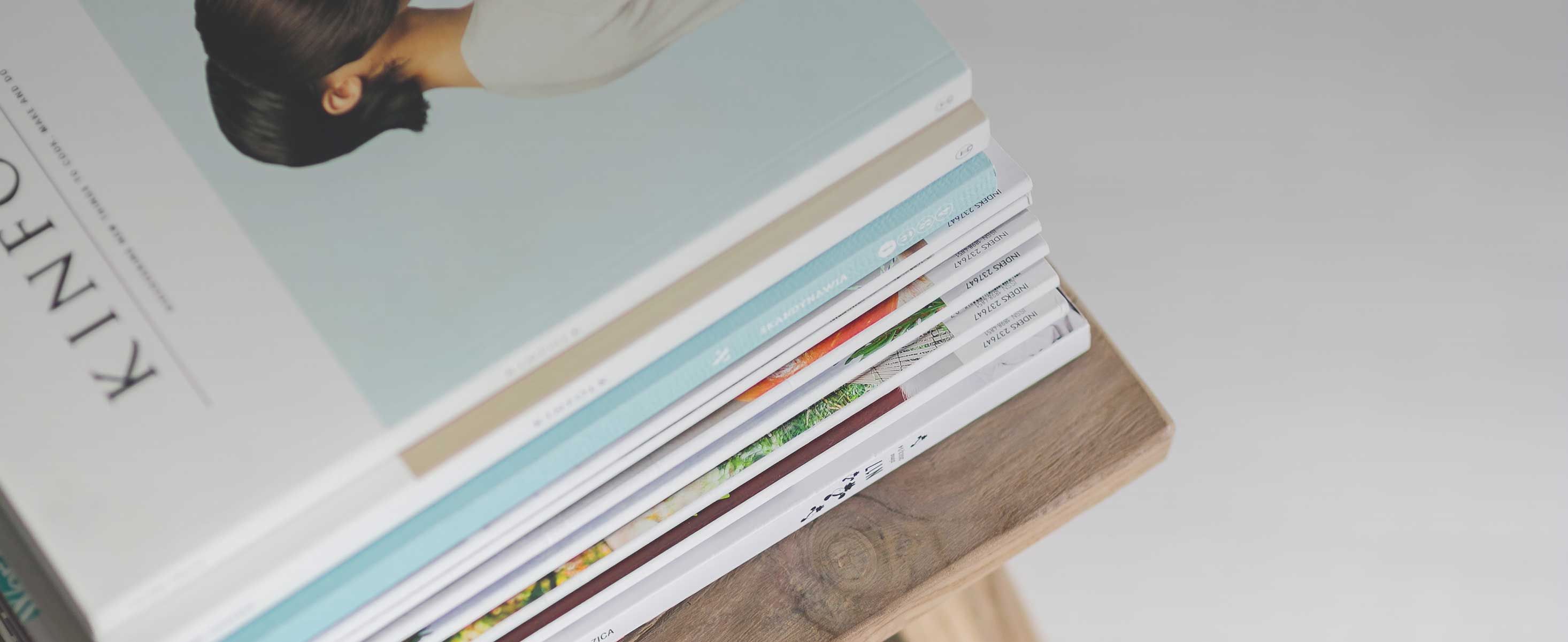
1 minute read
Sustainability risks
Nilorn’s risk management approach follows our decentralised structure and the same applies to our sustainability risks. All managers at Nilorn with operational responsibilities are expected to ensure that risks associated with their operations are appropriately identified, evaluated and managed.
RISK CATEGORY
Advertisement
COMPLIANCE
RISK DESCRIPTION
Risks that legal and regulatory requirements are not met.
HEALTH & SAFETY Injuries or work related sickness at Nilorn own production sites or at supplier sites.
ENVIRONMENT Managing increased demand of more environmentally conscious products by our clients. Increased demand to understand climate change effect on both internal and external operations.
SUPPLY CHAIN Risk of suppliers not complying with the Supplier Code of Conduct and not following national laws and regulations.
RISK CONSEQUENCES
Negative reputational and/or financial impact.
Fatal accidents, serious injuries or long-term absenteeism at production sites. Risk of legal and financial conseqences if OHS has been managed poorly. Risk that employees find the work environ ment unsatisfactory, resulting in difficulties to retain and recruit. Reputational risk if poor safety conditions exist in the company, resulting in damage to our brand.
Risk of losing clients. Not being able to meet clients’ expectations in our operations and/or products with regards to environmental performance and new materials. Risk of problems with supply due to climate related incidents.
Negative reputation and risk that we do not live up to the requirements of our clients. Delays in delivery and increased costs.
RISK MITIGATION
Nilorn has a group governance framework and compliance, including anti-bribery and corruption policy. Increase training. Establish appropriate procedures, monitoring and reporting to prevent violation of laws, corruption or handling of personal data. 3rd party social audit at own production units.
3rd party social audit at Nilorn production units. Own and 3rd party audits of suppliers. Continue to build a common H&S culture and effective management systems.
Focus on improved efficiency to minimise environmental impact in our own operations and in supply chain, bluesign certification being one method. Keep high awareness of new regulations and market demands.
Continue to build strong supplier relationships. Increase awareness of Code of Conduct, environmental requirements and other policies. Own and 3rd party audits of suppliers.