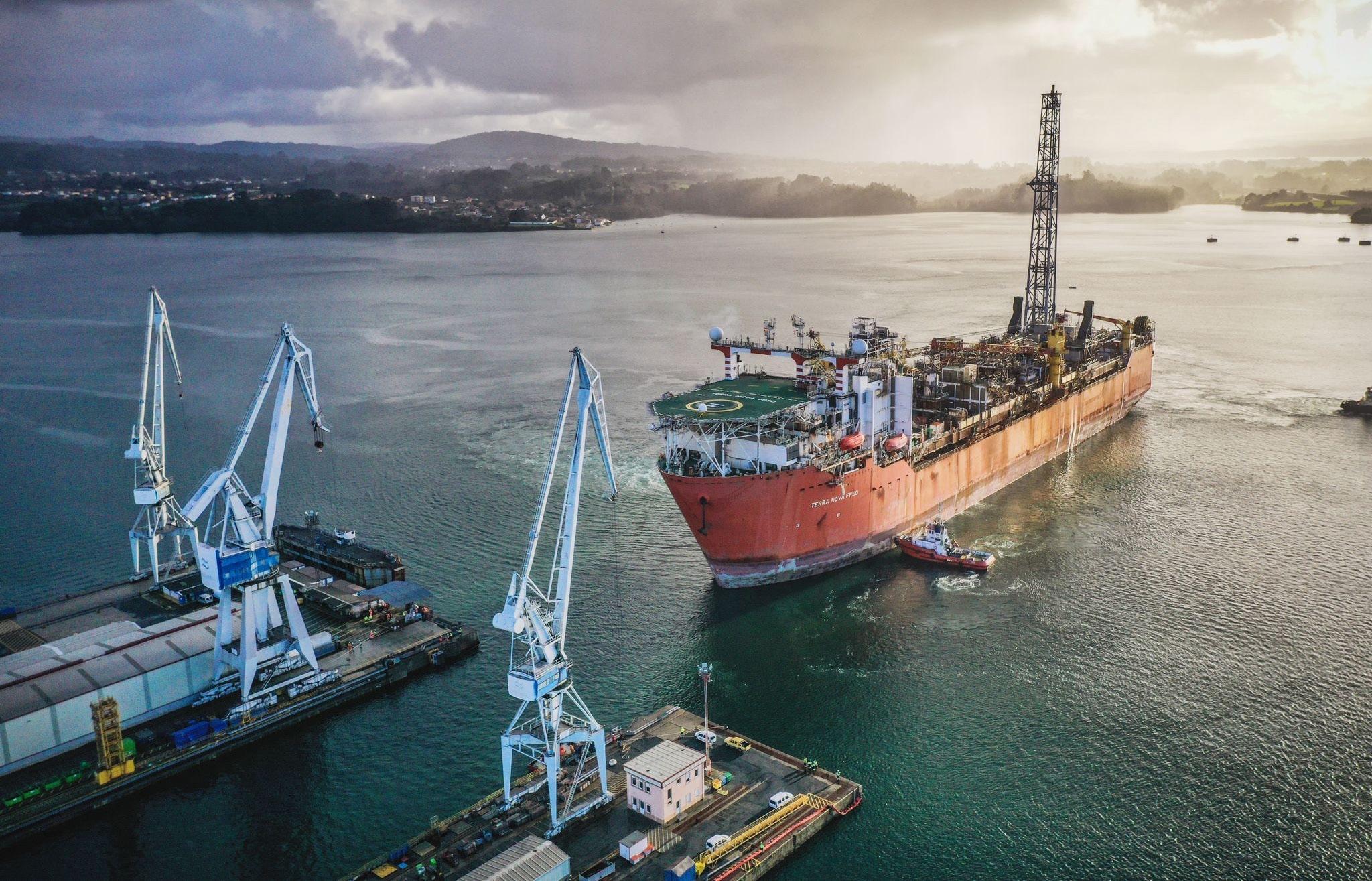
The FPSO Terra Nova arrives in Ferrol
Ferry and cruiseship work at Palumbo
A total of five vessels, two cruise vessels and three ro/pax ferries were undergoing repair at Palumbo Malta Shipyard during February. These were Tirrenia’s 31,041 gt Raffaele Rubattino, and two from Italy’s Grandi Navi Veloci’s – the 26,904 gt GNV Sealand ex Scottish Viking and the 31,785 gt GNV Aries ex Pride of York .
There have also been a number of cruiseships from MSC in the yard over recent weeks - MSC Armonia (58,174 gt), MSC Lirica (58,625 gt), MSC Poesia (92,627 gt), MSC Orchestra (92,409 gt) and MSC Sinfonia (58,174 gt), and one containership - MSC Pina (117,236 dwt)
Other ships recently in the yard included Tsakos Columbia’s 68,439 dwt product tanker Andes (docking, blasting painting, mechanical and electrical works), DEME’s 44,180kW cutter suction dredger Spartacus (full blasting and painting works, docking, steel repairs and pipe works) and Tsakos Energy’s 113,611 dwt tanker Leontios H (standard class renewal work).
In Palumbo Viktor Lenac, Rijeka, there has been a number of interesting projects including Ambassador Cruise Line’s 70,285 gt cruiseship Satoshi (major upgrade work), SMT Shipping’s 5,661 dwt cement carrier Danavik (installation of a 334 m3/hr Optimarin BWM system and alongside, installation and welding of boom foundation and associated components, various LSA testing, and CO2 cylinders inspection), Amoretti Armatori’s 12,094 dwt product tanker Dante ( AC treatment of hull, mechanical works on overboard and safety valves, scrubber outlet pipe renewal, dismounting and complete overhaul of PS windlass with renewal of chockfast, welding on windlass by build-up, light steel repairs, PV valves inspection, main engine vibration damper dismounting and inspection in workshop, Portside Reduction Gearbox complete overhaul, Diathermic Oil System renewal of heating coils inserts, stainless steel),
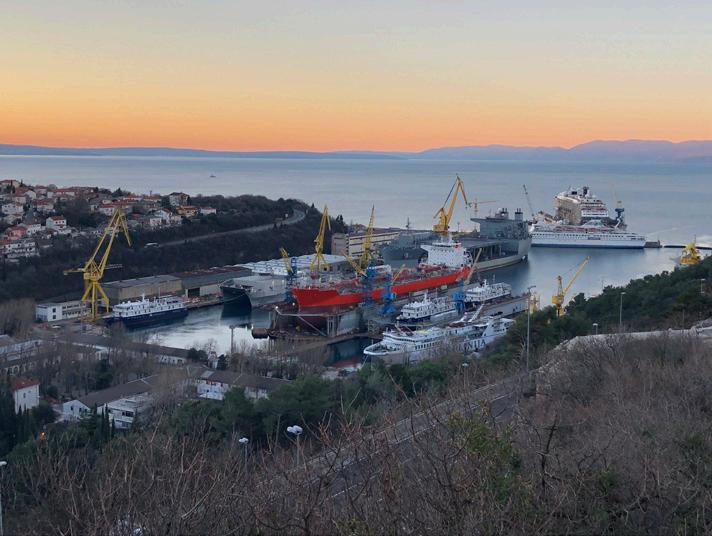
Croatia’s Palumbo Viktor Lenac shipyard
and two cutter suction dredgers from Belgium’s Jan de Nul – the 40,975 kW cutter suction dredger Willem von Rubroeck (work on the spud carrier, cutter ladder, sea water line, steel renewal and piping works) and then 23,520 kW IBN Battuta (standard docking, piping and steel works, installation of BWM system).
There have been two ships recently in Palumbo Naples – Tschudi Lines’ 3,250 dwt cement carrier Capo Cinto (standard drydocking and BWM system installation) and Fugro’s 1,340 gt research/survey vessel Kobi Ruegg (emergency repairs and mechanical works).
In Palumbo Messina, a total of five vessels have recently been repaired, all standard class renewal or drydocking operations – Ponte Ferries’ high-speed ferry HSC Artemis (also aluminium repairs), Augusta Due’s 40,083 dwt chemical tanker Alicudi M, Synergas’ 4,026 dwt LPG tanker Syn Zania and the Italian-registered 2,377 gt ro/pax ferry Riace (also steel renewal)
Good start to the year at A&P
A&P North East’s Tyne facility has reported a busy start to the New Year with its drydock and quays operating at full capacity. Boasting the largest commercial drydock on the East coast of England, A&P Tyne facility provides world-class shiprepair, conversion and fabrication services across the marine and energy sectors.
A range of vessels from the offshore sector are currently undergoing extensive programmes of works at the facility, with vessels Ulisse, Deepsea Worker and Cable Enterprise all
benefitting from A&P Tyne’s expertise.
Prysmian Group’s 17,160 dwt cable laying barge, Ulisse, has arrived again at the facility for significant modifications, with work to include the fabrication and installation of a new mezzanine deck, two new thrusters, including compartments, and Lifeboat platforms. Meanwhile, another ship from the Prysmian fleet, the 13,671 dwt Cable Enterprise has returned to the facility and is currently alongside A&P Tyne’s West Quay for minor maintenance prior to deployment for cable operations,
DOK (UK)’s 3,345 gt Deepsea Worker is alongside on A&P’s Bede Quay following her drydocking. The offshore support vessel’s scope of work included a full hull paint programme, the range and calibration of anchors and cables and the emptying and cleaning of the sewage tank.
Accompanying Ulisse in drydock is Prysmian’s newly acquired shallow water cable installation barge Barbarossa. She will undergo some maintenance and cable lay equipment mobilisation prior to her first project.
Speaking about the buoyant start, Chris Davies, Business Development Manager at A&P Marine, said, “The simultaneous drydockings of Ulisse and Barbarossa demonstrates the flexibility of A&P’s facilities, which enables us to deliver multiple programmes of works at any one time. The successes of the last few months reflect the hard work and dedication of our team throughout the pandemic and our long-standing relationships with clients and their returning vessels.”
Meanwhile, A&P Group UK and A&P Australia has simultaneously carried out refits of two Bay Class vessels - RFA Cardigan Bay in the UK and HMAS Choules in Australia. RFA Cardigan Bay has recently completed her refit at A&P Falmouth and resumed her MoD ‘Fleet Time’ schedule, whilst HMAS Choules continues a significant refit period at A&P Australia’s facility in Sydney.
The Bay Class are amphibious landing ships built for the British Royal Fleet Auxiliary (RFA) during the 2000s. UK based A&P Group supports RFA Cardigan Bay, RFA Lyme’s Bay and RFA Mounts Bay as part of its Through Life Support (TLS) contract with the MoD. HMAS Choules, formerly RFA Largs Bay, was purchased by the Royal Australian Navy in 2011. A&P Australia was incorporated in 2012 and has been supporting HMAS Choules since her arrival in Australia. In 2015, A&P Australia was awarded the In-Service Sustainment and Support Contract for HMAS Choules which was extended in 2019.
RFA Cardigan Bay has completed a significant mid-life refit at A&P Falmouth. The work included critical equipment and obsolescence upgrades and accommodation updates. The vessel underwent a substantial docking period at the start of the refit carried out over 90 days including painting, hull access, stern/side ramp removal and significant work to the propulsion system. The remainder of the period was spent alongside A&P’s Falmouth facility and ensured the continued performance and availability of this RFA Bay Class vessel.
The vessel’s refit was the second of three planned refits being delivered at A&P Falmouth for the Bay Class vessels with RFA Mounts Bay completed prior and RFA Lyme Bay scheduled for 2022.
Since 2019, A&P Australia has been tasked as the principal systems integrator for the HMAS Choules Capability Assurance Project (CAP). The project involves the design and installation of over 80 engineering changes across 44 capability enhancement areas to assure the capability and supportability of the vessel until her planned withdrawal date early next decade.
The CAP has been integrated with sustainment and has been delivered progressively through a number of maintenance periods - however, this current refit is the major upgrade window and is acting as a mid-life upgrade for the platform. Refit Period 21 is spanning over 300 days at an estimated production cost of $90m and is being delivered by a 500-strong daily workforce from over 50 suppliers.
The Refit Period includes a major system renewals programme which includes the Dry Exhaust, HVAC, BWM system, numerous

The Cable Enterprise alongside at A&P Tyne
Shuttle tanker repairs in Lisnave
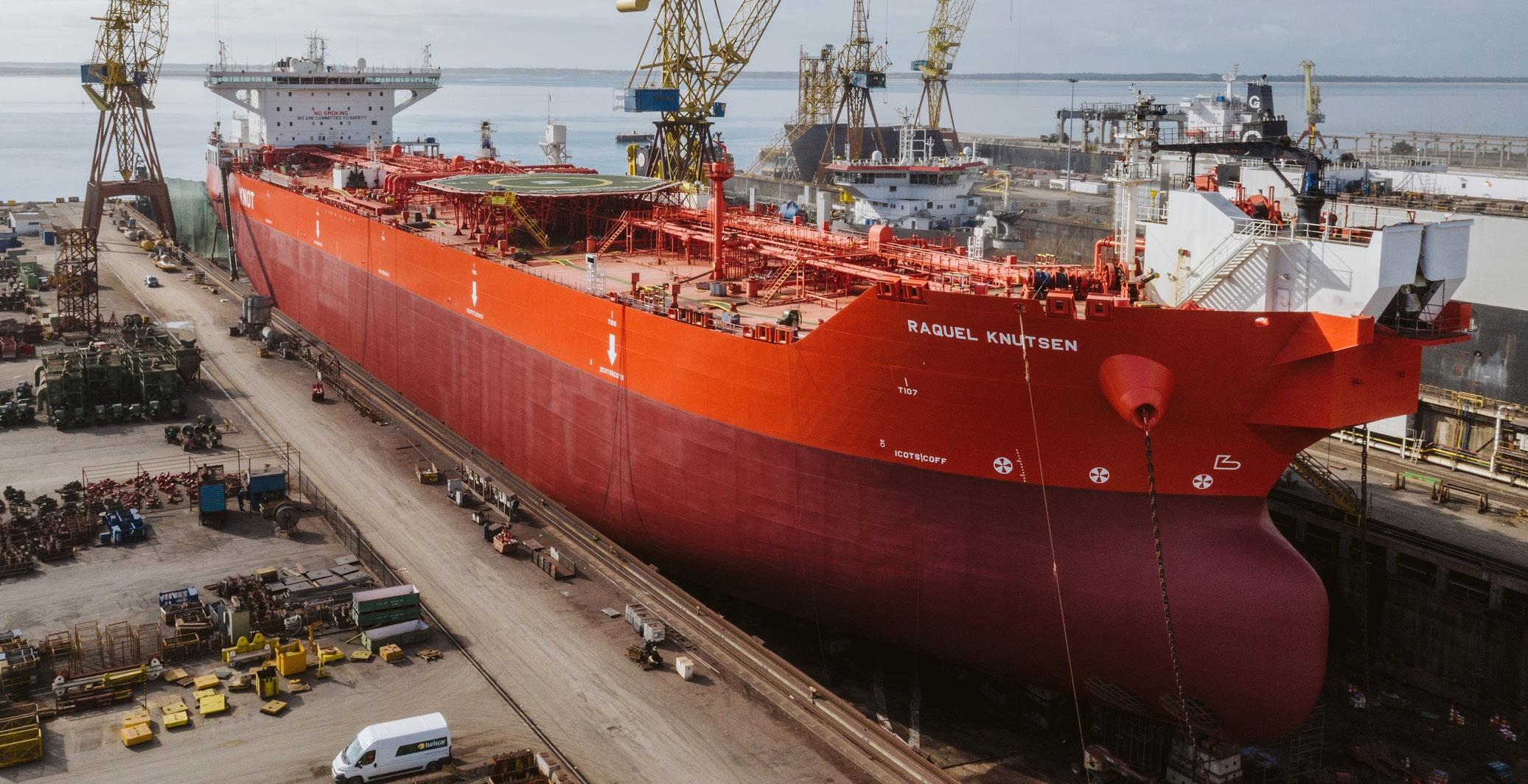
auxiliary and mission system upgrades and enhancements, as well as a major sustainment package for hull and tank preservation, structural and machinery repairs and planned maintenance across all fitted equipment, including main engines, power generation, propulsion and auxiliary systems.
2021 results from Lisnave
During last year (2021) Portugal’s Lisnave, Setubal, successfully concluded repairs to some 80 vessels, which is an increase of four compared with the previous year. A total of 58 shipowners/managers from 20 countries used the shipyard, with Greece (15), Norway (12), United Kingdom (11) and Germany (7) having the highest involvement.
Lisnave has always had a first-class reputation in the general repair market, especially in the various tanker trades. Tankers (including product/chemical) were the largest category repaired last year with 31 projects completed, followed by gas tankers (21 LPG tankers and one LNG tanker), containerships (9), and bulk carriers (5).
This is reflected by the number of traditional owners sending multiple ships to the yard for schedule repairs - UK’s Navigator Gas, Northern Marine and Zodiac Maritime, Denmark’s Maersk, Norway ‘s Knutsen OAS and Solvang, and Greece’s Latsco Marine,
Among the repair projects carried out last year, the largest and most complicated were the extensive steel renewals on-board Knutsen OAS’ 90,814 m3 LNG tanker Bilbao Knutsen (130 tonnes), and Scorpio Shipmanagement’s 38,734 dwt chemical tanker STI Pimlico (188
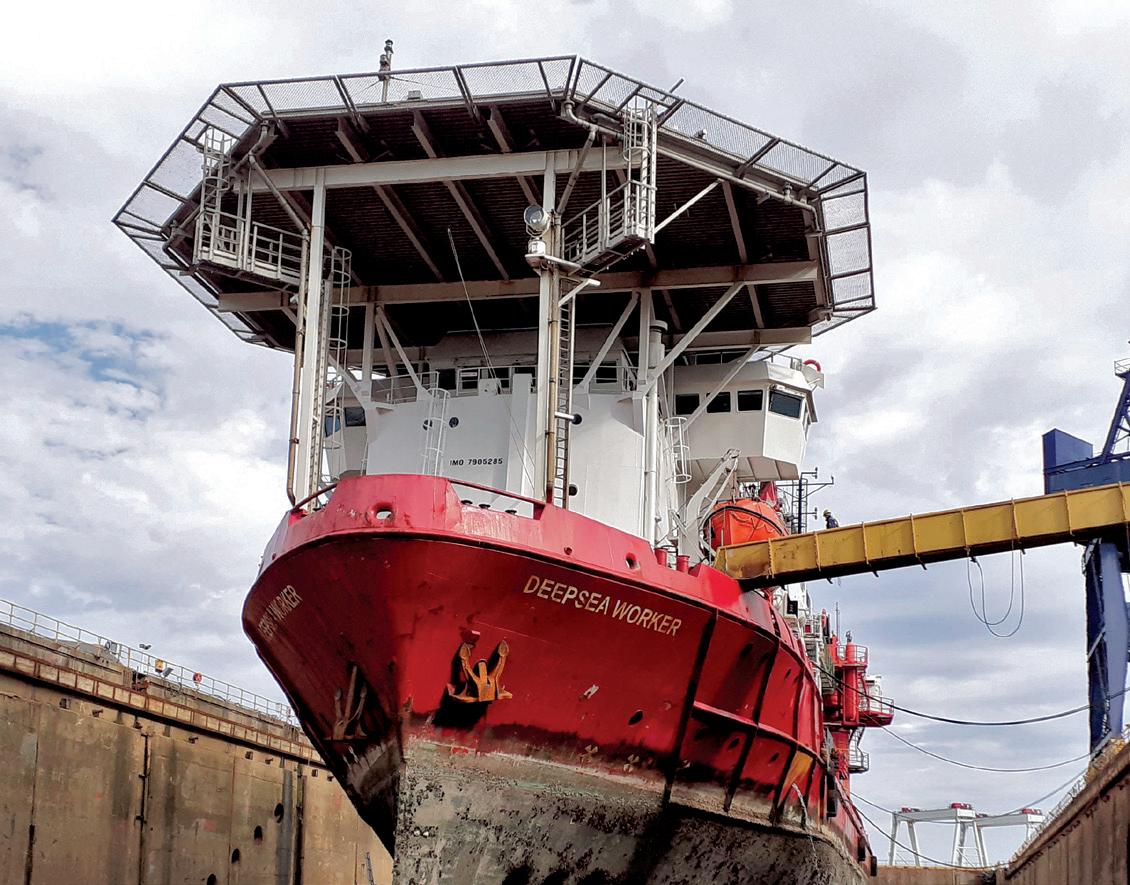
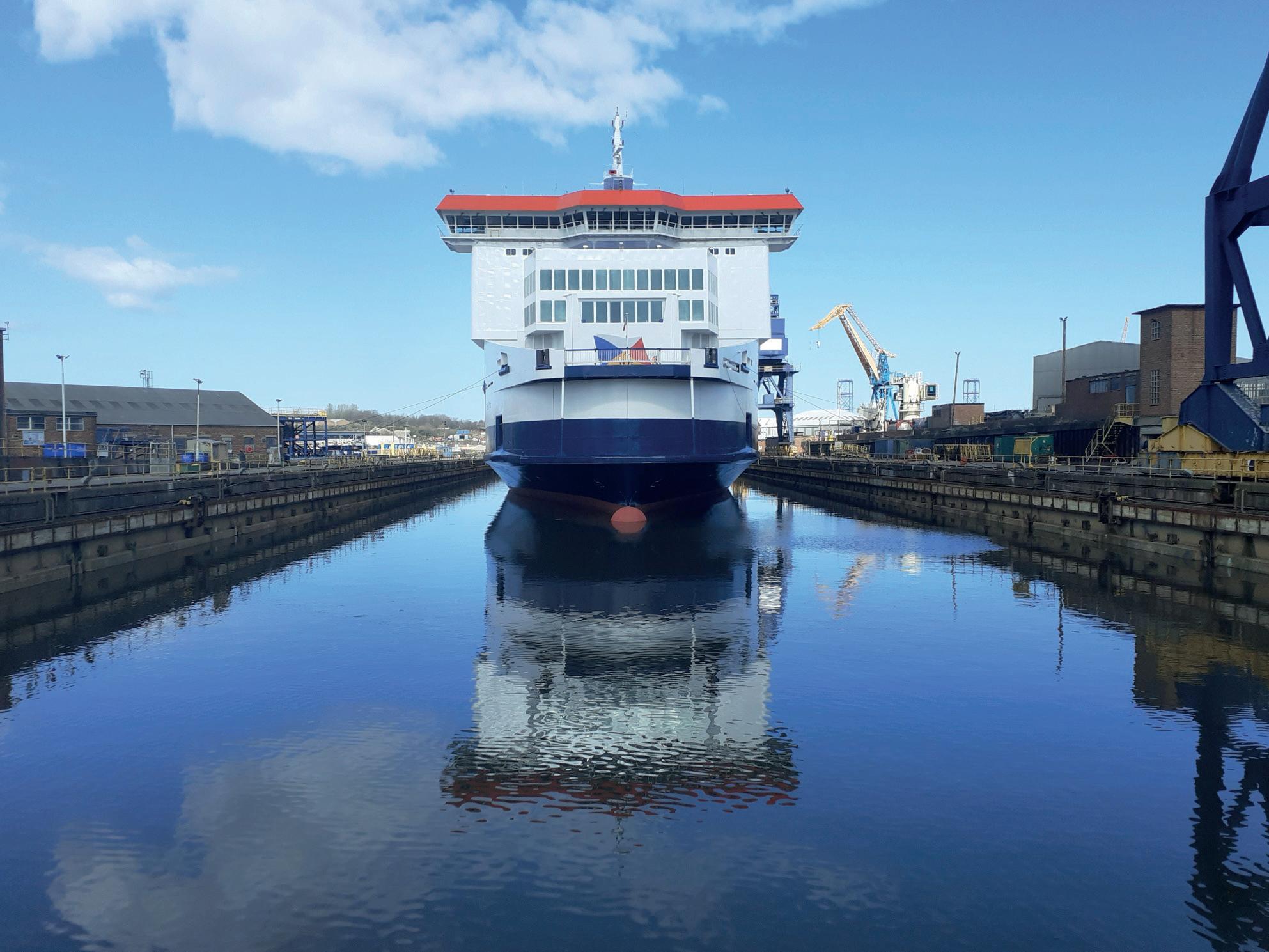
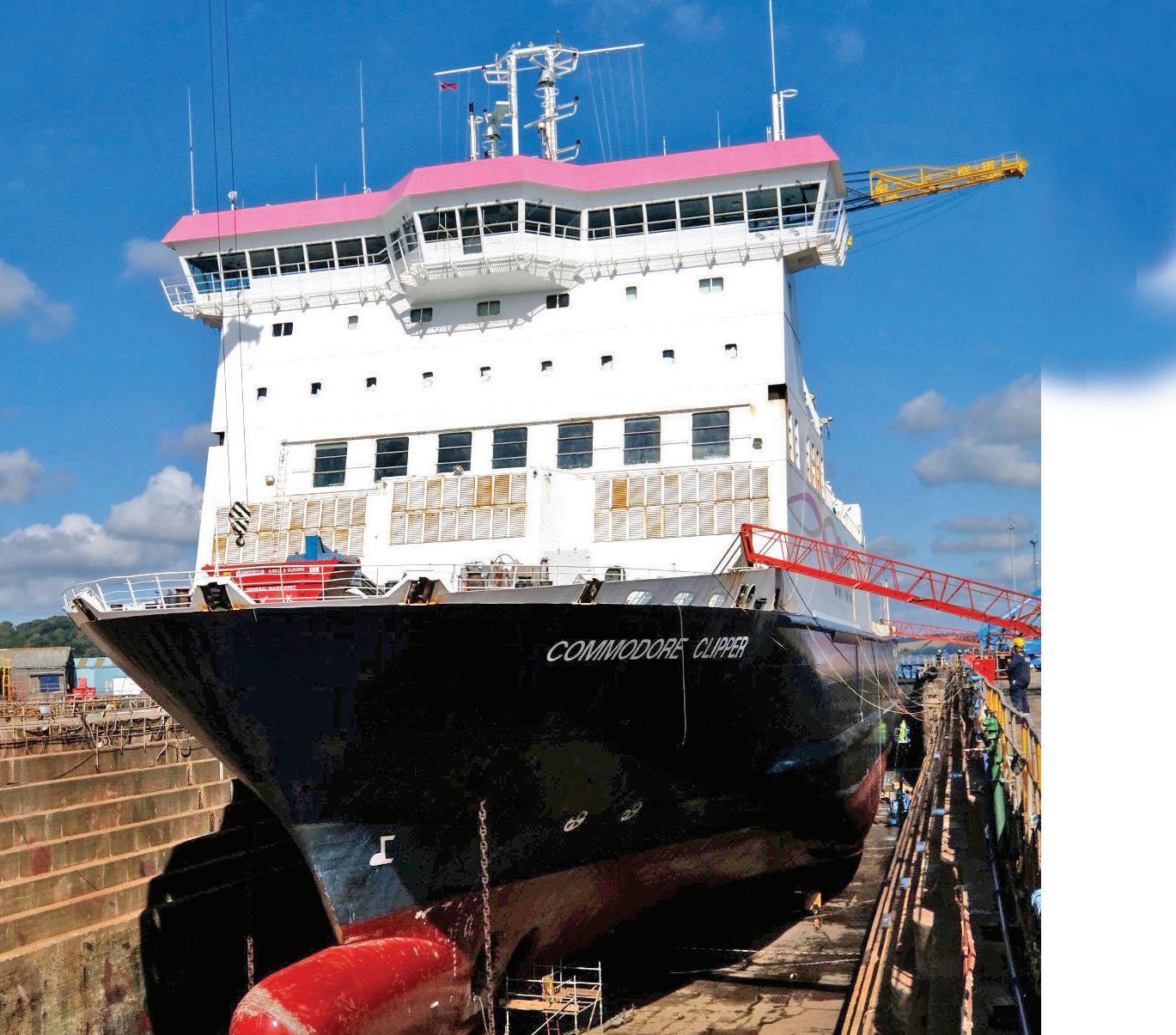
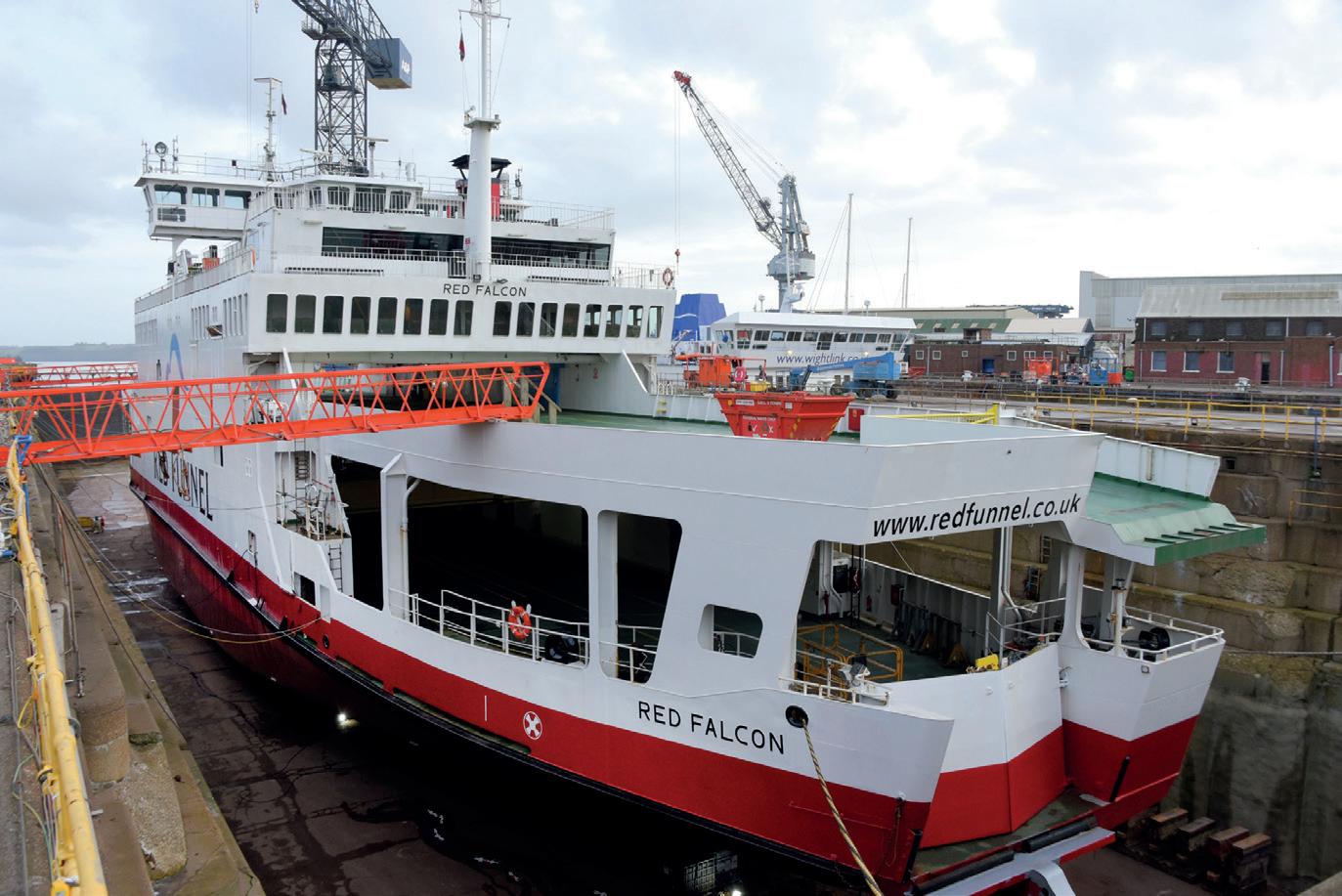
A&P NORTH EAST
A&P GROUP - THE UK’S LARGEST COMMERCIAL SHIP REPAIR FACILITY
A&P operates three full service ship repair facilities located on the North East Coast and South West coast of the UK.
A&P provides ship repair, maintenance, conversion, life extension and fabrication services to the commercial marine sector and energy sector industry.
includes the successful turnaround of passenger vessels, offshore units
A&P SOUTH WEST
A&P SOUTH WEST
DOCK NO. 2 259.1 x 39.6 M
DOCK NO. 3 228.8 x 26.8 M
DOCK NO. 4 177.7 x 26.2 M A&P NORTH EAST
DOCK NO. 1 259 x 44 M
DOCK NO. 5 175 x 22 M
DOCK NO. 6 120 x 17 M
MARINESALES@AP-GROUP.CO.UK WWW.AP-GROUP.CO.UK
The Stena Hollandica in EDR Antwerp Shipyard
tonnes).
One of the largest projects carried out by Lisnave during 2021, was the modifications on-board of 55,451 gt cruise vessel Vasco da Gama built in Italy during 1991 and now owned by Mystic Cruises.
She entered the yard during July 2021, for an extensive upgrade project, including interior refurbishment to new higher standards and a major upgrade to adhere to the most stringent international rules, including environmental and energy increased performance and digitalisation, making this project a fantastic ‘Circular Economy’ example applied to the Maritime Industry.
Two Stena vessels in EDR
Recent weeks have seen Swedish ferry company Stena Line’s two largest ferries, the 63,000 gt Stena Hollandica and Stena Britannica, complete a €1m refit to provide brand new on-board facilities. The North Sea vessels, which sail between Harwich (UK) and Hoek van Holland (Netherlands), were in drydock in Belgium’s EDR Shipyard, Antwerp to undergo their regular annual maintenance to keep them up to the company’s high standards. While there they also received some new additions to the on-board services on offer for passengers.
To cater for a huge demand since Brexit, Stena Line has added a new additional Duty Free shop to each vessel, extending the retail floorspace on both ships by a whopping 40%. Allowing the company to greatly increase not only the capacity of goods on sale, but also extend the range of products on sale by almost a third. Meaning more Duty Free bargains on sale for its North Sea customers, who can save up to 50% off UK high street prices. The interior work was carried out by Northern Ireland’s Maddens Marine, Belfast.
Meanwhile, for those passengers that enjoy the wide selection of on-board facilities, the vessels two popular Barista Bars have received a new stylish Scandinavian look and feel. Allowing customers to enjoy their journeys eating, drinking, and relaxing in luxury and comfort. Each of the vessels top of the range Captain’s Suites have also been refurbished to maintain the high standards that Stena Line’s premium customers demand and expect.
The Stena Hollandica and Stena Britannica are 240 m in length and at 32 m width, each vessel has over 5 kms of vehicle lanes. This allows each ship to carry 300 trucks, 230 cars and 1,200 passengers looked after by 85 crew.

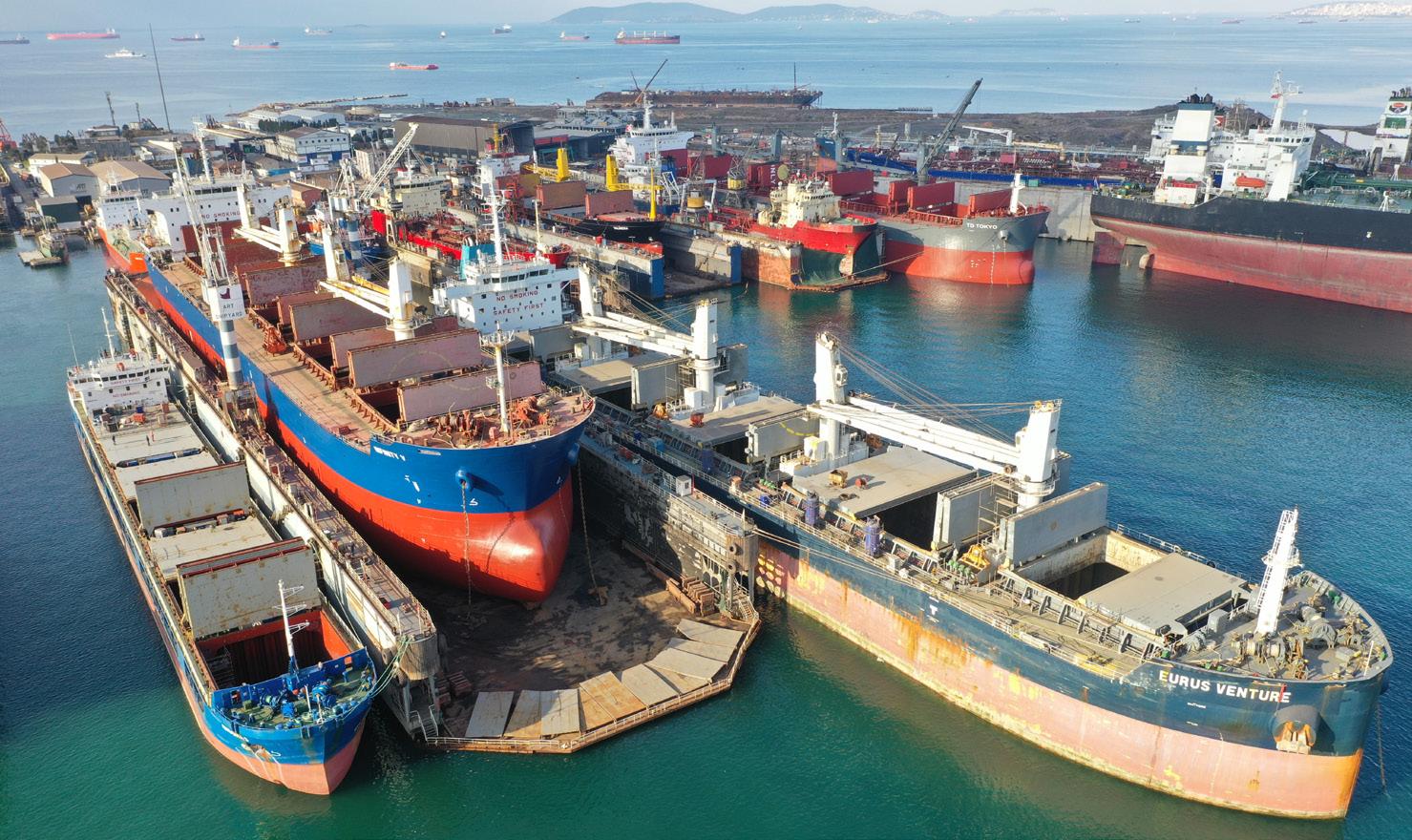
Turkey’s ART Shipyard
ART Shipyard to expand
Since its establishment in 2019, Turkey’s Art Shipyard has gained the appreciation of leading shipowners and exponentially widening its customer range with the continuous improvements of the yard’s facilities.
Art Shipyard is part of the Besiktas Group in Tuzla Bay and has a passionate and young team working hard to make the yard one of the key players in the industry. Last year Art Shipyard completed 82 repair and maintenance projects, an increase of 15% of turnover and reached 207 shiprepair projects since its inauguration.
Besides its work quality, engineering power and short delivery schedules, the improvements in yard facilities played an important role in this success. The yard strengthens its position with a continuous development strategy. Due to increasing demand of BWM system projects, the 1,500 m2 pipe manufacturing and equipment workshop has been modernised.
The Heat Exchanger Ultrasonic cleaning workshop has started operation inside the shipyard. A new shaft and mechanical workshop and the other workshops areas are being enlarged in order to meet the industry’s increasing demand.
During the first quarter of this year (2022), steel work has totalled some 435 tonnes for some three repair projects. Ship types in the yard in this period includes repairs to five chemical tankers, 10 bulk carriers, one general cargo vessel, and two containerships. Within these projects a total of 13 BWM systems have been installed, the equipment supplied by various manufacturers including DESMI, Techcross, Panasia, Ocean Guard and Alfa Laval. SORJ